生産ラインが突然停止。エンジニアは謎の空気圧の故障を直そうと奔走する。ほとんどの人は、現代のオートメーションの動力源である単純な物理学を理解することはない。
空気圧シリンダーの動作原理はパスカルの法則に基づくもので、圧縮空気の圧力が密閉されたチャンバー内であらゆる方向に等しく作用し、圧力差によってシリンダー内径を通るピストンが移動するときに直線的な力が発生する。
昨年、私はテキサス州の自動車工場でメンテナンスを担当するサラを訪ねた。彼女のチームは、空気圧シリンダーがなぜ故障するのかを理解しないまま、数週間ごとに交換していた。私が2時間かけて基本原理を説明したところ、彼女の故障率は1ヵ月で80%も減少した。基本を理解することですべてが変わったのだ。
目次
- パスカルの法則と空気圧シリンダーへの適用とは?
- 空気圧はどのようにして直線運動を生み出すのか?
- 空気圧シリンダーを機能させるために不可欠な部品とは?
- 単動シリンダーと複動シリンダーの違いは?
- シリンダーの作動においてシールとバルブはどのような役割を果たすのか?
- 力、スピード、空気消費量はどのように計算するのか?
- 空気圧駆動の利点と限界とは?
- 環境要因は空気圧シリンダーの性能にどう影響するか?
- どのような問題がよく起こり、どのようにそれを防ぐか?
- 結論
- 空気圧シリンダーの原理に関するFAQ
パスカルの法則と空気圧シリンダーへの適用とは?
パスカルの法則は、すべての空気圧シリンダー操作の基礎を形成し、圧縮空気が大きな力を発生できる理由を説明します。
パスカルの法則は、閉じ込められた流体に加えられた圧力は、すべての方向に等しく伝わるというもので、空気圧シリンダーは、ピストン表面に圧力差を加えることによって、空気圧を直線的な力に変換することができる。
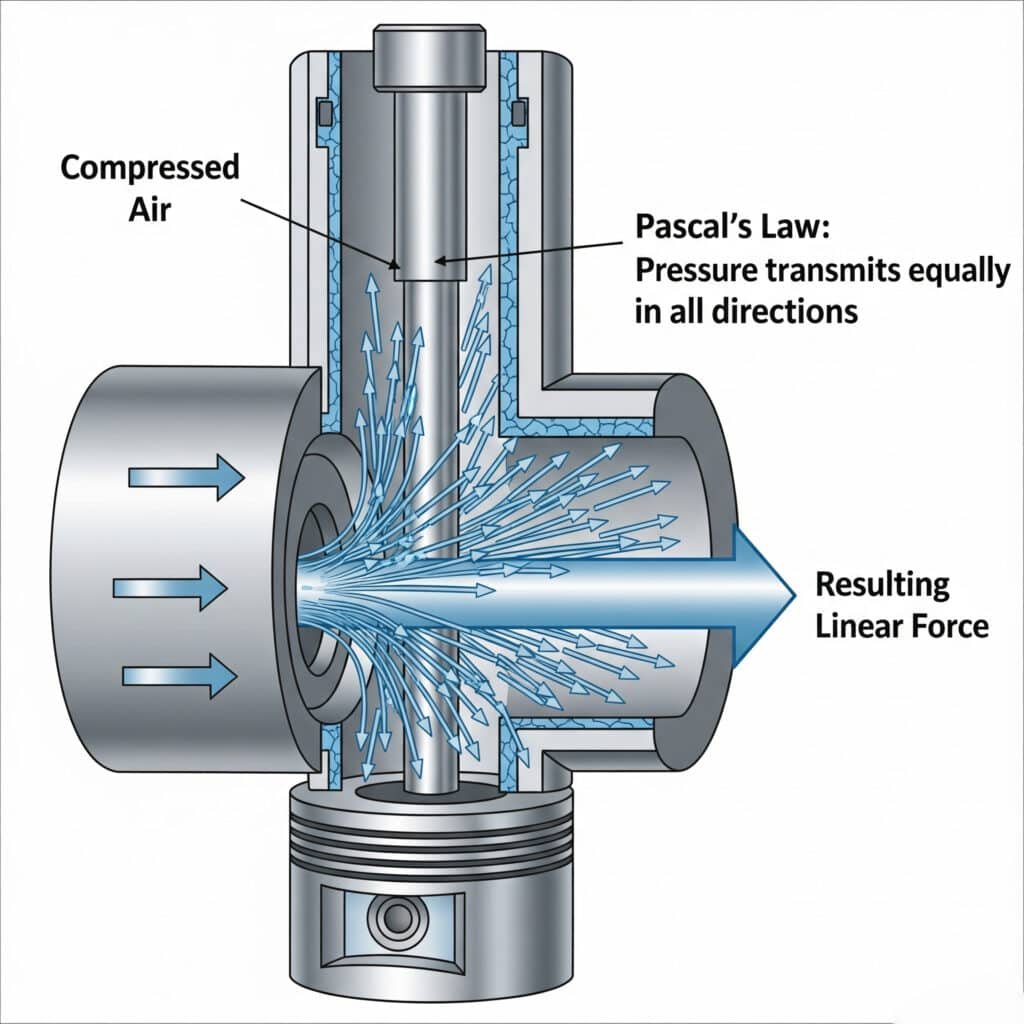
圧力伝達を理解する
パスカルの法則 ブレーズ・パスカル1 1653年)は、閉じ込められた流体が圧力下でどのように振る舞うかを説明している。閉じ込められた流体のどの点にも圧力をかけると、その圧力は流体体積全体に均等に伝わる。
空気圧シリンダーでは、圧縮空気が作動流体として働く。空気圧がシリンダーの片側に入ると、ピストンの表面積全体に等しい力でピストンを押します。
圧力は空気容積全体で一定だが、力は圧力が作用する表面積に依存する。この関係により、空気圧シリンダーは比較的低い空気圧から大きな力を発生させることができる。
数学財団
基本的な力の式はパスカルの法則から直接導かれる:F=P×A、ここで力は圧力×面積に等しい。この単純な関係は、すべての空気圧シリンダーの計算に適用されます。
圧力の単位は通常、場所によってbar、PSI、パスカルのいずれかを使用する。1バールは約14.5 PSIまたは100,000パスカルに相当します。
面積計算では、複動シリンダーのロッド面積を考慮した有効ピストン直径を使用する。ロッドはピストンの片側の有効面積を減少させる。
圧力差の概念
空気圧シリンダーは、ピストン全体に圧力差を作ることで機能する。片側の圧力が高くなると、ピストンを低圧側に動かす正味の力が生じます。
背圧が存在しない限り、排気側には大気圧(1 barまたは14.7 PSI)が存在します。圧力差が実際の出力を決定します。
理論的な最大出力は、片側が全システム圧力で、もう片側が大気に排気されるときに発生します。実際のシステムには、実際の力出力を低下させる損失があります。
実践的応用
パスカルの法則を理解することは、空気圧のトラブルシューティングに役立ちます。圧力降下が発生した場合、力の出力はシステム全体で比例して減少します。
システム設計では、バルブ、継手、チューブを介した圧力損失を考慮する必要があります。これらの損失は、シリンダーで利用可能な有効圧力を減少させます。
同じ圧力源に接続された複数のシリンダーは、パスカルの法則に従い、利用可能な圧力を等しく共有する。
圧力 (bar) | ピストン面積 (cm²) | 理論力 (N) | 実用力 (N) |
---|---|---|---|
6 | 50 | 3000 | 2700 |
6 | 100 | 6000 | 5400 |
8 | 50 | 4000 | 3600 |
8 | 100 | 8000 | 7200 |
空気圧はどのようにして直線運動を生み出すのか?
空気圧を直線運動に変換するには、制御された動きを生み出すために、いくつかの物理的原理が連動する。
空気圧は、ピストン表面に力を加え、静止摩擦と負荷抵抗に打ち勝ち、空気流量によって決定される速度でシリンダーボアを通してピストンとロッドアセンブリを加速することによって直線運動を生み出します。
戦力創出プロセス
圧縮空気はシリンダー室に入り、利用可能な容積を満たすために膨張する。空気分子は、ピストン面を含むすべての面に対して圧力をかける。
圧力力はピストン表面に垂直に作用し、運動方向に正味の力を生み出す。この力は、運動が始まる前に静止摩擦に打ち勝たなければなりません。
運動が始まると、動摩擦が静止摩擦に取って代わり、通常、抵抗力が減少します。そして、正味の力がピストンと取り付けられた荷重を加速させます。
モーション・コントロール・メカニズム
シリンダーへの空気流量は、ピストンの速度を決定する。流量が多いほど速い動きが可能になり、逆に流量が制限されると、より遅く、より制御された動きが可能になる。
流量制御バルブは、所望の速度を達成するために空気流量を調整します。メーター・イン制御は加速に影響し、メーター・アウト制御は減速と負荷処理に影響する。
排気側の背圧がクッションとなり、スムーズな減速を実現。調整可能なクッション・バルブは、特定の用途に合わせて運動特性を最適化します。
加速と減速
ニュートンの第二法則2 (F=ma)は、ピストンの加速度を支配する。正味の力を移動質量で割ったものが加速度を決定します。
初期加速度は、圧力差が最大で速度がゼロのときに最も大きくなります。速度が上がると、流量の制限によって加速度が低下することがあります。
減速は、排気の流れが制限されたり、背圧が高まったりしたときに起こります。制御された減速はショック荷重を防ぎ、システムの寿命を向上させます。
エネルギー伝達効率
空気圧システムは通常、コンプレッサーの入力から有用な仕事の出力まで、25~35%のエネルギー効率を達成します。ほとんどのエネルギーは、圧縮と膨張の間に熱に変換されます。
シリンダー効率は、摩擦損失、漏れ、流量制限に左右されます。うまく設計されたシステムは、85~95%のシリンダー効率を達成します。
システムの最適化は、圧力損失を最小化し、適切なシリンダーサイジングを使用して、実用的な制約の中で効率を最大化することに重点を置いています。
空気圧シリンダーを機能させるために不可欠な部品とは?
各コンポーネントの機能を理解することで、空気圧シリンダシステムの選択、メンテナンス、トラブルシューティングを効率的に行うことができます。
空圧シリンダに不可欠なコンポーネントには、シリンダ本体、ピストンアセンブリ、ピストンロッド、エンドキャップ、シール、ポート、および取付け金具があり、それぞれが信頼性の高いリニアモーション生成のために連携して動作するように設計されています。
シリンダーボディの構造
シリンダー本体は、作動圧力を保持し、ピストンの動きをガイドします。ほとんどのシリンダーは、ボディの材料にシームレス鋼管またはアルミニウム押出材を使用しています。
内部表面の仕上げは、シールの寿命と性能に決定的な影響を与えます。 ホーニング・ボア3 0.4~0.8Raの表面仕上げで、最適なシール動作と長寿命を提供します。
肉厚は、適切な安全係数で使用圧力に耐えなければならない。標準設計では、4:1の安全係数で10-16 barの使用圧力に対応します。
本体材質には、炭素鋼、ステンレス鋼、アルミニウム合金がある。材料の選択は、使用環境、圧力要件、およびコストの考慮事項によって異なります。
ピストン・アセンブリ設計
ピストンはシリンダー室を分離し、ピストンロッドに力を伝達する。ピストンの設計は、性能、効率、寿命に影響します。
ピストンの材質は通常、アルミニウムかスチール製です。アルミニウム製ピストンは移動質量を減らして加速を速くし、スチール製ピストンはより大きな力に対応する。
ピストンシールはチャンバー間の圧力境界を作ります。一次シールは圧力の封じ込めを行い、二次シールは漏れを防ぎます。
ピストンの直径は、F = P × Aに従って力の出力を決定します。大きなピストンはより大きな力を発生させますが、より多くの空気量と流量を必要とします。
ピストンロッド仕様
ピストンロッドは、シリンダーの力を外部負荷に伝達する。ロッドの設計は、座屈やたわみなしに加えられた力を処理しなければならない。
ロッドの材質には、クロムメッキ鋼、ステンレス鋼、特殊合金などがあります。クロムメッキは、耐食性と滑らかな表面仕上げを提供します。
ロッドの直径は座屈強度とシステム剛性に影響する。より大きなロッドは、より高い側面荷重に対応しますが、シリンダーサイズとコストが増加します。
ロッドの表面仕上げは、シールの性能と寿命に影響します。滑らかで硬い表面はシールの摩耗を最小限に抑え、メンテナンス間隔を延長します。
エンドキャップとマウントシステム
エンドキャップは、シリンダー端部をシールし、シリンダーボディの取り付けポイントを提供する。全システム圧力と取付け荷重に耐えなければならない。
タイロッド構造4 は、エンドキャップをシリンダー本体に固定するためにネジ付きロッドを使用しています。この設計により、フィールドサービスやシール交換が可能になります。
溶接構造により、エンドキャップはシリンダー本体に永久的に取り付けられます。これにより、よりコンパクトな設計になりますが、現場でのサービスはできません。
取り付けスタイルには、クレビス、トラニオン、フランジ、フット取り付けオプションがあります。適切な取り付け方法を選択することで、応力集中や早期故障を防ぐことができます。
コンポーネント | 素材オプション | 主要機能 | 故障モード |
---|---|---|---|
シリンダーボディ | スチール、アルミニウム | 圧力封じ込め | 腐食、摩耗 |
ピストン | アルミニウム、スチール | 力の伝達 | シールの不具合、摩耗 |
ピストンロッド | クロム鋼、SS | 負荷接続 | 座屈、腐食 |
エンドキャップ | スチール、アルミニウム | 圧力シール | 割れ、漏れ |
シール | NBR、PU、PTFE | 圧力隔離 | 摩耗、ケミカル・アタック |
シール技術
プライマリーピストンシールは、シリンダー室間の圧力分離を維持します。シールの選択は、圧力、温度、および化学的適合性の要件に依存します。
ロッドシールは外部リークやコンタミの侵入を防ぎます。効果的なシール性を維持しながら、ダイナミックな動きにも対応しなければなりません。
ワイパーシールは、引き込み中にロッド表面の汚れを取り除きます。これにより内部シールを保護し、寿命を延ばします。
静的シールは、ねじ接続部やエンドキャップ界面での漏れを防ぎます。表面間の相対運動なしに圧力に対応します。
単動シリンダーと複動シリンダーの違いは?
単動シリンダーか複動シリンダーかの選択は、性能、制御、用途適合性に大きく影響する。
単動シリンダーは、スプリングまたは重力リターンによって一方向の動きに空気圧を使用するのに対し、複動シリンダーは両方向の動きに空気圧を使用し、より優れた制御とより大きな力を提供する。
単動シリンダーの操作
単動シリンダーは、ピストンの片側だけに空気圧を加える。リターン・ストロークは、内部スプリング、外部スプリング、または重力に頼ってピストンを後退させます。
スプリング・リターン・シリンダーは、空気圧が解放されると内部の圧縮スプリングを使用してピストンを後退させます。スプリングの力は、摩擦や外部からの荷重に打ち勝たなければなりません。
重力リターンシリンダは、ピストンを後退させるために重量または外力に依存します。この設計は、重力が復帰動作を補助する垂直用途に適しています。
加圧された空気は一方向の動きにしか使用されないため、空気消費量が少ない。これにより、コンプレッサーの要件と運転コストが削減されます。
複動シリンダーの作動
複動式シリンダーは、ピストンの両側に交互に空気圧を加える。これにより、伸長方向と引込方向の両方向に動力が供給される。
ロッド面積が片側の有効ピストン面積を減少させるため、力の出力は伸長ストロークと収縮ストロークで異なる可能性があります。一般的に伸長側の力が大きくなります。
速度制御は、別々の流量制御バルブを使用して、両方向で独立しています。これにより、異なる負荷条件に対して最適化されたサイクルタイムを実現します。
空気圧が両方向の外力に対して位置を維持するため、位置保持能力が優れている。
パフォーマンス比較
単動シリンダーの力出力は、伸長時にスプリング力によって制限される。スプリング力は、作業に利用できる正味の出力力を減少させる。
複動シリンダーは、摩擦損失を除いた全空気圧力を両方向に提供します。これにより、外部負荷に利用可能な力が最大化されます。
単動式設計では、戻り速度は制御された空気の流れではなく、スプリングの特性や重力に依存するため、速度制御はより制限される。
エネルギー効率は、空気消費量が少なく制御システムが単純なため、単純な用途では単動式設計の方が有利かもしれない。
選考基準
単動シリンダーは、軽い戻り荷重で一方向の動きを必要とする単純な用途に適しています。例えば、クランプ、プレス、リフティング作業などがあります。
複動式シリンダーは、両方向に制御された動きや、引き込み時に大きな力を必要とする用途に適しています。マテリアルハンドリングや位置決め用途には、複動式設計が有効です。
安全性を考慮すると、空気圧が失われたときに安全な位置まで故障する単動式設計が好まれる場合があります。スプリングリターンにより、予測可能な故障モードの動作が保証されます。
コスト分析には、シリンダー価格、バルブの複雑さ、システム寿命にわたる空気消費量などを含め、最も経済的な選択を決定する必要がある。
特徴 | 単動 | ダブルアクション | ベスト・アプリケーション |
---|---|---|---|
フォースコントロール | 一方向のみ | 両方向 | SA:クランプ、DA:ポジショニング |
スピードコントロール | 限定リターン | フルコントロール | SA:シンプル、DA:コンプレックス |
空気消費量 | より低い | より高い | SA:コスト重視、DA:パフォーマンス |
ポジション保持 | 中程度 | 素晴らしい | SA:グラビティ・ロード、DA:プレシジョン・ロード |
安全行動 | 予測可能なリターン | バルビングによる | SA:フェイルセーフ、DA:制御 |
シリンダーの作動においてシールとバルブはどのような役割を果たすのか?
シールとバルブは、空気圧シリンダーの適切な機能、効率、信頼性を可能にする重要なコンポーネントです。
シールが圧力分離を維持し、コンタミネーションを防止する一方で、バルブがエアフローの方向、速度、圧力を制御し、シリンダーの望ましい動きと位置決めを実現する。
シールの機能と種類
プライマリー・ピストン・シールは、シリンダー・チャンバー間の圧力バリアとなります。最小限の摩擦でスムーズなピストン運動を可能にしながら、効果的にシールする必要があります。
ロッドシールは、ピストンロッドの周囲から加圧空気が漏れるのを防ぎます。また、外部からのコンタミネーションがシリンダー内に侵入するのを防ぎます。
ワイパーシールは、引き込み中にロッド表面から汚れ、水分、ゴミを取り除きます。これにより、内部シールを保護し、システムを清潔に保ちます。
静的シールは、ねじ接続部、エンドキャップ、ポート継手での漏れを防ぎます。シール面間の相対運動なしに圧力を扱うことができます。
シール材の選択
ニトリルゴム(NBR)シールは、耐薬品性に優れ、適度な温度範囲(-20℃~+80℃)で一般産業用途に対応します。
ポリウレタン(PU)シールは、ハイサイクル用途に優れた耐摩耗性と低摩擦性を提供します。PUシールは-35°Cから+80°Cの温度範囲で使用できます。
PTFEシールは耐薬品性と低摩擦性に優れていますが、取り付けには注意が必要です。耐熱温度は-200℃から+200℃です。
バイトンシールは、過酷な環境下でも優れた耐薬品性と耐熱性を発揮します。20℃から+200℃まで確実に作動します。
バルブ制御機能
方向制御弁は、シリンダーを伸縮させるためのエアーの流れ方向を決定します。一般的なタイプには、3/2 方弁と 5/2 方弁があります。
流量制御バルブは、シリンダー速度を制御するために空気流量を調整する。メーター・イン制御は加速に影響し、メーター・アウト制御は減速に影響する。
圧力制御弁は安定した作動圧力を維持し、過負荷保護を提供します。安定した出力を保証し、システムの損傷を防ぎます。
クイックエキゾーストバルブは、メインバルブの流量制限をバイパスして、大気へ直接空気を素早く排出することで、シリンダーの動きを加速させます。
バルブの選択基準
流量容量は、所望の運転速度に対するシリンダー要件に適合していなければなりません。過小サイズのバルブは、性能を制限する流量制限を生じます。
応答時間は高速アプリケーションのシステム性能に影響します。即効性のあるバルブは、迅速な方向転換と正確な位置決めを可能にします。
定格圧力は、適切な安全マージンを確保した上で、システムの最大圧力を上回る必要があります。バルブの故障は危険な圧力開放を引き起こす可能性があります。
環境適合性には、温度範囲、耐振動性、汚染の侵入に対する保護が含まれる。
システム・インテグレーション
バルブの取り付けオプションには、コンパクトな設置向けのマニホールド取り付けと、分散制御システム向けの個別取り付けがあります。
電気接続は、制御システムの要件に適合する必要があります。オプションとして、ソレノイド操作、パイロット操作、手動オーバーライド機能があります。
位置センサーからのフィードバック信号は、クローズドループ制御システムを可能にします。バルブの応答は、安定した動作のためにセンサー信号と協調する必要があります。
メンテナンスへのアクセスは、システムの保守性に影響する。バルブの配置は、点検、調整、および必要な場合の交換を容易に行えるものでなければならない。
力、スピード、空気消費量はどのように計算するのか?
正確な計算により、適切な空気圧シリンダのサイズ決定と、特定のアプリケーション要件に対するシステム性能の予測が可能になります。
空気圧シリンダーの力をF = P × Aで計算し、速度をV = Q/Aで決定し、空気量と圧力の関係を用いて空気消費量を見積もり、システムの設計と性能を最適化する。
力の計算方法
理論的な力は、空気圧×有効ピストン面積に等しい:これは、理想的な条件下で利用可能な最大力を表しています。
複動シリンダでは、ロッド面積の関係で、伸びストロークと縮みストロークで有効ピストン面積が異なる:A_retract = A_piston - A_rod。
実用的な力は摩擦損失を考慮したもので、通常理論的な力の10~15%である。シールの摩擦、ガイドの摩擦、エアフローの損失が利用可能な力を減少させます。
荷重分析には、静的重量、プロセス力、加速力、安全係数を含めること。必要な力の合計がシリンダーの最小サイズを決定する。
速度計算の原則
シリンダー速度は空気流量に直接関係する:ここで、速度は体積流量を有効ピストン面積で割ったものに等しい。
流量はバルブの容量、圧力差、チューブのサイズに依存する。システムのどこかに流量制限があると、最高速度が制限されます。
加速段階の速度は、空気流量が増加するにつれて徐々に増加する。定常速度は、流量が最大容量で安定するときに発生する。
減速度は排気流量と背圧に依存する。緩衝装置が減速を制御し、衝撃荷重を防ぐ。
空気消費分析
1サイクルあたりの空気消費量は、シリンダー容積×圧力比に等しい:V_air = V_cylinder × (P_absolute/P_atmospheric).
複動式シリンダーは、伸長ストロークと収縮ストロークの両方にエアを消費する。単動シリンダーは動力ストロークにのみ空気を消費する。
バルブ、継手、漏れによるシステム損失は、通常、理論消費量に20~30%を加える。適切なシステム設計は、これらの損失を最小限に抑えます。
コンプレッサーのサイジングは、十分な予備能力でピーク需要とシステムロスを処理する必要があります。サイズが小さいコンプレッサーは、圧力低下と性能低下を引き起こします。
パフォーマンスの最適化
ボアサイズの選択は、必要な力とスピードおよびエア消費量のバランスをとる。より大きなボアは、より大きな力を提供しますが、より多くの空気を使用し、動きが遅くなります。
ストロークの長さは、空気消費量とシステムの応答時間に影響する。ストロークが長いと、より多くの空気量が必要となり、充填時間も長くなる。
運転圧力の最適化は、力の必要性、エネルギーコスト、部品の寿命を考慮します。高い圧力はシリンダーサイズを小さくしますが、エネルギー消費と部品へのストレスを増加させます。
システム効率は、コンポーネントの適切なサイジング、最小限の圧力損失、効果的な空気処理によって向上します。適切に設計されたシステムは、85~95%の効率を達成します。
シリンダーボア | 動作圧力 | エクステンド・フォース | 引き込み力 | エア・パー・サイクル |
---|---|---|---|---|
50mm | 6バー | 1180N | 950N | 2.4リットル |
63mm | 6バー | 1870N | 1500N | 3.7リットル |
80mm | 6バー | 3020N | 2420N | 6.0リットル |
100mm | 6バー | 4710N | 3770N | 9.4リットル |
実践的な計算例
例1:内径63mm、圧力6 barのシリンダー
- 力を伸ばす:F = 6 × π × (63/2)² = 1870N
- 空気消費量V = π × (63/2)² × ストローク × 6 = ストローク × 18.7リットル/メートル
例2:6バールで2000Nの力に必要なシリンダーサイズ
- 必要な面積A = F/P = 2000/6 = 333 cm²
- 必要な直径D = √(4A/π) = √(4×333/π) = 65mm
これらの計算は、シリンダー選定の出発点となり、最終的なサイジングは安全係数とアプリケーション固有の要件を考慮します。
空気圧駆動の利点と限界とは?
空圧システムの利点と制約を理解することで、空圧シリンダがお客様のアプリケーションに最適な選択であるかを判断することができます。
空気圧は、クリーンな操作性、シンプルな制御、高速性、安全性といった利点があるが、油圧や電気に比べ、出力、エネルギー効率、正確な位置決めには限界がある。
空気圧システムの主な利点
クリーンな操作により、空気圧システムは食品加工、製薬、クリーンルーム用途に理想的です。圧縮空気の漏れは製品や環境に無害です。
シンプルな制御システムは、操作に基本的なバルブとスイッチを使用する。そのため、複雑さやトレーニングの必要性、メンテナンスが、より洗練された代替品に比べて軽減される。
高速運転は、低移動質量と圧縮性の空気特性により、迅速なサイクルタイムを可能にします。空気圧シリンダーは最高10m/sの速度を達成することができます。
安全上の利点として、不燃性の作業媒体と予測可能な故障モードがあります。空気漏れは火災の危険や環境汚染を引き起こさない。
単純な用途での費用対効果には、初期コストの低さ、設置の簡単さ、ほとんどの産業施設で容易に利用できる圧縮空気が含まれます。
システムの限界
力出力は実用的な空気圧レベルによって制限され、産業用システムでは通常6~10 barです。このため、空気圧シリンダーは中程度の力の用途に制限されます。
エネルギー効率は悪く、コンプレッサー入力から有用な仕事出力まで、通常25~35%である。ほとんどのエネルギーは、圧縮と膨張のサイクル中に熱に変換される。
空気の圧縮性と温度の影響により、正確な位置決めは難しい。空気圧システムは、±1mm以上の位置決め精度が要求される用途では苦労します。
空気の密度と圧力が温度によって変化するため、温度感度が性能に影響する。システム性能は周囲条件によって変化する。
排気やコンプレッサーの作動により、騒音レベルが大きくなることがある。騒音に敏感な環境では、防音対策が必要な場合があります。
代替技術との比較
油圧システムは、より大きな力とより優れた位置決め精度を提供するが、複雑な流体の取り扱いを必要とし、オイル漏れによる環境への懸念が生じる。
電動アクチュエータは、正確な位置決めと高効率を提供するが、初期コストが高く、高荷重用途では速度に限界がある。
空気圧システムは、中程度の力、高速性、クリーンな操作性、シンプルな制御、リーズナブルなイニシャルコストを必要とする用途に優れています。
アプリケーション適合性マトリックス
理想的な用途としては、精密さや大きな力よりもスピードや清潔さが重視される、包装、組立、マテリアルハンドリング、単純なオートメーションなどがある。
劣悪な用途としては、重量物持ち上げ、精密位置決め、連続運転、エネルギー効率が運転コストにとって重要な用途などがある。
ハイブリッドシステムは、システム全体の性能を最適化するために、空気圧スピードと電気精度または油圧力を組み合わせることがある。
ファクター | 空気圧式 | 油圧式 | 電気 | ベスト・チョイス |
---|---|---|---|---|
フォース出力 | 中程度 | 非常に高い | 高い | 油圧式:重負荷 |
スピード | 非常に高い | 中程度 | 可変 | 空気圧式:高速サイクル |
精密 | 貧しい | グッド | 素晴らしい | エレクトリックポジショニング |
清潔さ | 素晴らしい | 貧しい | グッド | 空気圧クリーンルーム |
エネルギー効率 | 貧しい | 中程度 | 素晴らしい | 電気式:連続デューティ |
初期費用 | 低い | 高い | 中程度 | 空気圧:シンプルなシステム |
経済的考察
運転コストには、圧縮空気の生成、メンテナンス、エネルギー消費が含まれます。空気コストは通常、1立方メートル当たり$0.02~0.05の範囲です。
構造がシンプルで交換部品が入手しやすいため、メンテナンスコストは一般的に低い。シール交換が主なメンテナンス要件です。
システムのライフサイクルコストは、初期投資、運用費用、予想される耐用年数にわたる生産性利益を考慮すべきである。
投資収益率分析は、生産性の向上、労働力の削減、製品品質の向上に基づいて、空気圧システムの選択を正当化するのに役立ちます。
環境要因は空気圧シリンダーの性能にどう影響するか?
環境条件は、実際の用途における空気圧シリンダの動作、信頼性、寿命に大きく影響します。
温度、湿度、汚染、振動、腐食性物質などの環境要因は、シールの劣化、腐食、摩擦の変化、部品の摩耗を通じて、空気圧シリンダーの性能に影響を与えます。
温度効果
作動温度は、空気密度、圧力、および構成部品の材質に影響する。温度が高くなると、空気密度と有効出力が低下します。
シール材には性能と寿命に影響する温度限界があります。標準的なNBRシールは-20℃から+80℃まで使用できますが、特殊な材料はこの範囲を広げます。
シリンダー部品の熱膨張は、クリアランスやシール性能に影響を与える可能性があります。結合や漏れを防ぐためには、熱膨張を考慮した設計が必要です。
圧縮空気が露点以下に冷却されると結露が発生します。システム内の水は、腐食、凍結、不安定な運転を引き起こします。
湿度と水分のコントロール
湿度が高いと、圧縮空気システムの結露リスクが高まります。水の蓄積は部品の腐食や動作不良を引き起こします。
フィルター、ドライヤー、セパレーターを含む空気処理システムは、湿気や汚染物質を取り除きます。信頼性の高い運転には、適切な空気処理が不可欠です。
ドレンシステムは、空気分配システムの低い位置から蓄積した凝縮水を除去しなければならない。自動ドレンは水の蓄積を防ぐ。
露点5 制御は、空気含水率を運転温度で結露を引き起こすレベル以下に維持する。目標露点は通常、最低運転温度より10℃低い。
汚染の影響
ダストやゴミはシールの摩耗、バルブの誤作動、内部部品の損傷を引き起こします。ろ過システムは、空気圧コンポーネントを汚染から保護します。
化学汚染はシールを攻撃し、腐食を引き起こし、運転の妨げとなる堆積物を作る可能性があります。化学的な環境では、材料の適合性が重要です。
微粒子による汚染は摩耗を促進し、バルブの固着やシール不良の原因となります。フィルターのメンテナンスは、システムの信頼性のために不可欠です。
コンプレッサーからのオイル汚染は、シールの膨潤や劣化の原因となります。オイルフリーコンプレッサーまたは適切なオイル除去システムは、汚染を防ぎます。
振動と衝撃
機械的振動はファスナーの緩み、シールの変位、部品の疲労の原因となります。適切な取り付けと防振がシステム部品を保護します。
急激な方向転換や外部からの衝撃による衝撃荷重は、内部部品を損傷させる可能性があります。クッションシステムは衝撃荷重を軽減し、部品の寿命を延ばします。
共振周波数は振動の影響を増幅します。システム設計では、搭載部品の共振周波数での動作は避けるべきである。
基礎の安定性はシステムの性能と寿命に影響します。剛性の高い取り付けは、過度の振動を防ぎ、適切なアライメントを維持します。
腐食環境保護
腐食性雰囲気は金属部品を侵し、早期故障の原因となります。材料の選択と保護コーティングは、過酷な環境での寿命を延ばします。
ステンレス鋼製は耐食性に優れるが、システ ムコストが高くなる。費用便益分析により、ステンレ ス鋼が正当化される時期が決定される。
アルマイト、メッキ、塗装を含む保護コーティングは、標準的な材料に腐食保護を提供します。コーティングの選択は、特定の環境条件によって異なります。
密閉設計は、腐食性物質が内部部品に接触するのを防ぎます。過酷なアプリケーションでは、環境シーリングが重要です。
環境要因 | パフォーマンスへの影響 | 保護方法 | 代表的なソリューション |
---|---|---|---|
高温 | 力の低下、シールの劣化 | ヒートシールド、冷却 | 高温シール、断熱材 |
低温 | 結露、シールの硬化 | 暖房、断熱 | 寒冷地用シール、ヒーター |
高湿度 | 腐食、水の蓄積 | 空気乾燥、水切り | 冷蔵乾燥機、オートドレン |
汚染 | 摩耗、故障 | ろ過、シール | フィルター、ワイパー、カバー |
振動 | 緩み、疲労 | アイソレーション、ダンピング | ショックマウント、クッション |
腐食 | コンポーネントの劣化 | 素材の選択 | ステンレススチール、コーティング |
どのような問題がよく起こり、どのようにそれを防ぐか?
空気圧シリンダーの一般的な問題とその防止策を理解することで、信頼性の高い運転を維持し、ダウンタイムを最小限に抑えることができます。
一般的な空圧シリンダーの問題には、シール漏れ、不安定な動き、力出力の低下、早期摩耗などがあるが、適切な空気処理、定期的なメンテナンス、正しいサイジング、環境保護によって防ぐことができる。
シール漏れ問題
シリンダー室間の内部漏れは、力出力を低下させ、不安定な動きを引き起こす。ピストンシールの摩耗や損傷が典型的な原因です。
ロッド周辺の外部漏れは、安全上の危険と空気の浪費を引き起こす。ロッドのシール不良や表面の損傷により、加圧された空気が漏れる。
シール不良の原因には、汚染、不適切な取り付け、化学的不適合、通常の摩耗などがある。予防は根本的な原因への対処に重点を置く。
交換手順には、適切なシールの選択、表面処理、取り付け技術が必要です。誤った取り付けは、直ちに故障の原因となります。
不規則な動きの問題
スティック・スリップは、摩擦のばらつき、汚れ、潤滑不足から生じます。スムーズな操作には、安定した摩擦レベルが必要です。
速度変動は、流量制限、圧力変動、または内部漏れを示します。システム診断により特定の原因を特定します。
位置ドリフトは、シリンダーが外部負荷に対して位置を維持できない場合に発生する。内部リークやバルブの問題が位置ドリフトを引き起こす。
ハンチングや発振は、制御システムの不安定性や過度のゲイン設定に起因します。適切なチューニングにより、不安定な動作はなくなります。
力出力低減
バルブ、継手、チューブを介した圧力損失は、シリンダーで利用可能な力を減少させます。適切なサイジングにより、過剰な圧力損失を防ぐことができます。
内部リークは、ピストンを横切る有効圧力差を減少させます。シール交換により、適切な出力が回復します。
摩擦は、汚染、摩耗、潤滑不足によって増加します。定期的なメンテナンスにより、低摩擦運転を維持します。
温度の影響は、空気密度と利用可能な力を減少させる。温度変化を考慮したシステム設計が必要。
部品の早期摩耗
汚染は、シール、ガイド、内部表面の摩耗を加速させる。適切な濾過と空気処理により、コンタミネーションによる損傷を防ぎます。
過負荷は設計限界を超え、急速な摩耗や故障を引き起こします。適切な安全係数を用いた適切なサイジングにより、過負荷による損傷を防ぎます。
ミスアライメントは、不均等な負荷と摩耗の加速を生み出します。適切な取り付けと装着により、アライメントの問題を防ぎます。
不十分な潤滑は摩擦と摩耗を増加させます。適切な潤滑システムは部品の寿命を維持します。
予防保全戦略
定期的な点検により、故障が発生する前に問題を特定します。目視点検、性能監視、漏水検知により、プロアクティブなメンテナンスが可能になります。
空気処理のメンテナンスには、フィルター交換、ドライヤー整備、ドレンシステム運転などが含まれます。クリーンで乾燥した空気は、信頼性の高い運転に不可欠です。
潤滑スケジュールは、問題の原因となる過剰な潤滑を行わず、適切な潤滑レベルを維持します。メーカーの推奨に従ってください。
性能モニタリングは、力出力、速度、空気消費量を追跡し、故障の前に性能低下を特定します。
問題の種類 | 症状 | 根本原因 | 予防法 |
---|---|---|---|
シール漏れ | エアロス、力の低下 | 摩耗、汚染 | クリーンな空気、適切なシール |
不規則な動き | 一貫性のないスピード | 摩擦、制限 | 潤滑、フローサイジング |
フォース・ロス | 弱い操作 | 圧力低下、漏れ | 適切なサイジング、メンテナンス |
早期摩耗 | 短い耐用年数 | 過負荷、汚染 | 正しいサイジング、ろ過 |
ポジション・ドリフト | ポジションをキープできない | 内部リーク | シールメンテナンス、バルブ |
トラブルシューティングの方法
体系的な診断は、症状の特定から始まり、論理的な検査手順を経て進行する。問題パターンを追跡するために所見を文書化する。
性能試験では、仕様に照らして実際の力、速度、空気消費量を測定する。これにより、具体的な性能劣化が特定される。
コンポーネント・テストは、問題を特定のシステム要素に分離する。アセンブリ全体ではなく、故障したコンポーネントのみを交換または修理する。
根本原因分析は、単なる症状ではなく、根本的な原因に対処することで、問題の再発を防ぐ。これにより、長期的なメンテナンスコストを削減することができます。
結論
空気圧シリンダの原理は、パスカルの法則と圧力差を利用して圧縮空気を信頼性の高い直線運動に変換するもので、適切に理解し適用することで、最新のオートメーションに不可欠なものとなります。
空気圧シリンダーの原理に関するFAQ
空気圧シリンダーの基本的な動作原理は何ですか?
基本原理はパスカルの法則を利用したもので、圧縮空気の圧力があらゆる方向に等しく作用し、圧力差がシリンダー内径を通してピストンを移動させるときに直線力を生み出し、空気圧エネルギーを機械的運動に変換する。
空気圧シリンダーの出力はどのように計算するのですか?
ここで、力は空気圧×有効ピストン面積に等しく、複動シリンダでは後退ストロークでのロッド面積の減少を考慮する。
単動と複動の空気圧シリンダーの違いは何ですか?
単動シリンダーは一方向に空気圧を使用し、スプリングまたは重力で戻るが、複動シリンダーは両方向に空気圧を使用するため、両方向でより優れた制御と高い力が得られる。
なぜ空気圧シリンダーは時間が経つと力がなくなるのか?
空気圧シリンダーは、内部シールの漏れ、空気システム内の圧力低下、摩擦の増加を引き起こす汚染、およびシステム効率を低下させる通常のコンポーネントの摩耗によって力を失う。
空気圧シリンダーでは、どのようにして空気圧が直線運動を生み出すのですか?
空気圧は、パスカルの法則に従ってピストン表面に力を加え、静止摩擦と負荷抵抗に打ち勝ち、シリンダーボアを通してピストンアセンブリを加速させることによって直線運動を生み出します。
空気圧シリンダーの性能に影響を与える要因は何ですか?
性能の要因には、空気圧と品質、空気密度に対する温度の影響、汚染レベル、シールの状態、アプリケーションに適したサイジング、湿度や振動などの環境条件が含まれる。
空気圧シリンダーのシールはどのように機能するのか?
シールは、シリンダー室間の圧力分離を維持し、ロッド周辺の外部漏れを防ぎ、特定の使用条件に合わせて選択されたNBR、ポリウレタン、PTFEなどの材料を使用して、汚染の侵入を遮断します。