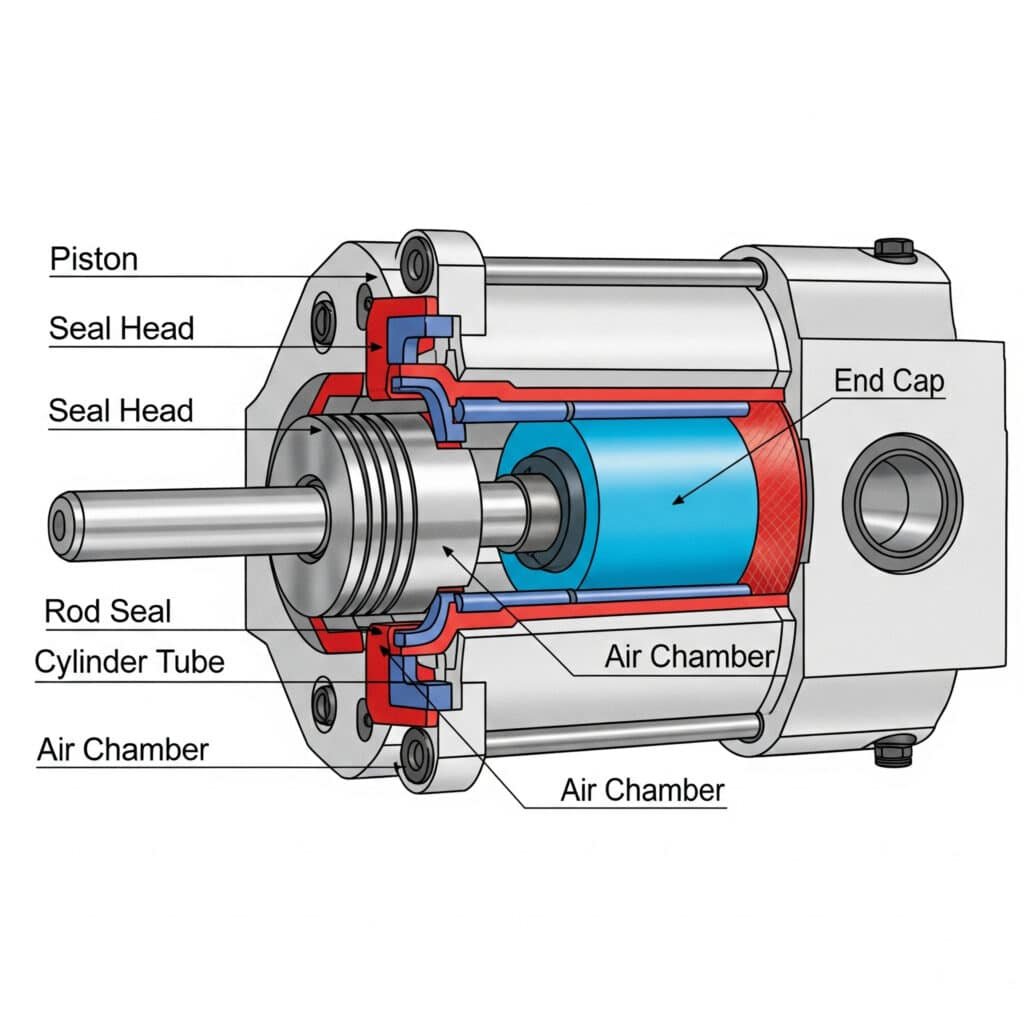
Az üzemi szintek leállnak, amikor a hengerek meghibásodnak. A mérnökök pánikba esnek, amikor a gyártósorok figyelmeztetés nélkül leállnak. A legtöbb ember soha nem érti meg azt az elegáns fizikát, amely az automatizálás e munkagépeit működteti.
A henger úgy működik, hogy sűrített levegő vagy hidraulikafolyadék segítségével nyomáskülönbséget hoz létre a dugattyú felületén, és a folyadéknyomást lineáris mechanikai erővé alakítja át a következők szerint Pascal törvénye1 (F = P × A), lehetővé téve a szabályozott lineáris mozgást az ipari automatizálásban.
A múlt héten sürgős hívást kaptam Robertótól, egy olaszországi üzemvezetőtől, akinek a palackozó sora 6 órája állt le. A karbantartó csapata véletlenszerűen cserélgette a palackokat anélkül, hogy megértette volna, miért nem működnek. Videohíváson keresztül végigvezettem őket az alapvető működési elveken, és azonosították a valódi problémát - a szennyezett levegőellátást. A vonal 30 perc alatt újra működött, és ezzel $15,000 kieső termelést takarítottak meg.
Tartalomjegyzék
- Mi a henger alapvető működési elve?
- Hogyan működnek együtt a belső komponensek?
- Milyen szerepet játszik a nyomás a henger működésében?
- Hogyan működnek a különböző henger típusok?
- Hogyan működtetik a vezérlőrendszerek a hengereket?
- Milyen erők és számítások irányítják a henger működését?
- Hogyan befolyásolják a környezeti tényezők a henger működését?
- Milyen gyakori problémák akadályozzák a henger megfelelő működését?
- Hogyan integrálódnak a modern hengerek az automatizálási rendszerekbe?
- Következtetés
- GYIK a hengerek működéséről
Mi a henger alapvető működési elve?
A hengerek működésének alapelve a fizika egyik legfontosabb, több mint 350 évvel ezelőtt felfedezett törvényén alapul.
A hengerek a Pascal-törvény alapján működnek, amely szerint a korlátozott folyadékra kifejtett nyomás minden irányban egyformán terjed, lehetővé téve a folyadéknyomás lineáris mechanikai erővé alakítását, amikor a nyomáskülönbség a dugattyú felületén hat.
Pascal törvénye Alapítvány
Blaise Pascal 1653-ban fedezte fel, hogy egy zárt folyadékban bárhol alkalmazott nyomás egyenletesen oszlik el a folyadék teljes térfogatában. Ez az elv képezi minden hidraulikus és pneumatikus henger működésének alapját.
Gyakorlatilag, amikor 6 bar nyomást alkalmazunk egy hengerben lévő sűrített levegőre, ugyanez a 6 bar nyomás a henger minden felületére hat, beleértve a dugattyú felületét is.
A varázslat azért történik, mert a dugattyú mozogni tud, míg más felületek nem. Ez hozza létre a lineáris erő és mozgás létrehozásához szükséges nyomáskülönbséget.
Nyomáskülönbség koncepció
A hengerek úgy működnek, hogy a dugattyú ellentétes oldalain különböző nyomást hoznak létre. A magasabb nyomás az egyik oldalon nettó erőt hoz létre, amely a dugattyút az alacsonyabb nyomású oldal felé nyomja.
A nyomáskülönbség határozza meg a leadott erőt: ha az egyik oldalon 6 bar, a másik oldalon pedig 1 bar (atmoszférikus) nyomás van, akkor a dugattyú területén 5 bar nettó nyomáskülönbség hat.
A maximális erő akkor jelentkezik, amikor az egyik oldal teljes rendszernyomást kap, míg a másik oldal a légkörbe távozik, így a lehető legnagyobb nyomáskülönbség alakul ki.
Erőgenerálás matematika
Az alapvető erőegyenlet F = P × A szabályozza a hengerek működését, ahol az erő egyenlő a nyomás és a dugattyú effektív felületének szorzatával. Ez az egyszerű összefüggés határozza meg a henger méretezését és teljesítményét.
A nyomásegységek világszerte eltérőek - 1 bar 14,5 PSI vagy 100 000 Pascal. A területszámítások a dugattyú tényleges átmérőjét használják, figyelembe véve a rúd területét a kettős működésű konstrukciókban.
A valóságban a súrlódási veszteségek, a tömítés ellenállása és az áramlási korlátozások miatt, amelyek csökkentik az effektív nyomást, a tényleges erő kimeneti teljesítménye jellemzően 85-90% az elméleti értékhez képest.
Energiaátalakítási folyamat
A hengerek a tárolt folyadékenergiát hasznos mechanikai munkává alakítják. A sűrített levegő vagy a nyomás alatt lévő hidraulikafolyadék potenciális energiát tartalmaz, amely a tágulás során felszabadul.
A pneumatikus (25-35%) és a hidraulikus (85-95%) rendszerek energiahatékonysága a kompressziós veszteségek és a hőtermelés miatt jelentősen eltér.
Az átalakítási folyamat több energiaátalakítást foglal magában: elektromos → kompresszió → folyadéknyomás → mechanikai erő → hasznos munka kimenet.
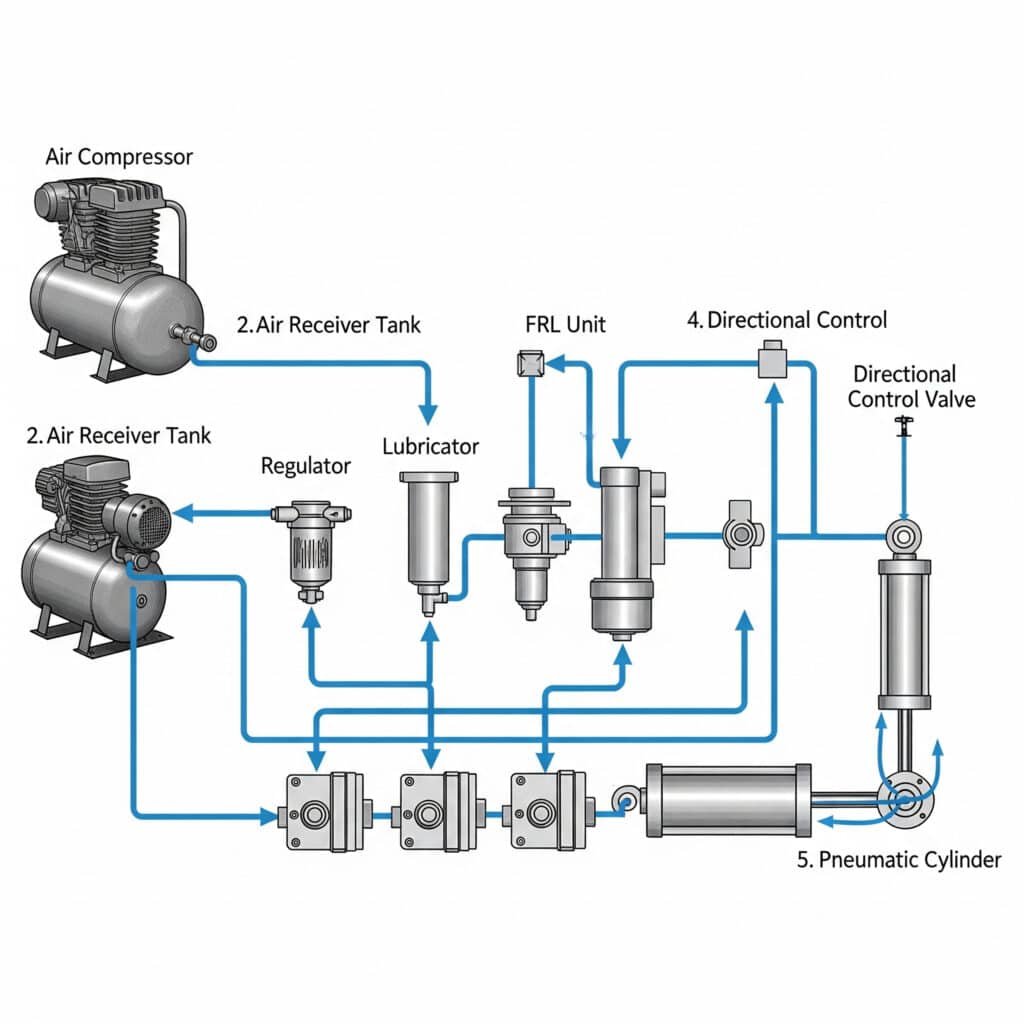
Hogyan működnek együtt a belső komponensek?
A belső alkatrészek kölcsönhatásának megértése megmutatja, hogy a megfelelő karbantartás és a minőségi alkatrészek miért elengedhetetlenek a megbízható működéshez.
A henger belső alkatrészei integrált rendszerként működnek együtt, ahol a hengertest tartalmazza a nyomást, a dugattyú a nyomást erővé alakítja, a tömítések fenntartják a nyomáshatárokat, a rúd pedig az erőt külső terhelésre továbbítja.
Hengertest funkció
A hengertest a munkafolyadékot tartalmazó és a dugattyú mozgását irányító nyomástartó edényként szolgál. A legtöbb hengertest varrat nélküli acélcsövet vagy alumínium extrudálást használ az optimális szilárdság-súly arány érdekében.
A belső felületkezelés döntően befolyásolja a teljesítményt - a 0,4-0,8 Ra felületkezelésű csiszolt furatok sima felületet biztosítanak. tömítés működése2 és meghosszabbított alkatrész-élettartam.
A falvastagságnak megfelelő biztonsági tényezőkkel kell ellenállnia az üzemi nyomásnak. A szabványos ipari hengerek 10-16 bar nyomást kezelnek, 4:1 biztonsági tartalékkal a tervezés során.
A készüléktest anyagai közé tartozik a szénacél az általános használatra, a rozsdamentes acél a korróziós környezetekhez és az alumíniumötvözetek a súlyérzékeny alkalmazásokhoz.
Dugattyú szerelvény működése
A dugattyú mozgatható nyomáshatárként működik, amely a folyadéknyomást lineáris erővé alakítja. A dugattyú kialakítása jelentősen befolyásolja a henger teljesítményét, hatékonyságát és élettartamát.
A dugattyúk anyagai jellemzően alumíniumot használnak a könnyű, gyors működésű alkalmazásokhoz, vagy acélt a nagy teherbírású, nagy erővel járó műveletekhez. Az anyagválasztás befolyásolja a gyorsulási jellemzőket és az erőkapacitást.
A dugattyútömítések hozzák létre a kritikus nyomáshatárt a hengertér között. Az elsődleges tömítések gondoskodnak a nyomás visszatartásáról, míg a másodlagos tömítések megakadályozzák a szivárgást és a szennyeződést.
A dugattyú átmérője közvetlenül meghatározza a leadott erőt az F = P × A összefüggésnek megfelelően. A nagyobb dugattyúk nagyobb erőt fejtenek ki, de nagyobb folyadéktérfogatot és áramlási kapacitást igényelnek.
Pecsét rendszerintegráció
A tömítések integrált rendszerként működnek, ahol minden egyes típus speciális funkciókat lát el. Az elsődleges dugattyútömítések fenntartják a nyomáselválasztást, a rúdtömítések megakadályozzák a külső szivárgást, a törlők pedig eltávolítják a szennyeződéseket.
A tömítőanyagoknak meg kell felelniük az üzemi körülményeknek - NBR az általános használathoz, poliuretán a kopásállósághoz, PTFE a kémiai kompatibilitáshoz és Viton a magas hőmérséklethez.
A tömítés beépítése precíz technikát és megfelelő kenést igényel. A helytelen beépítés azonnali meghibásodást és gyenge teljesítményt okoz, ami kihat az egész rendszerre.
A tömítések teljesítménye közvetlenül befolyásolja a hengerek hatékonyságát, mivel az elhasználódott tömítések csökkentik a teljesítményt és rendszertelen működést okoznak, ami kihat a termelés minőségére.
Rúd és végzáró sapka szerelvény
A dugattyúrúd a henger erejét külső terhelésre továbbítja, miközben fenntartja a nyomástömítés integritását. A rúd kialakításának az alkalmazott erőkkel kell megbirkóznia csavarodás vagy túlzott elhajlás nélkül.
A rudak anyagai közé tartozik a krómozott acél a korrózióállóság érdekében, a rozsdamentes acél a zord környezethez, valamint a speciális ötvözetek a szélsőséges körülményekhez.
A zárókupakok lezárják a hengervégeket és rögzítési pontokat biztosítanak. Meghibásodás vagy szivárgás nélkül kell ellenállniuk a teljes rendszernyomásnak és a külső szerelési terheknek.
A szerelési konfigurációk között szerepelnek a bilincses, a csapszeges, a karimás és a lábas szerelési típusok. A megfelelő rögzítés kiválasztása megakadályozza a feszültségkoncentrációt és az alkatrészek idő előtti meghibásodását.
Komponens | Anyagi lehetőségek | Kulcsfunkció | Hiba hatása |
---|---|---|---|
Hengertest | Acél, alumínium, SS | Nyomáskorlátozás | Teljes rendszerhiba |
Dugattyú | Alumínium, acél | Erőátváltás | Csökkent teljesítmény |
Pecsétek | NBR, PU, PTFE, Viton | Nyomásszigetelés | Szivárgás, szennyeződés |
Rod | Krómacél, SS | Erőátvitel | Terheléskezelési hiba |
Végsőkupakok | Acél, alumínium | A rendszer lezárása | Nyomásveszteség |
Milyen szerepet játszik a nyomás a henger működésében?
A nyomás az alapvető energiaforrás, amely lehetővé teszi a hengerek működését és meghatározza a teljesítményjellemzőket.
A nyomás központi szerepet játszik a henger működésében, mivel a mozgáshoz szükséges hajtóerőt biztosítja, meghatározza a maximális leadott erőt, befolyásolja a működési sebességet, valamint befolyásolja a rendszer hatékonyságát és megbízhatóságát.
A nyomás mint energiaforrás
A sűrített levegő vagy hidraulikafolyadék nyomás alatt tárolt energiát tartalmaz, amely felszabaduláskor mechanikai munkává alakul át. A nagyobb nyomás nagyobb energiát tárol egy térfogategységre vetítve.
A nyomási energiasűrűség a pneumatikus és a hidraulikus rendszerek között drámai eltéréseket mutat. A hidraulikus rendszerek 100-300 bar nyomáson működnek, míg a pneumatikus rendszerek jellemzően 6-10 bar nyomáson.
Az energiafelszabadulás mértéke az áramlási kapacitástól és a nyomáskülönbségtől függ. A gyors nyomásváltozások lehetővé teszik a henger gyors működését, míg a szabályozott kibocsátás egyenletes mozgást biztosít.
A rendszernyomásnak stabilnak kell maradnia az egyenletes teljesítmény érdekében. A nyomásingadozás szabálytalan mozgást és csökkentett erőkifejtést okoz, ami kihat a gyártási minőségre.
Erő kimeneti kapcsolat
A leadott erő közvetlenül korrelál az üzemi nyomással a következő összefüggés szerint: F = P × A. A nyomás megduplázása megduplázza a rendelkezésre álló erőt, így a nyomásszabályozás kritikus a teljesítmény szempontjából.
Az effektív nyomás egyenlő a szelepeken, szerelvényeken és áramláskorlátozásokon keresztüli veszteségekkel csökkentett tápfeszültségi nyomás. A rendszer tervezésénél az optimális teljesítmény érdekében minimalizálni kell ezeket a veszteségeket.
A dugattyún keresztüli nyomáskülönbség határozza meg a nettó erőt. A kipufogóoldalon fellépő ellennyomás csökkenti az effektív nyomást és a rendelkezésre álló erőkifejtést.
A maximális elméleti erő a maximális rendszernyomás és a légköri kipufogógáznyomás között jelentkezik, a lehető legnagyobb nyomáskülönbséget létrehozva.
Sebességszabályozás nyomáson keresztül
A henger fordulatszáma az áramlási sebességtől függ, amely az áramláskorlátozásokon keresztüli nyomáskülönbséggel függ össze. A nagyobb nyomáskülönbségek növelik az áramlási sebességet és a hengerek fordulatszámát.
Az áramlásszabályozó szelepek nyomásesést használnak a sebesség szabályozására. A beáramlásvezérlés a tápáramlást, míg a kimenetvezérlés a kipufogógáz-áramlást korlátozza különböző jellemzők esetén.
A nyomásszabályozás fenntartja az egyenletes sebességet a terhelésváltozások ellenére. Szabályozás nélkül a fordulatszám a változó terheléssel és a tápfeszültségi nyomás ingadozásával változik.
A gyorskiürítő szelepek áthidalják az áramláskorlátozásokat, hogy gyorsítsák a mozgást azáltal, hogy lehetővé teszik a gyors nyomásleadást közvetlenül a légkörbe.
Rendszernyomás-kezelés
A nyomásszabályozók a tápellátás ingadozásai ellenére is fenntartják az állandó üzemi nyomást. Ez biztosítja a megismételhető teljesítményt, és megvédi az alkatrészeket a túlnyomástól.
A nyomáscsökkentő szelepek biztonsági védelmet nyújtanak a rendszer maximális nyomásának korlátozásával. Megakadályozzák a nyomáscsúcsok vagy a rendszer meghibásodásából eredő károkat.
A gyűjtőrendszerek a csúcsigények kezelése és a nyomásingadozások kiegyenlítése érdekében tárolják a nyomás alatt álló folyadékot. Javítják a rendszer reakcióját és hatékonyságát.
A nyomásfigyelés lehetővé teszi a megelőző karbantartást azáltal, hogy a szivárgásokat, eltömődéseket és az alkatrészek károsodását még azelőtt észleli, hogy azok meghibásodást okoznának.
Hogyan működnek a különböző henger típusok?
A különböző hengerkonstrukciók ugyanazon az alapelven működnek, de különböző konfigurációkkal, amelyeket az egyes alkalmazásokhoz és teljesítménykövetelményekhez optimalizáltak.
A különböző hengertípusok ugyanazon a nyomáskülönbség-elv alapján működnek, de a működtetési módszer, a szerelési mód és a belső konfiguráció eltéréseivel, hogy optimalizálják a teljesítményt az adott alkalmazásokhoz és üzemi körülményekhez.
Egyszeres működtetésű henger működése
Az egyszeres működésű hengerek a dugattyúnak csak az egyik oldalára gyakorolnak nyomást, a visszatérő mozgást rugók vagy a gravitáció segítségével végzik. Ez az egyszerű kialakítás csökkenti a levegőfogyasztást és a vezérlés bonyolultságát.
A rugóvisszahúzó hengerek belső nyomórugókkal hajtják vissza a dugattyút, amikor a nyomás megszűnik. A megbízható visszatéréshez a rugóerőnek le kell győznie a súrlódást és a külső terhelést.
A gravitációs visszahúzás a súlyra vagy külső erőkre támaszkodik a visszahúzáshoz. Ez olyan függőleges alkalmazásokhoz illik, ahol a gravitáció rugók nélkül segíti a visszahúzást.
A kimenő erőt a rugóerő korlátozza a kinyúlás során. A rugó csökkenti a külső munkához rendelkezésre álló nettó erőt, így nagyobb hengerek szükségesek az egyenértékű teljesítményhez.
Dupla működtetésű henger működése
A kettős működésű hengerek felváltva gyakorolnak nyomást mindkét oldalra, így mindkét irányban motoros mozgást biztosítanak, független sebesség- és erőszabályozással.
A ki- és behúzási erők különböznek a rúdfelület miatt, amely az egyik oldalon csökkenti a dugattyú hatékony felületét. A kinyújtó erő jellemzően 15-20%-vel nagyobb, mint a behúzó erő.
A független áramlásszabályozás lehetővé teszi az egyes irányok eltérő sebességét, optimalizálva a ciklusidőt a különböző terhelési feltételek és alkalmazási követelmények esetén.
A pozíciótartó képesség kiváló, mivel a nyomás mindkét irányban energiafogyasztás nélkül tartja a pozíciót a külső erőkkel szemben.
Teleszkópos henger funkció
A teleszkópos hengerek több egymásba ágyazott, egymás után kinyúló fokozat segítségével kompakt csomagokban nagy lökethosszúságokat érnek el. Minden fokozat teljesen kinyúlik, mielőtt a következő elkezdődne.
A nyomásirányító rendszerek az egyes fokozatokhoz történő áramlást szabályozó belső csatornákon vagy külső elosztókon keresztül biztosítják a megfelelő sorrendben történő működést.
Az erőkifejtés minden egyes nyújtási szakaszban csökken, mivel a hatásos terület csökken. Az első fokozat maximális erőt, míg az utolsó fokozat minimális erőt biztosít.
A visszahúzás fordított sorrendben történik, az utolsó kihúzott fokozat húzódik vissza először. Ez megőrzi a szerkezeti integritást és megakadályozza a kötést.
Forgódugattyú működése
A forgódugattyús hengerek a lineáris dugattyúmozgást belső fogasléces vagy lapátos mechanizmusokon keresztül alakítják át forgó mozgást igénylő alkalmazásokban forgó kimenetteljesítménnyé.
A fogaskerék- és fogaskerék konstrukciók lineáris dugattyúmozgást használnak egy fogaskerék fogaskerék meghajtására, amely egy fogaskeréktengelyt forgat. A forgási szög a lökethossz és a fogaskerék áttétel függvénye.
A lamellás forgattyús hengerek a lamellákra ható nyomást használják a közvetlen forgó mozgás létrehozására lineáris-rotációs átalakító mechanizmusok nélkül.
A kimeneti nyomaték a nyomástól, a hatásos területtől és a nyomatékkaroktól függ. A nagyobb nyomás és a nagyobb hatásos terület növeli a rendelkezésre álló nyomatékot.
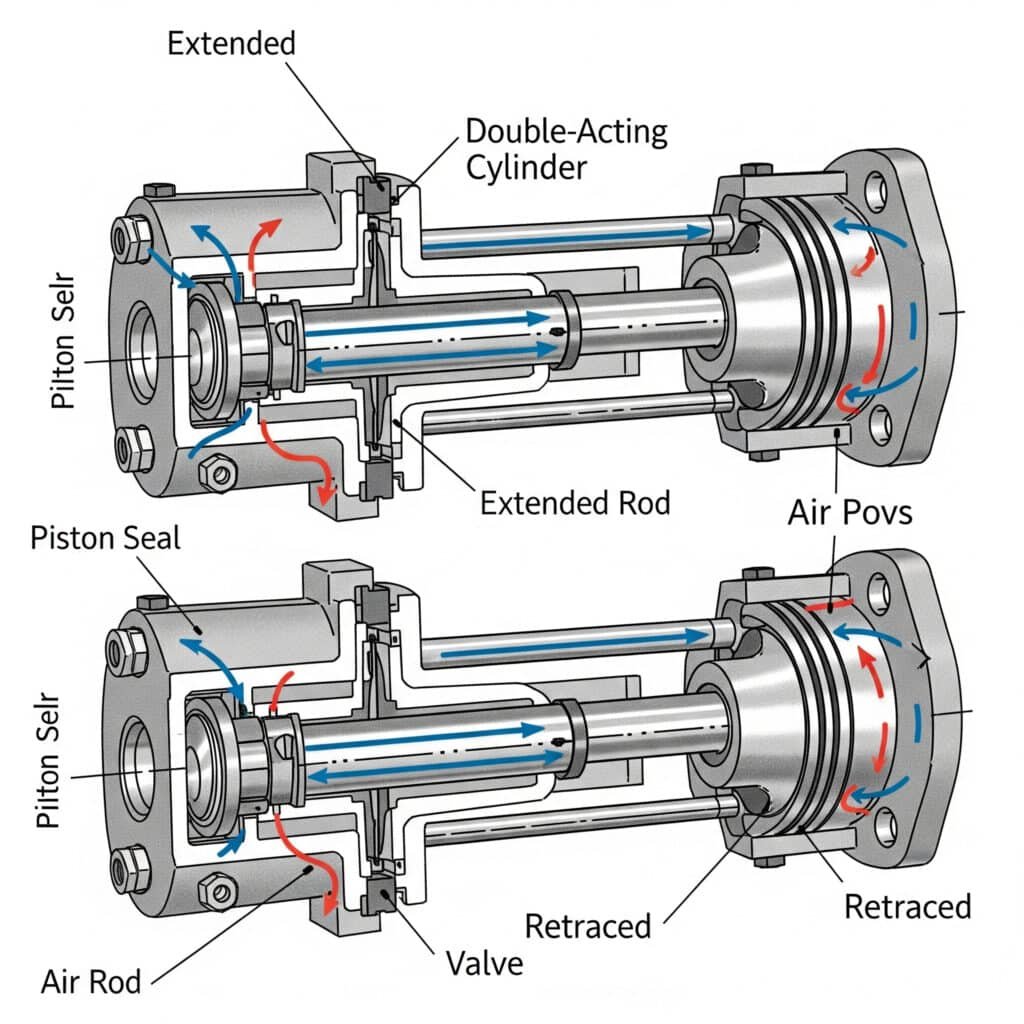
Hogyan működtetik a vezérlőrendszerek a hengereket?
A vezérlőrendszerek a hengerek működését a levegőáramlás, a nyomás és az időzítés kezelésével irányítják a kívánt mozgásprofilok és a rendszer koordinációjának elérése érdekében.
A vezérlőrendszerek a hengerek működését a folyadékáramlás irányának szabályozására szolgáló irányszelepek, a sebesség szabályozására szolgáló áramlásszabályozó szelepek, az erő szabályozására szolgáló nyomásszabályozók, valamint a pontos működéshez visszajelzést adó érzékelők segítségével biztosítják.
Irányváltó szelep működése
Az irányvezérlő szelepek határozzák meg a folyadékáramlási utakat a hengerek kihúzásához vagy behúzásához. Gyakori konfigurációk: 3/2-utas az egyszeresen működő és 5/2-utas a kétszeresen működő hengerekhez.
A szelepek működtetési módszerei közé tartozik a kézi, a pneumatikus vezérlés, a mágnesszelep és a mechanikus működtetés. A választás a vezérlőrendszer követelményeitől és az alkalmazási igényektől függ.
A szelep válaszideje befolyásolja a rendszer teljesítményét a nagy sebességű alkalmazásokban. A gyors működésű szelepek gyors irányváltásokat és pontos időzítésvezérlést tesznek lehetővé.
Az áramlási kapacitásnak meg kell felelnie a henger követelményeinek a kívánt üzemi sebességhez. Az alulméretezett szelepek olyan korlátozásokat hoznak létre, amelyek korlátozzák a teljesítményt és a hatékonyságot.
Áramlásszabályozás integrálása
Az áramlásszabályozó szelepek szabályozzák a folyadék áramlási sebességét a hengerek sebességének és gyorsulási jellemzőinek szabályozásához. A bemeneti adagoló szabályozása a gyorsulást, míg a kimeneti adagoló a lassulást befolyásolja.
A kétirányú áramlásszabályozás lehetővé teszi a sebesség független beállítását a kitoló és behúzó mozgásokhoz, optimalizálva a ciklusidőt a különböző terhelési körülményekhez.
A nyomáskompenzált áramlásszabályozók a nyomásváltozások ellenére is egyenletes fordulatszámot tartanak fenn, így biztosítva a megismételhető teljesítményt a különböző üzemi körülmények között.
Az elektronikus áramlásszabályozás arányos szelepeket használ a pontos, programozható sebességszabályozáshoz, változó gyorsulási és lassulási profilokkal.
Nyomásszabályozó rendszerek
A nyomásszabályozók egyenletes üzemi nyomást biztosítanak a megismételhető erőkifejtés és a stabil teljesítmény érdekében a tápfeszültségi nyomás ingadozásai ellenére.
A nyomáskapcsolók a kamra nyomása alapján egyszerű helyzet-visszacsatolást biztosítanak, érzékelve a löket végét és a rendszer meghibásodását.
Az arányos nyomásszabályozás lehetővé teszi a változó erőkifejtést olyan alkalmazásokhoz, amelyek különböző erőszinteket igényelnek működés közben vagy különböző termékekhez.
A nyomásfigyelő rendszerek még azelőtt észlelik a szivárgásokat, eltömődéseket és az alkatrészek károsodását, mielőtt azok rendszerhibát vagy biztonsági kockázatot okoznának.
Érzékelő integráció
A pozícióérzékelők visszajelzést biztosítanak a zárt hurkú vezérlőrendszerek számára. Az opciók között szerepelnek mágneses reed-kapcsolók, Hall-effektusú érzékelők és lineáris kódolók a különböző pontossági követelményekhez.
A végálláskapcsolók érzékelik a löket véghelyzetét, és biztonsági reteszeléssel megakadályozzák a túlhajtást, és megvédik a rendszerelemeket a károsodástól.
A nyomásérzékelők figyelemmel kísérik a rendszer teljesítményét, és még a meghibásodás előtt észlelik a kialakuló problémákat, például a szivárgásokat, korlátozásokat vagy az alkatrészek kopását.
A hőmérséklet-érzékelők védelmet nyújtanak a túlmelegedés ellen a folyamatos üzemű alkalmazásokban, és adatokat szolgáltatnak a megelőző karbantartási programokhoz.
Rendszerintegrációs képességek
A PLC-integráció lehetővé teszi a koordinációt más gépfunkciókkal a szabványos kommunikációs protokollok és az I/O-kapcsolatok révén az összetett automatizálási rendszerek számára.
A hálózati kapcsolat lehetővé teszi a távoli felügyeletet és vezérlést ipari hálózatok3 mint például Ethernet/IP, Profibus vagy DeviceNet a központi irányításhoz.
A HMI-interfészek érintőképernyős kijelzőkön és grafikus felhasználói felületeken keresztül kezelői vezérlési és rendszerfelügyeleti funkciókat biztosítanak.
Az adatnaplózás a rendszer működésének és karbantartási eljárásainak elemzéséhez, hibaelhárításához és optimalizálásához szükséges teljesítményadatokat rögzíti.
Milyen erők és számítások irányítják a henger működését?
A hengerek működésében szerepet játszó erők és számítások megértése lehetővé teszi a megfelelő méretezést, a teljesítmény előrejelzését és a rendszer optimalizálását.
A hengerek működését erőszámítások (F = P × A), sebességegyenletek (V = Q/A), gyorsuláselemzés (F = ma) és hatékonysági tényezők határozzák meg, amelyek meghatározzák a méretezési követelményeket és a teljesítményjellemzőket.
Alapvető erőszámítások
Az elméleti erő egyenlő a nyomás szorozva a dugattyú effektív területével: Ez az alapvető egyenlet határozza meg az ideális körülmények között elérhető maximális erőt.
A kettős működtetésű hengereknél a hatásos terület eltér a kihúzás és a behúzás között: A_kihúz = π × D²/4, A_visszahúz = π × (D² - d²)/4, ahol D a dugattyú átmérője és d a rúd átmérője.
A gyakorlati erő figyelembe veszi a súrlódás, a tömítés ellenállása és az áramláskorlátozások miatt jellemzően az elméleti hatékonyságveszteség 85-90% közötti értékét.
A kiszámított terhelésekre biztonsági tényezőket kell alkalmazni, jellemzően 1,5-2,5, az alkalmazás kritikusságától és a terhelés bizonytalanságától függően.
Sebesség és áramlási viszonyok
A henger fordulatszáma a térfogatáramhoz kapcsolódik: ahol a sebesség egyenlő az áramlási sebesség osztva a dugattyú effektív felületével.
Az áramlási sebesség a szelep teljesítményétől, a nyomáskülönbségtől és a rendszer korlátozásaitól függ. Az áramlási korlátozások a rendszerben bárhol csökkentik a maximálisan elérhető sebességet.
A gyorsulási idő a nettó erőtől és a mozgó tömegtől függ: t = (V × m)/F_net, ahol a nagyobb nettó erő gyorsabb gyorsulást tesz lehetővé a kívánt sebességre.
A lassulási jellemzők a kipufogógáz-áramlási kapacitástól és az ellennyomástól függenek. A lökésszerű terhelések elkerülése érdekében a csillapító rendszerek szabályozzák a lassulást.
Terheléselemzési követelmények
A statikus terhelések közé tartozik az alkatrész súlya, a folyamat erői és a súrlódás. A mozgás megkezdése előtt minden statikus erőt le kell győzni.
A dinamikus terhelések a mozgás során gyorsulási erőket adnak hozzá: ahol a gyorsulási erők jelentősen meghaladhatják a statikus terhelést.
Az oldalirányú terheléseket és nyomatékokat figyelembe kell venni a megfelelő vezető rendszer méretezéséhez. A hengerek oldalirányú terhelhetősége külső vezetők nélkül korlátozott.
A kombinált terheléselemzés biztosítja, hogy minden erőösszetevő a henger és a rendszer képességein belül legyen a megbízható működéshez.
Levegőfogyasztási számítások
A ciklusonkénti levegőfogyasztás egyenlő a henger térfogatának és a nyomásaránynak a szorzatával: V_levegő = V_henger × (P_abszolút/P_légköri).
A kettős működésű hengerek mindkét lökethez, míg az egyszerű működésű hengerek csak a hajtott löket irányához fogyasztanak levegőt.
A rendszer szelepeken, szerelvényeken és szivárgásokon keresztüli veszteségei általában 20-30%-t tesznek hozzá az elméleti fogyasztási értékekhez.
A kompresszorok méretezésének a csúcsigényt és a veszteségeket kell kezelniük, megfelelő tartalékkapacitással, hogy megakadályozzák a nyomásesést működés közben.
Teljesítmény optimalizálás
A furatméret kiválasztása egyensúlyban tartja az erőigényt a sebességgel és a levegőfogyasztással. A nagyobb furatok nagyobb erőt biztosítanak, de több levegőt fogyasztanak és lassabban mozoghatnak.
A löket hossza befolyásolja a levegőfogyasztást és a reakcióidőt. A hosszabb löketek nagyobb levegőmennyiséget és hosszabb töltési időt igényelnek a mozgás elindításához.
Az üzemi nyomás optimalizálása figyelembe veszi az erőszükségletet, az energiaköltségeket és az alkatrészek élettartamát. A nagyobb nyomás csökkenti a henger méretét, de növeli az energiafogyasztást.
A rendszer hatékonysága javul a komponensek megfelelő méretezésével, a minimális nyomáseséssel és a hatékony légkezeléssel, amely csökkenti a veszteségeket és a karbantartást.
Paraméter | Számítás | Egységek | Tipikus értékek |
---|---|---|---|
Erő | F = P × A | Newtons | 500-50,000N |
Sebesség | V = Q/A | m/s | 0,1-10 m/s |
Levegőfogyasztás | V = löket × terület × nyomásarány | liter/ciklus | 1-50 L/ciklus |
Teljesítmény | P = F × V | Watts | 100-10,000W |
Hogyan befolyásolják a környezeti tényezők a henger működését?
A környezeti feltételek jelentősen befolyásolják a hengerek teljesítményét, megbízhatóságát és élettartamát különböző mechanizmusok révén, amelyeket a rendszer tervezésekor figyelembe kell venni.
A környezeti tényezők befolyásolják a henger működését a folyadék tulajdonságait és a tömítések teljesítményét megváltoztató hőmérséklet-változások, a kopást és meghibásodást okozó szennyeződések, a korróziót okozó páratartalom és az alkatrészek fáradását felgyorsító rezgés révén.
A hőmérséklet hatása a működésre
Az üzemi hőmérséklet befolyásolja a folyadék viszkozitását, sűrűségét és nyomását. A magasabb hőmérséklet csökkenti a levegő sűrűségét és a pneumatikus rendszerek hatékony erőleadásának mértékét.
A tömítőanyagoknak vannak a teljesítményt és az élettartamot befolyásoló hőmérsékleti határértékei. A szabványos NBR tömítések -20°C és +80°C között működnek, míg a speciális anyagok kiterjesztik a hőmérsékleti tartományt.
Az alkatrészek hőtágulása befolyásolhatja a hézagokat és a tömítés teljesítményét. A kialakításnak figyelembe kell vennie a hőnövekedést, hogy megakadályozza a kötést vagy a túlzott kopást.
Kondenzáció akkor keletkezik, amikor a sűrített levegő a harmatponti hőmérséklet alá hűl. A víz felhalmozódása korróziót, fagyást és hibás működést okoz.
Szennyezés hatásai
A por és a törmelék tömítések kopását, szelepek beragadását és belső alkatrészek károsodását okozza. A szennyeződés a hengerek idő előtti meghibásodásának vezető oka.
A részecskeméret befolyásolja a károsodás súlyosságát - a tömítés távolságánál nagyobb részecskék azonnali károsodást, míg a kisebb részecskék fokozatos kopást okoznak.
A vegyi szennyeződés megtámadja a tömítéseket és korróziót okoz. Az anyagkompatibilitás kritikus a vegyszereket, oldószereket vagy technológiai folyadékokat tartalmazó környezetben.
A nedvesség okozta szennyeződés a belső alkatrészek korrózióját okozza, hidegben pedig megfagyhat, elzárva a légutakat és megakadályozva a működést.
Páratartalom és korrózió
A magas páratartalom növeli a sűrített levegős rendszerekben a kondenzáció kockázatát. A vízgőz a levegő lehűlésekor lecsapódik, és folyékony víz keletkezik a rendszerben.
A korrózió az acél alkatrészeket érinti, és lyukacsosodást, vízkőlerakódást és végső soron meghibásodást okozhat. A rozsdamentes acél vagy a védőbevonatok megakadályozzák a korróziós károkat.
Galvanikus korrózió akkor keletkezik, amikor különböző fémek nedvesség jelenlétében érintkeznek egymással. A megfelelő anyagválasztás megelőzi a galvanikus korróziós problémákat.
A vízelvezető rendszereknek el kell távolítaniuk a felgyülemlett vizet a rendszer alacsony pontjairól. Az automatikus lefolyók megakadályozzák a működési problémákat okozó vízfelhalmozódást.
Rázkódás és ütéshatások
A mechanikus rezgés a kötőelemek meglazulását, a tömítések elmozdulását és az alkatrészek kifáradását okozza. A megfelelő szerelés és szigetelés véd a rezgéskárok ellen.
A gyors irányváltásokból vagy külső behatásokból származó lökésszerű terhelések károsíthatják a belső alkatrészeket. A csillapító rendszerek csökkentik a lökésszerű terhelést és meghosszabbítják az élettartamot.
A rezonancia felerősíti a rezgéshatásokat, ha a működési frekvenciák megegyeznek az alkatrészek sajátfrekvenciáival. A tervezésnek el kell kerülnie a rezonanciás állapotokat.
Az alapítvány stabilitása befolyásolja a rendszer teljesítményét. A merev rögzítés megakadályozza a túlzott rezgést, míg a rugalmas rögzítés szigetelést biztosít.
Magasság és nyomás hatása
A nagy tengerszint feletti magasság csökkenti a légköri nyomást, ami befolyásolja a pneumatikus hengerek teljesítményét. A légköri ellennyomás csökkenésével csökken a leadott erő.
A nyomáskülönbség-számításokban figyelembe kell venni a magassági hatásokat. A tengerszint feletti számítások nem alkalmazhatók közvetlenül a nagy magasságú létesítményeknél.
A levegő sűrűsége a magassággal csökken, ami csökkenti a tömegáramot és befolyásolja a henger fordulatszám-karakterisztikát állandó térfogatáram mellett.
A kompresszor teljesítménye szintén csökken a tengerszint feletti magassággal, ami nagyobb kompresszorokat vagy nagyobb üzemi nyomást igényel a rendszer teljesítményének fenntartásához.
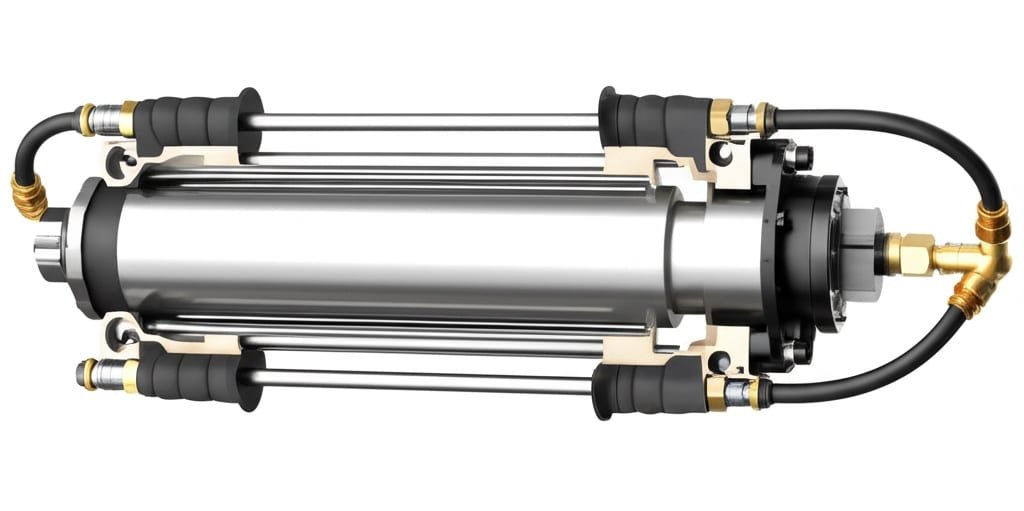
Milyen gyakori problémák akadályozzák a henger megfelelő működését?
A gyakori problémák és kiváltó okaik megértése lehetővé teszi a hatékony hibaelhárítást és a megelőző karbantartási stratégiákat.
A gyakori hengerproblémák közé tartozik a tömítés szivárgása, ami erőveszteséget okoz, a szennyeződés, ami szabálytalan mozgást okoz, a nem megfelelő méretezés, ami gyenge teljesítményt eredményez, és a nem megfelelő teljesítmény. légkezelés4 ami az alkatrészek idő előtti meghibásodásához vezet.
Tömítéssel kapcsolatos problémák
A kamrák közötti belső szivárgás csökkenti a leadott erőt és lassú működést okoz. A teljesítménycsökkenés leggyakoribb oka az elhasználódott dugattyútömítések.
A rúd körüli külső szivárgás biztonsági kockázatot jelent és pazarolja a sűrített levegőt. A rúdtömítés meghibásodása általában szennyeződés vagy felületi sérülés következménye.
A tömítés extrudálása akkor következik be, amikor a tömítések nagy nyomás alatt a hézagokba kényszerülnek. Ez károsítja a tömítéseket és állandó szivárgási utakat hoz létre.
A tömítés hő- vagy vegyszerhatás miatti megkeményedése csökkenti a rugalmasságot és a tömítés hatékonyságát. A megfelelő anyagválasztás megelőzi a kémiai kompatibilitási problémákat.
Szennyezési kérdések
A részecskeszennyezés felgyorsítja a tömítés kopását és szelephibát okoz. A nem megfelelő szűrés a szennyeződési problémák elsődleges oka.
A vízszennyezés korróziót okoz, és hidegben megfagyhat. A megfelelő légszárítás megelőzi a vízzel kapcsolatos problémákat és meghosszabbítja az alkatrészek élettartamát.
A kompresszorokból származó olajszennyezés tömítésduzzadást és -romlást okoz. Az olajmentes kompresszorok vagy a hatékony olajeltávolítás megakadályozza a szennyeződést.
A vegyi szennyeződések megtámadják a tömítéseket és a fém alkatrészeket. Az anyagkompatibilitási elemzés megakadályozza a vegyi károsodást a zord környezetben.
Méretezési és alkalmazási problémák
Az alulméretezett hengerek nem képesek megfelelő erőt kifejteni az alkalmazáshoz, ami lassú működéshez vagy a munkaciklus befejezésének ellehetetlenüléséhez vezet.
A túlméretezett hengerek energiát pazarolnak, és a megfelelő vezérléshez túl gyorsan működhetnek. A megfelelő méretezés optimalizálja a teljesítményt és az energiahatékonyságot.
A nem megfelelő vezetőrendszerek oldalirányú terhelést tesznek lehetővé, ami kötést és idő előtti kopást okoz. Oldalirányú terhelés esetén külső vezetőkre lehet szükség.
A helytelen szerelés feszültségkoncentrációkat és helytelen igazodást eredményez, amelyek felgyorsítják az alkatrészek kopását és csökkentik a rendszer megbízhatóságát.
Rendszertervezési kérdések
A nem megfelelő áramlási kapacitás korlátozza a hengerek sebességét, és nyomásesést okoz, ami csökkenti az erőterhelést és a rendszer hatékonyságát.
A rossz szelepválasztás befolyásolja a válaszidőt és az áramlási jellemzőket. A szelep teljesítményének meg kell felelnie a henger követelményeinek az optimális teljesítmény érdekében.
A nem megfelelő légkezelés lehetővé teszi, hogy a szennyeződés és a nedvesség károsítsa az alkatrészeket. A megfelelő szűrés és szárítás elengedhetetlen a megbízhatósághoz.
A nem megfelelő nyomásszabályozás rendszertelen teljesítményt okoz, és túlnyomásos körülmények miatt károsíthatja az alkatrészeket.
Karbantartással kapcsolatos problémák
A ritkán elvégzett szűrőcserék lehetővé teszik a szennyeződések felhalmozódását, amelyek károsítják az alkatrészeket, és csökkentik a rendszer megbízhatóságát és teljesítményét.
A nem megfelelő kenés megnövekedett súrlódást és gyorsabb kopást okoz. Mind az alul-, mind a túlkenés problémákat okoz.
A késedelmes tömítéscsere lehetővé teszi, hogy a kisebb szivárgások nagyobb meghibásodásokká váljanak, amelyek kiterjedt javításokat igényelnek és hosszabb állásidőt okoznak.
A teljesítményfigyelés hiánya megakadályozza a kialakuló problémák korai észlelését, amelyeket még a meghibásodást okozó hibák előtt ki lehetne javítani.
Probléma kategória | Tünetek | Gyökeres okok | Megelőzési módszerek |
---|---|---|---|
Pecsét meghibásodása | Szivárgás, csökkentett erő | Szennyeződés, kopás | Tiszta levegő, megfelelő anyagok |
Szennyezés | Szabálytalan mozgás, tapadás | Gyenge szűrés | Megfelelő légkezelés |
Méretezési kérdések | Gyenge teljesítmény | Helytelen kiválasztás | Megfelelő számítások |
Rendszerproblémák | Következetlen működés | Tervezési hiányosságok | Professzionális tervezés |
Karbantartás | Korai kudarc | Elhanyagolás | Ütemezett karbantartás |
Hogyan integrálódnak a modern hengerek az automatizálási rendszerekbe?
A modern hengerek fejlett technológiákat és kommunikációs képességeket tartalmaznak, amelyek lehetővé teszik a kifinomult automatizálási rendszerekbe való zökkenőmentes integrációt.
A modern hengerek a beágyazott érzékelők révén integrálódnak az automatizálási rendszerekbe a pozíció-visszacsatoláshoz, az elektronikus vezérlés a precíz működéshez, a kommunikációs protokollok a hálózati csatlakoztathatósághoz, valamint a diagnosztikai képességek a megelőző karbantartáshoz.
Érzékelő integrációs technológiák
A beágyazott helyzetérzékelők kiküszöbölik a külső érzékelési követelményeket, miközben pontos helyzet-visszacsatolást biztosítanak a zárt hurkú vezérlőrendszerek számára.
A mágneses érzékelők a henger falán keresztül érzékelik a dugattyú helyzetét Hall-effektus vagy magnetorezisztív technológiák segítségével, amelyek analóg helyzetjeleket szolgáltatnak.
A külső futóművekre szerelt optikai kódolók a legnagyobb felbontású pozíció-visszacsatolást biztosítják a precíziós pozicionálási alkalmazásokhoz.
A nyomásérzékelők figyelik a kamra nyomását az erővisszacsatolás és a diagnosztikai információk érdekében, amelyek lehetővé teszik a fejlett vezérlési stratégiákat és az állapotfelügyeletet.
Elektronikus vezérlés integrálása
A szervoszelepek elektromos parancsjelek alapján arányos áramlásszabályozást biztosítanak, lehetővé téve a pontos sebesség- és pozíciószabályozást programozható profilokkal.
Az elektronikus nyomásszabályozás arányos nyomásszelepekkel biztosítja a változó erőleadást és a nyomásszabályozást az egyenletes teljesítmény érdekében.
Az integrált vezérlők a szelepvezérlést, az érzékelőfeldolgozást és a kommunikációs funkciókat kompakt csomagokban egyesítik, amelyek egyszerűsítik a rendszerintegrációt.
A terepi buszcsatlakozás olyan elosztott vezérlési architektúrákat tesz lehetővé, ahol az egyes palackok közvetlenül kommunikálnak a központi vezérlőrendszerekkel.
Kommunikációs protokoll támogatás
Az ipari Ethernet protokollok, köztük az EtherNet/IP, a Profinet és az EtherCAT nagy sebességű kommunikációt és valós idejű vezérlési koordinációt tesznek lehetővé.
Az olyan terepi buszprotokollok, mint a DeviceNet, a Profibus és a CANopen robusztus kommunikációt biztosítanak az elosztott vezérlési alkalmazásokhoz.
A vezeték nélküli kommunikációs lehetőségek lehetővé teszik a mobil vagy távoli palackok felügyeletét és vezérlését fizikai kábelkapcsolat nélkül.
Az OPC-UA támogatás szabványosított kommunikációt biztosít az Ipar 4.0 alkalmazásokhoz és a vállalati rendszerekkel való integrációhoz.
Diagnosztikai és felügyeleti képességek
A beépített diagnosztika figyeli a teljesítményparamétereket és az alkatrészek állapotát a megelőző karbantartás lehetővé tétele és a váratlan meghibásodások megelőzése érdekében.
A rezgésfelügyelet még azelőtt észleli a kialakuló mechanikai problémákat, mint például a csapágykopás, a rossz beállítás vagy a rögzítési problémák, mielőtt azok meghibásodást okoznának.
A hőmérséklet-felügyelet véd a túlmelegedés ellen, és adatokat szolgáltat a hőelemzéshez és a rendszer optimalizálásához.
A használat nyomon követése rögzíti a ciklusok számát, az üzemórákat és a teljesítménytendenciákat a karbantartás ütemezéséhez és az életciklus-elemzéshez.
Ipar 4.0 integráció
Az IoT-kapcsolat lehetővé teszi a távfelügyeletet és -vezérlést a felhőalapú platformokon keresztül, amelyek globális hozzáférést biztosítanak a rendszerinformációkhoz.
Az adatelemzési képességek feldolgozzák az üzemeltetési adatokat az optimalizálási lehetőségek azonosítása és a karbantartási követelmények előrejelzése érdekében.
A digitális iker integráció a fizikai hengerek virtuális modelljeit hozza létre szimulációhoz, optimalizáláshoz és előrejelző elemzéshez.
A gépi tanulási algoritmusok a működési adatokat elemzik a teljesítmény optimalizálása és az alkatrészek meghibásodásának előrejelzése érdekében, mielőtt azok bekövetkeznének.
Biztonsági rendszer integrálása
A biztonsági besorolású érzékelők és vezérlők megfelelnek a funkcionális biztonsági követelményeknek az olyan alkalmazásokban, amelyek megkövetelik a következőket SIL-besorolású biztonság5 funkciók.
Az integrált biztonsági funkciók közé tartozik a biztonságos leállítás, a biztonságos pozíciófelügyelet és a biztonságos sebességfelügyelet, amelyek kiküszöbölik a külső biztonsági eszközök használatát.
A redundáns rendszerek biztonsági tartalék működést és felügyeletet biztosítanak olyan kritikus biztonsági alkalmazásokhoz, ahol a meghibásodás sérülést vagy kárt okozhat.
A biztonsági kommunikációs protokollok biztosítják a biztonság szempontjából kritikus információk megbízható továbbítását a rendszerelemek között.
Következtetés
A hengerek a Pascal-törvény elegáns alkalmazásával működnek, a folyadéknyomást precíz lineáris mozgássá alakítva a belső alkatrészek, a vezérlőrendszerek és a környezetvédelmi jellemzők összehangolt működésével, amelyek számtalan ipari alkalmazásban lehetővé teszik a megbízható automatizálást.
GYIK a hengerek működéséről
Hogyan működik egy pneumatikus henger?
A pneumatikus henger úgy működik, hogy a dugattyú felületére ható sűrített levegő nyomása lineáris erőt hoz létre az F = P × A egyenletnek megfelelően, a dugattyú és a csatlakoztatott rúd kitolását vagy behúzását irányszelepek vezérlik, amelyek a levegő áramlását szabályozzák.
Mi a hengerek működésének alapelve?
Az alapelv a Pascal-törvény, amely szerint a korlátozott folyadékra kifejtett nyomás minden irányban egyformán terjed, és erőt hoz létre, amikor a nyomáskülönbség a hengerben lévő mozgatható dugattyúfelületen keresztül hat.
Miben különbözik az egyszeresen és a kétszeresen működő hengerek működése?
Az egyszeresen működő hengerek egy irányban légnyomást használnak, rugós vagy gravitációs visszatéréssel, míg a kétszeresen működő hengerek a légnyomást használják mind a kitoló, mind a behúzó mozgásokhoz, mindkét irányban motoros mozgást biztosítva.
Milyen szerepet játszanak a tömítések a henger működésében?
A tömítések fenntartják a henger kamrák közötti nyomáshatárokat, megakadályozzák a külső szivárgást a rúd körül, és megakadályozzák a szennyeződések bejutását, lehetővé téve a megbízható működéshez szükséges megfelelő nyomáskülönbség és erőfejlesztést.
Hogyan számolja ki a henger erőterhelését?
Számítsa ki a henger erejét az F = P × A értékkel, ahol az erő egyenlő a légnyomás és a dugattyú effektív felületének szorzatával, figyelembe véve a rúd felületének csökkenését a visszahúzásnál és a 10-15% hatásfokveszteséget.
Mi okozza a hengerek nem megfelelő működését?
A leggyakoribb okok közé tartozik a tömítés szivárgása, amely csökkenti az erőteljesítményt, a szabálytalan mozgást okozó szennyeződés, az alkalmazáshoz nem megfelelő méretezés, a nem megfelelő légkezelés és a rossz karbantartás, amely lehetővé teszi az alkatrészek degradációját.
Hogyan integrálódnak a modern hengerek az automatizálási rendszerekbe?
A modern hengerek a beágyazott érzékelőkkel integrálódnak a pozíció-visszacsatoláshoz, az elektronikus vezérléssel a pontos működéshez, a hálózati csatlakoztathatóságot biztosító kommunikációs protokollokkal, valamint a diagnosztikai képességekkel a prediktív karbantartáshoz és az Ipar 4.0 alkalmazásokhoz.
Milyen környezeti tényezők befolyásolják a hengerek működését?
A környezeti tényezők közé tartozik a folyadék tulajdonságait és a tömítés teljesítményét befolyásoló hőmérséklet, a kopást és meghibásodást okozó szennyeződés, a korróziót okozó nedvesség, a fáradást gyorsító rezgés, valamint a nyomáskülönbségeket és a teljesítményt befolyásoló magasság.
Lábjegyzetek
-
Tudjon meg többet a Pascal-törvényről és annak a folyadékmechanikában betöltött alapvető szerepéről. ↩
-
Ismerje meg az ipari hengerekben használt különböző típusú tömítéseket és azok alkalmazási területeit. ↩
-
Ismerje meg az automatizálási rendszerek nagysebességű kommunikációjához használt különböző ipari Ethernet protokollokat. ↩
-
A sűrített levegő minőségére vonatkozó nemzetközi szabványok és azok fontosságának megértése a pneumatikus rendszerekben. ↩
-
Megérti a funkcionális biztonság biztonsági szintjeit (SIL) és azok jelentőségét az ipari automatizálásban. ↩