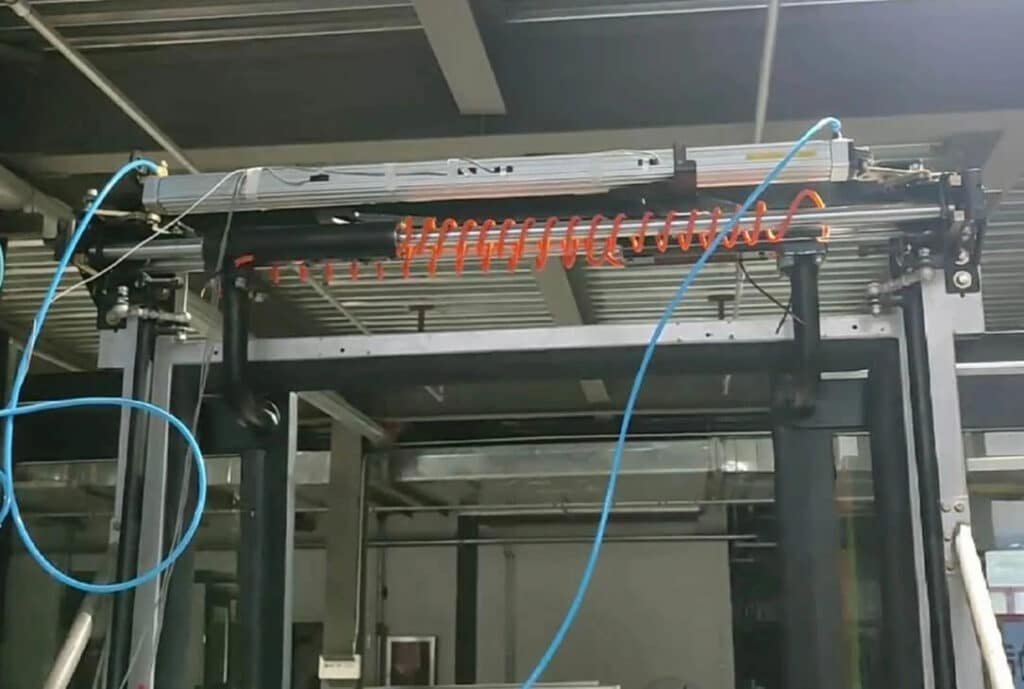
Sliter du med ineffektive pakkelinjer som ikke klarer å holde tritt med produksjonskravene? Mange pakkeoperasjoner står overfor betydelige utfordringer med tradisjonelle pneumatiske systemer som begrenser hastighet, presisjon og fleksibilitet, noe som resulterer i kostbare flaskehalser og vedlikeholdsproblemer.
Pneumatiske sylindere uten stang kan forbedre ytelsen til pakkemaskiner dramatisk ved å muliggjøre raskere syklustider, mer presis posisjonering, plassbesparende design og økt pålitelighet - noe som gir opptil 40% høyere gjennomstrømning i høyhastighets pakkeapplikasjoner.
Jeg besøkte nylig et matemballasjeanlegg i Tyskland, der det konvensjonelle sylinderbaserte pick-and-place-systemet skapte en stor flaskehals i produksjonen. Etter å ha tatt i bruk vår løsning med stangløse sylindere økte de pakkehastigheten med 35%, samtidig som de reduserte maskinens fotavtrykk med nesten halvparten. La meg vise deg hvordan lignende resultater er mulig for din virksomhet.
Innholdsfortegnelse
- Hva gjør høyhastighets gripemekanismer mer effektive med sylindere uten stang?
- Hvordan kan synkronisering av flere akser revolusjonere pakkeeffektiviteten?
- Hvorfor er antikollisjonssensorsystemer avgjørende for moderne pakkelinjer?
- Konklusjon
- Vanlige spørsmål om stangløse sylindere i emballasjeapplikasjoner
Hva gjør høyhastighets gripemekanismer mer effektive med sylindere uten stang?
Høyhastighets gripemekanismer er en av de mest utfordrende aspektene ved design av pakkemaskiner, ettersom de krever både hastighet og presisjon under kontinuerlig drift.
Høyhastighets gripemekanismer blir betydelig mer effektive med sylindere uten stang fordi de gir lavere bevegelig masse, muliggjør raskere akselerasjons-/retardasjonssykluser, gir mer kompakt integrering med Endeffektorer1og leverer jevn ytelse selv ved syklushastigheter på over 120 plukk per minutt.

Etter å ha implementert dusinvis av høyhastighets gripeløsninger i Europa og Nord-Amerika, har jeg identifisert flere kritiske faktorer som er avgjørende for suksess i disse krevende bruksområdene. Riktig konfigurasjon av den stangløse sylinderen utgjør hele forskjellen.
Viktige ytelsesfaktorer for høyhastighetsgriping
Når man designer høyhastighets gripesystemer for emballasje, er det flere elementer som må optimaliseres samtidig:
- Masseoptimalisering: Hvert gram teller ved høye syklushastigheter
- Akselerasjonsprofiler: Jevn ramping forhindrer produktskader
- Presisjon i høy hastighet: Opprettholder nøyaktigheten under raske bevegelser
- Konsistens i syklusen: Samme ytelse over millioner av sykluser
Sammenlignende prestasjonsanalyse
Parameter | Tradisjonell sylinder | Sylinder uten stang | Prestasjonsfordel |
---|---|---|---|
Masse i bevegelse | Høy (stang + ekstern mekanisme) | Lav (integrert vogn) | 30-50% raskere akselerasjon |
Kapasitet for syklushastighet | 40-60 sykluser/minutt | 100-140 sykluser/minutt | 2-3 ganger høyere gjennomstrømning |
Krav til fotavtrykk | Stor (slaglengde + sylinderlengde) | Kompakt (kun slaglengde) | 40-60% plassreduksjon |
Vedlikeholdsintervall | 3-5 millioner sykluser | 10-15 millioner sykluser | Betydelig redusert nedetid |
Casestudie av konfigurasjon: Emballering av konfekt
En av mine mest vellykkede implementeringer var for en produsent av premiumsjokolade i Sveits. Deres utfordring:
- Pakker delikate praliner i en hastighet på over 100 enheter per minutt
- Håndterer varierende produktstørrelser uten omstillinger
- Vær forsiktig med håndteringen for å unngå produktskader
- Kontinuerlig drift over tre skift
Løsningsarkitekturen
Vi utviklet en tilpasset konfigurasjon med:
Primær bevegelsesakse
- Magnetisk sylinder uten stang (tilsvarende MY1B40-serien)
- 400 mm slaglengde optimalisert for pakkelinjens layout
- Høy respons proporsjonal strømningsregulering for akselerasjonsstyringIntegrering av gripetang
- Lett monteringsbrakett i karbonfiber
- Vakuumkoppoppstilling med uavhengig fjæring
- Hurtigbyttegrensesnitt for vedlikeholdKontrollsystem
- Posisjonstilbakemelding med berøringsfrie sensorer
- Programmerbare bevegelsesprofiler for ulike produkttyper
- Syklusovervåking i sanntid med varsler om prediktivt vedlikehold
Resultatene var imponerende:
- Økt gjennomstrømning fra 60 til 110 enheter per minutt
- Redusert produktskade med 85%
- Redusert nedetid for vedlikehold med 67%
Den viktigste suksessfaktoren var å forstå at høyhastighetsgriping ikke bare handler om rå hastighet - det handler om kontrollerte, presise bevegelser som kan opprettholdes på en pålitelig måte over millioner av sykluser. Sylindere uten stenger er den ideelle plattformen for å oppnå denne balansen.
Hvordan kan synkronisering av flere akser revolusjonere pakkeeffektiviteten?
Synkronisering av flere akser representerer det neste steget innen emballasjeautomatisering, og muliggjør komplekse bevegelser som tidligere var umulige med konvensjonelle systemer.
Fleraksesynkronisering med stangløse sylindere revolusjonerer pakkeeffektiviteten ved å muliggjøre komplekse tredimensjonale bevegelser, legge til rette for sømløs produktflyt, eliminere overføringspunkter mellom operasjoner og muliggjøre dynamisk tilpasning til ulike pakkestørrelser uten mekaniske omstillinger.

I løpet av min karriere med å implementere emballasjeløsninger har jeg sett en tydelig utvikling mot mer sofistikerte fleraksede systemer. Den nyeste generasjonen av stangløs sylinderteknologi har vært en game-changer på dette området.
Synkroniseringsarkitekturer for pakkeapplikasjoner
Moderne pakkesystemer bruker vanligvis én av flere synkroniseringsmetoder:
Mekanisk synkronisering
Tradisjonelle metoder inkluderer:
- Kamdrevne mekanismer
- Mekaniske koblinger
- Girbaserte tidtakingssystemer
Disse tilnærmingene tilbyr:
- Enkel implementering
- Begrenset fleksibilitet
- Vanskelig omstilling for ulike produkter
- Høye krav til vedlikehold
Pneumatisk synkronisering av flere akser
Avanserte, stangløse sylindersystemer leverer:
- Elektronisk overvåking av posisjon
- Proporsjonal trykk-/strømregulering
- Uavhengig aksejustering
- Programmerbare bevegelsesprofiler
Programmeringsmetoder for fleraksede systemer
Synkroniseringsmetode | Programmeringstilnærming | Fordeler | Beste bruksområder |
---|---|---|---|
Master/Slave2 | Én akse styrer timingen av de andre | Forenklet programmering | Kartongering, pakking i esker |
Koordinert bevegelse | Alle akser følger programmerte baner | Kompleks bevegelsesevne | Wrap-around-emballasje |
Uavhengig med sjekkpunkter | Aksene beveger seg uavhengig av hverandre, men venter på koordineringspunkter | Fleksibel timing | Håndtering av blandede produkter |
Dynamisk traségenerering | Beregning av bane i sanntid basert på produktflyt | Tilpasser seg variasjoner | Tilfeldig produktankomst |
Implementeringscase: Fleksibel poseemballasje
Jeg hjalp nylig en matvareprodusent i Frankrike med å oppgradere posesystemet sitt. Utfordringene deres var blant annet
Håndtering av flere pakkestørrelser
- Syv forskjellige posedimensjoner
- Hyppige bytter mellom produkter
- Inkonsekvent avstand mellom produktankomsteneKomplekse bevegelseskrav
- Produktrotasjon under innsetting
- Skånsom akselerasjon for flytende produkter
- Nøyaktig posisjonering for tetningens integritet
Vi har implementert et treakset sylindersystem uten stang med:
- X-akse: 800 mm horisontal bevegelse (produktvalg)
- Y-akse: 400 mm vertikal bevegelse (innsettingsdybde)
- Z-akse: 200 mm sideveis bevegelse (justeringskontroll)
Synkroniseringsprogrammeringen er inkludert:
- Integrasjon av synssystemer3 for produktidentifikasjon
- Dynamisk banegenerering basert på innkommende produktavstand
- Justering av akselerasjonsprofilen basert på fyllingsgrad
- Posisjonsverifisering før kritiske operasjoner
Resultatene forandret virksomheten deres:
- Omstillingstiden reduseres fra 45 minutter til under 5 minutter
- Produksjonshastigheten økte med 40%
- Fleksibilitet til å håndtere nye pakningsstørrelser uten mekaniske endringer
- Betydelig reduksjon i antall tetningsfeil og produktskader
Den viktigste innsikten var å innse at ekte synkronisering ikke bare handler om å koordinere bevegelser - det krever integrert sensing, dynamisk justering og intelligent baneplanlegging. Sylindere uten stenger er den ideelle plattformen for dette sofistikerte nivået.
Hvorfor er antikollisjonssensorsystemer avgjørende for moderne pakkelinjer?
Etter hvert som emballasjesystemene blir mer komplekse og kompakte, øker risikoen for komponentkollisjoner dramatisk, noe som gjør det avgjørende med gode sensorsystemer.
Antikollisjonssensorsystemer er avgjørende for moderne pakkelinjer fordi de forhindrer kostbare skader på utstyret, eliminerer uventet nedetid, beskytter verdifulle produkter mot skader og muliggjør maskindesign med høyere tetthet som maksimerer produktiviteten på begrenset gulvplass.
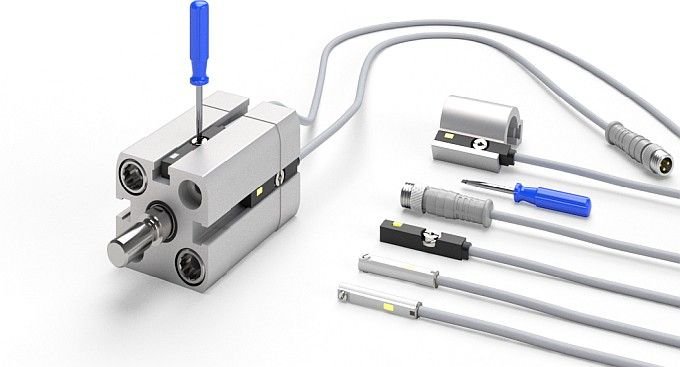
Etter å ha håndtert en rekke kollisjonsrelaterte feil i emballasjesystemer, kan jeg bekrefte hvor viktig det er å implementere sensorer på riktig måte. De økonomiske konsekvensene av selv én enkelt kollisjon kan være betydelige.
Vurdering av kollisjonsrisiko i emballasjesystemer
Moderne pakkelinjer står overfor flere kategorier av kollisjonsrisiko:
Kollisjoner i den interne mekanismen
- Mellom bevegelige komponenter i en og samme maskin
- Ofte forårsaket av tids- eller synkroniseringsfeilKollisjoner mellom produkt og mekanisme
- Mellom emballasjematerialer og maskinkomponenter
- Typisk som følge av produktstopp eller feilmatingEksterne kollisjoner
- Mellom tilstøtende maskiner eller operatørinteraksjon
- Ofte relatert til vedlikeholdsaktiviteter eller prosessjusteringer
Sensorteknologi for kollisjonsforebygging
Sensortype | Driftsprinsipp | Fordeler | Begrensninger |
---|---|---|---|
Nærhetssensorer4 | Oppdager objekter i nærheten uten kontakt | Rask respons, enkel implementering | Begrenset deteksjonsområde |
Gjennomstrålende fotoelektrisk | Oppdager avbrudd i strålen | Pålitelig i støvete omgivelser | Fast deteksjonssone |
Områdescannere | Overvåk definerte sikkerhetssoner | Fleksible beskyttelsesområder | Høyere kostnader |
Kraft-/momentsensorer | Oppdager motstand mot bevegelse | Kan fornemme forestående kollisjoner | Kompleks integrasjon |
Vision Systems | Kamerabasert objektdeteksjon | Omfattende overvåking | Bearbeidingskostnader |
Praktisk strategi for sensoroppsett
Ved implementering av antikollisjonssystemer med stangløse sylindere anbefaler jeg denne strukturerte tilnærmingen:
1. Identifisering av kritisk sone
Først må du identifisere alle potensielle kollisjonspunkter:
- Posisjoner ved slutten av slaget
- Krysningspunkter mellom aksene
- Produktoverføringssteder
- Interaksjonsområder for operatører
2. Valg og plassering av sensorer
Velg passende sensorer for hver sone basert på:
- Nødvendig deteksjonshastighet
- Miljøforhold (støv, fuktighet osv.)
- Plassbegrensninger
- Krav til pålitelighet
3. Integrering med kontrollsystemer
Utvikle en omfattende sikkerhetsarkitektur:
- Primær kollisjonsbeskyttelse (normal drift)
- Sekundære sikkerhetstiltak (feiltilstander)
- Beredskapsprotokoller
Implementering i den virkelige verden: Blisterpakkelinje
En kunde i Italia som emballerer legemidler, opplevde hyppige kollisjoner i blisterpakkelinjen, noe som resulterte i
- Omtrent 4-6 timers nedetid per måned
- Kostnader for reservedeler som overstiger 5 000 euro per kvartal
- Produkttap fra skadede pakker
Vi har implementert et omfattende antikollisjonssystem med
Overvåking av sylinderposisjon
- Magnetiske sensorer i kritiske posisjoner
- Kontinuerlig posisjonstilbakemelding på akser med lange slag
- Signalredundans for kritiske sonerDynamiske beskyttelsessoner
- Justerbare deteksjonsområder basert på pakningsstørrelse
- Prediktiv kollisjonsmodellering i kontrollsystemet
- Muligheter for banejustering i sanntidIntegrert sikkerhetsrespons
- Gradert fartsreduksjon nær potensielle kollisjonspunkter
- Kontrollert nødstopp for å forhindre produktskader
- Automatiserte gjenopprettingssekvenser etter feilretting
Resultatene var umiddelbare og betydelige:
- Ingen kollisjonshendelser i løpet av de 18 månedene som har gått siden implementeringen
- Økt maskinhastighet på grunn av tillit til beskyttelsessystemene
- Mulighet til å operere med tettere avstand mellom komponentene
- Betydelig reduksjon i vedlikeholdskostnadene
Den viktigste innsikten var å innse at effektiv kollisjonsforebygging ikke bare handler om å oppdage potensielle kollisjoner - det handler om å skape et omfattende system som forutser, forebygger og håndterer potensielle kollisjonsscenarioer på en sikker måte gjennom hele pakkeprosessen.
Konklusjon
Sylindere uten stang gir emballasjemaskiner helt nye fordeler, med den hastigheten, presisjonen og påliteligheten som trengs for gripemekanismer med høy ytelse, synkronisering av flere akser og omfattende antikollisjonssystemer. Ved å implementere disse løsningene strategisk kan emballasjevirksomheter oppnå betydelige forbedringer i gjennomstrømning, fleksibilitet og driftseffektivitet.
Vanlige spørsmål om stangløse sylindere i emballasjeapplikasjoner
Hva er hastighetsbegrensningene for sylindere uten stang i emballasjeapplikasjoner?
Moderne stangløse pneumatiske sylindere kan oppnå hastigheter på opptil 3 meter per sekund i emballasjeapplikasjoner, med akselerasjonshastigheter på over 30 m/s². Optimal ytelse innebærer imidlertid vanligvis drift ved 1-2 m/s med kontrollerte akselerasjonsprofiler for å opprettholde presisjon og produktintegritet under håndteringsoperasjoner.
Hvordan er sylindere uten stang sammenlignet med elektriske aktuatorer for pakkemaskiner?
Stangløse pneumatiske sylindere har flere fordeler i forhold til elektriske aktuatorer i emballasjeapplikasjoner, blant annet lavere kostnader (vanligvis 30-40% mindre), bedre motstand mot vasking, enklere vedlikehold og utmerket kraft-til-størrelse-forhold. Elektriske aktuatorer kan imidlertid gi bedre posisjonskontroll for ekstremt presise bruksområder som krever flere stoppposisjoner.
Hvilket vedlikehold kreves for sylindere uten stang i høyhastighetspakking?
Stangløse sylindere i høyhastighetspakking krever vanligvis periodisk inspeksjon av tetningsbåndene (hver 3.-6. måned), verifisering av sensorjusteringen, sporadisk smøring i henhold til produsentens spesifikasjoner og overvåking av dempingens effektivitet. Riktig vedlikeholdte enheter kan fungere i 10-15 millioner sykluser før det er behov for større service.
Kan sylindere uten stang håndtere de varierende produktstørrelsene i fleksible pakkelinjer?
Ja, sylindere uten stang utmerker seg i fleksible emballasjeapplikasjoner på grunn av deres programmerbare posisjoneringsevne, justerbare hastighetsprofiler og muligheten til å integrere med syns- og sensorsystemer. Moderne systemer kan håndtere produktstørrelsesvariasjoner på 200% eller mer uten mekaniske justeringer ved hjelp av posisjonstilbakemelding og proporsjonal styringsteknologi.
Hva er den typiske avkastningen på investeringen ved oppgradering til stangløse sylindere i pakkemaskiner?
De fleste pakkevirksomheter oppnår avkastning på investeringen innen 6-12 måneder etter at de har oppgradert til stangløs sylinderteknologi. Avkastningen kommer fra økt gjennomstrømning (vanligvis 30-50% høyere), reduserte omstillingstider (ofte 80-90% raskere), lavere vedlikeholdskostnader og forbedret produktkvalitet med færre kassasjoner på grunn av håndteringsskader.
-
Gir en detaljert forklaring av end-of-arm tooling (EOAT), eller endeeffektorer, som er enhetene på enden av en robotarm eller lineær aktuator som er utformet for å samhandle med omgivelsene. ↩
-
Beskriver master-slave-styringsarkitekturen, en vanlig metode innen flerakset bevegelseskontroll der posisjonen til en primær "master"-akse dikterer bevegelsen til en eller flere sekundære "slave"-akser. ↩
-
Gir en oversikt over maskinsyn, teknologien og metodene som brukes til bildebasert automatisk inspeksjon og analyse for bruksområder som robotstyring, kvalitetskontroll og sortering. ↩
-
Forklarer arbeidsprinsippet til induktive nærhetssensorer, en vanlig type berøringsfri sensor som bruker et elektromagnetisk felt til å detektere tilstedeværelsen av metalliske objekter. ↩