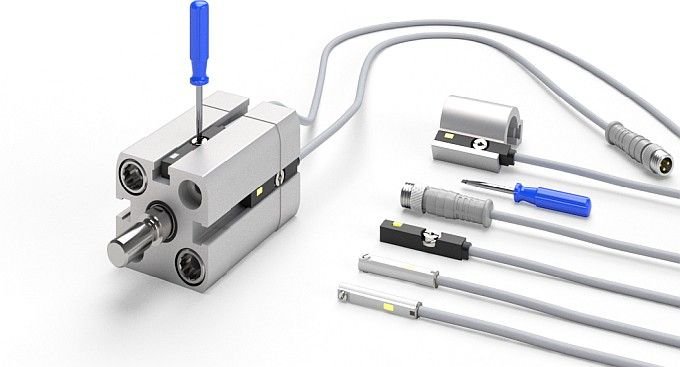
Se soočate z nepričakovanimi zaustavitvami strojev, nedoslednim delovanjem pnevmatskega sistema ali prezgodnjimi okvarami senzorjev v zahtevnih okoljih? Te pogoste težave so pogosto posledica neustrezne izbire senzorjev, kar vodi v drage zastoje, težave s kakovostjo in pretirano vzdrževanje. Z izbiro pravih pnevmatskih senzorjev lahko takoj rešite te kritične težave.
Idealen pnevmatski senzor mora biti ustrezno umerjen glede na specifične zahteve vašega sistema glede tlaka, odzivati se mora dovolj hitro, da zajame kritične dogodke pretoka, in zagotavljati ustrezno okoljsko zaščito za vaše delovne pogoje. Za pravilno izbiro je treba razumeti postopke umerjanja, metode preskušanja odzivnega časa in standarde zaščite.
Spomnim se, da sem lani obiskal obrat za predelavo hrane v Wisconsinu, kjer so zaradi poškodb pri pranju tlačna stikala zamenjali vsake 2-3 mesece. Po analizi njihove aplikacije in uvedbi ustrezno ocenjenih senzorjev z ustrezno zaščito IP67 se je pogostost zamenjav v naslednjem letu zmanjšala na nič, s čimer so prihranili več kot $32.000 EUR za izpade in material. Dovolite mi, da z vami delim znanje, ki sem se ga naučil v letih dela v pnevmatski industriji.
Kazalo vsebine
- Standardi in postopki umerjanja tlačnih stikal
- Kako preizkusiti in preveriti odzivni čas senzorja pretoka
- Izčrpen vodnik za oceno IP za težka okolja
Kako morate kalibrirati tlačna stikala za največjo natančnost in zanesljivost?
Ustrezno umerjanje tlačnega stikala zagotavlja natančne sprožitvene točke, preprečuje lažne alarme in povečuje zanesljivost sistema.
Kalibracija tlačnega stikala določa natančne nastavljene vrednosti vklopa in izklopa, pri čemer upošteva učinke histereze. Standardni postopki umerjanja vključujejo nadzorovano uporabo tlaka, nastavitev nastavljene vrednosti in preverjanje v dejanskih pogojih delovanja. Upoštevanje uveljavljenih protokolov umerjanja zagotavlja dosledno delovanje in podaljšuje življenjsko dobo senzorja.
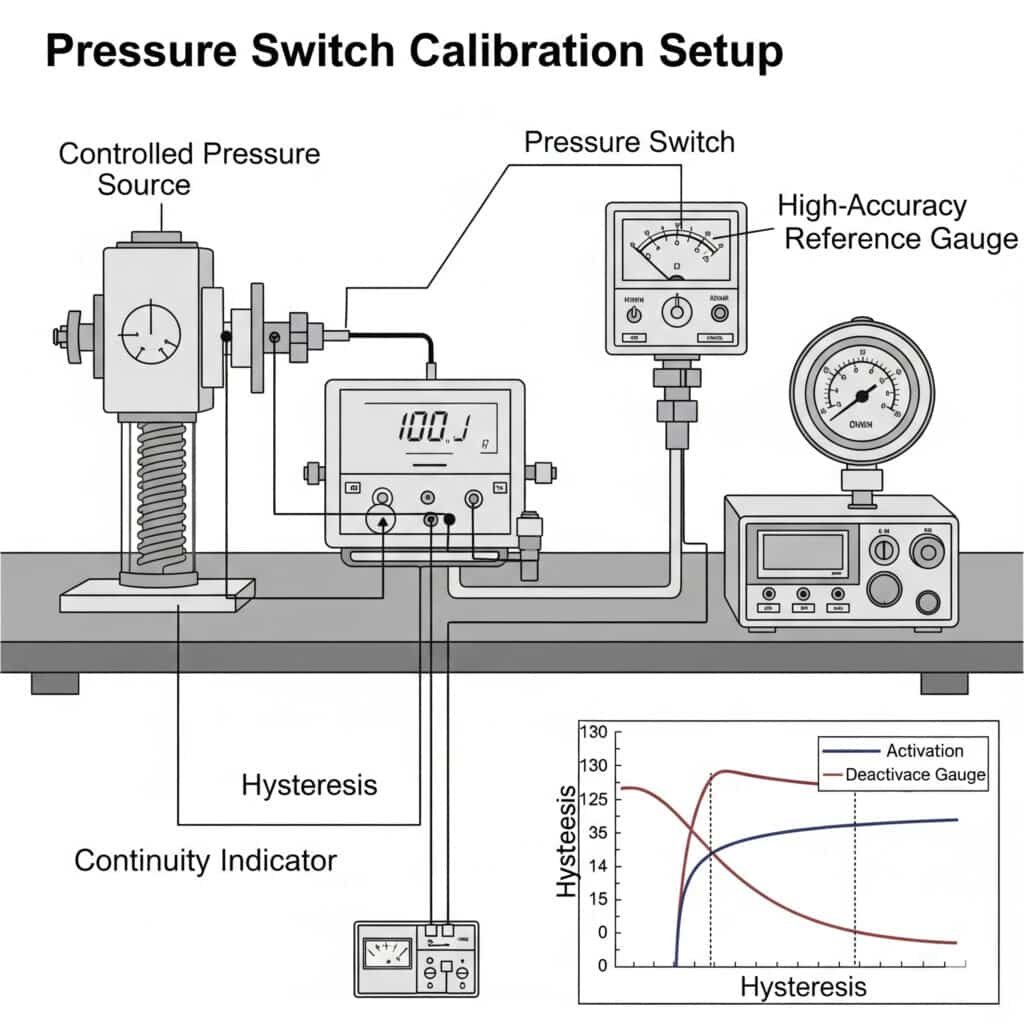
Razumevanje osnov tlačnih stikal
Preden se poglobite v postopke umerjanja, je treba razumeti ključne koncepte tlačnih stikal:
Ključni parametri tlačnega stikala
- Nastavljena vrednost (SP): Vrednost tlaka, pri kateri stikalo spremeni stanje
- Ponastavitvena točka (RP): Vrednost tlaka, pri kateri se stikalo vrne v prvotno stanje
- Histereza1: Razlika med nastavljeno in ponastavljeno točko
- Ponovljivost: Dosledno preklapljanje pri enaki vrednosti tlaka
- Natančnost: Odstopanje od prave vrednosti tlaka
- Mrtvi pas: Drug izraz za histerezo, razliko v tlaku med aktivacijo in deaktivacijo
Vrste tlačnih stikal in njihove kalibracijske značilnosti
Vrsta stikala | Metoda umerjanja | Tipična natančnost | Območje histereze | Najboljše aplikacije |
---|---|---|---|---|
Mehanska membrana | Ročna nastavitev | ±2-5% | 10-25% območja | Splošna industrija, občutljiva na stroške |
Batni tip | Ročna nastavitev | ±1-3% | 5-15% območja | Uporaba pri višjih tlakih |
Elektronski z zaslonom | Digitalno programiranje | ±0,5-2% | 0,5-10% (nastavljivo) | Natančne aplikacije, spremljanje podatkov |
Omogočeno s pametnimi napravami/IoT | Digitalno + daljinsko umerjanje | ±0,25-1% | 0,1-5% (programabilno) | Industrija 4.02, spremljanje na daljavo |
Bepto DigiSense | Digitalno s samodejno kompenzacijo | ±0,2-0,5% | 0,1-10% (programabilno) | Kritične aplikacije, različni pogoji |
Postopek umerjanja standardnega tlačnega stikala
Če želite zagotoviti natančno in zanesljivo delovanje tlačnega stikala, upoštevajte ta izčrpen postopek umerjanja:
Zahteve glede opreme
- Vir tlaka: zmožnost ustvarjanja stabilnega tlaka v celotnem zahtevanem območju
- Referenčni merilnik: Vsaj 4× natančnejše od kalibriranega stikala
- Strojna oprema za povezavo: Ustrezni priključki in adapterji
- Orodja za dokumentiranje: Obrazci za zapisovanje kalibracije ali digitalni sistem
Postopek kalibracije po korakih
Faza priprave
- Počakajte, da se stikalo aklimatizira na temperaturo okolice (najmanj 1 uro).
- Preverite, ali je kalibracija referenčnega merilnika trenutna.
- Preglejte stikalo za fizične poškodbe ali kontaminacijo.
- Dokumentirajte začetne nastavitve, preden jih spremenite.
- Sprostite ves tlak v sistemuZačetno preverjanje
- Priključite stikalo na sistem za umerjanje
- počasi izvajajte tlak do trenutne nastavljene vrednosti
- Evidentiranje dejanskega tlaka preklopa
- Počasi zmanjšajte tlak do ponastavitve.
- Zapišite dejanski ponastavljeni tlak
- Izračunajte dejansko histerezo
- Ponovite trikrat, da preverite ponovljivostPostopek prilagajanja
- Za mehanska stikala:
- Odstranite nastavitveni pokrov/zaporo
- Prilagodite mehanizem nastavljene vrednosti po navodilih proizvajalca
- Zategnite varovalno matico ali pritrdite mehanizem za nastavitev.
- Za elektronska stikala:
- Vstop v način programiranja
- Vnos želene nastavljene vrednosti in vrednosti histereze/reseta
- Shranjevanje nastavitev in izhod iz načina programiranjaPreveritveno testiranje
- Ponovite postopek začetnega preverjanja
- Potrdite, da je nastavljena vrednost znotraj zahtevanega odstopanja
- Potrdite, da je ponastavitvena točka/histerenca znotraj zahtevanega odstopanja.
- Izvedite najmanj 5 ciklov za preverjanje ponovljivosti
- Dokumentiranje končnih nastavitev in rezultatov preskusovNamestitev sistema
- Namestitev stikala v dejanski aplikaciji
- Izvedba funkcionalnega preskusa v normalnih pogojih delovanja
- Če je mogoče, preverite delovanje stikala pri ekstremnih procesih.
- Dokumentirajte parametre končne namestitve
Pogostost umerjanja in dokumentacija
Vzpostavite redni urnik umerjanja na podlagi:
- Priporočila proizvajalca: Običajno 6-12 mesecev
- Kritičnost aplikacije: Pogostejše za aplikacije, ki so pomembne za varnost
- Okoljski pogoji: Pogosteje v težkih okoljih
- Regulativne zahteve: Upoštevanje standardov, značilnih za posamezno panogo.
- Zgodovinska uspešnost: Prilagodite na podlagi odstopanj, ugotovljenih pri prejšnjih kalibracijah.
Vodenje podrobnih zapisov o kalibraciji, vključno z:
- Podatki o datumu in tehniku
- Nastavitve po najdbi in po zapustitvi
- Uporabljena referenčna oprema in stanje njene kalibracije
- Okoljski pogoji med umerjanjem
- Opazovane nepravilnosti ali pomisleki
- Naslednji načrtovani datum umerjanja
Optimizacija histereze za različne aplikacije
Pravilna nastavitev histereze je ključnega pomena za delovanje aplikacije:
Vrsta uporabe | Priporočena histereza | Razmišljanje |
---|---|---|
Natančen nadzor tlaka | 0,5-2% območja | Zmanjšuje nihanja tlaka |
Splošna avtomatizacija | 3-10% obsega | Preprečuje hitro kolesarjenje |
Upravljanje kompresorja | 10-20% območja | Zmanjša pogostost zagona/zaustavitve |
Spremljanje alarmov | 5-15% območja | Preprečuje moteče alarme |
Pulzirajoči sistemi | 15-25% obsega | Prilagaja se običajnim nihanjem |
Pogosti izzivi in rešitve za umerjanje
Izziv | Možni vzroki | Rešitve |
---|---|---|
Nedosledno preklapljanje | Vibracije, pulzacije tlaka | Povečajte histerezo, dodajte dušenje |
Drsenje skozi čas | Temperaturne spremembe, mehanska obraba | Pogostejše umerjanje, nadgradnja z elektronskim stikalom |
Ni mogoče doseči zahtevane nastavljene vrednosti | Zunaj območja nastavitve | Nadomestite z ustreznim stikalom. |
Prevelika histereza | Mehansko trenje, konstrukcijske omejitve | Nadgradnja na elektronsko stikalo z nastavljivo histerezo |
Slaba ponovljivost | Kontaminacija, mehanska obraba | Očistite ali zamenjajte stikalo, dodajte filtriranje |
Študija primera: Optimizacija kalibracije tlačnega stikala
Pred kratkim sem sodeloval s farmacevtskim proizvodnim obratom v New Jerseyju, ki je imel občasne lažne alarme iz tlačnih stikal, ki so nadzorovala kritične procesne linije. Njihov obstoječi postopek umerjanja je bil nedosleden in slabo dokumentiran.
Po analizi njihove uporabe:
- Zahtevana natančnost nastavljene vrednosti: ±1%
- Delovni tlak: 5,5 bara
- nihanja temperature okolja: 18-27°C
- Tlačne pulzacije zaradi batne opreme
Izvedli smo celovito rešitev:
- Nadgradnja z elektronskimi tlačnimi stikali Bepto DigiSense
- Razvit standardiziran postopek umerjanja s temperaturno kompenzacijo
- Optimizirane nastavitve histereze na 8% za prilagajanje pulziranju tlaka
- Izvedeno četrtletno preverjanje in letno popolno umerjanje
- Vzpostavljen sistem digitalne dokumentacije z zgodovinskimi trendi
Rezultati so bili pomembni:
- Zmanjšanje števila lažnih alarmov za 98%
- Čas umerjanja se je skrajšal s 45 minut na 15 minut na stikalo
- Skladnost dokumentacije je izboljšana na 100%
- Izrazito izboljšana zanesljivost procesov
- Letni prihranki v višini približno $45,000 zaradi krajšega časa izpada
Kako lahko natančno preizkusite odzivni čas senzorja pretoka za kritične aplikacije?
Odzivni čas senzorja pretoka je ključnega pomena pri aplikacijah, ki zahtevajo hitro zaznavanje sprememb pretoka, zlasti v varnostnih sistemih ali hitrih procesih.
Odzivni čas senzorja pretoka meri, kako hitro senzor zazna in signalizira spremembo pogojev pretoka. Standardno testiranje vključuje ustvarjanje nadzorovanih stopenjskih sprememb pretoka, medtem ko se izhodni podatki senzorja spremljajo z opremo za hiter zajem podatkov. Razumevanje značilnosti odziva zagotavlja, da lahko senzorji zaznajo kritične dogodke, preden pride do poškodbe sistema.
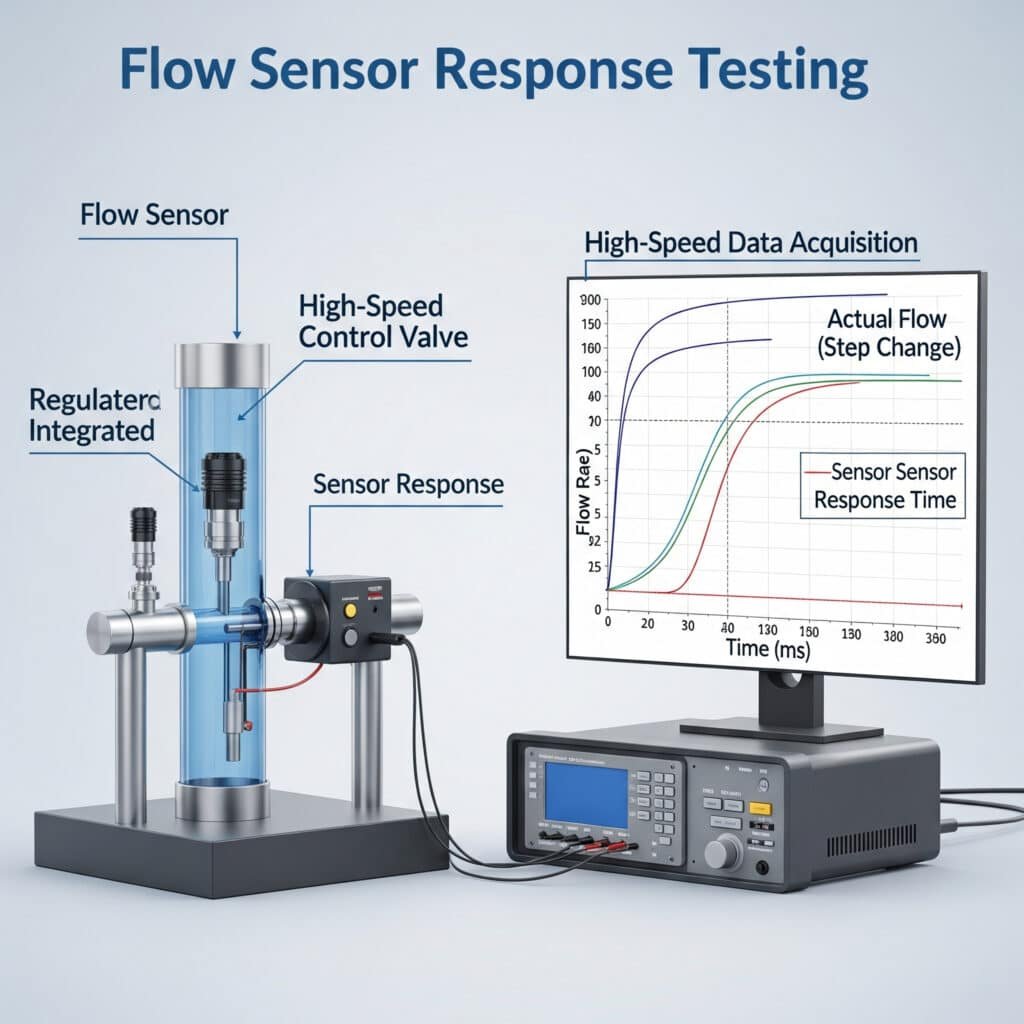
Razumevanje dinamike odziva senzorjev pretoka
Odzivni čas senzorja pretoka vključuje več različnih komponent:
Ključni parametri odzivnega časa
- Mrtvi čas (T₀): Začetna zakasnitev pred začetkom odziva senzorja
- Čas naraščanja (T₁₀₋₉₀): Čas za dvig od 10% do 90% končne vrednosti
- Čas poravnave (Tₛ): Čas za doseganje in ohranjanje ±2% končne vrednosti
- Odzivni čas (T₉₀): Čas za dosego 90% končne vrednosti (najpogosteje določen)
- Prekoračitev: Najvišja vrednost je presežena nad končno stabilno vrednostjo
- Čas okrevanja: Čas do vrnitve v normalno stanje po vrnitvi pretoka v začetno stanje
Metodologija testiranja odzivnega časa senzorja pretoka
Za pravilno preizkušanje odziva senzorja pretoka sta potrebna specializirana oprema in postopki:
Zahteve za preskusno opremo
- Generator pretoka: zmožnost hitrega in ponovljivega spreminjanja pretoka po korakih
- Referenčni senzor: z odzivnim časom, ki je vsaj 5× hitrejši od testiranega senzorja
- Sistem za zajem podatkov: Hitrost vzorčenja vsaj 10× hitrejša od pričakovanega odzivnega časa
- Oblikovanje signala: Primerno za tip izhoda senzorja
- Programska oprema za analizo: zmožnost izračuna parametrov odziva
Standardni preskusni postopek
Priprava testne nastavitve
- Senzor namestite v skladu s specifikacijami proizvajalca
- Povezava s sistemom za zajem podatkov
- Preverjanje pravilnega delovanja senzorja v ustaljenem stanju
- Konfiguracija hitro delujočega ventila ali regulatorja pretoka
- Vzpostavitev osnovnih pogojev pretokaPreizkušanje stopenjskih sprememb (povečanje pretoka)
- Vzpostavitev stabilnega začetnega pretoka (običajno nič ali najmanj)
- Vsaj 30 sekund beležite osnovni izhod.
- Hitro postopno povečanje pretoka (čas odpiranja ventila mora biti <10% pričakovanega odzivnega časa).
- Snemanje izhodnega signala senzorja z visoko frekvenco vzorčenja
- Ohranjajte končni pretok, dokler se proizvodnja popolnoma ne stabilizira.
- Za statistično veljavnost ponovite najmanj petkrat.Preizkušanje stopenjskih sprememb (zmanjševanje pretoka)
- Vzpostavitev stabilnega začetnega pretoka pri največji preskusni vrednosti
- Vsaj 30 sekund beležite osnovni izhod.
- Hitro postopno zmanjševanje pretoka
- Snemanje izhodnega signala senzorja z visoko frekvenco vzorčenja
- Ohranjajte končni pretok, dokler se proizvodnja popolnoma ne stabilizira.
- Za statistično veljavnost ponovite najmanj petkrat.Analiza podatkov
- Izračun povprečnih parametrov odziva iz več testov
- Določite standardni odklon, da ocenite skladnost
- Primerjajte z zahtevami vloge
- Dokumentiranje vseh rezultatov
Primerjava odzivnega časa senzorja pretoka
Tip senzorja | Tehnologija | Tipičen odziv T₉₀ | Najboljše aplikacije | Omejitve |
---|---|---|---|---|
Toplotni masni pretok | Vroča žica/film | 1-5 sekund | Čisti plini, nizek pretok | Počasen odziv, na katerega vpliva temperatura |
Turbina | Mehansko vrtenje | 50-250 milisekund | Čiste tekočine, srednji pretoki | Gibljivi deli, potrebno vzdrževanje |
Vortex | Izločanje vrtincev | 100-500 milisekund | Para, industrijski plini | Najmanjši zahtevani pretok |
Diferenčni tlak | Padec tlaka | 100-500 milisekund | Splošno uporaben, varčen | Vpliv sprememb gostote |
Ultrazvok | Tranzitni čas | 50-200 milisekund | Čiščenje tekočin, velikih cevi | Vpliv mehurčkov/delcev |
Coriolis3 | Merjenje mase | 100-500 milisekund | Visoka natančnost, masni pretok | Drago, omejitve velikosti |
Bepto QuickSense | Hibridni toplotni/tlačni sistem | 30-100 milisekund | Kritične aplikacije, odkrivanje uhajanja | Premium cene |
Zahteve za odzivanje, specifične za aplikacijo
Različne aplikacije imajo posebne zahteve glede odzivnega časa:
Aplikacija | Zahtevani odzivni čas | Kritični dejavniki |
---|---|---|
Odkrivanje puščanja | <100 milisekund | Zgodnje odkrivanje preprečuje izgubo izdelkov in težave z varnostjo. |
Zaščita stroja | <200 milisekund | težave je treba odkriti, preden nastane škoda. |
Nadzor serije | <500 milisekund | vpliva na natančnost doziranja in kakovost izdelka |
Spremljanje procesov | <2 sekunde | Splošno usmerjanje in nadzor |
Izdaja računov/prenos skrbništva | <1 sekunda | Natančnost je pomembnejša od hitrosti |
Tehnike optimizacije odzivnega časa
Izboljšanje odzivnega časa senzorja pretoka:
Dejavniki za izbiro senzorja
- Po potrebi izberite hitrejše tehnologije.
- Izberite ustrezno velikost senzorja (manjši senzorji se običajno odzivajo hitreje).
- Razmislite o neposredni potopitvi in vgradnji s pipo
- Ocenite možnosti digitalnega in analognega izhodaOptimizacija namestitve
- Zmanjšajte mrtvo prostornino v priključkih senzorjev
- Zmanjšanje razdalje med procesom in senzorjem
- Odpravite nepotrebne napeljave ali omejitve
- Zagotovite pravilno usmeritev in smer tokaIzboljšave obdelave signalov
- Uporaba višjih frekvenc vzorčenja
- Izvajanje ustreznega filtriranja
- Razmislite o napovednih algoritmih za kritične aplikacije
- Uravnotežite zavrnitev hrupa in odzivni čas
Študija primera: Optimizacija odzivnega časa pretoka
Pred kratkim sem se posvetoval s proizvajalcem avtomobilskih delov v Michiganu, ki je imel težave s kakovostjo na stojalu za preskušanje hladilnih sistemov. Njihovi obstoječi senzorji pretoka niso zaznali kratkih prekinitev pretoka, ki so povzročale okvare delov na terenu.
Analiza je pokazala:
- Odzivni čas obstoječega senzorja: 1,2 sekunde
- Trajanje prekinitev pretoka: 200-400 milisekund
- Kritični prag zaznavanja: 50% zmanjšanje pretoka
- Čas preskusnega cikla: 45 sekund
Z uporabo senzorjev pretoka Bepto QuickSense z:
- Odzivni čas (T₉₀): 75 milisekund
- Digitalni izhod z vzorčenjem 1 kHz
- Optimiziran položaj za namestitev
- Algoritem za obdelavo signalov po meri
Rezultati so bili impresivni:
- 100% zaznavanje prekinitev pretoka >100 milisekund
- Delež lažno pozitivnih rezultatov <0,1%
- Zanesljivost testov izboljšana na raven Six Sigma
- Število garancijskih zahtevkov strank se je zmanjšalo za 87%
- Letni prihranki v višini približno $280.000
Katero stopnjo zaščite IP potrebujejo vaši pnevmatski senzorji za zahtevna okolja?
Izbira ustreznega Stopnja zaščite IP (zaščita pred vdorom)4 zagotavlja, da senzorji zdržijo zahtevne okoljske razmere brez prezgodnje okvare.
Stopnja IP določa odpornost senzorja na vdor trdnih delcev in tekočin s standardizirano dvomestno kodo. Prva številka (0-6) označuje zaščito pred trdnimi predmeti, druga številka (0-9) pa zaščito pred tekočinami. Ustrezno prilagajanje stopenj IP okoljskim pogojem bistveno izboljša zanesljivost in življenjsko dobo senzorja.
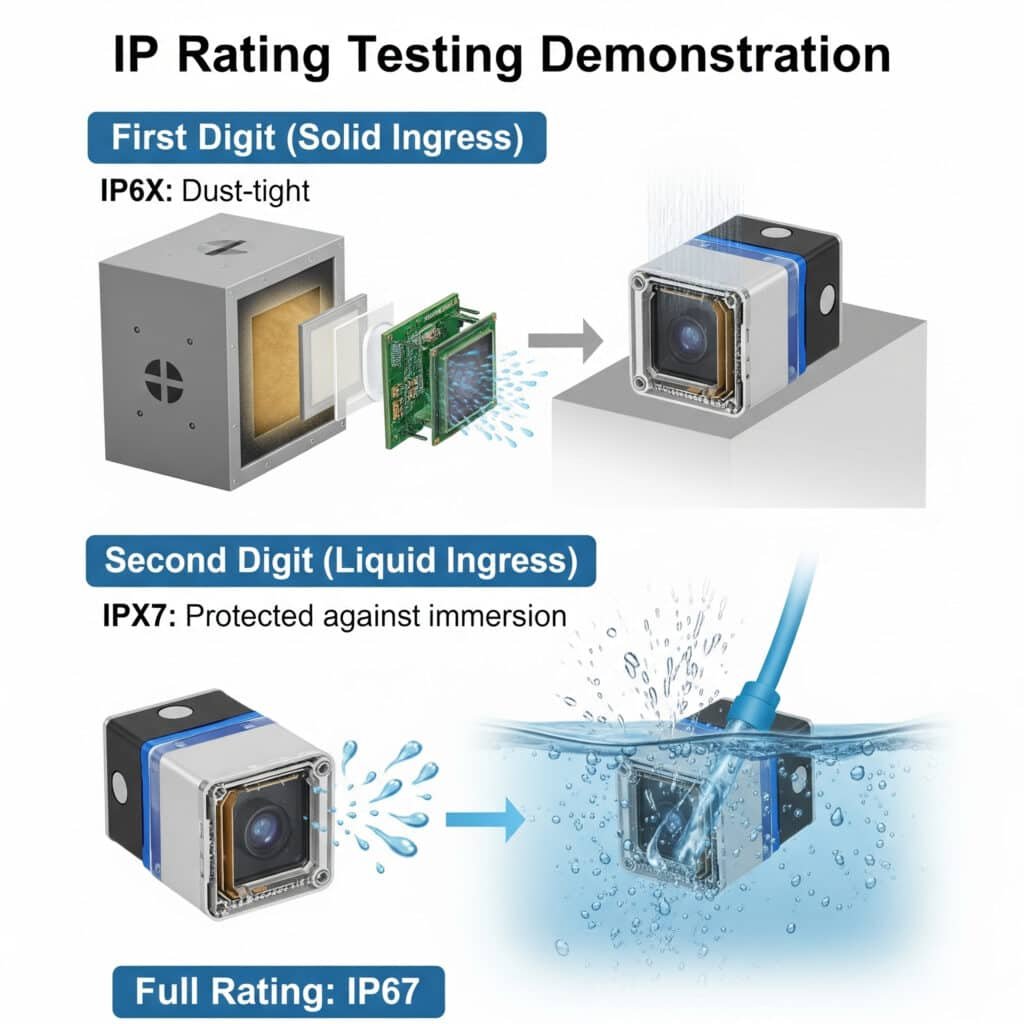
Razumevanje osnov ocenjevanja IP
Sistem zaščite IP (Ingress Protection) je opredeljen s standardom IEC 60529 in je sestavljen iz:
- Predpona IP: Označuje uporabljeni standard.
- Prva številka (0-6): Zaščita pred trdnimi predmeti in prahom
- Druga številka (0-9): Zaščita pred vodo in tekočinami
- Neobvezne črke: Dodatna posebna zaščita
Celovita referenčna tabela za oceno IP
Stopnja zaščite IP | Trdna zaščita | Zaščita pred tekočinami | Primerna okolja | Tipične aplikacije |
---|---|---|---|---|
IP00 | Brez zaščite | Brez zaščite | Čista in suha notranja okolja | Laboratorijska oprema, notranji sestavni deli |
IP20 | Zaščiteno pred predmeti >12,5 mm | Brez zaščite | Osnovna notranja okolja | Sestavni deli krmilne omare |
IP40 | Zaščiteno pred predmeti > 1 mm | Brez zaščite | Splošna uporaba v zaprtih prostorih | Prikazovalniki na plošči, zaprti upravljalni elementi |
IP54 | Zaščita pred prahom (omejen vdor) | Zaščiteno pred brizganjem vode | Lahka industrija, zaščitena na prostem | Splošni stroji, zunanje krmilne omarice |
IP65 | Odpornost na prah (brez vdora) | Zaščita pred vodnimi curki | Območja umivanja, izpostavljena na prostem | Oprema za predelavo hrane, zunanji senzorji |
IP66 | Odpornost na prah (brez vdora) | Zaščita pred močnimi vodnimi curki | Visokotlačno izpiranje | Težka industrijska oprema, pomorske aplikacije |
IP67 | Odpornost na prah (brez vdora) | Zaščita pred začasnim potopitvijo (do 1 m za 30 minut) | Občasno potopitev, močno izpiranje | Potopne črpalke, okolja z izpiranjem |
IP68 | Odpornost na prah (brez vdora) | Zaščita pred neprekinjenim potopitvijo (več kot 1 m, po podatkih proizvajalca) | Neprekinjeno potopitev | Podvodna oprema, potopni senzorji |
IP69K5 | Odpornost na prah (brez vdora) | Zaščiteno pred visokotemperaturnim in visokotlačnim izpiranjem | Čiščenje s paro, agresivno izpiranje | živilskopredelovalna, farmacevtska, mlečna industrija |
Prva številka: Zaščita pred trdnimi delci
Raven | Zaščita | Preskusna metoda | Učinkovito proti |
---|---|---|---|
0 | Brez zaščite | Ni | Brez zaščite |
1 | Predmeti >50 mm | 50 mm sonda | Veliki deli telesa (roka) |
2 | Predmeti >12,5 mm | 12,5 mm sonda | Prsti |
3 | Predmeti >2,5 mm | 2,5-milimetrska sonda | Orodja, debele žice |
4 | Predmeti >1 mm | 1 mm sonda | Večina žic, vijakov |
5 | Zaščiten prah | Preskus v prašni komori | Prah (dovoljen omejen vstop) |
6 | Tesen prah | Preskus v prašni komori | Prah (brez vdora) |
Druga številka: Zaščita pred vdorom tekočin
Raven | Zaščita | Preskusna metoda | Učinkovito proti |
---|---|---|---|
0 | Brez zaščite | Ni | Brez zaščite |
1 | Kapljanje vode | Preskus s kapljajočo vodo | Kondenzacija, rahlo kapljanje |
2 | Kapljanje vode (15° nagib) | Preskus nagiba za 15° | Kaplja, ko je nagnjena |
3 | Razprševanje vode | Preskus s pršenjem | Dež, škropilnice |
4 | brizganje vode | Preskus z brizganjem | brizganje iz katere koli smeri |
5 | Vodni curki | Preskus šobe 6,3 mm | Pranje pod nizkim tlakom |
6 | Močni vodni curki | Preskus 12,5 mm šobe | Močno morje, močno pranje |
7 | Začasno potopitev | 30min @ 1m potopitev | Začasne poplave |
8 | Neprekinjeno potopitev | Po podatkih proizvajalca | Neprekinjeno potopitev |
9K | Visokotemperaturni visokotlačni curki | 80 °C, 8-10 MPa, 10-15 cm | Čiščenje s paro, pranje pod pritiskom |
Zahteve glede stopnje zaščite IP, specifične za posamezno panogo
Različne panoge se soočajo s posebnimi okoljskimi izzivi, ki zahtevajo ustrezno zaščito:
Predelava hrane in pijač
- Tipične zahteve: IP65 do IP69K
- Okoljski izzivi:
- Pogosto izpiranje s kemikalijami
- Visokotlačno čiščenje z vročo vodo
- Potencialna kontaminacija z delci hrane
- Temperaturna nihanja - Priporočeni minimum: IP66 za splošna območja, IP69K za območja z neposrednim izpiranjem
Zunanja in težka industrija
- Tipične zahteve: IP65 do IP67
- Okoljski izzivi:
- Izpostavljenost vremenskim razmeram
- Prah in delci v zraku
- Občasna izpostavljenost vodi
- Temperaturni ekstremi - Priporočeni minimum: IP65 za zaščitena mesta, IP67 za izpostavljena mesta
Proizvodnja avtomobilov
- Tipične zahteve: IP54 do IP67
- Okoljski izzivi:
- Izpostavljenost olju in hladilni tekočini
- Kovinski drobci in prah
- Razpršitev pri varjenju
- Postopki čiščenja - Priporočeni minimum: IP65 za splošna območja, IP67 za območja, izpostavljena hladilni tekočini
Kemična predelava
- Tipične zahteve: IP65 do IP68
- Okoljski izzivi:
- Izpostavljenost jedkim kemikalijam
- Zahteve za izpiranje
- Potencialno eksplozivne atmosfere
- Visoka vlažnost - Priporočeni minimum: IP66 z ustrezno kemijsko odpornostjo
Zaščita senzorjev, ki presega stopnjo zaščite IP
Medtem ko ocene IP obravnavajo zaščito pred vdorom, je treba upoštevati tudi druge okoljske dejavnike:
Kemijska odpornost
- Preverite združljivost materiala ohišja s kemikalijami v procesu.
- Razmislite o PTFE, PVDF ali nerjavnem jeklu za kemična okolja.
- Ocenjevanje materialov za tesnila in tesnilne mase
Upoštevanje temperature
- Preverite temperaturna območja delovanja in shranjevanja
- Upoštevajte učinke termičnega cikliranja
- Ocenite potrebo po izolaciji ali hlajenju
Vibracijska in mehanska zaščita
- Preverite specifikacije za vibracije in udarce
- Razmislite o možnostih pritrditve za blaženje vibracij.
- Ocenite razbremenitev in zaščito kablov
Elektromagnetna zaščita
- Preverite ocene odpornosti EMC/EMI
- Upoštevajte zaščitene kable in ustrezno ozemljitev.
- Ocenite potrebo po dodatni električni zaščiti
Študija primera: Uspeh pri izbiri ocene IP
Pred kratkim sem sodeloval s podjetjem za predelavo mleka v Kaliforniji, ki je imelo pogoste okvare senzorjev v svojem sistemu CIP (Clean-in-Place). Obstoječi senzorji z razredom zaščite IP65 so odpovedali po 2-3 mesecih delovanja.
Analiza je pokazala:
- Vsakodnevno čiščenje s kavstično raztopino pri 85 °C
- Tedenski cikel kislinskega čiščenja
- Visokotlačno pršenje med ročnim čiščenjem
- Ciklično spreminjanje temperature okolice od 5 °C do 40 °C
Z namestitvijo senzorjev Bepto HygiSense z:
- Stopnja zaščite IP69K za zaščito pred visokimi temperaturami in visokimi tlaki
- Ohišje iz nerjavečega jekla 316L
- Tesnila EPDM za kemijsko združljivost
- Tovarniško zatesnjeni kabelski priključki
Rezultati so bili pomembni:
- Nič napak senzorja v več kot 18 mesecih delovanja
- Zmanjšanje stroškov vzdrževanja s 85%
- Zanesljivost sistema je izboljšana na 99,8%
- Čas obratovanja proizvodnje se je povečal za 3%
- Letni prihranki v višini približno $67,000
Vodnik za izbiro ocene IP glede na okolje
Okolje | Najmanjša priporočena stopnja zaščite IP | Ključni vidiki |
---|---|---|
Notranje, nadzorovano okolje | IP40 | Zaščita pred prahom, občasno čiščenje |
Splošna industrijska oprema v zaprtih prostorih | IP54 | Prah, občasna izpostavljenost vodi |
Strojna delavnica, lahka proizvodnja | IP65 | Hladila, čiščenje, kovinski drobci |
Na prostem, zaščiteno | IP65 | Dež, prah, temperaturne spremembe |
Na prostem, izpostavljeno | IP66/IP67 | Neposredna izpostavljenost vremenskim vplivom, možnost potopitve |
Okolja z izpiranjem | IP66 do IP69K | Kemikalije za čiščenje, tlak, temperatura |
Potopne aplikacije | IP68 | Neprekinjena izpostavljenost vodi, tlak |
Predelava hrane | IP69K | Sanitacija, kemikalije, čiščenje pri visoki temperaturi |
Zaključek
Za izbiro pravih pnevmatskih senzorjev je treba razumeti postopke kalibracije tlačnega stikala, metode testiranja odzivnega časa senzorja pretoka in ustrezne stopnje zaščite IP za določeno okolje. Z uporabo teh načel lahko optimizirate delovanje sistema, zmanjšate stroške vzdrževanja in zagotovite zanesljivo delovanje svoje pnevmatske opreme v vseh aplikacijah.
Pogosta vprašanja o izbiri pnevmatskega senzorja
Kako pogosto je treba kalibrirati tlačna stikala v tipičnem industrijskem okolju?
V tipičnih industrijskih okoljih je treba tlačna stikala kalibrirati vsakih 6-12 mesecev. Vendar je treba to pogostost povečati pri kritičnih aplikacijah, v težkih okoljih ali če je bilo pri prejšnjih kalibracijah opaženo odstopanje. Nekatere regulirane industrije imajo lahko posebne zahteve. Urnik umerjanja določite na podlagi priporočil proizvajalca in posebnih pogojev delovanja, nato pa ga prilagodite na podlagi preteklih podatkov o delovanju.
Kateri dejavniki poleg same tehnologije senzorja vplivajo na odzivni čas senzorja pretoka?
Poleg tehnologije senzorja na odzivni čas senzorja pretoka vplivajo tudi dejavniki namestitve (premer cevi, položaj senzorja, oddaljenost od motenj pretoka), značilnosti medija (viskoznost, gostota, temperatura), obdelava signala (filtriranje, stopnja vzorčenja, povprečenje) in okoljski pogoji (nihanje temperature, vibracije). Poleg tega velikost merjene spremembe pretoka vpliva na zaznani odzivni čas - večje spremembe se običajno zaznajo hitreje kot manjše spremembe.
Ali lahko uporabim senzor z nižjo stopnjo zaščite IP, če dodam dodatno zaščito, na primer ohišje?
Da, v ustreznem ohišju lahko uporabite senzor z nižjo stopnjo zaščite IP, če samo ohišje izpolnjuje okoljske zahteve in je pravilno nameščeno. Vendar ta pristop prinaša možne točke okvar na tesnilih ohišja in kabelskih vhodih. Upoštevajte potrebe po dostopnosti za vzdrževanje, morebitne težave s kondenzacijo v ohišju in zahteve glede odvajanja toplote. Pri kritičnih aplikacijah je na splošno zanesljivejša uporaba senzorjev z ustreznimi lastnimi ocenami IP.
Kako histereza v tlačnem stikalu vpliva na delovanje mojega pnevmatskega sistema?
Histereza v tlačnem stikalu ustvarja varovalni mehanizem med točkami vklopa in izklopa, kar preprečuje hitro kroženje, ko tlak niha okoli nastavljene vrednosti. Premajhna histereza lahko povzroči tresljaje (hitro vklapljanje in izklapljanje), ki poškodujejo stikalo in priključeno opremo ter povzročijo nestabilno delovanje sistema. Prevelika histereza lahko povzroči preveliko nihanje tlaka v sistemu. Optimalne nastavitve histereze uravnotežijo stabilnost in natančnost nadzora tlaka glede na posebne zahteve vaše uporabe.
Kakšna je razlika med ocenama IP67 in IP68 ter kako vem, katero oceno potrebujem?
Tako IP67 kot IP68 zagotavljata popolno zaščito pred vdorom prahu, razlikujeta pa se v zaščiti pred vodo: IP67 ščiti pred začasno potopitvijo (do 30 minut na globini 1 metra), medtem ko IP68 ščiti pred neprekinjeno potopitvijo na globini in v trajanju, ki ju določi proizvajalec. Za aplikacije, pri katerih lahko pride do občasnega kratkotrajnega potopitve, izberite IP67. IP68 izberite, kadar mora oprema zanesljivo delovati tudi ob stalnem potopljenju. Če sta za vašo aplikacijo določena globina in trajanje potopitve, uskladite te zahteve s proizvajalčevimi specifikacijami IP68.
Kako lahko preverim, ali se moj senzor pretoka odziva dovolj hitro za mojo aplikacijo?
Za preverjanje ustreznosti odzivnega časa senzorja pretoka primerjajte navedeni odzivni čas T₉₀ senzorja (čas za dosego 90% končne vrednosti) s kritičnim časovnim oknom vaše aplikacije. Za natančno preverjanje izvedite testiranje s postopno spremembo z uporabo hitrega sistema za zbiranje podatkov (vzorčenje vsaj 10× hitrejše od pričakovanega odzivnega časa) in hitro delujočega ventila. Ustvarite nenadne spremembe pretoka, ki so podobne tistim v vaši aplikaciji, medtem ko snemate izhodne podatke senzorja. Analizirajte krivuljo odziva, da izračunate dejanske parametre odziva in jih primerjate z zahtevami aplikacije.
-
Zagotavlja jasno opredelitev histereze v kontekstu senzorjev in nadzornih sistemov ter jo pojasnjuje kot pojav, pri katerem je izhodna vrednost na določeni vhodni točki odvisna od tega, ali se je tej točki približala z naraščajočim ali padajočim vhodom. ↩
-
Opisuje industrijo 4.0, znano tudi kot četrta industrijska revolucija, ki se nanaša na stalno avtomatizacijo tradicionalnih proizvodnih in industrijskih praks z uporabo sodobne pametne tehnologije, kot so internet stvari (IoT), računalništvo v oblaku in umetna inteligenca. ↩
-
Razloži načelo delovanja Coriolisovih merilnikov pretoka, ki uporabljajo Coriolisov učinek za neposredno merjenje masnega pretoka z vibriranjem cevi, skozi katero teče tekočina, in merjenjem nastalega zasuka. ↩
-
Podrobnosti o mednarodnem standardu IEC 60529, ki razvršča stopnje zaščite mehanskih ohišij in električnih ohišij pred vdorom, prahom, naključnim dotikom in vodo. ↩
-
Zagotavlja posebne informacije o stopnji zaščite IP69K, ki je najvišja stopnja zaščite, opredeljena v standardih ISO 20653 in DIN 40050-9, ki označuje zaščito pred izpiranjem pod visokim pritiskom in pri visoki temperaturi. ↩