Le linee di produzione si fermano inaspettatamente. Gli ingegneri si affannano a risolvere misteriosi guasti pneumatici. La maggior parte delle persone non comprende la semplice fisica che alimenta l'automazione moderna.
Il principio di funzionamento dei cilindri pneumatici si basa sulla legge di Pascal, secondo la quale la pressione dell'aria compressa agisce in modo uguale in tutte le direzioni all'interno di una camera sigillata, creando una forza lineare quando la differenza di pressione sposta un pistone attraverso il foro del cilindro.
L'anno scorso ho fatto visita a Sarah, supervisore della manutenzione in uno stabilimento automobilistico del Texas. Il suo team sostituiva i cilindri pneumatici ogni poche settimane senza capire perché si guastassero. Ho dedicato due ore a spiegare i principi di base e la percentuale di guasti è diminuita di 80% nel giro di un mese. La comprensione dei principi fondamentali ha cambiato tutto.
Indice dei contenuti
- Che cos'è la legge di Pascal e come si applica ai cilindri pneumatici?
- In che modo la pressione dell'aria crea un movimento lineare?
- Quali sono i componenti essenziali per il funzionamento dei cilindri pneumatici?
- Che differenza c'è tra cilindri a semplice effetto e cilindri a doppio effetto?
- Quale ruolo svolgono le guarnizioni e le valvole nel funzionamento del cilindro?
- Come si calcolano forza, velocità e consumo d'aria?
- Quali sono i vantaggi e i limiti dell'alimentazione pneumatica?
- In che modo i fattori ambientali influiscono sulle prestazioni dei cilindri pneumatici?
- Quali sono i problemi più comuni e come prevenirli?
- Conclusione
- Domande frequenti sui principi dei cilindri pneumatici
Che cos'è la legge di Pascal e come si applica ai cilindri pneumatici?
La legge di Pascal è alla base del funzionamento di tutti i cilindri pneumatici e spiega perché l'aria compressa può generare una forza enorme.
La legge di Pascal afferma che la pressione applicata a un fluido confinato si trasmette ugualmente in tutte le direzioni, consentendo ai cilindri pneumatici di convertire la pressione dell'aria in forza lineare applicando un differenziale di pressione sulla superficie del pistone.
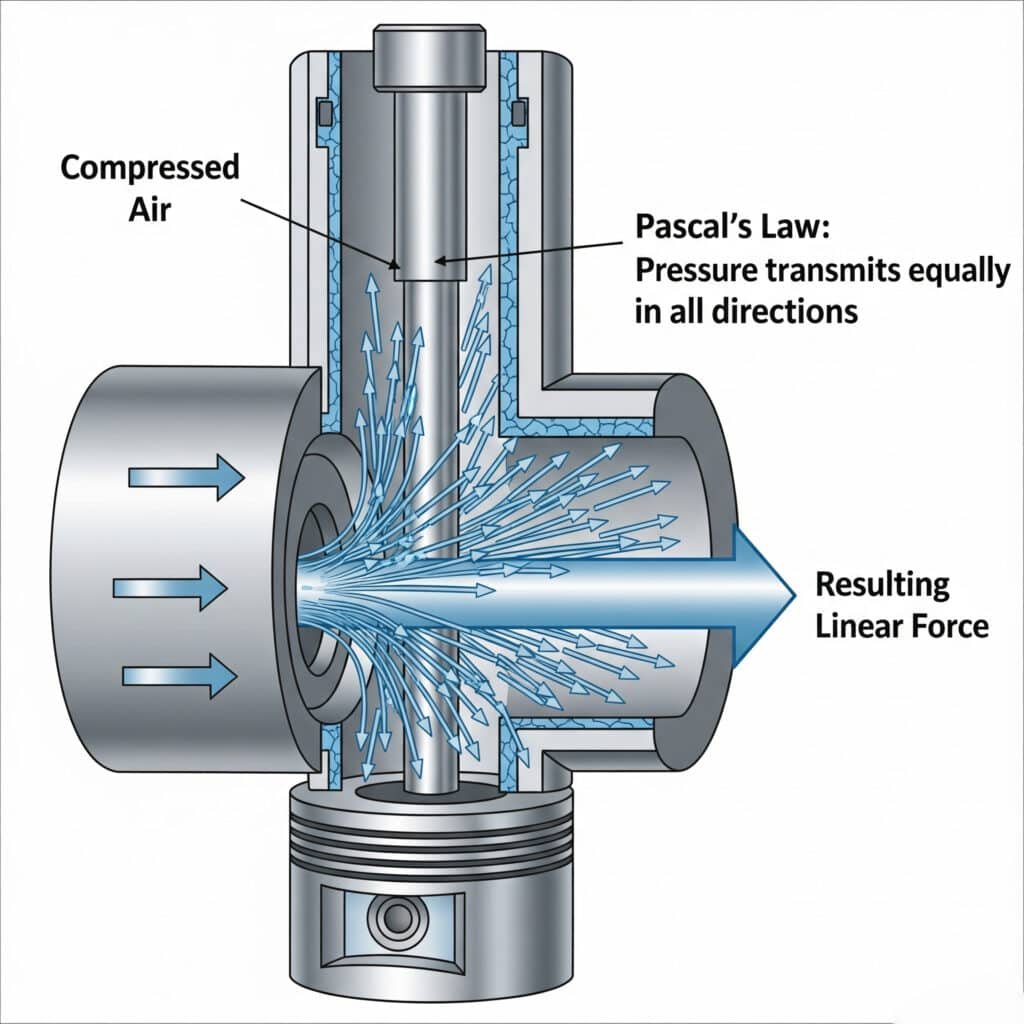
Comprendere la trasmissione della pressione
La Legge di Pascal, scoperta da Blaise Pascal1 nel 1653, spiega come si comportano i fluidi confinati sotto pressione. Quando si applica una pressione in un punto qualsiasi di un fluido confinato, tale pressione si trasmette in modo uguale in tutto il volume del fluido.
Nei cilindri pneumatici, l'aria compressa agisce come fluido di lavoro. Quando la pressione dell'aria entra in un lato del cilindro, spinge contro il pistone con una forza uguale su tutta la superficie del pistone.
La pressione rimane costante in tutto il volume d'aria, ma la forza dipende dalla superficie su cui agisce la pressione. Questa relazione consente ai cilindri pneumatici di generare forze notevoli da pressioni d'aria relativamente basse.
Fondazione matematica
L'equazione di base della forza deriva direttamente dalla legge di Pascal: F = P × A, dove la forza è uguale alla pressione per l'area. Questa semplice relazione regola tutti i calcoli dei cilindri pneumatici.
Le unità di misura della pressione utilizzano in genere bar, PSI o Pascal, a seconda del luogo in cui ci si trova. Un bar equivale a circa 14,5 PSI o 100.000 Pascal.
I calcoli dell'area utilizzano il diametro effettivo del pistone, tenendo conto dell'area dello stelo nei cilindri a doppio effetto. Lo stelo riduce l'area effettiva su un lato del pistone.
Concetto di differenziale di pressione
I cilindri pneumatici funzionano creando differenze di pressione tra i pistoni. La pressione più elevata su un lato crea una forza netta che sposta il pistone verso il lato a pressione più bassa.
La pressione atmosferica (1 bar o 14,7 PSI) esiste sul lato di scarico, a meno che non sia presente una contropressione. Il differenziale di pressione determina la forza effettiva in uscita.
La forza massima teorica si verifica quando un lato ha la pressione massima del sistema e l'altro sfoga nell'atmosfera. I sistemi reali presentano perdite che riducono la forza effettiva.
Applicazioni pratiche
La comprensione della Legge di Pascal aiuta a risolvere i problemi pneumatici. Se si verifica una caduta di pressione, la forza erogata diminuisce proporzionalmente in tutto il sistema.
La progettazione del sistema deve tenere conto delle perdite di pressione attraverso le valvole, i raccordi e le tubazioni. Queste perdite riducono la pressione effettiva disponibile al cilindro.
Più cilindri collegati alla stessa fonte di pressione condividono equamente la pressione disponibile, secondo i principi della Legge di Pascal.
Pressione (bar) | Area del pistone (cm²) | Forza teorica (N) | Forza pratica (N) |
---|---|---|---|
6 | 50 | 3000 | 2700 |
6 | 100 | 6000 | 5400 |
8 | 50 | 4000 | 3600 |
8 | 100 | 8000 | 7200 |
In che modo la pressione dell'aria crea un movimento lineare?
La conversione della pressione dell'aria in movimento lineare coinvolge diversi principi fisici che lavorano insieme per creare un movimento controllato.
La pressione dell'aria crea un movimento lineare applicando una forza alla superficie del pistone, superando l'attrito statico e la resistenza al carico, quindi accelerando il gruppo pistone e stelo attraverso l'alesaggio del cilindro a velocità determinate dalla portata dell'aria.
Processo di generazione della forza
L'aria compressa entra nella camera del cilindro e si espande per riempire il volume disponibile. Le molecole d'aria esercitano una pressione su tutte le superfici, compresa quella del pistone.
La forza di pressione agisce perpendicolarmente alla superficie del pistone, creando una forza netta nella direzione del movimento. Questa forza deve superare l'attrito statico prima che inizi il movimento.
Una volta iniziato il movimento, l'attrito cinetico sostituisce l'attrito statico, riducendo in genere la forza di resistenza. La forza netta accelera quindi il pistone e il carico collegato.
Meccanismi di controllo del movimento
La portata d'aria nel cilindro determina la velocità del pistone. Un flusso più elevato consente un movimento più rapido, mentre un flusso limitato crea un movimento più lento e controllato.
Le valvole di controllo del flusso regolano la portata d'aria per ottenere le velocità desiderate. Il controllo del contatore in entrata influisce sull'accelerazione, mentre il controllo del contatore in uscita influisce sulla decelerazione e sulla gestione del carico.
La contropressione sul lato di scarico garantisce un'ammortizzazione e una decelerazione dolce. Le valvole di ammortizzazione regolabili ottimizzano le caratteristiche di movimento per applicazioni specifiche.
Accelerazione e decelerazione
La seconda legge di Newton2 (F = ma) regola l'accelerazione del pistone. La forza netta divisa per la massa in movimento determina il tasso di accelerazione.
L'accelerazione iniziale è massima quando il differenziale di pressione è massimo e la velocità è nulla. Con l'aumento della velocità, le limitazioni di flusso possono ridurre l'accelerazione.
La decelerazione si verifica quando il flusso di scarico si restringe o la contropressione aumenta. La decelerazione controllata previene i carichi d'urto e migliora la durata del sistema.
Efficienza di trasferimento dell'energia
I sistemi pneumatici raggiungono in genere un'efficienza energetica di 25-35% dall'ingresso del compressore alla produzione di lavoro utile. La maggior parte dell'energia si converte in calore durante la compressione e l'espansione.
L'efficienza del cilindro dipende dalle perdite per attrito, dalle perdite e dalle restrizioni di flusso. I sistemi ben progettati raggiungono un'efficienza del cilindro di 85-95%.
L'ottimizzazione del sistema si concentra sulla minimizzazione delle perdite di carico e sul dimensionamento appropriato dei cilindri per massimizzare l'efficienza entro i vincoli pratici.
Quali sono i componenti essenziali per il funzionamento dei cilindri pneumatici?
La comprensione della funzione di ciascun componente aiuta a selezionare, mantenere e risolvere i problemi dei sistemi di cilindri pneumatici in modo efficace.
I componenti essenziali del cilindro pneumatico comprendono il corpo del cilindro, il gruppo del pistone, lo stelo del pistone, le testate, le guarnizioni, le porte e la ferramenta di montaggio, tutti progettati per funzionare insieme e generare un movimento lineare affidabile.
Costruzione del corpo del cilindro
Il corpo del cilindro contiene la pressione di esercizio e guida il movimento del pistone. La maggior parte dei cilindri utilizza tubi di acciaio senza saldatura o estrusioni di alluminio come materiale del corpo.
La finitura superficiale interna influisce in modo determinante sulla durata e sulle prestazioni della tenuta. Alesaggi levigati3 con finitura superficiale di 0,4-0,8 Ra garantiscono un funzionamento ottimale della tenuta e una lunga durata.
Lo spessore della parete deve resistere alla pressione di esercizio con fattori di sicurezza adeguati. I modelli standard gestiscono una pressione d'esercizio di 10-16 bar con fattori di sicurezza 4:1.
I materiali del corpo includono acciaio al carbonio, acciaio inossidabile e leghe di alluminio. La scelta del materiale dipende dall'ambiente operativo, dai requisiti di pressione e da considerazioni di costo.
Design del gruppo pistone
Il pistone separa le camere del cilindro e trasmette la forza allo stelo. Il design del pistone influisce sulle prestazioni, sull'efficienza e sulla durata.
I materiali dei pistoni sono tipicamente in alluminio o in acciaio. I pistoni in alluminio riducono la massa in movimento per un'accelerazione più rapida, mentre i pistoni in acciaio gestiscono forze più elevate.
Le guarnizioni del pistone creano il confine di pressione tra le camere. Le guarnizioni primarie si occupano del contenimento della pressione, mentre le guarnizioni secondarie prevengono le perdite.
Il diametro del pistone determina la forza erogata secondo la formula F = P × A. I pistoni più grandi generano una forza maggiore, ma richiedono un volume d'aria e una capacità di flusso maggiori.
Specifiche della biella
Lo stelo trasmette la forza del cilindro al carico esterno. Lo stelo deve essere progettato per gestire le forze applicate senza subire flessioni o deformazioni.
I materiali delle aste includono acciaio cromato, acciaio inossidabile e leghe speciali. La cromatura offre resistenza alla corrosione e una finitura superficiale liscia.
Il diametro dello stelo influisce sulla resistenza all'instabilità e sulla rigidità del sistema. Steli più grandi gestiscono carichi laterali più elevati, ma aumentano le dimensioni e il costo del cilindro.
La finitura superficiale dello stelo influisce sulle prestazioni della tenuta e sulla durata. Superfici lisce e dure riducono al minimo l'usura della tenuta e prolungano gli intervalli di manutenzione.
Sistemi di montaggio e tappi terminali
Le testate sigillano le estremità del cilindro e forniscono punti di montaggio per il corpo del cilindro. Devono resistere alla pressione totale del sistema e ai carichi di montaggio.
Costruzione del tirante4 utilizza aste filettate per fissare le testate al corpo del cilindro. Questo design consente la manutenzione sul campo e la sostituzione delle guarnizioni.
La costruzione saldata fissa in modo permanente le testate al corpo del cilindro. Questo crea un design più compatto, ma impedisce la manutenzione sul campo.
Gli stili di montaggio includono opzioni di montaggio a forcella, a cerniera, a flangia e a piede. La scelta di un montaggio corretto evita la concentrazione delle sollecitazioni e i guasti prematuri.
Componente | Opzioni di materiale | Funzione chiave | Modalità di guasto |
---|---|---|---|
Corpo cilindro | Acciaio, alluminio | Contenimento della pressione | Corrosione, usura |
Pistone | Alluminio, acciaio | Trasmissione della forza | Guasto della guarnizione, usura |
Stelo del pistone | Acciaio al cromo, SS | Collegamento del carico | Fibrillazione, corrosione |
Tappi terminali | Acciaio, alluminio | Tenuta a pressione | Crepe, perdite |
Guarnizioni | NBR, PU, PTFE | Isolamento della pressione | Usura, attacco chimico |
Tecnologia di tenuta
Le tenute primarie del pistone mantengono la separazione della pressione tra le camere del cilindro. La scelta delle tenute dipende dai requisiti di pressione, temperatura e compatibilità chimica.
Le guarnizioni per steli impediscono le perdite esterne e l'ingresso di contaminanti. Devono gestire il movimento dinamico mantenendo una tenuta efficace.
Le guarnizioni raschianti rimuovono la contaminazione dalla superficie dell'asta durante la ritrazione. Questo protegge le guarnizioni interne e ne prolunga la durata.
Le guarnizioni statiche prevengono le perdite in corrispondenza delle connessioni filettate e delle interfacce dei coperchi terminali. Gestiscono la pressione senza movimento relativo tra le superfici.
Che differenza c'è tra cilindri a semplice effetto e cilindri a doppio effetto?
La scelta tra cilindri a semplice effetto e cilindri a doppio effetto influisce notevolmente sulle prestazioni, sul controllo e sull'idoneità dell'applicazione.
I cilindri a semplice effetto utilizzano la pressione dell'aria per il movimento in una direzione con ritorno a molla o a gravità, mentre i cilindri a doppio effetto utilizzano la pressione dell'aria per il movimento in entrambe le direzioni, garantendo un controllo migliore e forze più elevate.
Funzionamento del cilindro a semplice effetto
I cilindri a semplice effetto applicano la pressione dell'aria a un solo lato del pistone. La corsa di ritorno si affida a una molla interna, a una molla esterna o alla gravità per far rientrare il pistone.
I cilindri con ritorno a molla utilizzano molle di compressione interne per far rientrare il pistone quando la pressione dell'aria viene meno. La forza della molla deve superare l'attrito ed eventuali carichi esterni.
I cilindri con ritorno a gravità si affidano al peso o a forze esterne per far rientrare il pistone. Questo design è adatto alle applicazioni verticali in cui la gravità assiste il movimento di ritorno.
Il consumo d'aria è inferiore, poiché l'aria pressurizzata viene utilizzata solo per una direzione di movimento. Ciò riduce i requisiti del compressore e i costi operativi.
Funzionamento del cilindro a doppio effetto
I cilindri a doppio effetto applicano la pressione dell'aria su entrambi i lati del pistone in modo alternato. In questo modo si ottiene un movimento motorizzato sia in estensione che in ritrazione.
La forza erogata può variare tra le corse di estensione e di ritrazione a causa dell'area dello stelo che riduce l'area effettiva del pistone su un lato. La forza in estensione è in genere più elevata.
Il controllo della velocità è indipendente per entrambe le direzioni grazie a valvole di controllo del flusso separate. Ciò consente di ottimizzare i tempi di ciclo per le diverse condizioni di carico.
La capacità di mantenere la posizione è eccellente, poiché la pressione dell'aria mantiene la posizione contro le forze esterne in entrambe le direzioni.
Confronto delle prestazioni
La forza erogata nei cilindri a semplice effetto è limitata dalla forza della molla durante l'estensione. La forza della molla riduce la forza netta in uscita disponibile per il lavoro.
I cilindri a doppio effetto forniscono una forza pneumatica completa in entrambe le direzioni, senza perdite per attrito. Questo massimizza la forza disponibile per i carichi esterni.
Il controllo della velocità è più limitato nei modelli a semplice effetto, poiché la velocità di ritorno dipende dalle caratteristiche della molla o dalla gravità piuttosto che dal flusso d'aria controllato.
L'efficienza energetica può favorire i progetti a semplice effetto per le applicazioni più semplici, grazie al minor consumo d'aria e ai sistemi di controllo più semplici.
Criteri di selezione della domanda
I cilindri a semplice effetto sono adatti ad applicazioni semplici che richiedono il movimento in una direzione con carichi di ritorno leggeri. Ad esempio, operazioni di bloccaggio, pressatura e sollevamento.
I cilindri a doppio effetto funzionano meglio per le applicazioni che richiedono un movimento controllato in entrambe le direzioni o forze elevate durante la ritrazione. Le applicazioni di movimentazione e posizionamento dei materiali traggono vantaggio dai cilindri a doppio effetto.
Le considerazioni sulla sicurezza possono favorire i progetti a singolo effetto, che si portano in posizione di sicurezza quando viene a mancare la pressione dell'aria. Il ritorno a molla garantisce un comportamento prevedibile in caso di guasto.
L'analisi dei costi deve includere il prezzo della bombola, la complessità della valvola e il consumo d'aria durante la vita del sistema per determinare la scelta più economica.
Caratteristica | Ad azione singola | A doppio effetto | Migliore applicazione |
---|---|---|---|
Controllo della forza | Una sola direzione | Entrambe le direzioni | SA: Serraggio, DA: Posizionamento |
Controllo della velocità | Ritorno limitato | Controllo completo | SA: Semplice, DA: Complesso |
Consumo d'aria | Più basso | Più alto | SA: Sensibile ai costi, DA: Prestazioni |
Posizione Mantenimento | Moderato | Eccellente | SA: Carichi di gravità, DA: Precisione |
Comportamento di sicurezza | Rendimento prevedibile | Dipende dalla valvola | SA: A prova di errore, DA: Controllato |
Quale ruolo svolgono le guarnizioni e le valvole nel funzionamento del cilindro?
Le guarnizioni e le valvole sono componenti critici che consentono il corretto funzionamento, l'efficienza e l'affidabilità dei cilindri pneumatici.
Le guarnizioni mantengono la separazione della pressione e prevengono la contaminazione, mentre le valvole controllano la direzione, la velocità e la pressione del flusso d'aria per ottenere il movimento e il posizionamento desiderato del cilindro.
Funzioni e tipi di guarnizioni
Le tenute primarie del pistone creano barriere di pressione tra le camere del cilindro. Devono sigillare efficacemente, consentendo al contempo un movimento fluido del pistone con un attrito minimo.
Le guarnizioni dello stelo impediscono la fuoriuscita dell'aria pressurizzata attorno allo stelo del pistone. Inoltre, impediscono l'ingresso di contaminanti esterni nel cilindro.
Le guarnizioni del tergicristallo rimuovono lo sporco, l'umidità e i detriti dalla superficie dell'asta durante la ritrazione. In questo modo si proteggono le guarnizioni interne e si mantiene la pulizia del sistema.
Le guarnizioni statiche prevengono le perdite in corrispondenza di connessioni filettate, tappi e raccordi. Gestiscono la pressione senza movimento relativo tra le superfici di tenuta.
Selezione del materiale delle guarnizioni
Le guarnizioni in gomma nitrilica (NBR) sono adatte ad applicazioni industriali generiche, con una buona resistenza chimica e un intervallo di temperatura moderato (da -20°C a +80°C).
Le guarnizioni in poliuretano (PU) offrono un'eccellente resistenza all'usura e un basso attrito per applicazioni ad alto numero di cicli. Funzionano bene a temperature comprese tra -35°C e +80°C.
Le guarnizioni in PTFE offrono una resistenza chimica superiore e un basso attrito, ma richiedono un'installazione accurata. Possono sopportare temperature da -200°C a +200°C.
Le guarnizioni in Viton offrono un'eccezionale resistenza chimica e termica per gli ambienti più difficili. Funzionano in modo affidabile da -20°C a +200°C.
Funzioni di controllo della valvola
Le valvole di controllo direzionale determinano la direzione del flusso d'aria per estendere o ritrarre il cilindro. I tipi più comuni includono configurazioni a 3/2 vie e 5/2 vie.
Le valvole di controllo del flusso regolano la portata d'aria per controllare la velocità del cilindro. Il controllo del contatore in entrata influisce sull'accelerazione, mentre il controllo del contatore in uscita influisce sulla decelerazione.
Le valvole di controllo della pressione mantengono una pressione di esercizio costante e forniscono una protezione da sovraccarico. Assicurano un'erogazione stabile della forza e prevengono i danni al sistema.
Le valvole di scarico rapido accelerano il movimento del cilindro consentendo lo scarico rapido dell'aria direttamente nell'atmosfera, aggirando le restrizioni di flusso della valvola principale.
Criteri di selezione delle valvole
La portata deve corrispondere ai requisiti del cilindro per le velocità operative desiderate. Le valvole sottodimensionate creano restrizioni di flusso che limitano le prestazioni.
Il tempo di risposta influisce sulle prestazioni del sistema nelle applicazioni ad alta velocità. Le valvole ad azione rapida consentono rapidi cambi di direzione e un posizionamento preciso.
La pressione nominale deve essere superiore alla pressione massima del sistema con margini di sicurezza adeguati. Il guasto della valvola può causare un pericoloso rilascio di pressione.
La compatibilità ambientale comprende l'intervallo di temperatura, la resistenza alle vibrazioni e la protezione dall'ingresso di contaminanti.
Integrazione del sistema
Le opzioni di montaggio della valvola includono il montaggio su manifold per installazioni compatte o il montaggio individuale per sistemi di controllo distribuiti.
I collegamenti elettrici devono corrispondere ai requisiti del sistema di controllo. Le opzioni comprendono il funzionamento a solenoide, il funzionamento pilotato o la possibilità di comando manuale.
I segnali di feedback dei sensori di posizione consentono di realizzare sistemi di controllo ad anello chiuso. La risposta della valvola deve essere coordinata con i segnali del sensore per garantire un funzionamento stabile.
L'accesso per la manutenzione influisce sulla manutenibilità del sistema. La collocazione delle valvole deve consentire una facile ispezione, regolazione e sostituzione in caso di necessità.
Come si calcolano forza, velocità e consumo d'aria?
Calcoli accurati assicurano il corretto dimensionamento dei cilindri pneumatici e prevedono le prestazioni del sistema per i requisiti dell'applicazione specifica.
Calcolare la forza del cilindro pneumatico utilizzando F = P × A, determinare la velocità da V = Q/A e stimare il consumo d'aria utilizzando le relazioni di volume e pressione per ottimizzare il progetto e le prestazioni del sistema.
Metodi di calcolo della forza
La forza teorica è uguale alla pressione dell'aria per l'area effettiva del pistone: F = P × A. Questa rappresenta la forza massima disponibile in condizioni ideali.
L'area effettiva del pistone differisce tra le corse di estensione e di ritrazione nei cilindri a doppio effetto a causa dell'area dello stelo: A_ritratto = A_pistone - A_stelo.
La forza pratica tiene conto delle perdite per attrito, in genere 10-15% della forza teorica. L'attrito della guarnizione, l'attrito della guida e le perdite di flusso d'aria riducono la forza disponibile.
L'analisi del carico deve includere il peso statico, le forze di processo, le forze di accelerazione e i fattori di sicurezza. La forza totale richiesta determina la dimensione minima del cilindro.
Principi di calcolo della velocità
La velocità del cilindro è direttamente correlata alla portata d'aria: V = Q/A, dove la velocità è uguale alla portata volumetrica divisa per l'area effettiva del pistone.
La portata dipende dalla capacità della valvola, dal differenziale di pressione e dalle dimensioni del tubo. Le restrizioni di flusso in qualsiasi punto del sistema limitano la velocità massima.
La velocità della fase di accelerazione aumenta gradualmente con l'aumentare del flusso d'aria. La velocità di regime si verifica quando la portata si stabilizza alla massima capacità.
La decelerazione dipende dalla capacità del flusso di scarico e dalla contropressione. I sistemi di ammortizzazione controllano la decelerazione per evitare carichi d'urto.
Analisi dei consumi d'aria
Il consumo di aria per ciclo è uguale al volume del cilindro per il rapporto di pressione: V_aria = V_cilindro × (P_assoluta/P_atmosferica).
I cilindri a doppio effetto consumano aria sia per la corsa di estensione che per quella di ritrazione. I cilindri a semplice effetto consumano aria solo per la corsa di alimentazione.
Le perdite del sistema dovute a valvole, raccordi e perdite aggiungono in genere 20-30% al consumo teorico. Una corretta progettazione del sistema riduce al minimo queste perdite.
Il dimensionamento dei compressori deve gestire i picchi di domanda e le perdite del sistema con un'adeguata capacità di riserva. I compressori sottodimensionati causano cadute di pressione e scarse prestazioni.
Ottimizzazione delle prestazioni
La scelta delle dimensioni del foro bilancia i requisiti di forza con la velocità e il consumo d'aria. I fori più grandi forniscono una forza maggiore, ma utilizzano più aria e si muovono più lentamente.
La lunghezza della corsa influisce sul consumo d'aria e sul tempo di risposta del sistema. Le corse più lunghe richiedono un volume d'aria maggiore e tempi di riempimento più lunghi.
L'ottimizzazione della pressione di esercizio tiene conto delle esigenze di forza, dei costi energetici e della durata dei componenti. Pressioni più elevate riducono le dimensioni del cilindro, ma aumentano il consumo energetico e la sollecitazione dei componenti.
L'efficienza del sistema migliora con un corretto dimensionamento dei componenti, perdite di carico minime e un efficace trattamento dell'aria. I sistemi ben progettati raggiungono un'efficienza di 85-95%.
Foro del cilindro | Pressione di esercizio | Estendere la forza | Forza di ritrazione | Aria per ciclo |
---|---|---|---|---|
50 mm | 6 bar | 1180N | 950N | 2,4 litri |
63 mm | 6 bar | 1870N | 1500N | 3,7 litri |
80 mm | 6 bar | 3020N | 2420N | 6,0 litri |
100 mm | 6 bar | 4710N | 3770N | 9,4 litri |
Esempi pratici di calcolo
Esempio 1: cilindro con alesaggio di 63 mm e pressione di 6 bar
- Forza di estensione: F = 6 × π × (63/2)² = 1870N
- Consumo d'aria: V = π × (63/2)² × corsa × 6 = corsa × 18,7 litri/metro
Esempio 2: Dimensione del cilindro richiesta per una forza di 2000N a 6 bar
- Area richiesta: A = F/P = 2000/6 = 333 cm²
- Diametro richiesto: D = √(4A/π) = √(4×333/π) = 65mm
Questi calcoli costituiscono il punto di partenza per la scelta del cilindro, mentre il dimensionamento finale tiene conto dei fattori di sicurezza e dei requisiti specifici dell'applicazione.
Quali sono i vantaggi e i limiti dell'alimentazione pneumatica?
La comprensione dei vantaggi e dei vincoli del sistema pneumatico aiuta a determinare quando i cilindri pneumatici sono la scelta migliore per la vostra applicazione.
L'alimentazione pneumatica offre un funzionamento pulito, un controllo semplice, un'elevata velocità e vantaggi in termini di sicurezza, ma presenta limiti in termini di forza erogata, efficienza energetica e precisione di posizionamento rispetto alle alternative idrauliche ed elettriche.
Vantaggi principali dei sistemi pneumatici
Il funzionamento pulito rende i sistemi pneumatici ideali per le applicazioni alimentari, farmaceutiche e per le camere bianche. Le perdite di aria compressa sono innocue per i prodotti e l'ambiente.
I sistemi di controllo semplici utilizzano valvole e interruttori di base per il funzionamento. Ciò riduce la complessità, i requisiti di formazione e la manutenzione rispetto ad alternative più sofisticate.
Il funzionamento ad alta velocità consente tempi di ciclo rapidi grazie alla bassa massa in movimento e alle proprietà comprimibili dell'aria. I cilindri pneumatici possono raggiungere velocità fino a 10 m/s.
I vantaggi per la sicurezza includono un mezzo di lavoro non infiammabile e modalità di guasto prevedibili. Le perdite d'aria non creano rischi di incendio o di contaminazione ambientale.
L'economicità per le applicazioni semplici comprende il basso costo iniziale, la semplicità di installazione e la disponibilità di aria compressa nella maggior parte degli impianti industriali.
Limitazioni del sistema
La forza erogata è limitata dai livelli pratici di pressione dell'aria, in genere 6-10 bar nei sistemi industriali. Questo limita i cilindri pneumatici ad applicazioni di forza moderata.
L'efficienza energetica è scarsa, in genere 25-35% dall'ingresso del compressore al lavoro utile in uscita. La maggior parte dell'energia si converte in calore durante i cicli di compressione ed espansione.
Il posizionamento preciso è difficile a causa della comprimibilità dell'aria e degli effetti della temperatura. I sistemi pneumatici hanno difficoltà nelle applicazioni che richiedono una precisione di posizionamento superiore a ±1 mm.
La sensibilità alla temperatura influisce sulle prestazioni, poiché la densità e la pressione dell'aria variano con la temperatura. Le prestazioni del sistema variano in base alle condizioni ambientali.
I livelli di rumore possono essere significativi a causa dello scarico dell'aria e del funzionamento del compressore. In ambienti sensibili al rumore può essere necessario un sistema di smorzamento del suono.
Confronto con tecnologie alternative
I sistemi idraulici forniscono forze più elevate e una migliore precisione di posizionamento, ma richiedono una gestione complessa dei fluidi e creano problemi ambientali con le perdite di olio.
Gli attuatori elettrici offrono un posizionamento preciso e un'elevata efficienza, ma hanno costi iniziali più elevati e una velocità limitata nelle applicazioni ad alta forza.
I sistemi pneumatici eccellono nelle applicazioni che richiedono forze moderate, velocità elevate, funzionamento pulito e controllo semplice con costi iniziali ragionevoli.
Matrice di idoneità all'applicazione
Le applicazioni ideali comprendono l'imballaggio, l'assemblaggio, la movimentazione dei materiali e l'automazione semplice, dove la velocità e la pulizia sono più importanti della precisione o delle forze elevate.
Tra le applicazioni più scarse figurano il sollevamento di carichi pesanti, il posizionamento di precisione, il servizio continuo e le applicazioni in cui l'efficienza energetica è fondamentale per i costi di esercizio.
I sistemi ibridi talvolta combinano la velocità pneumatica con la precisione elettrica o la forza idraulica per ottimizzare le prestazioni complessive del sistema.
Fattore | Pneumatico | Idraulico | Elettrico | Scelta migliore |
---|---|---|---|---|
Forza di uscita | Moderato | Molto alto | Alto | Idraulico: Carichi pesanti |
Velocità | Molto alto | Moderato | Variabile | Pneumatico: Cicli veloci |
Precisione | Povero | Buono | Eccellente | Elettrico: Posizionamento |
Pulizia | Eccellente | Povero | Buono | Pneumatico: Camere bianche |
Efficienza energetica | Povero | Moderato | Eccellente | Elettrico: Servizio continuo |
Costo iniziale | Basso | Alto | Moderato | Pneumatico: Sistemi semplici |
Considerazioni economiche
I costi operativi comprendono la generazione di aria compressa, la manutenzione e il consumo di energia. Il costo dell'aria varia in genere tra $0,02-0,05 per metro cubo.
I costi di manutenzione sono generalmente bassi grazie alla semplicità della costruzione e alla disponibilità di parti di ricambio. La sostituzione delle guarnizioni è il principale requisito di manutenzione.
I costi del ciclo di vita del sistema devono considerare l'investimento iniziale, le spese di esercizio e i benefici in termini di produttività nel corso della vita utile prevista.
L'analisi del ritorno sull'investimento aiuta a giustificare la scelta del sistema pneumatico in base alla maggiore produttività, alla riduzione della manodopera e alla migliore qualità del prodotto.
In che modo i fattori ambientali influiscono sulle prestazioni dei cilindri pneumatici?
Le condizioni ambientali influenzano in modo significativo il funzionamento, l'affidabilità e la durata dei cilindri pneumatici nelle applicazioni reali.
I fattori ambientali, tra cui la temperatura, l'umidità, la contaminazione, le vibrazioni e le sostanze corrosive, influiscono sulle prestazioni dei cilindri pneumatici attraverso la degradazione delle guarnizioni, la corrosione, le variazioni di attrito e l'usura dei componenti.
Effetti della temperatura
La temperatura di esercizio influisce sulla densità dell'aria, sulla pressione e sui materiali dei componenti. Temperature più elevate riducono la densità dell'aria e la forza effettiva erogata.
I materiali delle guarnizioni hanno limiti di temperatura che influiscono sulle prestazioni e sulla durata. Le guarnizioni NBR standard funzionano da -20°C a +80°C, mentre i materiali specializzati estendono questo intervallo.
L'espansione termica dei componenti del cilindro può influire sui giochi e sulle prestazioni della tenuta. La progettazione deve tenere conto dell'espansione termica per evitare che si verifichino legami o perdite.
La condensa si verifica quando l'aria compressa si raffredda al di sotto del suo punto di rugiada. L'acqua nel sistema causa corrosione, congelamento e funzionamento irregolare.
Controllo dell'umidità e dell'umidità
L'umidità elevata aumenta il rischio di condensa nei sistemi di aria compressa. L'accumulo di acqua provoca la corrosione dei componenti e un funzionamento irregolare.
I sistemi di trattamento dell'aria, tra cui filtri, essiccatori e separatori, rimuovono l'umidità e i contaminanti. Un corretto trattamento dell'aria è essenziale per un funzionamento affidabile.
I sistemi di drenaggio devono rimuovere la condensa accumulata dai punti bassi del sistema di distribuzione dell'aria. Gli scarichi automatici impediscono l'accumulo di acqua.
Punto di rugiada5 mantiene il contenuto di umidità dell'aria al di sotto dei livelli che causano la condensazione alle temperature di esercizio. I punti di rugiada target sono in genere 10°C al di sotto della temperatura minima di esercizio.
Impatto della contaminazione
Polvere e detriti causano usura delle guarnizioni, malfunzionamento delle valvole e danni ai componenti interni. I sistemi di filtrazione proteggono i componenti pneumatici dalla contaminazione.
La contaminazione chimica può attaccare le guarnizioni, causare corrosione e creare depositi che interferiscono con il funzionamento. La compatibilità dei materiali è fondamentale negli ambienti chimici.
La contaminazione da particolato accelera l'usura e può causare l'intasamento delle valvole o la rottura delle guarnizioni. La manutenzione dei filtri è essenziale per l'affidabilità del sistema.
La contaminazione dell'olio nei compressori può causare il rigonfiamento e la degradazione delle guarnizioni. I compressori oil-free o i sistemi di rimozione dell'olio appropriati prevengono la contaminazione.
Vibrazioni e urti
Le vibrazioni meccaniche possono causare l'allentamento dei dispositivi di fissaggio, lo spostamento delle guarnizioni e l'affaticamento dei componenti. Un montaggio corretto e l'isolamento dalle vibrazioni proteggono i componenti del sistema.
I carichi d'urto dovuti a rapidi cambi di direzione o a impatti esterni possono danneggiare i componenti interni. I sistemi di ammortizzazione riducono i carichi d'urto e prolungano la vita dei componenti.
Le frequenze di risonanza possono amplificare gli effetti delle vibrazioni. Il progetto del sistema deve evitare di operare alle frequenze di risonanza dei componenti montati.
La stabilità della fondazione influisce sulle prestazioni e sulla durata del sistema. Il montaggio rigido previene le vibrazioni eccessive e mantiene l'allineamento corretto.
Protezione dell'ambiente corrosivo
Le atmosfere corrosive attaccano i componenti metallici e causano guasti prematuri. La selezione dei materiali e i rivestimenti protettivi prolungano la durata in ambienti difficili.
La costruzione in acciaio inossidabile offre resistenza alla corrosione, ma aumenta il costo del sistema. L'analisi costi-benefici determina quando l'acciaio inossidabile è giustificato.
I rivestimenti protettivi, tra cui l'anodizzazione, la placcatura e la verniciatura, proteggono dalla corrosione i materiali standard. La scelta del rivestimento dipende dalle condizioni ambientali specifiche.
I design sigillati impediscono alle sostanze corrosive di entrare in contatto con i componenti interni. La tenuta ambientale è fondamentale nelle applicazioni più difficili.
Fattore ambientale | Effetto sulle prestazioni | Metodi di protezione | Soluzioni tipiche |
---|---|---|---|
Alta temperatura | Forza ridotta, degrado della tenuta | Scudi termici, raffreddamento | Guarnizioni ad alta temperatura, isolamento |
Bassa temperatura | Condensa, irrigidimento delle guarnizioni | Riscaldamento, isolamento | Guarnizioni per le stagioni fredde, riscaldatori |
Umidità elevata | Corrosione, accumulo di acqua | Essiccazione all'aria, drenaggio | Essiccatoi refrigerati, scarichi automatici |
Contaminazione | Usura, malfunzionamento | Filtrazione, sigillatura | Filtri, tergicristalli, coperture |
Vibrazioni | Allentamento, affaticamento | Isolamento, smorzamento | Supporti per gli urti, ammortizzazione |
Corrosione | Degrado dei componenti | Selezione del materiale | Acciaio inox, rivestimenti |
Quali sono i problemi più comuni e come prevenirli?
La comprensione dei problemi più comuni dei cilindri pneumatici e la loro prevenzione aiutano a mantenere un funzionamento affidabile e a ridurre al minimo i tempi di fermo.
I problemi più comuni dei cilindri pneumatici comprendono perdite di tenuta, movimenti irregolari, riduzione della forza erogata e usura precoce, che possono essere evitati grazie a un adeguato trattamento dell'aria, a una manutenzione regolare, a un corretto dimensionamento e alla tutela dell'ambiente.
Problemi di tenuta
Le perdite interne tra le camere del cilindro riducono la forza erogata e causano un movimento irregolare. Le guarnizioni del pistone usurate o danneggiate sono la causa tipica.
Le perdite esterne intorno all'asta creano rischi per la sicurezza e sprechi d'aria. Un guasto alla guarnizione dell'asta o un danno alla superficie consente la fuoriuscita di aria pressurizzata.
Le cause di guasto delle guarnizioni includono la contaminazione, l'installazione impropria, l'incompatibilità chimica e la normale usura. La prevenzione si concentra sulla risoluzione delle cause principali.
Le procedure di sostituzione richiedono una scelta corretta della guarnizione, la preparazione della superficie e le tecniche di installazione. Un'installazione errata provoca un guasto immediato.
Problemi di movimento irregolare
Il movimento di stick-slip deriva da variazioni di attrito, contaminazione o lubrificazione inadeguata. Un funzionamento regolare richiede livelli di attrito costanti.
Le variazioni di velocità indicano restrizioni di flusso, fluttuazioni di pressione o perdite interne. La diagnosi del sistema identifica la causa specifica.
La deriva della posizione si verifica quando i cilindri non riescono a mantenere la posizione a fronte di carichi esterni. La deriva della posizione è causata da perdite interne o da problemi alle valvole.
L'instabilità o l'oscillazione derivano dall'instabilità del sistema di controllo o da impostazioni di guadagno eccessive. Una corretta messa a punto elimina il funzionamento instabile.
Riduzione della forza in uscita
Le perdite di pressione attraverso le valvole, i raccordi e le tubazioni riducono la forza disponibile sul cilindro. Un corretto dimensionamento evita perdite di pressione eccessive.
Le perdite interne riducono il differenziale di pressione effettivo sul pistone. La sostituzione della guarnizione ripristina la forza di uscita corretta.
L'attrito aumenta a causa di contaminazione, usura o lubrificazione inadeguata. Una manutenzione regolare mantiene il funzionamento a basso attrito.
Gli effetti della temperatura riducono la densità dell'aria e la forza disponibile. La progettazione del sistema deve tenere conto delle variazioni di temperatura.
Usura prematura dei componenti
La contaminazione accelera l'usura di guarnizioni, guide e superfici interne. Un filtraggio e un trattamento dell'aria adeguati prevengono i danni da contaminazione.
Il sovraccarico supera i limiti di progetto e causa una rapida usura o un guasto. Un corretto dimensionamento con adeguati fattori di sicurezza previene i danni da sovraccarico.
Un disallineamento crea un carico non uniforme e un'usura accelerata. Un'installazione e un montaggio corretti prevengono i problemi di allineamento.
Una lubrificazione inadeguata aumenta l'attrito e l'usura. Un sistema di lubrificazione adeguato mantiene la durata dei componenti.
Strategie di manutenzione preventiva
L'ispezione regolare identifica i problemi prima che si verifichino i guasti. I controlli visivi, il monitoraggio delle prestazioni e il rilevamento delle perdite consentono una manutenzione proattiva.
La manutenzione del trattamento dell'aria comprende la sostituzione dei filtri, la manutenzione dell'essiccatore e il funzionamento del sistema di scarico. L'aria pulita e asciutta è essenziale per un funzionamento affidabile.
I programmi di lubrificazione mantengono i livelli di lubrificazione corretti senza una lubrificazione eccessiva che può causare problemi. Seguire le raccomandazioni del produttore.
Il monitoraggio delle prestazioni tiene traccia della forza erogata, della velocità e del consumo d'aria per identificare il degrado delle prestazioni prima del guasto.
Tipo di problema | Sintomi | Cause principali | Metodi di prevenzione |
---|---|---|---|
Perdite di tenuta | Perdita d'aria, forza ridotta | Usura, contaminazione | Aria pulita, guarnizioni adeguate |
Movimento irregolare | Velocità incoerente | Attrito, restrizioni | Lubrificazione, dimensionamento del flusso |
Perdita di forza | Funzionamento debole | Cali di pressione, perdite | Dimensionamento e manutenzione corretti |
Usura prematura | Breve durata di vita | Sovraccarico, contaminazione | Dimensionamento e filtrazione corretti |
Deriva della posizione | Non riesce a mantenere la posizione | Perdite interne | Manutenzione delle guarnizioni, valvole |
Metodologia di risoluzione dei problemi
La diagnosi sistematica inizia con l'identificazione dei sintomi e procede attraverso procedure di analisi logiche. Documentare i risultati per tracciare i modelli di problema.
Il test delle prestazioni misura la forza effettiva, la velocità e il consumo d'aria rispetto alle specifiche. In questo modo si identifica il degrado specifico delle prestazioni.
Il test dei componenti isola i problemi da elementi specifici del sistema. Sostituire o riparare solo i componenti guasti piuttosto che interi gruppi.
L'analisi delle cause profonde previene il ripetersi dei problemi affrontando le cause sottostanti anziché i semplici sintomi. In questo modo si riducono i costi di manutenzione a lungo termine.
Conclusione
I principi dei cilindri pneumatici si basano sulla legge di Pascal e sul differenziale di pressione per convertire l'aria compressa in un movimento lineare affidabile, rendendoli essenziali per l'automazione moderna, se correttamente compresi e applicati.
Domande frequenti sui principi dei cilindri pneumatici
Qual è il principio di base del funzionamento dei cilindri pneumatici?
Il principio di base utilizza la legge di Pascal, secondo la quale la pressione dell'aria compressa agisce in modo uguale in tutte le direzioni, creando una forza lineare quando il differenziale di pressione muove un pistone attraverso il foro del cilindro, convertendo l'energia pneumatica in movimento meccanico.
Come si calcola la forza di uscita di un cilindro pneumatico?
Calcolare la forza del cilindro pneumatico utilizzando F = P × A, dove la forza è uguale alla pressione dell'aria per l'area effettiva del pistone, tenendo conto della riduzione dell'area dello stelo nella corsa di rientro nei cilindri a doppio effetto.
Qual è la differenza tra cilindri pneumatici a semplice e a doppio effetto?
I cilindri a semplice effetto utilizzano la pressione dell'aria per una direzione con ritorno a molla o a gravità, mentre i cilindri a doppio effetto utilizzano la pressione dell'aria per entrambe le direzioni, garantendo un controllo migliore e forze più elevate in entrambe le direzioni.
Perché i cilindri pneumatici perdono forza nel tempo?
I cilindri pneumatici perdono forza a causa delle perdite delle guarnizioni interne, delle cadute di pressione nel sistema dell'aria, della contaminazione che provoca un aumento dell'attrito e della normale usura dei componenti che riduce l'efficienza del sistema.
In che modo la pressione dell'aria crea il movimento lineare nei cilindri pneumatici?
La pressione dell'aria crea un movimento lineare applicando una forza alla superficie del pistone secondo la Legge di Pascal, superando l'attrito statico e la resistenza al carico, quindi accelerando il gruppo pistone attraverso l'alesaggio del cilindro.
Quali fattori influenzano le prestazioni dei cilindri pneumatici?
I fattori di prestazione includono la pressione e la qualità dell'aria, gli effetti della temperatura sulla densità dell'aria, i livelli di contaminazione, le condizioni delle guarnizioni, il dimensionamento corretto per l'applicazione e le condizioni ambientali come l'umidità e le vibrazioni.
Come funzionano le guarnizioni nei cilindri pneumatici?
Le guarnizioni mantengono la separazione della pressione tra le camere del cilindro, prevengono le perdite esterne intorno allo stelo e bloccano l'ingresso di contaminanti, utilizzando materiali come NBR, poliuretano o PTFE selezionati per le specifiche condizioni operative.
-
Leggete la biografia di Blaise Pascal e scoprite i suoi contributi alla fisica e alla matematica. ↩
-
Rivedere i principi fondamentali della seconda legge di Newton e il modo in cui essa regola forza, massa e accelerazione. ↩
-
Vediamo una spiegazione tecnica del processo di levigatura dei cilindri e di come si crea una finitura superficiale ideale per le prestazioni della tenuta. ↩
-
Esplora i principi di progettazione e i vantaggi della costruzione dei tiranti per i cilindri pneumatici e idraulici industriali. ↩
-
Comprendere la definizione di punto di rugiada e il suo ruolo critico nella prevenzione dell'umidità e della corrosione nei sistemi di aria compressa. ↩