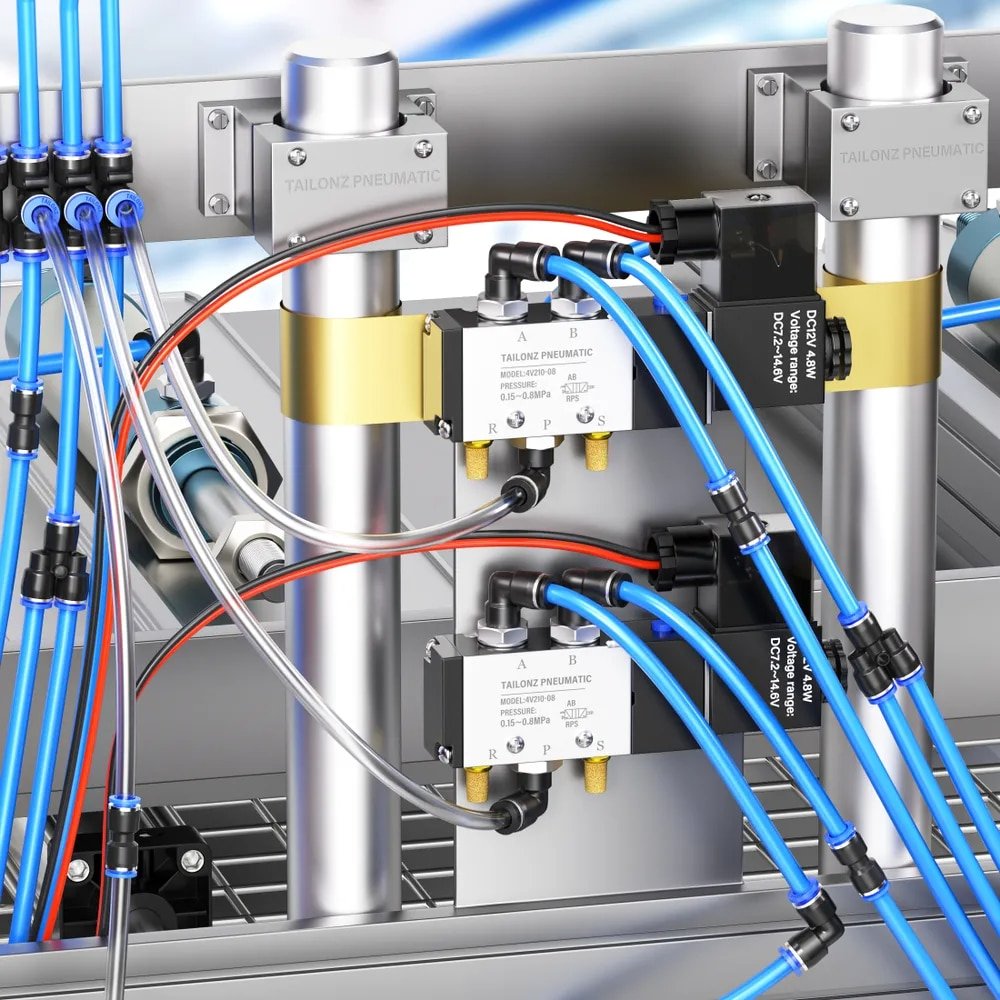
Имате ли неочаквани повреди на маркучите, опасни спадове на налягането или проблеми с химическата съвместимост във вашите пневматични системи? Тези често срещани проблеми често произтичат от неправилен избор на маркучи, което води до скъпоструващи престои, рискове за безопасността и преждевременна подмяна. Изборът на правилния пневматичен маркуч може незабавно да реши тези критични проблеми.
Идеалният пневматичен маркуч трябва да издържа на специфичните изисквания за огъване на вашето приложение, да е устойчив на химическа деградация от вътрешно и външно въздействие и да се съчетава правилно с бързите съединители, за да поддържа оптимални характеристики на налягането и потока. Правилният избор изисква разбиране на стандартите за умора при огъване, факторите за химическа съвместимост и зависимостите между налягане и поток.
Спомням си, че миналата година се консултирах със завод за химическа обработка в Тексас, където на всеки 2-3 месеца подменяха пневматични маркучи поради преждевременни повреди. След като анализираха приложението си и внедриха правилно определени маркучи с подходящи показатели за химическа устойчивост и радиус на огъване, честотата на подмяната им спадна до годишна поддръжка, спестявайки над $45,000 за престой и материали. Позволете ми да споделя какво съм научил през годините си в пневматичната индустрия.
Съдържание
- Разбиране на стандартите за изпитване на умора при огъване за пневматични маркучи
- Изчерпателно справочно ръководство за химическа съвместимост
- Как да подбираме бързите съединители за оптимално налягане и дебит
Как тестовете за умора при огъване предсказват продължителността на живота на пневматичните маркучи при динамични приложения?
Изпитването за умора при огъване предоставя важни данни за избора на маркучи в приложения с непрекъснато движение, вибрации или честа промяна на конфигурацията.
Тестовете за умора при огъване измерват способността на маркуча да издържа на многократно огъване, без да се повреди. Стандартните тестове обикновено извършват циклично огъване на маркучите през определени радиуси на огъване при контролирани налягания и температури, като броят циклите до отказ. Резултатите помагат да се предвиди реалното функциониране и да се установят минимални спецификации за радиуса на огъване за различните конструкции маркучи.
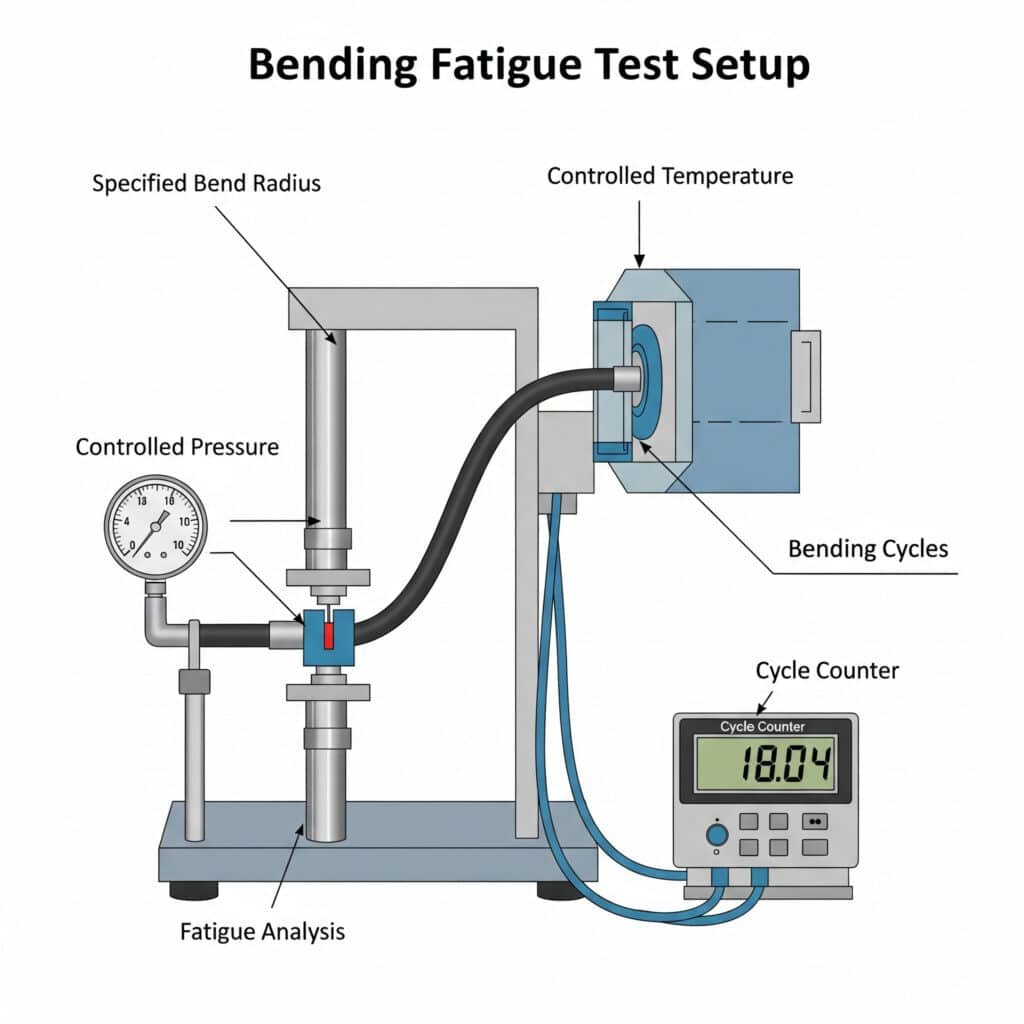
Разбиране на основите на умората при огъване
Повреда от умора при огъване възниква, когато маркучът се огъва многократно над конструктивните му възможности:
Механизмите на повреда включват:
- Напукване на вътрешната тръба
- Разбивка на слоя армировка
- Изтриване и напукване на покритието
- Неизправности при свързването на фитингите
- Прегъване и постоянна деформацияКритични фактори, влияещи върху устойчивостта на умора при огъване:
- Конструктивни материали за маркуча
- Конструкция на армировката (спирала срещу оплетка)
- Дебелина на стената и гъвкавост
- Работно налягане (по-високо налягане = по-ниска устойчивост на умора)
- Температура (екстремните температури намаляват устойчивостта на умора)
- Радиус на огъване (по-тесните огъвания ускоряват повредата)
Промишлени стандартни протоколи за тестване
Няколко утвърдени метода за изпитване оценяват характеристиките на умора при огъване:
ISO 83311 Метод
Този международен стандарт определя:
- Изисквания към апаратурата за изпитване
- Процедури за подготовка на пробите
- Стандартизиране на условията за изпитване
- Определения на критериите за отказ
- Изисквания за докладване
Стандарт SAE J517
Този автомобилен/индустриален стандарт включва:
- Специфични параметри на изпитването за различните видове маркучи
- Минимални изисквания за цикъл по класове приложения
- Връзка с очакванията за работата на терен
- Препоръки за коефициент на безопасност
Процедури за изпитване на умора при огъване
Типичното изпитване за умора при огъване следва следните стъпки:
Подготовка на пробата
- Състояние на маркуча при тестова температура
- Монтирайте подходящи крайни фитинги
- Измерване на първоначалните размери и характеристикиНастройка за изпитване
- Монтиране на маркуча в апарата за изпитване
- Прилагане на определено вътрешно налягане
- Задайте радиус на огъване (обикновено 80-120% от минималния номинален радиус на огъване)
- Конфигуриране на скоростта на цикъла (обикновено 5-30 цикъла в минута)Изпълнение на теста
- Цикъл на маркуча през определен модел на огъване
- Наблюдение за течове, деформации или загуба на налягане
- Продължете до отказ или до предварително определен брой цикли
- Записване на броя на циклите и начина на отказАнализ на данните
- Изчисляване на средните цикли до отказ
- Определяне на статистическото разпределение
- Сравняване с изискванията на приложението
- Прилагане на подходящи коефициенти на безопасност
Сравнение на ефективността на умората при огъване
Тип на маркуча | Строителство | Средни цикли до отказ* | Минимален радиус на завой | Най-добри приложения |
---|---|---|---|---|
Стандартен полиуретан | Единичен слой | 100,000 – 250,000 | 25-50 мм | Общо предназначение, леко натоварване |
Подсилен полиуретан | Полиестерна оплетка | 250,000 – 500,000 | 40-75 мм | Средно натоварване, умерено огъване |
Термопластична гума | Синтетичен каучук с единична оплетка | 150,000 – 300,000 | 50-100 мм | Обща промишленост, умерени условия |
Премиум полиуретан | Двоен слой с арамидна армировка2 | 500,000 – 1,000,000 | 50-100 мм | Високоциклична автоматизация, роботика |
Каучук (EPDM/NBR) | Синтетичен каучук с двойна оплетка | 200,000 – 400,000 | 75-150 мм | Тежък режим на работа, високо налягане |
Bepto FlexMotion | Специализиран полимер с многослойна армировка | 750,000 – 1,500,000 | 35-75 мм | Роботика с висок цикъл, непрекъснато огъване |
*При 80% от максималното номинално налягане, стандартни условия на изпитване
Тълкуване на спецификациите за минимален радиус на завой
Спецификацията на минималния радиус на огъване е от решаващо значение за правилния избор на маркуч:
- Статични приложения: Може да работи при публикуван минимален радиус на завой
- От време на време се огъва: Използвайте 1,5× минимален радиус на завой
- Постоянно огъване: Използвайте 2-3× минимален радиус на завой
- Приложения с високо налягане: Добавете 10% към радиуса на огъване за всеки 25% от максималното налягане
- Повишени температури: Добавяне на 20% към радиуса на огъване при работа при температура, близка до максималната
Пример за приложение в реалния свят
Неотдавна се консултирах с производител на роботи за сглобяване в Германия, който често се сблъскваше с повреди на маркучи в своите многоосни роботи. Техните съществуващи пневматични линии се повреждаха след приблизително 100 000 цикъла, което причиняваше значителни престои.
Анализът разкрива:
- Необходим радиус на огъване: 65 мм
- Работно налягане: 6,5 бара
- Честота на цикъла: 12 цикъла в минута
- Ежедневна работа: 16 часа
- Очакван живот: 5 години (приблизително 700 000 цикъла)
Чрез използването на маркучи Bepto FlexMotion с:
- Тестван живот на умора: >1 000 000 цикъла при тестови условия
- Многослойна армировка, предназначена за непрекъснато огъване
- Оптимизирана конструкция за специфичния им радиус на огъване
- Специализирани крайни фитинги за динамични приложения
Резултатите бяха впечатляващи:
- Нула повреди след 18 месеца експлоатация
- Разходи за поддръжка, намалени с 82%
- Премахване на престоя поради повреди на маркучите
- Прогнозен срок на експлоатация, удължен над 5-годишната цел
Кои материали за пневматични маркучи са съвместими с вашия Химическа среда3?
Химическата съвместимост е от решаващо значение за осигуряване на дълготрайност и безопасност на маркучите в среди, изложени на масла, разтворители и други химикали.
Химическата съвместимост се отнася до способността на материала на маркуча да устоява на разграждане, когато е изложен на въздействието на определени вещества. Несъвместимите химикали могат да причинят набъбване, втвърдяване, напукване или пълно разрушаване на материалите за маркучи. Правилният избор изисква съчетаване на материалите за маркучи както с вътрешните среди, така и с експозицията на външната среда.
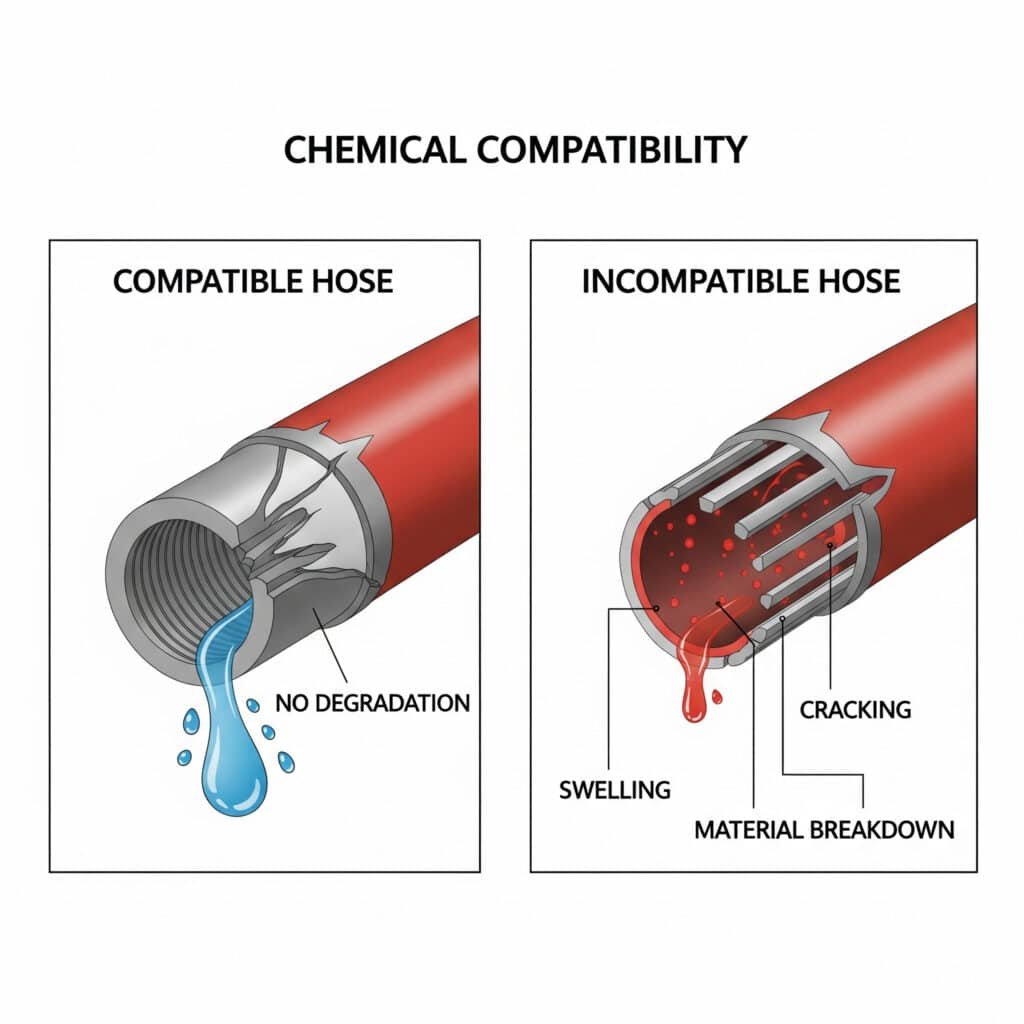
Разбиране на основите на химическата съвместимост
Химическата съвместимост включва няколко потенциални механизма на взаимодействие:
- Химическа абсорбция: Материалът абсорбира химикали, което води до подуване и омекване
- Химическа адсорбция: Химически връзки с повърхността на материала, които променят свойствата му
- Окисляване: Химическата реакция разрушава структурата на материала
- Извличане: Химикали отстраняване на пластификатори или други компоненти
- Хидролиза: Разграждане на структурата на материала на водна основа
Изчерпателна таблица за бърза справка за химическа съвместимост
Тази таблица предоставя бърза справка за често срещани материали за маркучи и химически експозиции:
Химически | Полиуретан | Найлон | PVC | NBR (нитрил) | EPDM | FKM (Viton) |
---|---|---|---|---|---|---|
Вода | A | A | A | B | A | A |
Въздух (с маслена мъгла) | A | A | B | A | C | A |
Хидравлично масло (минерално) | B | A | C | A | D | A |
Синтетична хидравлична течност | C | B | D | B | B | A |
Бензин | D | D | D | C | D | A |
Дизелово гориво | C | C | D | B | D | A |
Ацетон | D | D | D | D | C | C |
Алкохоли (метил, етил) | B | B | B | B | A | A |
Слаби киселини | C | C | B | C | A | A |
Силни киселини | D | D | D | D | C | B |
Слаби основи | B | D | B | B | A | C |
Силни основи | C | D | C | C | A | D |
Растителни масла | B | A | C | A | C | A |
Озон | B | A | C | C | A | A |
Излагане на UV лъчи | C | B | C | C | B | A |
Ключ за оценка:
- А: Отличен (минимален или никакъв ефект)
- B: Добър (незначителен ефект, подходящ за повечето приложения)
- C: Добър (умерен ефект, подходящ за ограничена експозиция)
- D: Слаб (значително влошаване, не се препоръчва)
Специфични за материала свойства на химическа устойчивост
Полиуретан
- Силни страни: Отлична устойчивост на масла, горива и озон
- Слабости: Слаба устойчивост на някои разтворители, силни киселини и основи
- Най-добри приложения: Обща пневматика, среди, съдържащи масла
- Избягвайте: Кетони, хлорирани въглеводороди, силни киселини/основи
Найлон
- Силни страни: Отлична устойчивост на масла, горива и много разтворители
- Слабости: Слаба устойчивост на киселини и продължително излагане на вода
- Най-добри приложения: Системи за сух въздух, работа с гориво
- Избягвайте: Киселини, среди с висока влажност
PVC
- Силни страни: Добра устойчивост на киселини, основи и алкохоли
- Слабости: Слаба устойчивост на много разтворители и петролни продукти
- Най-добри приложения: Вода, леки химически среди
- Избягвайте: Ароматни и хлорирани въглеводороди
NBR (нитрил)
- Силни страни: Отлична устойчивост на масла, горива и грес
- Слабости: Слаба устойчивост на кетони, озон и силни химикали
- Най-добри приложения: Маслосъдържащи въздушни и хидравлични системи
- Избягвайте: Кетони, хлорирани разтворители, нитросъединения
EPDM
- Силни страни: Отлична устойчивост на вода, химикали и атмосферни влияния
- Слабости: Много слаба устойчивост на масла и петролни продукти
- Най-добри приложения: Излагане на открито, пара, спирачни системи
- Избягвайте: Всякакви течности или смазочни материали на петролна основа
FKM (Viton)
- Силни страни: Изключителна химическа и температурна устойчивост
- Слабости: Висока цена, слаба устойчивост на определени химикали
- Най-добри приложения: Тежки химически среди, високи температури
- Избягвайте: Кетони, естери и етери с ниско молекулно тегло
Методология за изпитване на химическа съвместимост
Когато не са налични конкретни данни за съвместимост, може да се наложи тестване:
Изпитване чрез потапяне
- Потапяне на пробата от материала в химикал
- Наблюдение за промяна на теглото, размерите и визуално влошаване
- Изпитване при температура на приложение (по-високите температури ускоряват ефектите)
- Оценка след 24 часа, 7 дни и 30 дниДинамично изпитване
- Излагане на маркуча под налягане на химикали при огъване
- Наблюдение за течове, загуба на налягане или физически промени
- Ускоряване на изпитването с повишени температури, ако е необходимо
Проучване на случай: Решение за химическа съвместимост
Неотдавна работих с фармацевтично предприятие в Ирландия, което често се сблъскваше с повреди на маркучи в системата си за почистване. Системата използваше ротационен набор от почистващи химикали, включително разтвори на каустик, меки киселини и дезинфектанти.
Съществуващите PVC маркучи се повреждат след 3-4 месеца експлоатация, което води до забавяне на производството и риск от замърсяване.
След анализ на профила на експозиция на химикали:
- Първична вътрешна експозиция: Редуващи се разтвори на каустик (pH 12) и киселина (pH 3)
- Вторична експозиция: Дезинфектанти (на основата на пероцетна киселина)
- Външна експозиция: Почистващи препарати и случайни пръски от химикали
- Температурен диапазон: Околна среда до 65°C
Приложихме решение с два материала:
- Маркучи с EPDM облицовка за контурите за почистване с каустик
- Маркучи с FKM облицовка за цикъла за киселина и дезинфектант
- И двата с химически устойчиви външни капаци
- Специализирана система за свързване за предотвратяване на кръстосано замърсяване
Резултатите бяха значителни:
- Удължен експлоатационен живот на маркуча до над 18 месеца
- Нула инциденти със замърсяване
- Намалени разходи за поддръжка чрез 70%
- Подобрена надеждност на цикъла на почистване
Как да съчетаете бързите съединители, за да поддържате оптимално налягане и дебит в пневматичните системи?
Правилното съчетаване на бързите съединители с маркучите и изискванията на системата е от решаващо значение за поддържане на налягането и дебита.
Бърз съединител Изборът им оказва значително влияние върху спада на налягането в системата и капацитета на потока. Недостатъчно оразмерените или ограничаващи съединители могат да създадат тесни места, които намаляват производителността на инструмента и ефективността на системата. Правилното подбиране изисква разбиране на стойностите на коефициента на потока (Cv), номиналното налягане и съвместимостта на връзките.
Разбиране на характеристиките на бързия съединител
Бързите съединители влияят на работата на пневматичните системи чрез няколко ключови характеристики:
Коефициент на потока (Cv)4
Коефициентът на потока показва колко ефективно даден съединител пропуска въздух:
- По-високите стойности на Cv показват по-малко ограничение на потока
- Cv е пряко свързано с вътрешния диаметър на съединителя и конструкцията.
- Рестриктивните вътрешни конструкции могат значително да намалят Cv въпреки размера
Връзка с падането на налягането
Падането на налягането в съединителя следва тази зависимост:
ΔP = Q² / (Cv² × K)
Къде:
- ΔP = спад на налягането
- Q = Дебит
- Cv = Коефициент на потока
- K = константа, базирана на единици
Това показва, че:
- Падането на налягането се увеличава с квадрата на дебита
- Удвояването на дебита увеличава четирикратно спада на налягането
- По-високите стойности на Cv значително намаляват спада на налягането
Ръководство за избор на бърз съединител по приложение
Приложение | Необходима скорост на потока | Препоръчителен размер на съединителя | Минимална стойност на Cv | Максимален пад на налягането* |
---|---|---|---|---|
Малки ръчни инструменти | 0-15 SCFM | 1/4″ | 0.8-1.2 | 0,3 бара |
Средни пневматични инструменти | 15-30 SCFM | 3/8″ | 1.2-2.0 | 0,3 бара |
Големи пневматични инструменти | 30-50 SCFM | 1/2″ | 2.0-3.5 | 0,3 бара |
Много висок дебит | >50 SCFM | 3/4″ или по-големи | >3.5 | 0,3 бара |
Прецизен контрол | Варира | Размер за спад от <0,1 бара | Варира | 0,1 бара |
*При максималния посочен дебит
Принципи на съгласуване на съединителя и маркуча
За оптимална работа на системата спазвайте тези принципи на съгласуване:
Съвпадение на капацитета на потока
- Cv на съединителя трябва да позволява поток, равен или по-голям от капацитета на маркуча
- Няколко малки съединителя не могат да се равняват на един правилно оразмерен съединител
- При изчисляване на спада на налягането в системата вземете предвид всички съединители в серия.Вземете предвид стойностите на налягането
- Номиналното налягане на съединителя трябва да отговаря или да надвишава изискванията на системата
- Прилагане на подходящи коефициенти на сигурност (обикновено 1,5-2 пъти)
- Не забравяйте, че динамичните скокове на налягането могат да надвишат статичните стойностиОценка на съвместимостта на връзката
- Уверете се, че типовете и размерите на резбата са съвместими
- Разглеждане на международни стандарти, ако оборудването е от няколко региона
- Проверете дали методът на свързване е подходящ за изискванията за наляганеотчитане на факторите на околната среда
- Температурата влияе върху номиналното налягане (обикновено се намалява при по-високи температури)
- Корозивни среди могат да изискват специални материали
- Ударите или вибрациите могат да изискват заключващи механизми.
Сравнение на капацитета на потока на бързия съединител
Тип съединител | Номинален размер | Типична стойност на Cv | Дебит при спад от 0,5 бара* | Най-добри приложения |
---|---|---|---|---|
Стандартни индустриални | 1/4″ | 0.8-1.2 | 15-22 SCFM | Ръчни инструменти с общо предназначение |
Стандартни индустриални | 3/8″ | 1.5-2.0 | 28-37 SCFM | Инструменти за средно натоварване |
Стандартни индустриални | 1/2″ | 2.5-3.5 | 46-65 SCFM | Големи пневматични инструменти, основни линии |
Дизайн с висок дебит | 1/4″ | 1.3-1.8 | 24-33 SCFM | Компактни приложения с висок дебит |
Дизайн с висок дебит | 3/8″ | 2.2-3.0 | 41-55 SCFM | Критични за производителността инструменти |
Дизайн с висок дебит | 1/2″ | 4.0-5.5 | 74-102 SCFM | Критични системи с висок дебит |
Bepto UltraFlow | 1/4″ | 1.9-2.2 | 35-41 SCFM | Премиум компактни приложения |
Bepto UltraFlow | 3/8″ | 3.2-3.8 | 59-70 SCFM | Високопроизводителни инструменти |
Bepto UltraFlow | 1/2″ | 5.8-6.5 | 107-120 SCFM | Изисквания за максимален дебит |
*При 6 бара захранващо налягане
Изчисляване на пада на налягането в системата
За да подберете правилно компонентите, изчислете общия пад на налягането в системата:
Изчисляване на капките на отделните компоненти
- Маркуч: ΔP = (L × Q² × f) / (2 × d⁵)
- L = дължина
- Q = Дебит
- f = коефициент на триене
- d = вътрешен диаметър
- Фитинги/съединители: ΔP = Q² / (Cv² × K)Сумиране на всички спадове на налягането на компонентите
- Общо ΔP = ΔP₁ + ΔP₂ + ... + ΔPₙ
- Не забравяйте, че капките се натрупват в системата.Проверка на приемливия общ спад на налягането
- Промишлен стандарт: Максимално налягане на подаване 10%
- Критични приложения: Максимално налягане на подаване 5%
- Специфичен инструмент: Проверете изискванията на производителя за минимално налягане
Практически пример: Оптимизация на бърз съединител
Наскоро се консултирах с автомобилен завод в Мичиган, който имаше проблеми с работата на ударните си гайковерти. Въпреки че компресорът имаше достатъчен капацитет и захранващо налягане, инструментите не постигаха определения въртящ момент.
Анализът разкрива:
- Налягане на подаване към компресора: 7,2 bar
- Изисквано налягане на инструмента: 6,2 бара
- Разход на въздух за инструмента: 35 SCFM
- Съществуваща конфигурация: 3/8″ маркуч със стандартни 1/4″ съединители
Измерванията на налягането показват:
- Падане на 0,7 бара през бързите съединители
- спад от 0,4 бара по маркуча
- Общ спад на налягането: 1,1 бара (15% от подаваното налягане)
Чрез надграждане до компоненти Bepto UltraFlow:
- 3/8″ съединители с висок дебит (Cv = 3,5)
- Оптимизиран монтаж на маркуч 3/8″
- Оптимизирани връзки
Резултатите бяха незабавни:
- Спадът на налягането е намален до 0,4 бара (5,5% от налягането на подаване)
- Възстановяване на производителността на инструментите в съответствие със спецификациите
- Подобрена производителност чрез 12%
- Подобрена енергийна ефективност поради по-ниското необходимо налягане на подаване
Контролен списък за избор на бърз съединител
При избора на бързи съединители вземете предвид тези фактори:
Изисквания за потока
- Изчисляване на необходимия максимален дебит
- Определяне на приемливия спад на налягането
- Изберете куплунг с подходяща стойност на CvИзисквания за налягане
- Определяне на максималното налягане в системата
- Прилагане на подходящ коефициент на сигурност
- Вземете предвид колебанията на налягането и пренапрежениятаСъвместимост на свързването
- Вид и размер на резбата
- Международни стандарти (ISO, ANSI и др.)
- Съществуващи компоненти на систематаЕкологични съображения
- Температурен диапазон
- Експозиция на химикали
- Механичен стрес (вибрации, удари)Оперативни фактори
- Честота на свързване/прекъсване на връзката
- Изисквания за работа с една ръка
- Характеристики за безопасност (безопасно изключване под налягане)
Заключение
Изборът на правилния пневматичен маркуч и система за свързване изисква разбиране на характеристиките на умора при огъване, факторите за химическа съвместимост и съотношението налягане/ток при бързите съединители. Като прилагате тези принципи, можете да оптимизирате работата на системата, да намалите разходите за поддръжка и да осигурите безопасна и надеждна работа на пневматичното си оборудване.
Често задавани въпроси за избора на пневматични маркучи
Как радиусът на огъване влияе върху продължителността на живота на пневматичния маркуч?
Радиусът на огъване оказва значително влияние върху продължителността на живота на маркуча, особено при динамични приложения. Работата с маркуч под минималния радиус на огъване създава прекомерно натоварване на вътрешната тръба и армировъчните слоеве, което ускорява разрушаването от умора. За статични приложения обикновено е достатъчно да се поддържа минималният посочен радиус на огъване или да се надвишава той. За динамични приложения с непрекъснато огъване използвайте 2-3 пъти минималния радиус на огъване, за да удължите значително експлоатационния живот.
Какво се случва, ако използвам пневматичен маркуч с химикал, който е несъвместим с материала, от който е изработен?
Използването на маркуч с несъвместими химикали може да доведе до няколко начина на повреда. Първоначално маркучът може да набъбне, да омекне или да се обезцвети. При продължаване на излагането материалът може да се напука, втвърди или разслои. В крайна сметка това води до изтичане, скъсване или пълна повреда. Освен това, химическата атака може да компрометира номиналното налягане на маркуча, което го прави опасен дори преди да се появят видими повреди. Винаги проверявайте химическата съвместимост преди избора.
Какъв пад на налягането е допустим през бързите съединители в пневматична система?
Обикновено при повечето приложения спадът на налягането в бързите съединители не трябва да надвишава 0,3 bar (5 psi) при максимален дебит. За цялата пневматична система общият пад на налягането трябва да бъде ограничен до 10% от захранващото налягане (напр. 0,6 bar в система с налягане 6 bar). Критичните или прецизните приложения могат да изискват още по-нисък спад на налягането, обикновено 5% или по-малко от подаваното налягане.
Мога ли да използвам бърз съединител с по-голям диаметър, за да намаля спада на налягането?
Да, използването на бърз съединител с по-голям диаметър обикновено увеличава капацитета на потока и намалява спада на налягането. Подобрението обаче следва нелинейна зависимост - удвояването на диаметъра увеличава капацитета на потока приблизително четири пъти (при сходна вътрешна конструкция). При модернизиране вземете предвид както номиналния размер на съединителя, така и неговия коефициент на потока (Cv), тъй като вътрешната конструкция оказва значително влияние върху производителността независимо от размера.
Как да разбера кога пневматичният маркуч се нуждае от подмяна поради умора при огъване?
Признаците, че пневматичният маркуч се приближава към повреда поради умора при огъване, включват: видимо напукване или напукване на външното покритие, особено в точките на огъване; необичайна твърдост или мекота в сравнение с новия маркуч; деформация, която не се възстановява при освобождаване на налягането; мехурчета или мехури в точките на огъване; и лек теч или "плакнене" през материала на маркуча. Приложете програма за превантивна подмяна въз основа на броя на циклите или работните часове, преди да се появят тези признаци.
Каква е разликата между работното налягане и налягането на разрушаване при пневматичните маркучи?
Работното налягане е максималното налягане, при което маркучът е проектиран да работи непрекъснато при нормални условия, докато налягането на разрушаване е налягането, при което се очаква маркучът да се разруши. Обикновено налягането на разрушаване е 3-4 пъти по-голямо от работното налягане, което осигурява коефициент на безопасност. Никога не работете с маркуч под налягане, близко до това на разрушаване. Също така имайте предвид, че стойностите на работното налягане обикновено намаляват с повишаване на температурата и с остаряването или износването на маркуча.
-
Предоставя преглед на стандарта ISO 8331, който определя метод за изпитване на живота при умора на гумени и пластмасови маркучи в условия на многократно огъване, което е от решаващо значение за динамични приложения. ↩
-
Обяснява свойствата на арамидните влакна - клас високоефективни синтетични влакна, известни с изключителното си съотношение между здравина и тегло, устойчивост на топлина и използване като армировка в съвременни композити и гъвкави материали. ↩
-
Предлага практичен инструмент или изчерпателна таблица, която позволява на потребителите да проверят устойчивостта на различни пластмаси и еластомери срещу широк спектър от химикали, което е от съществено значение за избора на правилния материал за маркуч. ↩
-
Предоставя техническо определение на коефициента на потока (Cv) - стандартизирано безразмерно число, което представлява ефективността на вентила или друг компонент при пропускане на флуид, което се използва за изчисляване на пада на налягането. ↩