
Setiap insinyur keselamatan yang saya ajak berkonsultasi menghadapi tantangan yang sama: sistem keselamatan pneumatik standar sering kali gagal memberikan perlindungan yang memadai dalam aplikasi berisiko tinggi. Anda mungkin pernah mengalami kecemasan akibat nyaris celaka, frustrasi akibat penundaan produksi karena gangguan, atau yang lebih buruk lagi - kehancuran akibat insiden keselamatan yang sebenarnya meskipun telah memiliki sistem yang "sesuai". Kekurangan ini membuat pekerja rentan dan perusahaan terpapar pada tanggung jawab yang signifikan.
Sistem keamanan pneumatik yang paling efektif menggabungkan respons darurat yang cepat katup penghenti (di bawah 50ms), dirancang dengan baik Nilai SIL1 sirkuit keselamatan dengan redundansi, dan mekanisme penguncian tekanan ganda yang tervalidasi. Pendekatan komprehensif ini biasanya mengurangi risiko cedera serius hingga 96-99% dibandingkan dengan sistem yang berfokus pada kepatuhan dasar.
Bulan lalu, saya bekerja dengan sebuah fasilitas manufaktur di Ontario yang mengalami cedera serius ketika sistem keselamatan pneumatik standar mereka gagal mencegah gerakan tak terduga selama pemeliharaan. Setelah menerapkan pendekatan keselamatan kami yang komprehensif, mereka tidak hanya menghilangkan insiden keselamatan, tetapi juga meningkatkan produktivitas sebesar 14% karena berkurangnya waktu henti akibat perjalanan yang mengganggu dan prosedur akses pemeliharaan yang lebih baik.
Daftar Isi
- Standar Waktu Respons Katup Penghenti Darurat
- Spesifikasi Desain Sirkuit Keselamatan Tingkat SIL
- Proses Validasi Mekanisme Penguncian Tekanan Ganda
- Kesimpulan
- Tanya Jawab Tentang Sistem Keselamatan Pneumatik
Berapa Waktu Tanggap yang Sebenarnya Dibutuhkan Katup Penghenti Darurat untuk Mencegah Cedera?
Banyak insinyur keselamatan memilih katup penghenti darurat terutama berdasarkan kapasitas aliran dan biaya, dengan mengabaikan faktor kritis waktu respons. Kelalaian ini dapat menimbulkan konsekuensi bencana ketika milidetik dapat membuat perbedaan antara nyaris celaka dan cedera serius.
Katup penghenti darurat yang efektif untuk sistem pneumatik harus mencapai penutupan penuh dalam waktu 15-50 ms tergantung pada tingkat risiko aplikasi, mempertahankan kinerja yang konsisten selama masa pakai, dan menyertakan kemampuan pemantauan untuk mendeteksi degradasi. Desain yang paling andal menggabungkan solenoida ganda dengan posisi spul yang dipantau secara dinamis dan arsitektur kontrol yang tahan terhadap kesalahan.
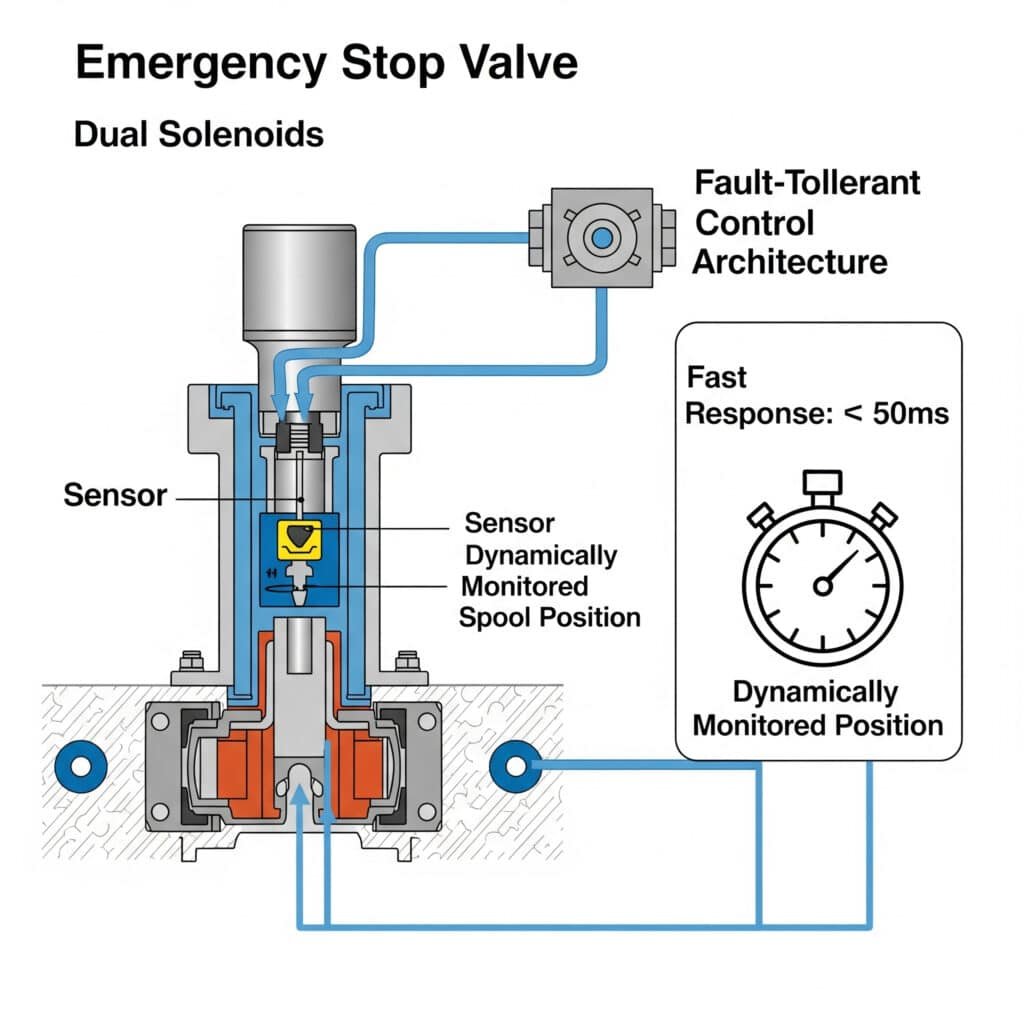
Standar Waktu Respons Komprehensif untuk Katup Penghenti Darurat
Setelah menganalisis ratusan insiden keselamatan pneumatik dan melakukan pengujian ekstensif, saya telah mengembangkan standar waktu respons khusus aplikasi ini:
Kategori Risiko | Waktu Respons yang Dibutuhkan | Teknologi Katup | Persyaratan Pemantauan | Frekuensi Pengujian | Aplikasi Khas |
---|---|---|---|---|---|
Risiko Ekstrim | 10-15ms | Dipantau secara dinamis, solenoida ganda | Pemantauan siklus berkelanjutan, deteksi kesalahan | Bulanan | Pengepresan berkecepatan tinggi, sel kerja robotik, pemotongan otomatis |
Risiko Tinggi | 15-30ms | Dipantau secara dinamis, solenoida ganda | Umpan balik posisi, deteksi kesalahan | Triwulanan | Peralatan penanganan material, perakitan otomatis, mesin pengemasan |
Risiko Sedang | 30-50ms | Dipantau statis, solenoida ganda | Umpan balik posisi | Setengah tahunan | Sistem konveyor, otomatisasi sederhana, pemrosesan material |
Risiko Rendah | 50-100ms | Solenoid tunggal dengan pegas kembali | Umpan balik posisi dasar | Setiap tahun | Aplikasi yang tidak berbahaya, perkakas sederhana, sistem bantu |
Metodologi Pengukuran dan Validasi Waktu Respons
Untuk memvalidasi kinerja katup penghenti darurat dengan benar, ikuti protokol pengujian komprehensif ini:
Fase 1: Karakterisasi Waktu Respons Awal
Menetapkan kinerja dasar melalui pengujian yang ketat:
Sinyal Listrik ke Gerakan Awal
Ukur penundaan antara penghentian energi listrik dan gerakan katup yang pertama kali terdeteksi:
- Gunakan akuisisi data berkecepatan tinggi (pengambilan sampel minimum 1kHz)
- Uji pada tegangan suplai minimum, nominal, dan maksimum
- Ulangi pengukuran pada tekanan operasi minimum, nominal, dan maksimum
- Lakukan minimal 10 siklus untuk menetapkan validitas statistik
- Menghitung waktu respons rata-rata dan maksimumPengukuran Waktu Perjalanan Penuh
Tentukan waktu yang diperlukan untuk penutupan katup sepenuhnya:
- Gunakan sensor aliran untuk mendeteksi penghentian aliran sepenuhnya
- Mengukur kurva peluruhan tekanan di bagian hilir katup
- Hitung waktu penutupan efektif berdasarkan pengurangan aliran
- Uji dalam berbagai kondisi aliran (25%, 50%, 75%, 100% aliran terukur)
- Mendokumentasikan skenario respons kasus terburukValidasi Respons Sistem
Mengevaluasi kinerja fungsi keselamatan secara menyeluruh:
- Mengukur waktu dari peristiwa pemicu hingga penghentian gerakan berbahaya
- Sertakan semua komponen sistem (sensor, pengontrol, katup, aktuator)
- Uji di bawah kondisi beban yang realistis
- Mendokumentasikan waktu respons fungsi keselamatan total
- Bandingkan dengan persyaratan jarak aman yang dihitung
Tahap 2: Pengujian Lingkungan dan Kondisi
Verifikasi kinerja di seluruh lingkungan operasi:
Analisis Efek Suhu
Menguji waktu respons di seluruh rentang suhu penuh:
- Performa start dingin (suhu pengenal minimum)
- Pengoperasian suhu tinggi (suhu pengenal maksimum)
- Skenario perubahan suhu dinamis
- Efek siklus termal pada konsistensi responsPengujian Variasi Pasokan
Mengevaluasi kinerja dalam kondisi pasokan yang tidak ideal:
- Tekanan suplai yang berkurang (minimum yang ditentukan -10%)
- Tekanan suplai yang meningkat (maksimum yang ditentukan +10%)
- Fluktuasi tekanan selama pengoperasian
- Udara suplai yang terkontaminasi (memperkenalkan kontaminasi terkontrol)
- Fluktuasi tegangan (±10% dari nominal)Penilaian Kinerja Daya Tahan
Verifikasi konsistensi respons jangka panjang:
- Pengukuran waktu respons awal
- Siklus hidup yang dipercepat (minimal 100.000 siklus)
- Pengukuran waktu respons berkala selama bersepeda
- Verifikasi waktu respons akhir
- Analisis statistik penyimpangan waktu respons
Tahap 3: Pengujian Mode Kegagalan
Mengevaluasi kinerja selama kondisi kegagalan yang dapat diperkirakan:
Pengujian Skenario Kegagalan Sebagian
Menilai respons selama degradasi komponen:
- Degradasi solenoida yang disimulasikan (daya berkurang)
- Obstruksi mekanis parsial
- Peningkatan gesekan melalui kontaminasi yang terkendali
- Gaya pegas yang berkurang (jika ada)
- Simulasi kegagalan sensorAnalisis Kegagalan Penyebab Umum
Menguji ketahanan terhadap kegagalan sistemik:
- Gangguan catu daya
- Gangguan suplai tekanan
- Kondisi lingkungan yang ekstrem
- Pengujian interferensi EMC/EMI
- Pengujian getaran dan guncangan
Studi Kasus: Peningkatan Keselamatan Operasi Stamping Logam
Sebuah fasilitas pencetakan logam di Pennsylvania mengalami insiden nyaris celaka ketika sistem keamanan mesin cetak pneumatik mereka gagal merespons dengan cukup cepat selama situasi penghentian darurat. Katup yang ada memiliki waktu respons terukur 85ms, yang memungkinkan mesin cetak melanjutkan gerakan selama 38mm setelah tirai cahaya dipicu.
Kami melakukan penilaian keselamatan yang komprehensif:
Analisis Sistem Awal
- Kecepatan penutupan tekan: 450mm/detik
- Waktu respons katup yang ada: 85ms
- Total waktu respons sistem: 115ms
- Gerakan setelah deteksi: 51,75mm
- Performa penghentian yang aman yang diperlukan: <10mm gerakan
Implementasi Solusi
Kami merekomendasikan dan menerapkan perbaikan ini:
Komponen | Spesifikasi Asli | Spesifikasi yang Ditingkatkan | Peningkatan Kinerja |
---|---|---|---|
Katup Penghenti Darurat | Solenoida tunggal, respons 85ms | Solenoida yang dipantau ganda, respons 12ms | 85.9% respons lebih cepat |
Arsitektur Kontrol | Logika relai dasar | PLC Keselamatan dengan diagnostik | Pemantauan dan redundansi yang ditingkatkan |
Posisi Pemasangan | Jauh dari aktuator | Pemasangan langsung ke silinder | Mengurangi penundaan transmisi pneumatik |
Kapasitas Knalpot | Knalpot standar | Knalpot cepat aliran tinggi | Pelepasan tekanan 3,2x lebih cepat |
Sistem Pemantauan | Tidak ada | Pemantauan posisi katup dinamis | Deteksi kesalahan waktu nyata |
Hasil Validasi
Setelah diimplementasikan, sistem ini berhasil:
- Waktu respons katup: 12ms (peningkatan 85,9%)
- Total waktu respons sistem: 28ms (peningkatan 75,7%)
- Gerakan setelah deteksi: 12,6 mm (peningkatan 75,7%)
- Sistem sekarang sesuai dengan ISO 138552 persyaratan jarak aman
- Manfaat tambahan: Pengurangan 22% dalam perjalanan gangguan karena diagnostik yang lebih baik
Praktik-praktik Terbaik Implementasi
Untuk kinerja katup penghenti darurat yang optimal:
Kriteria Pemilihan Katup
Fokuslah pada spesifikasi penting ini:
- Dokumentasi waktu respons yang terverifikasi (bukan hanya klaim katalog)
- Nilai B10d3 atau peringkat MTTFd yang sesuai untuk Tingkat Kinerja yang diperlukan
- Kemampuan pemantauan dinamis untuk posisi katup
- Toleransi kesalahan yang sesuai dengan tingkat risiko
- Kapasitas aliran dengan margin keamanan yang memadai (minimal 20%)
Panduan Instalasi
Optimalkan instalasi untuk respons tercepat:
- Posisikan katup sedekat mungkin dengan aktuator
- Ukuran jalur suplai untuk penurunan tekanan minimal
- Memaksimalkan kapasitas knalpot dengan batasan minimal
- Menerapkan katup buang cepat untuk silinder besar
- Pastikan sambungan listrik memenuhi waktu respons yang diperlukan
Protokol Pemeliharaan dan Pengujian
Menetapkan validasi berkelanjutan yang ketat:
- Mendokumentasikan waktu respons dasar saat commissioning
- Menerapkan pengujian waktu respons secara teratur pada interval yang sesuai dengan risiko
- Menetapkan degradasi waktu respons maksimum yang dapat diterima (biasanya 20%)
- Buat kriteria yang jelas untuk penggantian atau rekondisi katup
- Menyimpan catatan pengujian untuk dokumentasi kepatuhan
Bagaimana Anda Merancang Sirkuit Keselamatan Pneumatik yang Benar-Benar Mencapai Peringkat SIL-nya?
Banyak sirkuit keselamatan pneumatik yang memiliki peringkat SIL di atas kertas tetapi gagal memberikan kinerja tersebut dalam kondisi dunia nyata karena kekeliruan desain, pemilihan komponen yang tidak tepat, atau validasi yang tidak memadai.
Sirkuit keselamatan pneumatik dengan peringkat SIL yang efektif memerlukan pemilihan komponen yang sistematis berdasarkan data keandalan, arsitektur yang sesuai dengan tingkat SIL yang diperlukan, analisis mode kegagalan yang komprehensif, dan prosedur pengujian bukti yang divalidasi. Desain yang paling andal menggabungkan beragam redundansi, diagnostik otomatis, dan interval uji bukti yang ditentukan berdasarkan perhitungan PFDavg4 nilai-nilai.
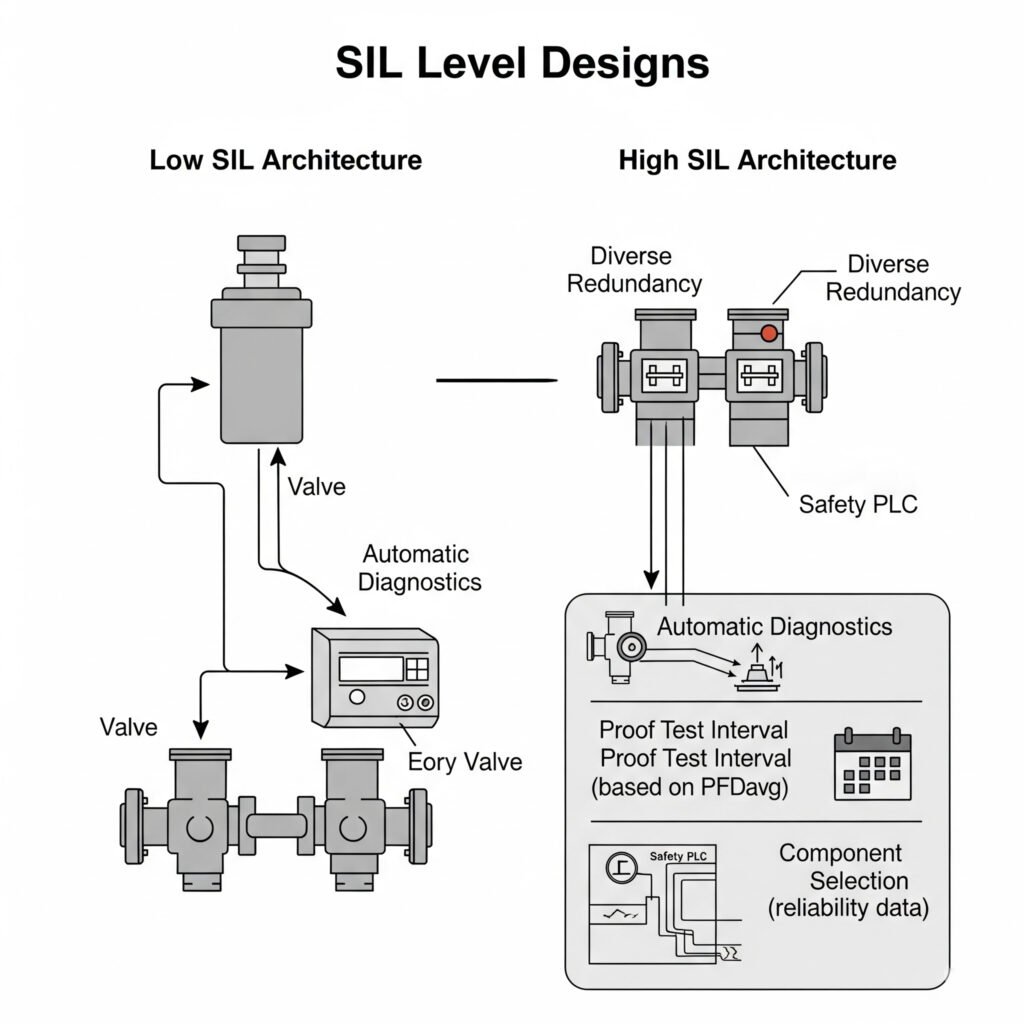
Kerangka Kerja Desain SIL yang Komprehensif untuk Sirkuit Keselamatan Pneumatik
Setelah menerapkan ratusan sistem keselamatan pneumatik dengan peringkat SIL, saya telah mengembangkan pendekatan desain terstruktur ini:
Tingkat SIL | PFDavg yang diperlukan | Arsitektur Khas | Cakupan Diagnostik | Interval Uji Bukti | Persyaratan Komponen |
---|---|---|---|---|---|
SIL 1 | 10-¹ hingga 10-² | 1oo1 dengan diagnostik | > 60% | 1-3 tahun | Data keandalan dasar, MTTF sedang |
SIL 2 | 10-² hingga 10-³ | 1oo2 atau 2oo3 | > 90% | 6 bulan - 1 tahun | Komponen bersertifikat, MTTF tinggi, data kegagalan |
SIL 3 | 10-³ hingga 10-⁴ | 2oo3 atau lebih baik | >99% | 1-6 bulan | Bersertifikat SIL 3, data kegagalan yang komprehensif, teknologi yang beragam |
SIL 4 | 10-⁴ hingga 10-⁵ | Beberapa redundansi yang beragam | > 99,9% | <1 bulan | Komponen khusus, terbukti dalam aplikasi serupa |
Metodologi Desain SIL Terstruktur untuk Sistem Pneumatik
Untuk merancang sirkuit keselamatan pneumatik dengan peringkat SIL dengan benar, ikuti metodologi komprehensif ini:
Tahap 1: Definisi Fungsi Keselamatan
Mulailah dengan definisi yang tepat tentang persyaratan keselamatan:
Spesifikasi Persyaratan Fungsional
Dokumentasikan dengan tepat apa yang harus dicapai oleh fungsi keselamatan:
- Bahaya spesifik yang dimitigasi
- Waktu respons yang diperlukan
- Definisi status aman
- Mode operasi yang tercakup
- Persyaratan pengaturan ulang manual
- Integrasi dengan fungsi keselamatan lainnyaPenentuan Target SIL
Menetapkan tingkat integritas keselamatan yang diperlukan:
- Melakukan penilaian risiko sesuai dengan IEC 61508/62061 atau ISO 13849
- Menentukan pengurangan risiko yang diperlukan
- Hitung probabilitas kegagalan target
- Menetapkan target SIL yang sesuai
- Dasar pemikiran dokumen untuk pemilihan SILDefinisi Kriteria Kinerja
Menetapkan persyaratan kinerja yang terukur:
- Probabilitas kegagalan berbahaya maksimum yang diijinkan
- Cakupan diagnostik yang diperlukan
- Toleransi kesalahan perangkat keras minimum
- Persyaratan kemampuan sistematis
- Kondisi lingkungan
- Waktu misi dan interval uji bukti
Tahap 2: Desain Arsitektur
Mengembangkan arsitektur sistem yang dapat mencapai SIL yang dibutuhkan:
Dekomposisi Subsistem
Pisahkan fungsi keselamatan menjadi beberapa elemen yang dapat dikelola:
- Perangkat input (misalnya, penghenti darurat, sakelar tekanan)
- Pemecah logika (relai pengaman, PLC pengaman)
- Elemen akhir (katup, mekanisme penguncian)
- Antarmuka antar subsistem
- Elemen pemantauan dan diagnostikPengembangan Strategi Redundansi
Rancang redundansi yang sesuai berdasarkan persyaratan SIL:
- Redundansi komponen (pengaturan paralel atau seri)
- Teknologi yang beragam untuk mencegah kegagalan penyebab umum
- Pengaturan pemungutan suara (1oo1, 1oo2, 2oo2, 2oo3, dst.)
- Independensi antara saluran yang berlebihan
- Mitigasi kegagalan penyebab umumDesain Sistem Diagnostik
Mengembangkan diagnostik komprehensif yang sesuai untuk SIL:
- Tes diagnostik otomatis dan frekuensi
- Kemampuan deteksi kesalahan
- Perhitungan cakupan diagnostik
- Tanggapan terhadap kesalahan yang terdeteksi
- Indikator dan antarmuka diagnostik
Tahap 3: Pemilihan Komponen
Pilih komponen yang mendukung SIL yang diperlukan:
Pengumpulan Data Keandalan
Mengumpulkan informasi keandalan yang komprehensif:
- Data tingkat kegagalan (terdeteksi berbahaya, tidak terdeteksi berbahaya)
- Nilai B10d untuk komponen pneumatik
- Nilai SFF (Fraksi Kegagalan Aman)
- Pengalaman operasi sebelumnya
- Data keandalan produsen
- Tingkat sertifikasi SIL komponenEvaluasi dan Pemilihan Komponen
Menilai komponen-komponen terhadap persyaratan SIL:
- Verifikasi sertifikasi kemampuan SIL
- Mengevaluasi kemampuan sistematis
- Periksa kesesuaian lingkungan
- Konfirmasikan kemampuan diagnostik
- Verifikasi kompatibilitas dengan arsitektur
- Menilai kerentanan kegagalan penyebab umumAnalisis Mode Kegagalan
Melakukan penilaian modus kegagalan secara terperinci:
- FMEDA (Mode Kegagalan, Efek, dan Analisis Diagnostik)
- Identifikasi semua mode kegagalan yang relevan
- Klasifikasi kegagalan (aman, berbahaya, terdeteksi, tidak terdeteksi)
- Analisis kegagalan penyebab umum
- Mekanisme keausan dan masa pakai misi
Tahap 4: Verifikasi dan Validasi
Konfirmasikan desain memenuhi persyaratan SIL:
Analisis Kuantitatif
Hitung metrik kinerja keselamatan:
- PFDavg (Probabilitas Kegagalan pada Permintaan rata-rata)
- HFT (Toleransi Kesalahan Perangkat Keras)
- SFF (Fraksi Kegagalan Aman)
- Persentase cakupan diagnostik
- Kontribusi kegagalan penyebab umum
- Verifikasi pencapaian SIL secara keseluruhanPengembangan Prosedur Uji Bukti
Membuat protokol pengujian yang komprehensif:
- Langkah-langkah pengujian terperinci untuk setiap komponen
- Peralatan dan pengaturan uji yang diperlukan
- Kriteria lulus/gagal
- Penentuan frekuensi uji
- Persyaratan dokumentasi
- Pengujian stroke parsial jika memungkinkanPembuatan Paket Dokumentasi
Menyusun dokumentasi keselamatan yang lengkap:
- Spesifikasi persyaratan keselamatan
- Perhitungan dan analisis desain
- Lembar data dan sertifikat komponen
- Prosedur uji bukti
- Persyaratan pemeliharaan
- Prosedur kontrol modifikasi
Studi Kasus: Sistem Keamanan Pengolahan Bahan Kimia
Fasilitas pemrosesan bahan kimia di Texas perlu menerapkan sistem keselamatan pneumatik dengan peringkat SIL 2 untuk fungsi penghentian darurat reaktor mereka. Fungsi keselamatan yang diperlukan untuk memastikan depressurisasi yang andal dari aktuator pneumatik yang mengendalikan katup proses kritis dalam waktu 2 detik dari kondisi darurat.
Kami merancang sirkuit keselamatan pneumatik SIL 2 yang komprehensif:
Definisi Fungsi Keselamatan
- Fungsi: Depressurisasi darurat aktuator katup pneumatik
- Keadaan aman: Semua katup proses dalam posisi aman dari kegagalan
- Waktu respons: <2 detik untuk menyelesaikan depresurisasi
- Target SIL: SIL 2 (PFDavg antara 10-² dan 10-³)
- Waktu misi: 15 tahun dengan pengujian bukti berkala
Desain Arsitektur dan Pemilihan Komponen
Subsistem | Arsitektur | Komponen yang Dipilih | Data Keandalan | Cakupan Diagnostik |
---|---|---|---|---|
Perangkat Input | 1oo2 | Pemancar tekanan ganda dengan perbandingan | λDU = 2,3 × 10-⁷/jam masing-masing | 92% |
Pemecah Logika | 1oo2D | PLC Keselamatan dengan modul output pneumatik | λDU = 5,1 × 10-⁸/jam | 99% |
Elemen Akhir | 1oo2 | Katup pembuangan pengaman yang dipantau ganda | B10d = 2,5 × 10⁶ siklus | 95% |
Pasokan Pneumatik | Redundansi seri | Regulator tekanan ganda dengan pemantauan | λDU = 3,4 × 10-⁷/jam masing-masing | 85% |
Hasil Verifikasi
- PFDavg yang dihitung: 8,7×10-³ (dalam kisaran SIL 2)
- Toleransi Kesalahan Perangkat Keras: HFT = 1 (memenuhi persyaratan SIL 2)
- Fraksi Kegagalan Aman: SFF = 94% (melebihi minimum SIL 2)
- Faktor Penyebab Umum: β = 2% (dengan pemilihan komponen yang beragam)
- Interval Uji Bukti: 6 bulan (berdasarkan perhitungan PFDavg)
- Kemampuan Sistematis: SC 2 (semua komponen dengan SC 2 atau lebih tinggi)
Hasil Implementasi
Setelah implementasi dan validasi:
- Sistem berhasil lolos verifikasi SIL pihak ketiga
- Pengujian bukti mengkonfirmasi kinerja yang dihitung
- Pengujian stroke parsial diimplementasikan untuk validasi bulanan
- Prosedur pengujian bukti lengkap didokumentasikan dan divalidasi
- Staf pemeliharaan terlatih sepenuhnya dalam pengoperasian dan pengujian sistem
- Sistem telah melakukan 12 kali pemadaman darurat yang berhasil selama 3 tahun
Praktik-praktik Terbaik Implementasi
Untuk implementasi sirkuit keselamatan pneumatik dengan peringkat SIL yang sukses:
Persyaratan Dokumentasi Desain
Menyimpan catatan desain yang komprehensif:
- Spesifikasi persyaratan keselamatan dengan target SIL yang jelas
- Diagram blok keandalan dengan detail arsitektur
- Justifikasi pemilihan komponen dan lembar data
- Perhitungan dan asumsi tingkat kegagalan
- Analisis kegagalan penyebab umum
- Perhitungan verifikasi SIL akhir
Perangkap Umum yang Harus Dihindari
Waspadai kesalahan desain yang sering terjadi ini:
- Toleransi kesalahan perangkat keras yang tidak memadai untuk tingkat SIL
- Cakupan diagnostik yang tidak memadai untuk arsitektur
- Mengabaikan penyebab umum kegagalan
- Interval uji bukti yang tidak tepat
- Tidak adanya penilaian kemampuan yang sistematis
- Pertimbangan kondisi lingkungan yang tidak memadai
- Dokumentasi yang tidak memadai untuk verifikasi SIL
Pemeliharaan dan Pengelolaan Perubahan
Menetapkan proses berkelanjutan yang ketat:
- Prosedur uji bukti yang terdokumentasi dengan kriteria lulus/gagal yang jelas
- Kebijakan penggantian komponen yang ketat (like-for-like)
- Proses manajemen perubahan untuk setiap modifikasi
- Sistem pelacakan dan analisis kegagalan
- Validasi ulang perhitungan SIL secara berkala
- Program pelatihan untuk personel pemeliharaan
Bagaimana Anda Memvalidasi Mekanisme Penguncian Tekanan Ganda untuk Memastikannya Benar-Benar Bekerja?
Mekanisme penguncian tekanan ganda adalah perangkat keamanan penting yang mencegah gerakan tak terduga dalam sistem pneumatik, namun banyak yang diimplementasikan tanpa validasi yang tepat, sehingga menciptakan rasa aman yang palsu.
Validasi yang efektif untuk mekanisme penguncian tekanan ganda memerlukan pengujian komprehensif dalam semua kondisi pengoperasian yang dapat diperkirakan, analisis mode kegagalan, dan verifikasi kinerja secara berkala. Proses validasi yang paling andal menggabungkan pengujian penahanan tekanan statis, pengujian beban dinamis, dan penilaian siklus hidup yang dipercepat untuk memastikan kinerja yang konsisten selama masa pakai perangkat.
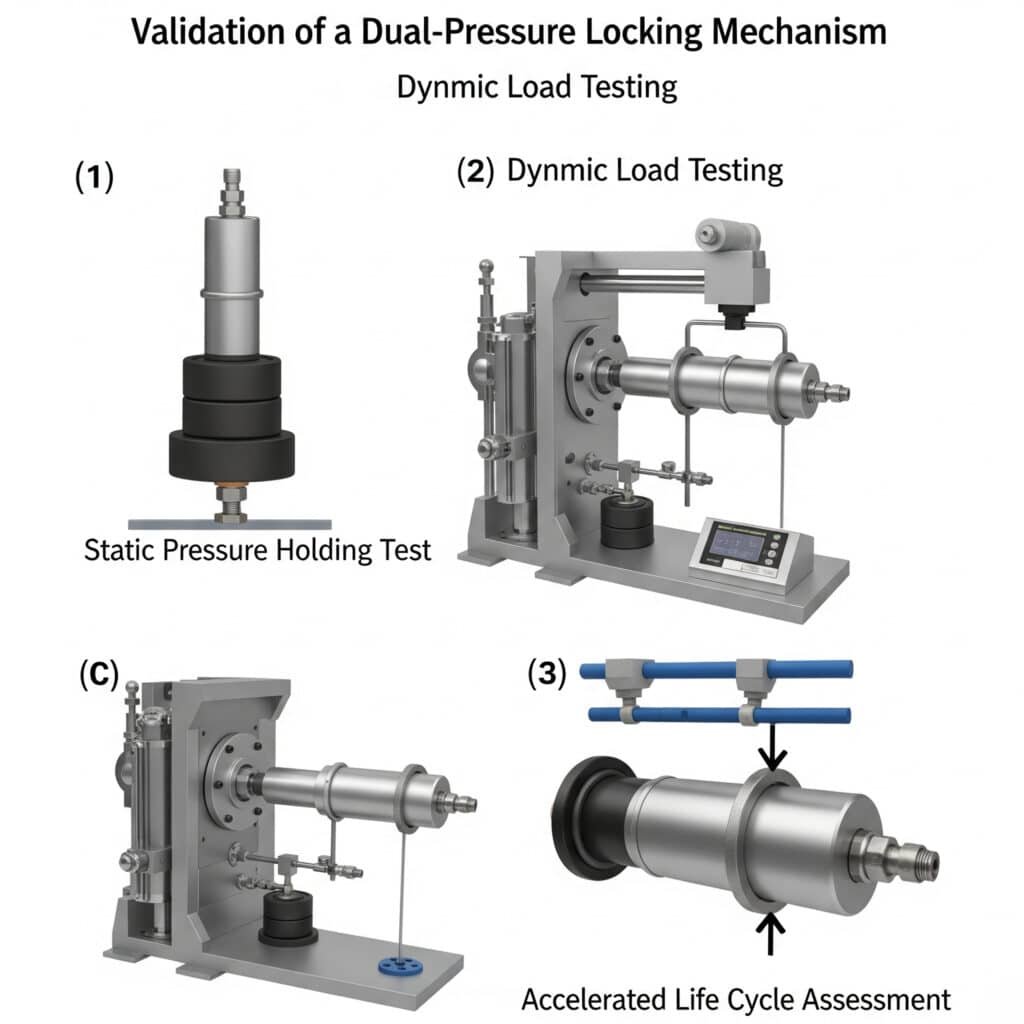
Kerangka Kerja Validasi Mekanisme Penguncian Tekanan Ganda yang Komprehensif
Setelah menerapkan dan memvalidasi ratusan sistem penguncian tekanan ganda, saya telah mengembangkan pendekatan validasi terstruktur ini:
Tahap Validasi | Metode Pengujian | Kriteria Penerimaan | Persyaratan Dokumentasi | Frekuensi Validasi |
---|---|---|---|---|
Validasi Desain | Analisis FEA5pengujian prototipe, analisis mode kegagalan | Tidak ada gerakan di bawah beban pengenal 150%, perilaku yang aman dari kegagalan | Perhitungan desain, laporan pengujian, dokumentasi FMEA | Sekali selama fase desain |
Validasi Produksi | Pengujian beban, pengujian siklus, pengukuran waktu respons | Keterlibatan kunci 100%, kinerja yang konsisten | Sertifikat uji, data kinerja, catatan ketertelusuran | Setiap batch produksi |
Validasi Instalasi | Pengujian beban in-situ, verifikasi waktu, pengujian integrasi | Fungsi yang tepat dalam aplikasi aktual | Daftar periksa instalasi, hasil pengujian, laporan komisioning | Setiap instalasi |
Validasi Berkala | Inspeksi visual, pengujian fungsional, pengujian beban parsial | Mempertahankan kinerja dalam 10% dari spesifikasi aslinya | Catatan inspeksi, hasil pengujian, analisis tren | Berdasarkan penilaian risiko (biasanya 3-12 bulan) |
Proses Validasi Mekanisme Penguncian Tekanan Ganda Terstruktur
Untuk memvalidasi mekanisme penguncian tekanan ganda dengan benar, ikuti proses komprehensif ini:
Tahap 1: Validasi Desain
Verifikasi konsep desain yang mendasar:
Analisis Desain Mekanis
Mengevaluasi prinsip-prinsip mekanis dasar:
- Perhitungan keseimbangan gaya dalam semua kondisi
- Analisis tekanan pada komponen-komponen penting
- Analisis penumpukan toleransi
- Verifikasi pemilihan bahan
- Korosi dan ketahanan lingkunganAnalisis Modus dan Efek Kegagalan
Melakukan FMEA yang komprehensif:
- Mengidentifikasi semua mode kegagalan potensial
- Menilai efek kegagalan dan kekritisan
- Menentukan metode deteksi
- Menghitung Angka Prioritas Risiko (RPN)
- Mengembangkan strategi mitigasi untuk kegagalan berisiko tinggiPengujian Kinerja Prototipe
Verifikasi kinerja desain melalui pengujian:
- Verifikasi kapasitas penyimpanan statis
- Pengujian keterlibatan dinamis
- Pengukuran waktu respons
- Pengujian kondisi lingkungan
- Pengujian siklus hidup yang dipercepat
Tahap 2: Validasi Produksi
Memastikan kualitas produksi yang konsisten:
Protokol Pemeriksaan Komponen
Verifikasi spesifikasi komponen penting:
- Verifikasi dimensi elemen pengunci
- Konfirmasi sertifikasi material
- Pemeriksaan permukaan akhir
- Verifikasi perlakuan panas jika ada
- Pengujian non-destruktif untuk komponen pentingPengujian Verifikasi Perakitan
Konfirmasikan perakitan dan penyesuaian yang tepat:
- Penyelarasan elemen penguncian yang tepat
- Beban awal yang benar pada pegas dan elemen mekanis
- Torsi yang tepat pada pengencang
- Penyegelan sirkuit pneumatik yang tepat
- Penyesuaian yang benar dari setiap elemen variabelPengujian Kinerja Fungsional
Verifikasi pengoperasian sebelum pemasangan:
- Verifikasi keterlibatan kunci
- Pengukuran gaya penahan
- Waktu pelibatan/pelepasan
- Pengujian kebocoran sirkuit pneumatik
- Pengujian siklus (minimal 1.000 siklus)
Tahap 3: Validasi Instalasi
Verifikasi kinerja dalam aplikasi yang sebenarnya:
Daftar Periksa Verifikasi Instalasi
Konfirmasikan kondisi pemasangan yang benar:
- Keselarasan dan stabilitas pemasangan
- Kualitas dan tekanan pasokan pneumatik
- Kontrol integritas sinyal
- Perlindungan lingkungan
- Aksesibilitas untuk pemeriksaan dan pemeliharaanPengujian Sistem Terpadu
Verifikasi kinerja dalam sistem yang lengkap:
- Interaksi dengan sistem kontrol
- Respons terhadap sinyal berhenti darurat
- Performa dalam kondisi beban aktual
- Kompatibilitas dengan siklus operasi
- Integrasi dengan sistem pemantauanPengujian Beban Khusus Aplikasi
Memvalidasi kinerja dalam kondisi yang sebenarnya:
- Uji penahanan beban statis pada beban aplikasi maksimum
- Pengujian beban dinamis selama pengoperasian normal
- Ketahanan getaran dalam kondisi pengoperasian
- Siklus suhu jika ada
- Pengujian paparan kontaminan jika relevan
Tahap 4: Validasi Berkala
Memastikan integritas kinerja yang berkelanjutan:
Protokol Inspeksi Visual
Mengembangkan pemeriksaan visual yang komprehensif:
- Kerusakan atau korosi eksternal
- Kebocoran atau kontaminasi cairan
- Pengencang atau sambungan yang longgar
- Keselarasan dan integritas pemasangan
- Kenakan indikator jika memungkinkanProsedur Pengujian Fungsional
Buat verifikasi kinerja non-invasif:
- Verifikasi keterlibatan kunci
- Menahan terhadap beban uji yang berkurang
- Pengukuran waktu
- Pengujian kebocoran
- Respons sinyal kontrolSertifikasi Ulang Berkala yang Komprehensif
Menetapkan interval validasi utama:
- Pembongkaran dan pemeriksaan lengkap
- Penggantian komponen berdasarkan kondisi
- Pengujian beban penuh setelah pemasangan kembali
- Pembaruan dan sertifikasi ulang dokumentasi
- Penilaian dan perpanjangan masa pakai layanan
Studi Kasus: Sistem Penanganan Material Otomatis
Sebuah pusat distribusi di Illinois mengalami insiden keselamatan yang serius ketika mekanisme penguncian tekanan ganda pada sistem penanganan material di atas kepala mengalami kegagalan, sehingga menyebabkan beban jatuh secara tidak terduga. Investigasi mengungkapkan bahwa mekanisme penguncian tidak pernah divalidasi dengan benar setelah pemasangan dan mengalami keausan internal yang tidak terdeteksi.
Kami mengembangkan program validasi yang komprehensif:
Temuan Penilaian Awal
- Desain kunci: Desain piston berlawanan tekanan ganda
- Tekanan pengoperasian: Nominal 6,5 bar
- Kapasitas beban: Dinilai untuk 1.500 kg, beroperasi dengan 1.200 kg
- Mode kegagalan: Degradasi segel internal yang menyebabkan penurunan tekanan
- Status validasi: Hanya pengujian awal pabrik, tidak ada validasi berkala
Implementasi Program Validasi
Kami menerapkan pendekatan validasi multi-fase ini:
Elemen Validasi | Metodologi Pengujian | Hasil | Tindakan Korektif |
---|---|---|---|
Tinjauan Desain | Analisis teknik, pemodelan FEA | Margin desain memadai tetapi pemantauan tidak memadai | Menambahkan pemantauan tekanan, desain segel yang dimodifikasi |
Analisis Mode Kegagalan | FMEA yang komprehensif | Mengidentifikasi 3 mode kegagalan kritis tanpa deteksi | Menerapkan pemantauan untuk setiap mode kegagalan kritis |
Pengujian Beban Statis | Aplikasi beban tambahan hingga 150% dari kapasitas pengenal | Semua unit lulus setelah modifikasi desain | Ditetapkan sebagai persyaratan tes tahunan |
Kinerja Dinamis | Pengujian siklus dengan beban | 2 unit menunjukkan keterlibatan yang lebih lambat dari yang ditentukan | Unit yang dibangun kembali dengan komponen yang disempurnakan |
Sistem Pemantauan | Pemantauan tekanan berkelanjutan dengan alarm | Berhasil mendeteksi kebocoran yang disimulasikan | Terintegrasi dengan sistem keamanan fasilitas |
Validasi Berkala | Mengembangkan program inspeksi 3 tingkat | Menetapkan data kinerja dasar | Membuat dokumentasi dan program pelatihan |
Hasil Program Validasi
Setelah menerapkan program validasi yang komprehensif:
- Mekanisme penguncian 100% sekarang memenuhi atau melampaui spesifikasi
- Pemantauan otomatis memberikan validasi berkelanjutan
- Program inspeksi bulanan menangkap masalah lebih awal
- Pengujian beban tahunan memastikan kinerja yang berkelanjutan
- Tidak ada insiden keselamatan dalam 30 bulan sejak implementasi
- Manfaat tambahan: Pengurangan 35% dalam pemeliharaan darurat
Praktik-praktik Terbaik Implementasi
Untuk validasi mekanisme penguncian tekanan ganda yang efektif:
Persyaratan Dokumentasi
Menyimpan catatan validasi yang komprehensif:
- Laporan dan perhitungan validasi desain
- Sertifikat uji produksi
- Daftar periksa validasi instalasi
- Catatan pemeriksaan berkala
- Investigasi kegagalan dan tindakan korektif
- Riwayat modifikasi dan hasil validasi ulang
Peralatan Pengujian dan Kalibrasi
Memastikan integritas pengukuran:
- Peralatan pengujian beban dengan kalibrasi yang valid
- Alat pengukur tekanan dengan akurasi yang sesuai
- Sistem pengukuran waktu untuk validasi respons
- Kemampuan simulasi lingkungan jika diperlukan
- Akuisisi data otomatis untuk konsistensi
Manajemen Program Validasi
Menetapkan proses tata kelola yang kuat:
- Penugasan tanggung jawab yang jelas untuk kegiatan validasi
- Persyaratan kompetensi untuk personel validasi
- Tinjauan manajemen atas hasil validasi
- Proses tindakan korektif untuk validasi yang gagal
- Peningkatan metode validasi yang berkelanjutan
- Manajemen perubahan untuk pembaruan program validasi
Kesimpulan
Menerapkan sistem keselamatan pneumatik yang benar-benar efektif memerlukan pendekatan komprehensif yang melampaui kepatuhan dasar. Dengan berfokus pada tiga elemen penting yang dibahas - katup penghenti darurat respons cepat, sirkuit keselamatan dengan peringkat SIL yang dirancang dengan benar, dan mekanisme penguncian tekanan ganda yang divalidasi - organisasi dapat secara dramatis mengurangi risiko cedera serius sekaligus meningkatkan efisiensi operasional.
Implementasi keselamatan yang paling sukses memperlakukan validasi sebagai proses yang berkelanjutan, bukan hanya sekali saja. Dengan menetapkan protokol pengujian yang kuat, memelihara dokumentasi yang komprehensif, dan terus memantau kinerja, Anda dapat memastikan sistem keselamatan pneumatik Anda memberikan perlindungan yang andal selama masa pakainya.
Tanya Jawab Tentang Sistem Keselamatan Pneumatik
Seberapa sering katup penghenti darurat harus diuji untuk memastikan katup tersebut mempertahankan kinerja waktu responsnya?
Katup penghenti darurat harus diuji pada interval yang ditentukan oleh kategori risiko dan aplikasinya. Aplikasi berisiko tinggi memerlukan pengujian bulanan, aplikasi berisiko sedang pengujian triwulanan, dan aplikasi berisiko rendah pengujian semi-tahunan atau tahunan. Pengujian harus mencakup pengukuran waktu respons dan verifikasi fungsionalitas penuh. Selain itu, setiap katup yang menunjukkan penurunan waktu respons lebih dari 20% dari spesifikasi aslinya harus segera diganti atau direkondisi, terlepas dari jadwal pengujian rutin.
Apa alasan paling umum sirkuit keselamatan pneumatik gagal mencapai peringkat SIL yang ditentukan dalam aplikasi dunia nyata?
Alasan paling umum sirkuit keselamatan pneumatik gagal mencapai peringkat SIL yang ditetapkan adalah pertimbangan yang tidak memadai atas kegagalan penyebab umum (CCF). Meskipun perancang sering kali berfokus pada keandalan komponen dan arsitektur redundansi, mereka sering kali meremehkan dampak faktor yang secara bersamaan dapat memengaruhi banyak komponen, seperti pasokan udara yang terkontaminasi, fluktuasi voltase, kondisi lingkungan yang ekstrem, atau kesalahan pemeliharaan. Analisis dan mitigasi CCF yang tepat dapat meningkatkan kinerja SIL dengan faktor 3-5 dalam aplikasi keselamatan pneumatik yang khas.
Dapatkah mekanisme penguncian tekanan ganda dipasang pada sistem pneumatik yang sudah ada, atau apakah mekanisme tersebut memerlukan desain ulang sistem secara menyeluruh?
Mekanisme penguncian tekanan ganda dapat berhasil dipasang pada sebagian besar sistem pneumatik yang ada tanpa mendesain ulang sepenuhnya, meskipun implementasi spesifiknya tergantung pada arsitektur sistem. Untuk sistem berbasis silinder, perangkat penguncian eksternal dapat ditambahkan dengan modifikasi minimal. Untuk sistem yang lebih kompleks, blok pengaman modular dapat diintegrasikan ke dalam manifold katup yang ada. Persyaratan utamanya adalah validasi yang tepat setelah pemasangan, karena sistem yang dipasang kembali sering kali memiliki karakteristik kinerja yang berbeda dari sistem yang dirancang sebelumnya. Biasanya, mekanisme penguncian yang dipasang kembali mencapai 90-95% dari kinerja desain terintegrasi jika diterapkan dengan benar.
Apa hubungan antara waktu respons dan jarak aman dalam sistem keselamatan pneumatik?
Hubungan antara waktu respons dan jarak aman mengikuti rumus S = (K × T) + C, di mana S adalah jarak aman minimum, K adalah kecepatan pendekatan (biasanya 1600-2000 mm/dtk untuk gerakan tangan/lengan), T adalah total waktu respons sistem (termasuk deteksi, pemrosesan sinyal, dan respons katup), dan C adalah jarak tambahan berdasarkan potensi gangguan. Untuk sistem pneumatik, setiap pengurangan 10ms dalam waktu respons katup biasanya memungkinkan pengurangan jarak aman 16-20mm. Hubungan ini membuat katup respons cepat sangat berharga dalam aplikasi terbatas ruang di mana mencapai jarak aman yang besar tidak praktis.
Bagaimana faktor lingkungan memengaruhi kinerja sistem keselamatan pneumatik?
Faktor lingkungan secara signifikan memengaruhi kinerja sistem keselamatan pneumatik, dengan suhu memiliki efek yang paling menonjol. Suhu rendah (di bawah 5 ° C) dapat meningkatkan waktu respons sebesar 15-30% karena peningkatan viskositas udara dan kekakuan segel. Suhu tinggi (di atas 40 ° C) dapat mengurangi efektivitas seal dan mempercepat degradasi komponen. Kelembaban memengaruhi kualitas udara dan dapat memasukkan air ke dalam sistem, yang berpotensi menyebabkan masalah korosi atau pembekuan. Kontaminasi dari lingkungan industri dapat menyumbat lubang kecil dan memengaruhi pergerakan katup. Getaran dapat melonggarkan koneksi dan menyebabkan keausan komponen dini. Validasi komprehensif harus mencakup pengujian di seluruh rentang lingkungan yang diharapkan dalam aplikasi.
Dokumentasi apa yang diperlukan untuk menunjukkan kepatuhan terhadap standar keselamatan untuk sistem pneumatik?
Dokumentasi keselamatan yang komprehensif untuk sistem pneumatik harus mencakup:
(1) Penilaian risiko yang mendokumentasikan bahaya dan pengurangan risiko yang diperlukan; (2) Spesifikasi persyaratan keselamatan yang merinci persyaratan kinerja dan fungsi keselamatan;
(3) Dokumentasi desain sistem termasuk alasan pemilihan komponen dan keputusan arsitektur; (4) Laporan perhitungan yang menunjukkan pencapaian tingkat kinerja yang diperlukan atau SIL; (5) Laporan uji validasi yang mengonfirmasi kinerja sistem;
(6) Catatan verifikasi instalasi; (7) Prosedur inspeksi dan pengujian berkala;
(8) Persyaratan dan catatan pemeliharaan;
(9) Materi pelatihan dan catatan kompetensi; dan
(10) Manajemen prosedur perubahan. Dokumentasi ini harus dipelihara sepanjang siklus hidup sistem dan diperbarui setiap kali ada modifikasi.
-
Menawarkan penjelasan terperinci tentang Tingkat Integritas Keselamatan (SIL), ukuran kinerja sistem keselamatan dalam hal probabilitas kegagalan sesuai permintaan (PFD), seperti yang didefinisikan oleh standar seperti IEC 61508. ↩
-
Memberikan informasi tentang standar internasional ISO 13855, yang menentukan parameter untuk memposisikan pengaman berdasarkan kecepatan bagian tubuh manusia dan waktu penghentian keseluruhan fungsi pengaman. ↩
-
Menjelaskan konsep B10d, metrik keandalan yang mewakili jumlah siklus di mana 10% dari sampel komponen mekanis atau pneumatik diperkirakan mengalami kegagalan yang berbahaya, yang digunakan dalam perhitungan keselamatan. ↩
-
Menggambarkan Probabilitas Kegagalan Sesuai Permintaan (PFDavg), probabilitas rata-rata bahwa sistem keselamatan akan gagal menjalankan fungsi yang dirancang ketika terjadi permintaan, yang merupakan metrik utama untuk menentukan SIL sistem. ↩
-
Memberikan gambaran umum tentang Analisis Elemen Hingga (FEA), metode terkomputerisasi untuk memprediksi bagaimana suatu produk bereaksi terhadap gaya, getaran, panas, dan efek fisik lainnya di dunia nyata dengan memecahnya menjadi sejumlah elemen kecil yang terbatas. ↩