
만져본 적이 있나요? 공압 실린더 계속 작동한 후 뜨거운 느낌에 놀란 적이 있나요? 이러한 열은 단순한 불편함을 넘어 에너지 낭비, 효율성 저하, 잠재적인 신뢰성 문제로 인해 운영 비용이 수천만 달러에 달할 수 있습니다.
공압 시스템의 열 전달은 부품 재료를 통한 전도, 표면과 공기 사이의 대류, 뜨거운 표면에서 발생하는 복사라는 세 가지 메커니즘을 통해 이루어집니다. 이러한 원리를 이해하고 최적화하면 작동 온도를 15-30% 낮추고 부품 수명을 최대 40% 연장하며 에너지 효율을 5-15% 개선할 수 있습니다.
지난달에는 열 문제로 인해 3~4개월마다 로드리스 실린더가 고장 나는 조지아의 한 식품 가공 공장에 컨설팅을 제공한 적이 있습니다. 이 공장의 유지보수 팀은 근본 원인을 해결하지 않고 단순히 부품만 교체하고 있었습니다. 적절한 열 전달 원리를 적용하여 작동 온도를 22°C 낮추고 부품 수명을 1년 이상 연장했습니다. 저희가 어떻게 그렇게 했는지, 그리고 동일한 원리를 귀사의 시스템에 어떻게 적용할 수 있는지 보여드리겠습니다.
목차
- 전도 계수 계산: 열은 부품을 통해 어떻게 이동하나요?
- 대류 개선 방법: 공기 대 표면 열전달을 극대화하는 기술에는 어떤 것이 있을까요?
- 방사 효율 모델: 공압 시스템에서 열 방사는 언제 중요할까요?
- 결론
- 공압 시스템의 열전달에 관한 FAQ
전도 계수 계산: 열은 부품을 통해 어떻게 이동하나요?
전도는 고체 공압 부품 내의 주요 열 전달 메커니즘입니다. 전도 계수를 계산하고 최적화하는 방법을 이해하는 것은 시스템 온도를 관리하는 데 필수적입니다.
열전도 계수는 다음을 사용하여 계산할 수 있습니다. 푸리에의 법칙1여기서 q는 열유속(W/m²), k는 열전도율(W/m-K), dT/dx는 온도 구배입니다. 공압 부품의 경우 효과적인 전도는 재료 선택, 인터페이스 품질, 열 경로 길이와 단면적에 영향을 미치는 기하학적 요인에 따라 달라집니다.
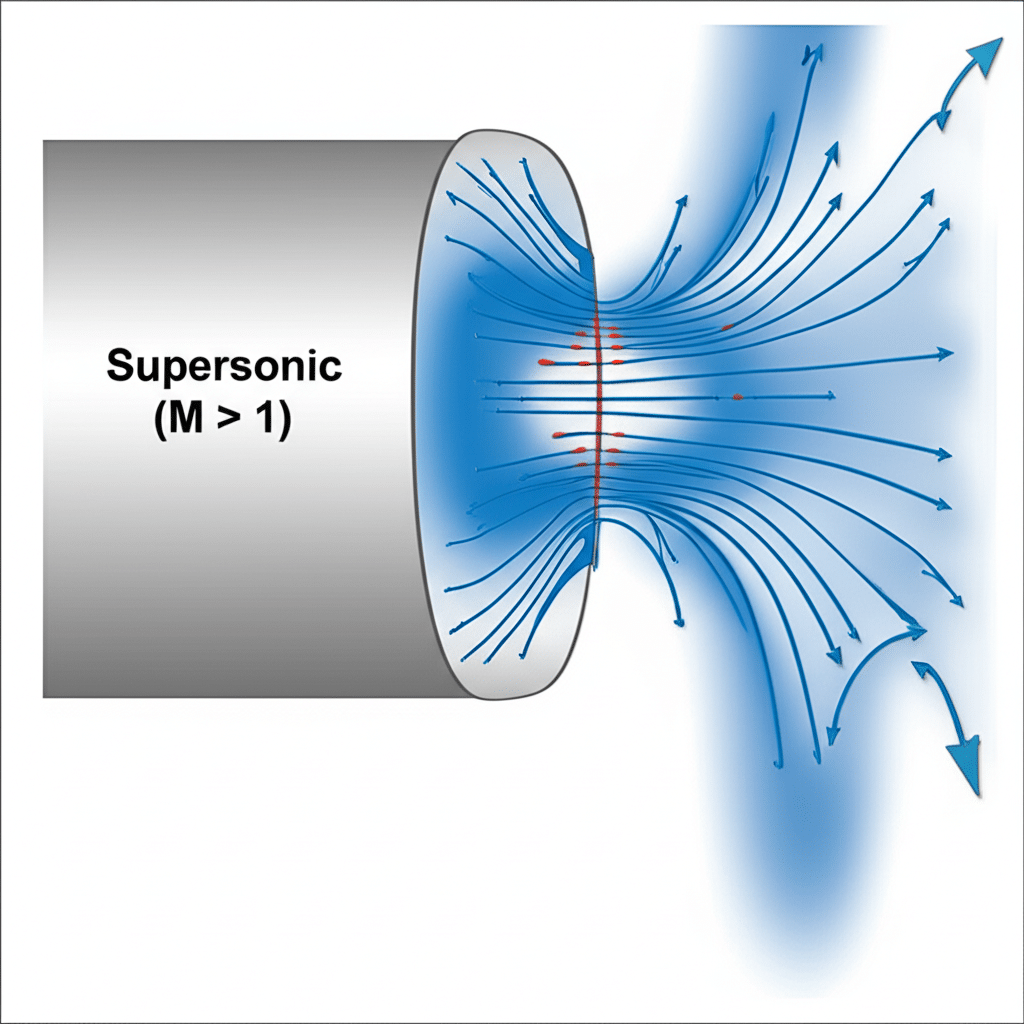
테네시주의 한 제조 라인에서 로드리스 실린더 베어링이 조기에 고장 나던 문제를 해결했던 기억이 납니다. 유지보수 팀은 여러 윤활유를 사용해봤지만 성공하지 못했습니다. 전도 경로를 분석하던 중 베어링 하우징 인터페이스에서 열 병목 현상을 발견했습니다. 표면 마감을 개선하고 열 전도성 화합물을 도포하여 유효 전도 계수를 340%까지 높이고 고장을 완전히 제거했습니다.
기본 전도 방정식
공압 부품의 전도도를 계산하는 주요 방정식을 분석해 보겠습니다:
열 전도에 대한 푸리에의 법칙
열 전도를 지배하는 기본 방정식은 다음과 같습니다:
q = -k(dT/dx)
Where:
- q = 열유속(W/m²)
- k = 열전도율(W/m-K)
- dT/dx = 온도 구배(K/m)
단면적이 일정한 단순한 1차원 케이스의 경우:
Q = kA(T₁-T₂)/L
Where:
- Q = 열전달률(W)
- A = 단면적(m²)
- T₁, T₂ = 양쪽 끝의 온도(K)
- L = 열 경로의 길이(m)
열 저항 개념
복잡한 형상의 경우 열 저항 접근 방식이 더 실용적인 경우가 많습니다:
R = L/(kA)
Where:
- R = 열 저항(K/W)
여러 구성 요소가 직렬로 연결된 시스템의 경우:
Rtotal = R₁ + R₂ + R₃ + ... + Rₙ
그리고 열전달률은 다음과 같습니다:
Q = ΔT/R총계
재료 열전도율 비교
재료 | 열 전도성(W/m-K) | 상대 전도도 | 일반적인 애플리케이션 |
---|---|---|---|
알루미늄 | 205-250 | 높음 | 실린더, 방열판 |
Steel | 36-54 | Medium | 구조적 구성 요소 |
스테인리스 스틸 | 14-16 | 낮음-중간 | 부식성 환경 |
브론즈 | 26-50 | Medium | 베어링, 부싱 |
PTFE | 0.25 | 매우 낮음 | 씰, 베어링 |
니트릴 고무 | 0.13 | 매우 낮음 | O링, 씰 |
Air(스틸) | 0.026 | 매우 낮음 | 갭 필러 |
열 페이스트 | 3-8 | 낮음 | 인터페이스 재료 |
공압 어셈블리의 접촉 저항
구성 요소 간의 인터페이스에서 접촉 저항은 열 전달에 큰 영향을 미칩니다:
Rcontact = 1/(hc × A)
Where:
- hc = 접촉 계수(W/m²-K)
- A = 접촉 면적(m²)
접촉 저항에 영향을 미치는 요인은 다음과 같습니다:
- 표면 거칠기: 표면이 거칠수록 실제 접촉 면적이 적습니다.
- 접촉 압력: 높은 압력으로 유효 접촉 면적 증가
- 인터페이스 재료: 열 화합물로 에어 갭 메우기
- 표면 청결도: 오염 물질은 저항을 증가시킬 수 있습니다.
사례 연구: 로드리스 실린더 열 최적화
열 문제가 발생하는 마그네틱 로드리스 실린더의 경우:
구성 요소 | 독창적인 디자인 | 최적화된 디자인 | 개선 사항 |
---|---|---|---|
실린더 본체 | 아노다이징 알루미늄 | 동일한 소재, 개선된 마감 | 15% 더 나은 전도성 |
베어링 인터페이스 | 금속 대 금속 접촉 | 열 화합물 추가 | 340% 더 나은 전도성 |
마운팅 브래킷 | 도장된 강철 | 베어 알루미늄 | 280% 더 나은 전도성 |
전체 열 저항 | 2.8 K/W | 0.7 K/W | 75% 감소 |
작동 온도 | 78°C | 56°C | 22°C 감소 |
구성 요소 수명 | 4개월 | >12개월 이상 | 3배 개선 |
실용적인 전도 최적화 기술
수백 개의 공압 시스템에 대한 경험을 바탕으로 전도를 개선하기 위한 가장 효과적인 방법을 소개합니다:
인터페이스 최적화
- 표면 마감: 결합 표면 평활도를 Ra 0.4-0.8 μm로 개선
- 열 인터페이스 재료2: 적절한 화합물 도포(3-8W/m-K)
- 패스너 토크: 최적의 접촉 압력을 위해 적절히 조여야 합니다.
- 청결: 조립하기 전에 모든 오일과 오염 물질을 제거하세요.
재료 선택 전략
- 중요 열 경로: 고전도성 소재(알루미늄, 구리) 사용
- 열 차단: 열 차단을 위해 의도적으로 저전도성 소재 사용
- 복합적 접근 방식: 최적의 성능/비용을 위한 재료 조합
- 이방성 머티리얼: 적절한 경우 방향성 전도성 활용
기하학적 최적화
- 열 경로 길이: 열원과 방열판 사이의 거리 최소화
- 단면적: 열 흐름에 수직인 면적 최대화
- 열 병목 현상: 열 경로의 수축 파악 및 제거
- 중복 경로: 여러 병렬 전도 경로 만들기
대류 개선 방법: 공기 대 표면 열전달을 극대화하는 기술에는 어떤 것이 있을까요?
대류는 종종 공압 시스템 냉각의 제한 요소입니다. 대류 열 전달을 개선하면 열 관리 및 시스템 성능을 크게 향상시킬 수 있습니다.
대류 열 전달은 다음과 같습니다. 뉴턴의 냉각 법칙3: Q = hA(Ts-T∞) 여기서 h는 대류 계수(W/m²-K), A는 표면적, (Ts-T∞)는 표면과 유체 사이의 온도 차이입니다. 개선 방법에는 핀을 통한 표면적 증가, 방향성 기류로 유체 속도 개선, 난류 경계층을 촉진하기 위한 표면 특성 최적화 등이 있습니다.

애리조나주의 한 포장 시설에서 에너지 효율 감사를 하던 중 43°C의 주변 환경에서 작동하는 공압 시스템을 발견했습니다. 모든 유지보수 요건을 충족했음에도 불구하고 막대가 없는 실린더가 과열되고 있었습니다. 소형 알루미늄 핀과 저전력 팬을 추가하는 등 목표 대류 개선을 구현하여 대류 계수를 450%까지 높였습니다. 이를 통해 시스템을 크게 수정하지 않고도 작동 온도를 위험 수준에서 사양 이내로 낮출 수 있었습니다.
대류 열전달의 기초
대류 열 전달을 지배하는 기본 방정식은 다음과 같습니다:
Q = hA(Ts-T∞)
Where:
- Q = 열전달률(W)
- h = 대류 계수(W/m²-K)
- A = 표면적(m²)
- Ts = 표면 온도(K)
- T∞ = 유체(공기) 온도(K)
대류 계수 h는 여러 요인에 따라 달라집니다:
- 유체 특성(밀도, 점도, 열전도도)
- 흐름 특성(속도, 난기류)
- 표면 지오메트리 및 방향
- 흐름 체제(자연 대류 대 강제 대류)
자연 대류와 강제 대류
매개변수 | 자연 대류 | 강제 대류 | 시사점 |
---|---|---|---|
일반적인 h 값 | 5-25 W/m²-K | 25-250 W/m²-K | 강제 대류는 10배 더 효과적일 수 있습니다. |
원동력 | 부력(온도 차이) | 외부 압력(팬, 송풍기) | 강제 대류는 온도에 덜 의존합니다. |
흐름 패턴 | 표면을 따라 수직 흐름 | 강제 메커니즘에 기반한 방향성 | 특정 구성 요소에 맞게 강제 흐름을 최적화할 수 있습니다. |
신뢰성 | 수동적, 항상 존재 | 전원 및 유지 관리 필요 | 자연 대류가 기본 냉각을 제공합니다. |
공간 요구 사항 | 공기 순환을 위해 여유 공간이 필요합니다. | 에어 무버 및 덕트를 위한 공간 필요 | 강제 시스템에는 더 많은 계획이 필요합니다. |
대류 향상 기법
표면적 확대
유효 표면적을 늘립니다:
핀 및 확장된 표면
- 핀 핀: 전방향 공기 흐름, 150-300% 면적 증가
- 플레이트 핀: 방향성 공기 흐름, 200-500% 면적 증가
- 주름진 표면: 중간 정도의 향상, 50-150% 면적 증가표면 다듬기
- 마이크로 텍스처링: 5-15% 유효 면적 증가
- 딤플 표면: 10-30% 증가 및 경계층 효과 추가
- 그루브 패턴: 방향성 이점으로 15-40% 증가
흐름 조작
이를 통해 공기 흐름 특성을 개선합니다:
강제 공기 시스템
- 팬: 방향성 공기 흐름, 200-600% h 개선
- 블로어: 고압 유량, 300-800% h 개선
- 압축 공기 분사: 표적 냉각, 400-1000% 로컬 h 개선흐름 경로 최적화
- 배플: 중요한 구성 요소에 직접 공기 공급
- 벤츄리 효과: 특정 표면 위의 공기 가속
- 볼텍스 제너레이터: 경계층 파괴를 위한 난기류 생성하기
표면 수정
표면 속성을 변경하여 대류를 강화합니다:
방사율 처리
- 검은 산화물: 방사율이 0.7-0.9로 증가합니다.
- 아노다이징: 0.4~0.9%의 방사율 제어
- 페인트 및 코팅: 최대 0.98%의 방사율을 사용자 지정할 수 있습니다.습윤성 제어
- 친수성 코팅: 액체 냉각 강화
- 소수성 표면: 결로 문제 방지
- 패턴화된 습윤성: 응축수 흐름 방향
실제 구현 예시
고온 환경에서 작동하는 로드리스 공압 실린더의 경우:
향상 방법 | 구현 | h 개선 | 온도 감소 |
---|---|---|---|
핀 핀(6mm) | 알루미늄 클립온 핀, 10mm 간격 | 180% | 12°C |
직접 공기 흐름 | 80mm, 2W DC 팬(1.5m/s) | 320% | 18°C |
표면 처리 | 블랙 아노다이징 | 40% | 3°C |
결합된 접근 방식 | 모든 방법 통합 | 450% | 24°C |
설계 계산을 위한 누셀트 수 상관관계
엔지니어링 계산의 경우 누셀 번호4 (Nu)는 대류에 대한 차원 없는 접근 방식을 제공합니다:
Nu = hL/k
Where:
- L = 특성 길이
- k = 유체 열전도율
평판 위 강제 대류의 경우:
Nu = 0.664Re^(1/2)Pr^(1/3) (층류)
Nu = 0.037Re^(4/5)Pr^(1/3) (난류)
Where:
- Re = 레이놀즈 수(속도 × 길이 × 밀도/점도)
- Pr = 프랜들틀 수(비열 × 점도/열전도도)
이러한 상관관계를 통해 엔지니어는 다양한 구성에 대한 대류 계수를 예측하고 그에 따라 냉각 전략을 최적화할 수 있습니다.
방사 효율 모델: 공압 시스템에서 열 방사는 언제 중요할까요?
공압 시스템 열 관리에서 복사는 종종 간과되지만 많은 애플리케이션에서 전체 열 전달의 15~30%를 차지할 수 있습니다. 종합적인 열 관리를 위해서는 복사 열 전달을 최적화하는 시기와 방법을 이해하는 것이 중요합니다.
복사 열 전달은 스테판-볼츠만 법칙5: Q = εσA(T₁⁴-T₂⁴) 여기서 ε는 표면 방사율, σ는 스테판-볼츠만 상수, A는 표면 면적, T₁ 및 T₂는 방출 표면과 주변의 절대 온도입니다. 공압 시스템의 방사 효율은 주로 표면 방사율, 온도 차이, 구성 요소와 환경 간의 시야 인자에 따라 달라집니다.
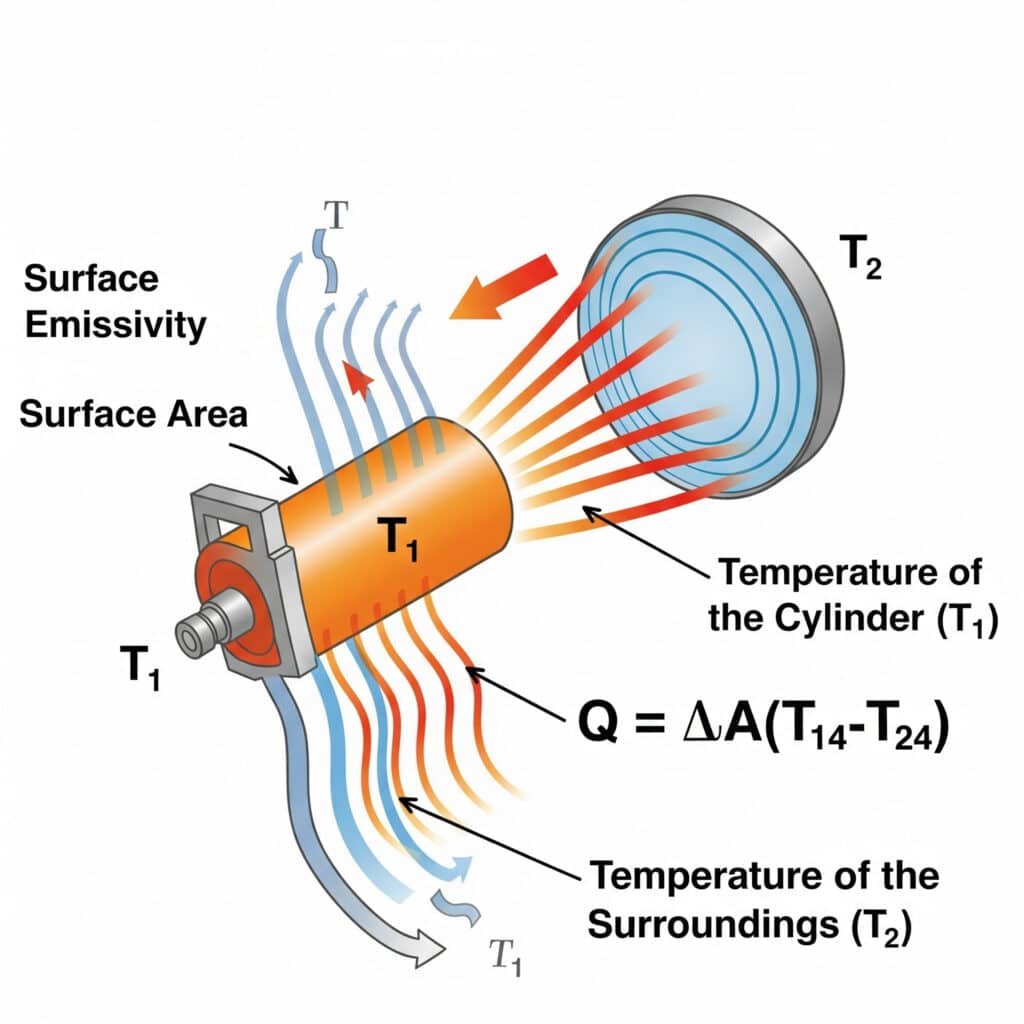
저는 최근 오리건주의 한 반도체 장비 제조업체가 정밀 로드리스 실린더의 과열 문제를 해결하는 데 도움을 주었습니다. 이 업체의 엔지니어들은 전도와 대류에만 집중한 나머지 방사선을 간과하고 있었습니다. 고방사율 코팅(ε를 0.11에서 0.92로 증가)을 적용하여 복사열 전달을 700% 이상 향상시켰습니다. 이 간단한 패시브 솔루션은 움직이는 부품이나 에너지 소비 없이도 작동 온도를 9°C 낮췄으며, 이는 클린룸 환경에서 중요한 요건입니다.
복사 열전달의 기초
복사열 전달을 지배하는 기본 방정식은 다음과 같습니다:
Q = εσA(T₁⁴-T₂⁴)
Where:
- Q = 열전달률(W)
- ε = 방사율(무차원, 0-1)
- σ = 스테판-볼츠만 상수(5.67 × 10-⁸ W/m²-K⁴)
- A = 표면적(m²)
- T₁ = 표면 절대 온도(K)
- T₂ = 주변 절대 온도(K)
일반적인 공압 재료의 표면 방사율 값
재질/표면 | 방사율(ε) | 방사 효율 | 강화 잠재력 |
---|---|---|---|
광택 알루미늄 | 0.04-0.06 | 매우 열악함 | >1500% 개선 가능 |
아노다이징 알루미늄 | 0.7-0.9 | 우수 | 이미 최적화됨 |
스테인리스 스틸(광택) | 0.07-0.14 | Poor | >600% 개선 가능 |
스테인리스 스틸(산화 처리) | 0.6-0.85 | Good | 중간 정도의 개선 가능 |
스틸(광택 처리) | 0.07-0.10 | Poor | >900% 개선 가능 |
강철(산화) | 0.7-0.9 | 우수 | 이미 최적화됨 |
페인트 표면 | 0.8-0.98 | 우수 | 이미 최적화됨 |
PTFE(흰색) | 0.8-0.9 | 우수 | 이미 최적화됨 |
니트릴 고무 | 0.86-0.94 | 우수 | 이미 최적화됨 |
보기 요소 고려 사항
방사선 교환은 방사율뿐만 아니라 표면 간의 기하학적 관계에 따라 달라집니다:
F₁₂ = 표면 1을 떠난 방사선 중 표면 2에 부딪히는 방사선 비율
복잡한 지오메트리의 경우 다음을 사용하여 뷰 인자를 계산할 수 있습니다:
- 분석 솔루션 간단한 지오메트리의 경우
- 인수 대수 보기 알려진 솔루션을 결합하기 위한
- 수치적 방법 복잡한 배열의 경우
- 경험적 근사치 실용적인 엔지니어링을 위한
방사선의 온도 의존성
4승의 온도 관계는 방사선이 더 높은 온도에서 특히 효과적이라는 것을 의미합니다:
표면 온도 | 복사에 의한 열 전달 비율* |
---|---|
30°C(303K) | 5-15% |
50°C(323K) | 10-25% |
75°C(348K) | 15-35% |
100°C(373K) | 25-45% |
150°C(423K) | 35-60% |
*자연 대류 조건 가정, ε = 0.8, 주변 온도 25°C
방사선 효율성 향상 전략
산업용 공압 시스템에 대한 제 경험을 바탕으로 복사 열 전달을 개선하는 가장 효과적인 방법을 소개합니다:
표면 방사율 수정
고방사율 코팅
- 알루미늄용 블랙 아노다이징(ε ≈ 0.8-0.9)
- 강철용 흑색 산화물(ε ≈ 0.7-0.8)
- 특수 세라믹 코팅(ε ≈ 0.9-0.98)표면 텍스처링
- 마이크로 러프닝으로 유효 방사율 증가
- 다공성 표면으로 복사 특성 향상
- 방사율/대류 개선 기능 결합
환경 최적화
주변 온도 관리
- 뜨거운 장비/프로세스로부터의 차폐
- 더 나은 방사선 교환을 위한 차가운 벽/천장
- 냉각기 표면으로 직접 방사되는 방사선을 차단하는 반사 장벽뷰 팩터 개선
- 시원한 표면 노출을 극대화하는 방향 설정
- 차단 물체 제거
- 냉각기와의 방사선 교환을 개선하는 반사판
사례 연구: 정밀 공압 분야의 방사선 강화
클린룸 환경의 고정밀 로드리스 실린더에 적합합니다:
매개변수 | 독창적인 디자인 | 방사선 강화 설계 | 개선 사항 |
---|---|---|---|
표면 재질 | 광택 알루미늄(ε ≈ 0.06) | 세라믹 코팅 알루미늄(ε ≈ 0.94) | 1467% 방사율 증가 |
복사 열전달 | 2.1W | 32.7W | 방사선량 1457% 증가 |
작동 온도 | 68°C | 59°C | 9°C 감소 |
구성 요소 수명 | 8개월 | >24개월 이상 | 3배 개선 |
구현 비용 | – | 실린더당 $175 | 4.2개월 투자 회수 |
복사 대 기타 열 전달 모드
효율적인 열 관리를 위해서는 복사열이 지배적인 시기를 파악하는 것이 중요합니다:
조건 | 전도 우위 | 대류 우세 | 방사선 우위 |
---|---|---|---|
온도 범위 | 낮음에서 높음으로 | 낮음에서 중간 | 중간에서 높음 |
머티리얼 속성 | 하이케이 소재 | 낮은 k, 높은 표면적 | 높은 ε 표면 |
환경적 요인 | 우수한 열 접촉 | 움직이는 공기, 팬 | 큰 온도 차이 |
공간 제약 | 견고한 포장 | 개방형 공기 흐름 | 시원한 주변 환경 보기 |
최고의 애플리케이션 | 컴포넌트 인터페이스 | 일반 냉각 | 뜨거운 표면, 진공, 정적 공기 |
결론
전도 계수 계산, 대류 향상 방법, 복사 효율 모델링 등 열 전달 원리를 숙지하면 공압 시스템의 효과적인 열 관리를 위한 토대를 마련할 수 있습니다. 이러한 원리를 적용하면 작동 온도를 낮추고 부품 수명을 연장하며 에너지 효율을 개선하는 동시에 까다로운 환경에서도 안정적인 작동을 보장할 수 있습니다.
공압 시스템의 열전달에 관한 FAQ
작동 중 공압 실린더의 일반적인 온도 상승은 어느 정도인가요?
공압 실린더는 일반적으로 연속 작동 중에 주변 온도보다 20~40°C 정도 온도가 상승합니다. 이러한 온도 상승은 씰과 실린더 벽 사이의 마찰, 공기의 압축 가열, 기계 작업이 열로 변환되는 과정에서 발생합니다. 로드리스 실린더는 더 복잡한 씰링 시스템과 베어링/씰 어셈블리의 집중된 열 발생으로 인해 더 높은 온도 상승(30~50°C)을 경험하는 경우가 많습니다.
작동 압력은 공압 시스템의 열 발생에 어떤 영향을 미칩니까?
작동 압력은 열 발생에 큰 영향을 미치며, 압력이 높을수록 여러 메커니즘을 통해 더 많은 열이 발생합니다. 씰과 표면 사이의 마찰력 증가, 압축 가열 증가, 누출 관련 손실 증가로 인해 일반적으로 작동 압력이 1bar 증가할 때마다 열 발생량이 8~12% 증가합니다. 이 관계는 정상 작동 범위(3~10bar) 내에서 거의 선형적입니다.
다양한 환경에서 공압 부품을 위한 최적의 냉각 방식은 무엇일까요?
최적의 냉각 방식은 환경에 따라 달라지는데, 청결하고 중간 온도(15~30°C)의 환경에서는 적절한 부품 간격을 유지한 자연 대류만으로도 충분한 경우가 많습니다. 고온 환경(30~50°C)에서는 팬이나 압축 공기를 이용한 강제 대류가 필요합니다. 극도로 더운 환경(50°C 이상)이나 공기 흐름이 제한되는 곳에서는 열전 냉각기나 액체 냉각과 같은 능동적인 냉각 방법이 필요할 수 있습니다. 모든 경우에 방사율이 높은 표면을 통해 방사를 최대화하면 추가적인 수동 냉각이 가능합니다.
공압 부품의 총 열 전달량은 어떻게 계산하나요?
각 메커니즘의 기여도를 합산하여 총 열 전달량을 계산합니다: Q총계 = Q전도 + Q대류 + Q복사. 전도의 경우 각 열 경로에 대해 Q = kA(T₁-T₂)/L을 사용합니다. 대류의 경우 적절한 대류 계수와 함께 Q = hA(Ts-T∞)를 사용합니다. 복사의 경우 Q = εσA(T₁⁴-T₂⁴)를 사용합니다. 30~80°C에서 작동하는 대부분의 산업용 공압 애플리케이션에서 대략적인 분포는 전도 20~40%, 대류 40~70%, 복사 10~30%입니다.
온도와 공압 부품 수명은 어떤 관계가 있나요?
부품 수명은 수정된 아레니우스 관계에 따라 온도가 상승함에 따라 기하급수적으로 감소합니다. 일반적으로 작동 온도가 10°C 상승할 때마다 씰 및 부품 수명은 40~50% 감소합니다. 즉, 70°C에서 작동하는 부품은 50°C에서 작동하는 동일한 부품보다 수명이 1/3에 불과할 수 있습니다. 이 관계는 공압 시스템의 유지보수 주기를 결정하는 씰, 베어링, 개스킷과 같은 폴리머 구성품에 특히 중요합니다.
-
열전도율과 온도 구배에 따라 고체 물질을 통해 열이 전도되는 방식을 설명하는 기본 원리인 푸리에의 법칙에 대한 기초적인 설명을 제공합니다. ↩
-
열전도를 개선하고 열 저항을 줄이기 위해 부품 사이의 미세한 공기 간격을 메우는 데 사용되는 열 인터페이스 재료(TIM)의 기능과 종류에 대해 설명합니다. ↩
-
시스템 냉각 설계의 핵심 요소인 대류를 통해 주변 유체에 열을 전달하여 물체를 냉각시키는 뉴턴의 냉각 법칙의 원리에 대해 자세히 설명합니다. ↩
-
유체 역학 및 열 전달에서 경계를 가로지르는 대류 대 전도 열 전달의 비율을 나타내는 차원이 없는 중요한 양인 누셀 수에 대해 자세히 살펴봅니다. ↩
-
뜨거운 표면의 열 손실을 계산하는 데 필수적인 흑체가 복사하는 총 에너지를 정량화하는 기본 물리 원리인 스테판-볼츠만 법칙에 대해 설명합니다. ↩