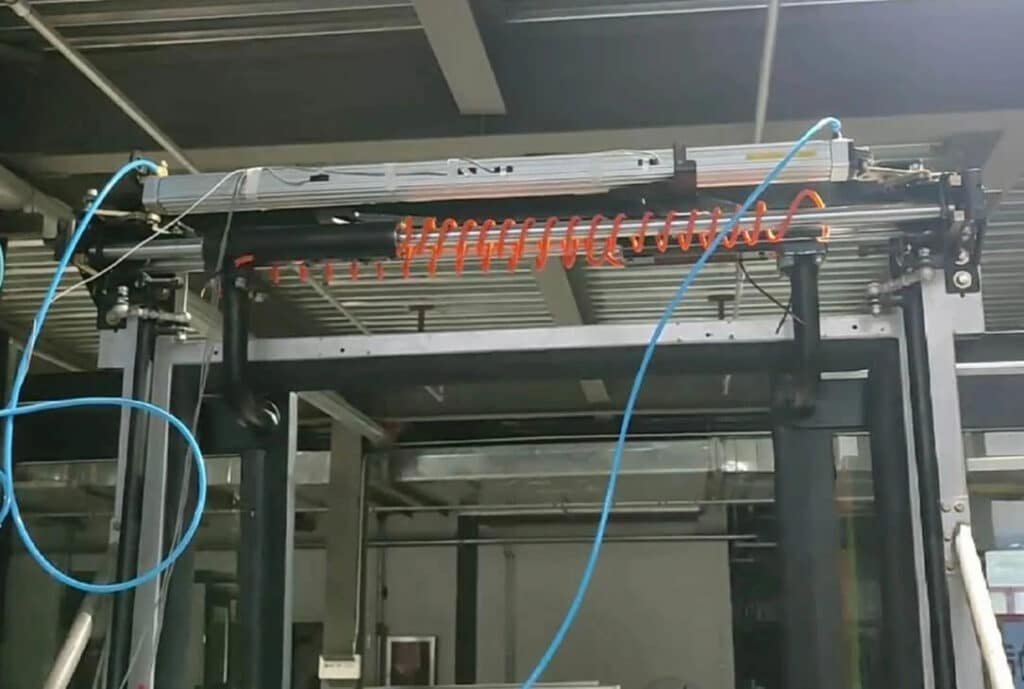
Potýkáte se s neefektivními balicími linkami, které nedokážou držet krok s požadavky na výrobu? Mnoho balicích provozů se potýká se značnými problémy s tradičními pneumatickými systémy, které omezují rychlost, přesnost a flexibilitu, což vede k nákladným překážkám a problémům s údržbou.
Pneumatické válce bez tyčí mohou výrazně zlepšit výkonnost balicích strojů tím, že umožňují kratší časy cyklů, přesnější polohování, prostorově úsporné konstrukce a vyšší spolehlivost - což přináší až o 40% vyšší výkon ve vysokorychlostních balicích aplikacích.
Nedávno jsem navštívil závod na balení potravin v Německu, kde jejich konvenční systém pick-and-place založený na válcích vytvářel velké překážky ve výrobě. Po zavedení našeho řešení bez tyčových válců zvýšili rychlost balení o 35% a zároveň snížili plochu stroje téměř o polovinu. Dovolte mi, abych vám ukázal, jak je možné dosáhnout podobných výsledků i ve vašem provozu.
Obsah
- V čem jsou vysokorychlostní uchopovací mechanismy s beztaktními válci účinnější?
- Jak může víceosá synchronizace změnit efektivitu balení?
- Proč jsou pro moderní balicí linky důležité systémy s antikolizními senzory?
- Závěr
- Časté dotazy o beztlakových válcích v obalových aplikacích
V čem jsou vysokorychlostní uchopovací mechanismy s beztaktními válci účinnější?
Vysokorychlostní uchopovací mechanismy představují jeden z nejnáročnějších aspektů konstrukce balicích strojů, protože vyžadují rychlost i přesnost při nepřetržitém provozu.
Vysokorychlostní uchopovací mechanismy jsou výrazně efektivnější s beztaktními válci, protože poskytují nižší pohyblivou hmotnost, umožňují rychlejší cykly zrychlení/zpomalení, nabízejí kompaktnější integraci s koncové efektory1a poskytují konzistentní výkon i při rychlosti cyklu přesahující 120 sběrů za minutu.
Po implementaci desítek vysokorychlostních uchopovacích řešení v Evropě a Severní Americe jsem identifikoval několik kritických faktorů, které rozhodují o úspěchu v těchto náročných aplikacích. Správná konfigurace beztyčového válce rozhoduje o všem.
Klíčové faktory výkonu pro vysokorychlostní uchopení
Při navrhování vysokorychlostních uchopovacích systémů pro balicí aplikace je třeba optimalizovat několik prvků současně:
- Hmotnostní optimalizace: Při vysokém počtu cyklů záleží na každém gramu
- Profily zrychlení: Plynulý nájezd zabraňuje poškození výrobku
- Přesnost při rychlosti: Udržení přesnosti při rychlém pohybu
- Konzistence cyklu: Stejný výkon v milionech cyklů
Srovnávací analýza výkonu
Parametr | Tradiční válec | Válec bez tyčí | Výhoda výkonu |
---|---|---|---|
Pohyblivá hmota | Vysoká (tyč + vnější mechanismus) | Nízká (integrovaný vozík) | 30-50% rychlejší zrychlení |
Schopnost rychlosti cyklu | 40-60 cyklů/minutu | 100-140 cyklů za minutu | 2-3x vyšší propustnost |
Požadavek na plochu | Velký (zdvih + délka válce) | Kompaktní (pouze délka zdvihu) | 40-60% redukce prostoru |
Interval údržby | 3-5 milionů cyklů | 10-15 milionů cyklů | Výrazné zkrácení prostojů |
Případová studie konfigurace: Obaly na cukrovinky
Jednu z mých nejúspěšnějších implementací jsem provedl pro výrobce prémiové čokolády ve Švýcarsku. Jejich úkolem bylo:
- Balení jemných pralinek rychlostí 100+ kusů za minutu
- manipulace s různými velikostmi výrobků bez nutnosti výměny
- Zachovávejte šetrné zacházení, aby nedošlo k poškození výrobku
- nepřetržitý provoz ve třech směnách
Architektura řešení
Vyvinuli jsme vlastní konfiguraci, která obsahuje:
Primární osa pohybu
- Magnetický válec bez tyče (ekvivalent řady MY1B40)
- 400mm zdvih optimalizovaný pro uspořádání balicí linky
- Vysoká odezva proporcionální řízení průtoku pro řízení zrychleníIntegrace uchopovače
- Lehká montážní konzola z uhlíkových vláken
- Vakuová soustava pohárků s nezávislým zavěšením
- Rychlovýměnné rozhraní pro údržbuŘídicí systém
- Zpětná vazba polohy pomocí bezkontaktních senzorů
- Programovatelné profily pohybu pro různé typy výrobků
- Monitorování cyklu v reálném čase s upozorněními na prediktivní údržbu
Výsledky byly působivé:
- Zvýšená propustnost z 60 na 110 jednotek za minutu
- Snížení poškození výrobku o 85%
- Snížení prostojů při údržbě o 67%
Klíčovým faktorem úspěchu bylo pochopení, že vysokorychlostní uchopení není jen o hrubé rychlosti - jde o kontrolovaný, přesný pohyb, který lze spolehlivě udržet po miliony cyklů. Beztyčové válce představují ideální platformu pro dosažení této rovnováhy.
Jak může víceosá synchronizace změnit efektivitu balení?
Víceosá synchronizace představuje novou hranici v automatizaci balení, která umožňuje složité pohyby, jež byly dříve u běžných systémů nemožné.
Víceosá synchronizace s beztaktními válci přináší revoluci v efektivitě balení tím, že umožňuje komplexní trojrozměrné pohyby, usnadňuje plynulý tok výrobků, eliminuje body přenosu mezi operacemi a umožňuje dynamické přizpůsobení různým velikostem balení bez mechanických přestaveb.
Během své kariéry, kdy jsem implementoval obalová řešení, jsem viděl jasný vývoj směrem k sofistikovanějším víceosým systémům. Nejnovější generace technologie válců bez tyčí v této oblasti změnila pravidla hry.
Synchronizační architektury pro obalové aplikace
Moderní balicí systémy obvykle používají jeden z několika synchronizačních přístupů:
Mechanická synchronizace
Mezi tradiční metody patří:
- Vačkové mechanismy
- Mechanické vazby
- Časovací systémy založené na převodovce
Tyto přístupy nabízejí:
- Jednoduchá implementace
- Omezená flexibilita
- Obtížný přechod na jiné produkty
- Vysoké nároky na údržbu
Pneumatická víceosá synchronizace
Pokročilé beztlakové válcové systémy poskytují:
- Elektronické sledování polohy
- Proporcionální regulace tlaku/průtoku
- Nezávislé nastavení osy
- Programovatelné profily pohybu
Metodiky programování víceosých systémů
Metoda synchronizace | Přístup k programování | Výhody | Nejlepší aplikace |
---|---|---|---|
Master/Slave2 | Jedna osa řídí časování ostatních | Zjednodušené programování | Kartonování, balení do krabic |
Koordinovaný pohyb | Všechny osy sledují naprogramované dráhy | Komplexní pohybová schopnost | Obalové balení |
Nezávislost s kontrolními body | Osy se pohybují nezávisle, ale čekají v koordinačních bodech. | Flexibilní načasování | Manipulace se smíšenými produkty |
Dynamické generování cest | Výpočet cesty v reálném čase na základě toku produktu | Přizpůsobuje se změnám | Náhodný příchod produktu |
Případ implementace: Balení do flexibilních sáčků
Nedávno jsem pomáhal jednomu francouzskému výrobci potravin modernizovat jeho systém balení do sáčků. Jejich úkoly zahrnovaly:
Manipulace s více velikostmi balení
- Sedm různých rozměrů sáčků
- Časté střídání produktů
- Nejednotné rozestupy při příchodu výrobkuKomplexní požadavky na pohyb
- Rotace výrobku během vkládání
- Jemné zrychlení pro tekuté produkty
- Přesné umístění pro zajištění integrity těsnění
Zavedli jsme tříosý systém válců bez tyčí s:
- Osa X: 800mm horizontální pohyb (výběr produktu)
- Osa Y: 400 mm vertikální pohyb (hloubka zasunutí)
- Osa Z: boční pohyb 200 mm (kontrola vyrovnání)
Programování synchronizace zahrnovalo:
- Integrace systému Vision3 pro identifikaci výrobku
- Dynamické generování cesty na základě vzdálenosti mezi příchozími produkty
- Nastavení profilu zrychlení v závislosti na úrovni naplnění
- Ověření polohy před kritickými operacemi
Výsledky změnily jejich fungování:
- Zkrácení doby výměny ze 45 minut na méně než 5 minut
- Zvýšení rychlosti výroby o 40%
- Flexibilita při zpracování nových velikostí balení bez mechanických změn
- Výrazné snížení počtu selhání těsnění a poškození výrobků
Klíčovým poznatkem bylo poznání, že skutečná synchronizace přesahuje pouhou koordinaci pohybu - vyžaduje integrované snímání, dynamické přizpůsobení a inteligentní plánování cesty. Bezprutové válce představují ideální platformu pro tuto úroveň sofistikovanosti.
Proč jsou pro moderní balicí linky důležité systémy s antikolizními senzory?
S tím, jak se obalové systémy stávají složitějšími a kompaktnějšími, dramaticky roste riziko kolize komponent, a proto jsou nezbytné správné senzorové systémy.
Antikolizní senzorové systémy mají pro moderní balicí linky zásadní význam, protože zabraňují nákladnému poškození zařízení, eliminují neočekávané prostoje, chrání cenné výrobky před poškozením a umožňují konstrukci strojů s vyšší hustotou, která maximalizuje produktivitu na omezeném prostoru.
Protože jsem v obalových systémech řešil řadu selhání souvisejících s kolizí, mohu potvrdit důležitost správné implementace senzorů. Finanční dopad i jediné kolizní události může být značný.
Posuzování rizika kolize v obalových systémech
Moderní balicí linky čelí několika kategoriím kolizních rizik:
Kolize vnitřních mechanismů
- mezi pohyblivými součástmi v rámci jednoho stroje
- Často způsobené selháním časování nebo synchronizace.Kolize výrobku a mechanismu
- Mezi obalovými materiály a součástmi strojů
- Obvykle v důsledku zaseknutí produktu nebo nesprávného podávání.Vnější kolize
- mezi sousedními stroji nebo interakcí obsluhy
- Často souvisí s údržbou nebo úpravami procesů.
Senzorové technologie pro prevenci kolizí
Typ senzoru | Princip fungování | Výhody | Omezení |
---|---|---|---|
Senzory přiblížení4 | Detekce blízkých objektů bez kontaktu | Rychlá odezva, jednoduchá implementace | Omezený dosah detekce |
Průchozí fotoelektrický paprsek | Detekce přerušení paprsku | Spolehlivost v prašném prostředí | Pevná detekční zóna |
Oblastní skenery | Sledování vymezených bezpečnostních zón | Flexibilní ochranné oblasti | Vyšší náklady |
Snímače síly a točivého momentu | Zjištění odporu proti pohybu | Dokáže vycítit blížící se kolizi | Komplexní integrace |
Systémy Vision | Detekce objektů pomocí kamery | Komplexní monitorování | Režijní náklady na zpracování |
Praktická strategie nastavení senzorů
Při zavádění antikolizních systémů s válci bez tyčí doporučuji tento strukturovaný přístup:
1. Identifikace kritické zóny
Nejprve identifikujte všechny potenciální kolizní body:
- Pozice na konci zdvihu
- Průsečíky mezi osami
- Místa přenosu produktů
- Oblasti interakce obsluhy
2. Výběr a umístění senzorů
Pro každou zónu vyberte vhodné senzory na základě:
- Požadovaná rychlost detekce
- Podmínky prostředí (prach, vlhkost atd.)
- Prostorová omezení
- Požadavky na spolehlivost
3. Integrace s řídicími systémy
Vytvoření komplexní bezpečnostní architektury:
- Primární prevence kolize (normální provoz)
- Sekundární pojistky (poruchové stavy)
- Protokoly pro reakci na mimořádné události
Reálná implementace: Linka blistrů
U klienta, který se zabýval balením léčiv v Itálii, docházelo k častým kolizím na lince na balení blistrů, což mělo za následek:
- Přibližně 4-6 hodin odstávek měsíčně
- Náklady na náhradní díly přesahující 5 000 EUR čtvrtletně
- Ztráta výrobku z poškozených obalů
Zavedli jsme komplexní antikolizní systém, který obsahuje:
Sledování polohy válce
- Magnetické senzory v kritických polohách
- Průběžná zpětná vazba polohy na osách s dlouhým zdvihem
- Redundance signálů pro kritické zónyDynamické ochranné zóny
- Nastavitelné detekční oblasti podle velikosti balení
- Prediktivní modelování kolizí v řídicím systému
- Možnost nastavení trasy v reálném časeIntegrovaná bezpečnostní reakce
- Odstupňované snížení rychlosti v blízkosti potenciálních kolizních bodů
- Řízené nouzové zastavení, aby se zabránilo poškození výrobku
- Automatizované sekvence obnovy po odstranění závady
Výsledky byly okamžité a významné:
- Nulový počet kolizních událostí za 18 měsíců od zavedení systému
- Zvýšená rychlost stroje díky důvěře v ochranné systémy
- Schopnost pracovat s menšími rozestupy mezi součástmi
- Výrazné snížení nákladů na údržbu
Klíčovým poznatkem bylo poznání, že účinná prevence kolizí není jen o detekci potenciálních nárazů - jde o vytvoření komplexního systému, který předvídá, předchází a bezpečně řídí možné kolizní scénáře v průběhu celého procesu balení.
Závěr
Beztyčové válce nabízejí transformativní výhody pro balicí stroje a poskytují rychlost, přesnost a spolehlivost potřebnou pro vysoce výkonné uchopovací mechanismy, víceosou synchronizaci a komplexní antikolizní systémy. Strategickou implementací těchto řešení mohou balicí provozy dosáhnout významného zlepšení propustnosti, flexibility a provozní efektivity.
Časté dotazy o beztlakových válcích v obalových aplikacích
Jaká jsou omezení rychlosti beztlakových válců v balicích aplikacích?
Moderní pneumatické válce bez tyčí mohou v balicích aplikacích dosahovat rychlosti až 3 m/s, přičemž zrychlení přesahuje 30 m/s². Optimální výkon však obvykle zahrnuje provoz při rychlostech 1-2 m/s s řízenými profily zrychlení, aby byla zachována přesnost a integrita produktu během manipulačních operací.
Jak si vedou beztyčové válce v porovnání s elektrickými pohony pro balicí stroje?
Pneumatické válce bez tyčí mají oproti elektrickým pohonům v obalových aplikacích několik výhod, včetně nižších nákladů (obvykle o 30-40% méně), lepší odolnosti vůči smývatelnému prostředí, jednodušší údržby a vynikajícího poměru síly k velikosti. Elektrické pohony však mohou poskytovat lepší řízení polohy pro extrémně přesné aplikace vyžadující více poloh zastavení.
Jaká údržba je nutná u beztlakových válců ve vysokorychlostních balicích provozech?
Bezprutové válce ve vysokorychlostním balení obvykle vyžadují pravidelnou kontrolu těsnicích pásů (každých 3-6 měsíců), ověření seřízení snímače, občasné mazání podle specifikací výrobce a sledování účinnosti tlumení. Správně udržované jednotky mohou pracovat 10-15 milionů cyklů, než budou vyžadovat větší servis.
Zvládnou beztyčové válce různé velikosti výrobků v pružných balicích linkách?
Ano, beztyčové válce vynikají v aplikacích flexibilního balení díky své programovatelné polohovatelnosti, nastavitelným rychlostním profilům a schopnosti integrace s vidícími a snímacími systémy. Moderní systémy mohou díky využití technologií zpětné vazby polohy a proporcionálního řízení zvládnout změny velikosti produktu o velikosti 200% nebo více bez mechanických úprav.
Jaká je typická návratnost investice při přechodu na beztlakové válce v balicích strojích?
Většina balicích provozů dosáhne návratnosti investic do 6-12 měsíců po přechodu na beztlakovou technologii válců. Návratnost plyne ze zvýšené propustnosti (obvykle o 30-50% vyšší), zkrácení doby výměny (často o 80-90% rychlejší), nižších nákladů na údržbu a lepší kvality výrobků s menším počtem zmetků v důsledku poškození při manipulaci.
-
Poskytuje podrobný výklad o nástrojích na konci ramene (EOAT) neboli koncových efektorech, což jsou zařízení na konci robotického ramene nebo lineárního aktuátoru určená k interakci s okolím. ↩
-
Popisuje architekturu řízení master-slave, běžnou metodu řízení pohybu ve více osách, kdy poloha primární "master" osy určuje pohyb jedné nebo více sekundárních "slave" os. ↩
-
Nabízí přehled strojového vidění, technologií a metod používaných k automatické kontrole a analýze na základě zobrazování pro aplikace, jako je robotické navádění, kontrola kvality a třídění. ↩
-
Vysvětluje princip fungování indukčních snímačů přiblížení, běžného typu bezkontaktního snímače, který využívá elektromagnetické pole k detekci přítomnosti kovových předmětů. ↩