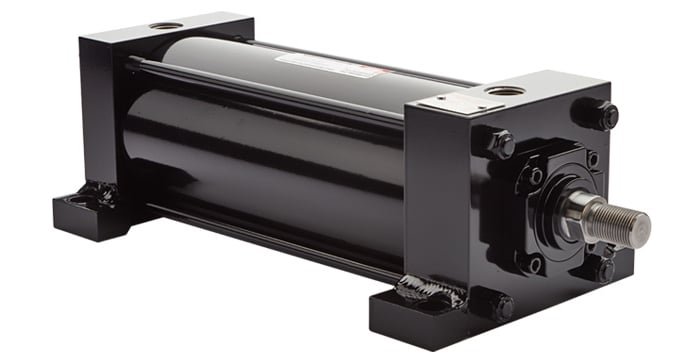
Le condizioni ambientali vengono spesso trascurate durante la selezione degli attuatori, causando guasti prematuri, rischi per la sicurezza e costose sostituzioni del sistema quando la tecnologia scelta non è in grado di resistere alle reali condizioni operative.
I fattori ambientali, tra cui temperature estreme, atmosfere esplosive, livelli di contaminazione, umidità, vibrazioni ed esposizione chimica, determinano in modo critico la scelta dell'attuatore: i cilindri pneumatici eccellono in condizioni difficili, mentre gli attuatori elettrici richiedono ambienti controllati per un funzionamento affidabile.
La scorsa settimana, Patricia di un impianto petrolchimico della Louisiana ha scoperto che i suoi costosi attuatori elettrici si stavano guastando dopo soli sei mesi di permanenza nell'ambiente corrosivo in cui si trovavano, mentre i cilindri pneumatici antideflagranti avrebbero fornito decenni di servizio affidabile con una scelta adeguata dei materiali.
Indice dei contenuti
- In che modo gli estremi di temperatura influiscono sulle prestazioni di cilindri e attuatori?
- Quale tecnologia gestisce meglio le atmosfere esplosive e pericolose?
- In che modo i requisiti di contaminazione e lavaggio influiscono sulla scelta dell'attuatore?
- Che ruolo hanno le vibrazioni, gli urti e l'esposizione ai prodotti chimici nella selezione?
In che modo gli estremi di temperatura influiscono sulle prestazioni di cilindri e attuatori?
Le variazioni di temperatura hanno un impatto significativo sulle prestazioni, l'affidabilità e la durata degli attuatori, con tecnologie diverse che mostrano capacità molto diverse in condizioni termiche estreme.
I cilindri pneumatici funzionano in modo affidabile da -40°F a +200°F (da -40°C a +93°C) con materiali e guarnizioni adeguati, mentre gli attuatori elettrici funzionano tipicamente in intervalli da -10°F a +140°F (da -23°C a +60°C), rendendo i sistemi pneumatici superiori per le applicazioni a temperature estreme in fonderie, magazzini frigoriferi e installazioni all'aperto.

Prestazioni ad alta temperatura
Capacità del cilindro pneumatico alle alte temperature
I sistemi ad aria compressa eccellono nelle applicazioni a caldo estremo:
- Campo di funzionamento: da -40°F a +200°F (da -40°C a +93°C) con materiali standard
- Gamma estesa: Fino a +300°F (+149°C) con guarnizioni e materiali speciali
- Resistenza al calore: La struttura in metallo resiste ai cicli termici
- Espansione termica: I sistemi meccanici si adattano alle variazioni dimensionali
Limiti di temperatura dell'attuatore elettrico
I sistemi elettronici si trovano in difficoltà in ambienti ad alta temperatura:
- Gamma standard: Da +32°F a +140°F (da 0°C a +60°C) per la maggior parte delle unità.
- Sensibilità elettronica: I circuiti di controllo si guastano a temperature elevate
- Limitazioni del motore: Degrado del magnete permanente e dell'avvolgimento
- Requisiti di raffreddamento: Per le temperature più elevate è necessario un raffreddamento ad aria forzata o a liquido.
Sfide a bassa temperatura
Prestazioni pneumatiche in condizioni di freddo
I cilindri funzionano in modo affidabile in condizioni di congelamento:
Intervallo di temperatura | Capacità pneumatica | Modifiche richieste | Esempi di applicazione |
---|---|---|---|
+Da 32°F a 0°F | Funzionamento standard | Rimozione dell'umidità | Attrezzature per esterni |
Da 0°F a -20°F | Buone prestazioni | Additivi antigelo | Conservazione a freddo |
Da -20°F a -40°F | Funzionamento affidabile | Guarnizioni speciali/lubrificanti | Applicazioni artiche |
Sotto i -40°F | Possibile con le modifiche | Custodie riscaldate | Climi freddi estremi |
Attuatore elettrico Problemi di freddo
I sistemi elettronici devono affrontare diverse sfide legate al freddo:
- Degrado della batteria: Capacità e prestazioni ridotte con il freddo
- Addensamento del lubrificante: Aumento dell'attrito e dell'usura
- Stress dei componenti elettronici: I cicli termici danneggiano i circuiti
- Problemi di condensazione: Formazione di umidità durante i cicli di temperatura
Impatto del ciclo termico
Stabilità termica del sistema pneumatico
I cilindri gestiscono efficacemente le variazioni di temperatura:
- Compatibilità dei materiali: La struttura in metallo resiste alle sollecitazioni termiche
- Flessibilità della guarnizione: Le moderne guarnizioni si adattano all'espansione termica
- Compensazione della pressione: La pressione del sistema si regola con la temperatura
- Elettronica minimale: Meno componenti sensibili alla temperatura
Stress termico del sistema elettrico
I componenti elettronici sono soggetti a cicli di temperatura:
- Fatica del giunto a saldare: L'espansione/contrazione ripetuta causa guasti
- Deriva dei componenti: I valori elettronici cambiano con la temperatura
- Guasto dell'isolamento: Lo stress termico degrada l'isolamento elettrico
- Stress meccanico: Tassi di espansione diversi causano danni ai componenti
Applicazioni di temperatura specifiche per il settore
Applicazioni per fonderie e acciaierie
Gli ambienti a calore estremo favoriscono le soluzioni pneumatiche:
- Temperature di esercizio: Da +150°F a +200°F (da +66°C a +93°C) comune
- Calore radiante: Elevate temperature ambientali da forni e metallo fuso
- Shock termico: Rapide variazioni di temperatura durante le operazioni
- Vantaggio Bepto: Disponibili guarnizioni e materiali per alte temperature
Stoccaggio e refrigerazione
Le applicazioni sotto zero traggono vantaggio dall'affidabilità del pneumatico:
- Operazioni di congelamento: ambienti da -10°F a -40°F (da -23°C a -40°C)
- Inverno all'aperto: Apparecchiature esposte a temperature stagionali estreme
- Ciclo termico: Variazioni di temperatura giornaliere nella lavorazione
- Gestione dell'umidità: Prevenzione della formazione di ghiaccio nei sistemi pneumatici
Selezione del materiale per temperature estreme
Materiali pneumatici per alte temperature
Componenti specializzati per il calore estremo:
- Guarnizioni in Viton1: Campo di funzionamento fino a +400°F (+204°C)
- Guarnizioni in PTFE: Resistenza agli agenti chimici e alle alte temperature
- Acciaio inox: Resistenza alla corrosione e stabilità termica
- Lubrificanti per alte temperature: Oli sintetici per condizioni estreme
Modifiche pneumatiche per il freddo
Adattamenti per il funzionamento a bassa temperatura:
- Guarnizioni per basse temperature: Materiali flessibili per il funzionamento sotto zero
- Additivi antigelo: Prevenzione del congelamento dell'umidità nelle linee dell'aria
- Sistemi di isolamento: Protezione dei componenti critici dal freddo estremo
- Custodie riscaldate: Mantenimento della temperatura di esercizio per l'elettronica
Controllo e monitoraggio della temperatura
Gestione pneumatica della temperatura
Approcci semplici al controllo della temperatura:
- Isolamento: Protezione delle bombole da temperature ambientali estreme
- Elementi di riscaldamento: Riscaldatori elettrici per applicazioni a basse temperature
- Ventilazione: Circolazione dell'aria per ambienti ad alta temperatura
- Barriere termiche: Schermatura da fonti di calore radiante
Protezione della temperatura del sistema elettrico
Gestione termica complessa dei sistemi elettronici:
- Sistemi di raffreddamento: Raffreddamento ad aria forzata o a liquido per le alte temperature
- Sistemi di riscaldamento: Mantenimento delle temperature minime di esercizio
- Monitoraggio termico: Sensori di temperatura e sistemi di controllo
- Contenitori ambientali: Proteggere l'elettronica dalle temperature estreme
Roberto, che gestisce le attrezzature di un'azienda mineraria canadese, aveva bisogno di attuatori per i nastri trasportatori esterni che operano con inverni a -30°F ed estati a +100°F. Gli attuatori elettrici richiedevano costosi involucri riscaldati e sistemi di raffreddamento, mentre i cilindri pneumatici Bepto con guarnizioni per i climi freddi funzionavano in modo affidabile tutto l'anno a un costo totale 60% inferiore e con requisiti minimi di manutenzione.
Quale tecnologia gestisce meglio le atmosfere esplosive e pericolose?
I requisiti di sicurezza in ambienti esplosivi e pericolosi spesso impongono la scelta della tecnologia degli attuatori, con differenze significative nelle capacità di certificazione e nelle caratteristiche di sicurezza intrinseche.
I cilindri pneumatici offrono un funzionamento intrinsecamente a prova di esplosione senza fonti di accensione elettrica, rendendoli ideali per le atmosfere pericolose, mentre gli attuatori elettrici richiedono costose custodie e certificazioni antideflagranti, rendendo spesso le soluzioni pneumatiche l'unica scelta pratica per le applicazioni critiche per la sicurezza.

Classificazioni delle aree pericolose
Comprendere le categorie di rischio di esplosione
Gli ambienti industriali sono classificati in base al potenziale di esplosione:
- Classe I: Gas e vapori infiammabili (raffinerie, impianti chimici)
- Classe II: Polveri combustibili (ascensori per cereali, lavorazione del carbone)
- Classe III: Fibre infiammabili (fabbriche tessili, lavorazione della carta)
- Classificazioni delle zone: Sistema europeo (Zona 0, 1, 2 per i gas; Zona 20, 21, 22 per le polveri).
Requisiti della fonte di accensione
I diversi livelli di pericolo richiedono una specifica prevenzione dell'accensione:
- Divisione 1/Zona 1: Materiali pericolosi presenti durante il normale funzionamento
- Divisione 2/Zona 2: Materiali pericolosi presenti solo in condizioni anomale.
- Valori di temperatura: Temperature superficiali massime (classificazioni T1-T6)
- Limiti energetici: Circuiti a sicurezza intrinseca con energia limitata
Vantaggi del sistema pneumatico antideflagrante
Caratteristiche di sicurezza intrinseche
I cilindri offrono una protezione naturale contro le esplosioni:
- Nessuna accensione elettrica: Il funzionamento ad aria compressa elimina le fonti di scintilla
- Nessuna generazione di calore: Il funzionamento meccanico produce un calore minimo
- Costruzione semplice: Un minor numero di componenti riduce le potenziali modalità di guasto
- Funzionamento meccanico: La funzione continua anche in caso di interruzione dell'alimentazione elettrica
Certificazioni pneumatiche per aree pericolose
Certificazioni standard per sistemi pneumatici:
Certificazione | Applicazione | Vantaggio pneumatico | Costo tipico |
---|---|---|---|
ATEX (Europa)2 | Atmosfere esplosive | Intrinsecamente sicuro | Prezzi standard |
NEC 500 (USA) | Luoghi pericolosi | Nessun involucro speciale | Prezzi standard |
IECEx (Internazionale) | Atmosfere esplosive globali | Conformità semplice | Prezzi standard |
FM/UL (USA) | Elenco di fabbrica Mutual/UL | Approvazione semplice | Prezzi standard |
Attuatore elettrico Sfide per le aree pericolose
Requisiti antideflagranti
I sistemi elettrici richiedono ampie misure di sicurezza:
- Custodie antideflagranti: Alloggiamenti pesanti e costosi che contengono esplosioni
- Circuiti a sicurezza intrinseca: Circuiti ad energia limitata che impediscono l'accensione
- Contenitori spurgati: Sistemi a pressione positiva che escludono i gas pericolosi
- Maggiore sicurezza: Costruzione migliorata per prevenire le fonti di accensione
Impatto sui costi dei sistemi elettrici per aree pericolose
I requisiti di sicurezza aumentano drasticamente i costi degli attuatori elettrici:
- Costi dell'involucro: $1000-$5000 supplementare per custodie antideflagranti
- Spese di certificazione: $5000-$25000 per il collaudo e l'omologazione
- Complessità dell'installazione: Requisiti per guaine e cablaggi speciali
- Requisiti di manutenzione: Ispezione e ricertificazione periodica
Applicazioni pericolose specifiche del settore
Industria del petrolio e del gas
Le operazioni petrolifere richiedono attrezzature a prova di esplosione:
- Raffinerie: Ambienti di Classe I, Divisione 1 con vapori di idrocarburi.
- Piattaforme offshore: Ambienti marini con potenziale di gas esplosivo
- Operazioni di pipeline: Luoghi remoti con metano e idrogeno solforato
- Allevamenti di serbatoi: Spazi a vapore che richiedono apparecchiature a sicurezza intrinseca
Trattamento chimico
Gli impianti chimici presentano molteplici rischi di esplosione:
- Sistemi di reattori: Solventi infiammabili e prodotti di reazione
- Colonne di distillazione: Composti organici volatili e vapori
- Aree di stoccaggio: Vapori e polveri chimiche concentrate
- Operazioni di trasferimento: Elettricità statica e generazione di vapore
Soluzioni per aree pericolose Bepto
Cilindri standard a prova di esplosione
Le nostre bombole soddisfano i requisiti per le aree pericolose:
- Certificazione ATEX: Conformità alla direttiva europea 2014/34/UE
- Conformità alla norma NEC 500: Requisiti del National Electrical Code statunitense
- Selezione del materiale: Metalli e guarnizioni appropriati per la compatibilità chimica
- Documentazione: Pacchetti di certificazione completi e guide all'installazione
Caratteristiche dell'area pericolosa specializzata
Caratteristiche di sicurezza avanzate per applicazioni critiche:
- Disposizioni in materia di vincoli: Collegamenti elettrici di messa a terra per la dissipazione statica
- Materiali speciali: Acciaio inossidabile e leghe esotiche per ambienti corrosivi
- Compatibilità delle guarnizioni: Guarnizioni resistenti agli agenti chimici per atmosfere aggressive
- Valori di temperatura: Funzionamento ad alta e bassa temperatura in aree pericolose
Integrazione del sistema di sicurezza
Sistemi di arresto di emergenza
Vantaggi della pneumatica nelle applicazioni critiche per la sicurezza:
- Funzionamento a prova di guasto: Ritorno a molla e protezione dalla perdita di pressione dell'aria
- Risposta rapida: Intervento immediato sui segnali di emergenza
- Comando manuale: Capacità di funzionamento del backup meccanico
- Indicazione visibile: Indicazione chiara della posizione per la verifica della sicurezza
Integrazione del rilevamento di incendi e gas
I sistemi pneumatici si integrano facilmente con i sistemi di sicurezza:
- Interfacce semplici: Segnali elettrici di base per il controllo delle valvole pneumatiche
- Funzionamento affidabile: Funzionamento dei sistemi meccanici durante le emergenze
- Bassa manutenzione: I componenti elettronici minimi riducono il potenziale di guasto
- Tecnologia comprovata: Decenni di applicazioni di successo dei sistemi di sicurezza
Considerazioni sulla conformità normativa
Standard internazionali
Requisiti globali per le apparecchiature per aree pericolose:
- IEC 60079: Norma internazionale per le atmosfere esplosive
- NFPA 497: Standard USA per la classificazione delle aree pericolose
- Standard API: Requisiti dell'American Petroleum Institute
- Regolamenti OSHA: Requisiti di sicurezza sul lavoro negli Stati Uniti
Documentazione e formazione
Requisiti di conformità per le apparecchiature per aree pericolose:
- Procedure di installazione: Installazione corretta in aree pericolose
- Protocolli di manutenzione: Procedure di servizio sicure per atmosfere esplosive
- Requisiti per la formazione: Certificazione del personale per lavori in aree pericolose
- Programmi di ispezione: Verifica periodica della sicurezza e documentazione
Analisi costi-benefici per le aree pericolose
Confronto dei costi totali
Analisi dei costi quinquennali per applicazioni in aree pericolose:
Fattore di costo | Cilindro pneumatico | Attuatore elettrico | Risparmio |
---|---|---|---|
Costo dell'attrezzatura | $500-$1500 | $3000-$8000 | 70-80% |
Certificazione | Incluso | $5000-$15000 | 100% |
Installazione | $200-$500 | $1500-$4000 | 75-85% |
Manutenzione | $100-$300/year | $500-$1500/year | 70-80% |
Totale 5 anni | $1200-$3000 | $12000-$35000 | 85-90% |
Jennifer, ingegnere della sicurezza in una raffineria del Texas, aveva bisogno di attuatori per una nuova unità di lavorazione degli idrocarburi classificata come Classe I, Divisione 1. Gli attuatori elettrici richiedevano $12.000 in custodie e certificazioni antideflagranti per unità. Gli attuatori elettrici richiedevano $12.000 in custodie antideflagranti e certificazioni per unità, mentre i cilindri pneumatici Bepto fornivano un funzionamento intrinsecamente antideflagrante a prezzi standard, con un risparmio di $180.000 sul progetto di 15 attuatori e il superamento di tutti i requisiti di sicurezza.
In che modo i requisiti di contaminazione e lavaggio influiscono sulla scelta dell'attuatore?
I livelli di contaminazione e i requisiti di pulizia influenzano in modo significativo la scelta dell'attuatore, con tecnologie diverse che mostrano capacità molto diverse in ambienti sporchi, umidi o sterili.
I cilindri pneumatici eccellono negli ambienti contaminati grazie a design sigillati, capacità di lavaggio e materiali per uso alimentare, mentre gli attuatori elettrici devono far fronte all'ingresso di contaminazione, alla sensibilità all'umidità e ai complessi requisiti di pulizia, rendendo i sistemi pneumatici superiori per le applicazioni alimentari, farmaceutiche e industriali difficili.

Capacità di resistenza alla contaminazione
Protezione dalla contaminazione dei cilindri pneumatici
I sistemi pneumatici sigillati resistono alla contaminazione ambientale:
- Classificazione IP65/IP673: Protezione completa contro l'ingresso di polvere e acqua
- Costruzione sigillata: Le guarnizioni O-ring e le guarnizioni di tenuta impediscono l'ingresso di agenti contaminanti.
- Pressione positiva: La pressione interna dell'aria esclude i contaminanti esterni
- Superfici semplici: Gli esterni lisci facilitano la pulizia e la decontaminazione
Vulnerabilità della contaminazione degli attuatori elettrici
I sistemi elettronici devono affrontare sfide di contaminazione:
- Requisiti di ventilazione: La circolazione dell'aria di raffreddamento consente l'ingresso della contaminazione
- Sensibilità elettronica: Circuiti di controllo dei danni da polvere e umidità
- Geometria complessa: Molteplici fessure e superfici intrappolano gli agenti contaminanti
- Accesso per la manutenzione: Componenti interni esposti durante il servizio
Requisiti dell'industria alimentare e delle bevande
Standard di progettazione sanitaria
La lavorazione degli alimenti richiede caratteristiche specifiche degli attuatori:
Requisiti | Capacità pneumatica | Sfida elettrica | Vantaggio Bepto |
---|---|---|---|
Materiali FDA | Acciaio inossidabile, guarnizioni FDA | Opzioni limitate | Conformità completa |
Capacità di lavaggio | IP67, design sigillato | Richiede custodie | Caratteristica standard |
Superfici lisce | Finiture lucide | Geometrie complesse | Design sanitario |
Compatibilità chimica | Materiali resistenti | Problemi di corrosione | Materiali specializzati |
Pulizia e sanificazione
I requisiti di pulizia dell'industria alimentare favoriscono i sistemi pneumatici:
- Lavaggio ad alta pressione: I cilindri sigillati resistono alla pulizia aggressiva
- Sanificatori chimici: I materiali compatibili resistono ai prodotti chimici per la pulizia
- Pulizia a vapore: Capacità di sterilizzazione ad alta temperatura
- Sistemi CIP/SIP: Compatibilità con la pulizia e la sterilizzazione in loco
Produzione farmaceutica
Requisiti dell'ambiente sterile
La produzione di farmaci richiede un funzionamento privo di contaminazioni:
- Compatibilità con la camera bianca: Minima generazione di particelle e facilità di pulizia
- Materiali sterili: Componenti biocompatibili e sterilizzabili
- Requisiti di convalida: Documentazione e procedure di qualificazione
- Controllo delle modifiche: Modifiche minime durante le campagne di produzione
Conformità normativa
Le applicazioni farmaceutiche richiedono un'ampia documentazione:
- Convalida FDAConformità alla normativa 21 CFR Part 11 per le registrazioni elettroniche.
- Requisiti GMP: Norme di buona fabbricazione
- Tracciabilità dei materiali: Documentazione completa dei materiali dei componenti
- Convalida della pulizia: Procedure di pulizia e decontaminazione collaudate
Ambienti di contaminazione industriale
Ambienti polverosi
Vantaggi pneumatici in atmosfere cariche di particelle:
- Impianti di cemento: Protezione dalle polveri di calcare e cemento
- Operazioni minerarie: Resistenza alla polvere di carbone e alle particelle minerali
- Movimentazione dei cereali: Protezione dalla polvere e dai detriti in agricoltura
- Lavorazione del legno: Ambienti con segatura e particelle di legno
Condizioni umide e bagnate
Capacità di resistenza all'umidità:
- Applicazioni esterne: Esposizione alle intemperie e precipitazioni
- Aree di lavaggio: Pulizia regolare con acqua ad alta pressione
- Ambienti a vapore: Umidità e condensa elevate
- Applicazioni marine: Esposizione a nebbia salina e umidità
Soluzioni Bepto resistenti alla contaminazione
Design del cilindro sanitario
Caratteristiche specifiche per ambienti puliti:
- Superfici elettrolucidate: Finiture lisce che impediscono l'accumulo di contaminazione
- Design senza crepe: Eliminazione delle aree in cui possono accumularsi i contaminanti
- Disposizioni per il drenaggio: Consente il drenaggio completo durante la pulizia
- Certificazioni dei materiali: Conformità agli standard sanitari FDA e 3A
Rivestimenti e materiali protettivi
Maggiore resistenza alla contaminazione:
Tipo di ambiente | Rivestimento/Materiale | Livello di protezione | Esempi di applicazione |
---|---|---|---|
Lavorazione degli alimenti | Elettrolucidato 316SS | Eccellente | Latticini, bevande |
Esposizione chimica | Rivestimento in PTFE | Superiore | Impianti chimici |
Ambiente marino | Inox duplex | Eccellente | Piattaforme offshore |
Alta temperatura | Rivestimento in ceramica | Buono | Fonderie, acciaierie |
Procedure di lavaggio e pulizia
Capacità di lavaggio pneumatico
Cilindri progettati per una pulizia aggressiva:
- Cuscinetti sigillati: Prevenzione dell'ingresso di acqua e sostanze chimiche
- Progettazione del drenaggio: Rimozione completa dell'acqua dopo la pulizia
- Resistenza chimica: Materiali compatibili con i detergenti
- Valori di pressione: Resistenza alla pulizia a spruzzo ad alta pressione
Limitazioni della pulizia dell'attuatore elettrico
I sistemi elettronici richiedono procedure di pulizia speciali:
- Requisiti dell'involucro: Alloggiamenti di protezione per ambienti di lavaggio
- Isolamento elettrico: Disconnessione dell'alimentazione durante la pulizia
- Requisiti di essiccazione: Tempo di asciugatura prolungato dopo la pulizia a umido
- Complessità della manutenzione: Smontaggio necessario per una pulizia accurata
Standard di tenuta ambientale
Sistema di classificazione IP
Classificazioni internazionali di protezione per la sigillatura ambientale:
- IP54: Protetto da polvere e spruzzi d'acqua
- IP65: Protezione completa dalla polvere e resistenza ai getti d'acqua
- IP67: Protezione completa dalla polvere e immersione temporanea in acqua
- IP69K: Capacità di lavaggio ad alta pressione e ad alta temperatura
Standard NEMA per le custodie
Classificazioni nordamericane di protezione ambientale:
- NEMA 4: Resistente alle intemperie per applicazioni esterne
- NEMA 4X: Materiali resistenti alla corrosione per ambienti difficili
- NEMA 6P: Protezione temporanea dall'immersione
- NEMA 12: Uso industriale con protezione contro la polvere e il gocciolamento di liquidi
Manutenzione in ambienti contaminati
Vantaggi della manutenzione pneumatica
Assistenza semplificata in ambienti sporchi:
- Servizio esterno: La maggior parte della manutenzione viene eseguita senza smontaggio
- Tolleranza alla contaminazione: I sistemi funzionano nonostante la contaminazione esterna
- Pulizia semplice: Procedure di decontaminazione di base
- Riparazione sul campo: Capacità di assistenza in loco in aree contaminate
Le sfide della manutenzione del sistema elettrico
Requisiti di servizio complessi in ambienti contaminati:
- Necessità di un ambiente pulito: Il servizio richiede condizioni di assenza di contaminazione
- Procedure specializzate: Decontaminazione prima e dopo il servizio
- Protezione delle apparecchiature: Prevenzione della contaminazione durante la manutenzione
- Tempi di inattività prolungati: Requisiti di tempo per la pulizia e la decontaminazione
Impatto dei costi della protezione dalla contaminazione
Analisi dei costi legati alla contaminazione
La protezione dell'ambiente influisce sui costi totali del sistema:
Livello di protezione | Pneumatico Premium | Elettrico Premium | Impatto della manutenzione |
---|---|---|---|
Basic (IP54) | 0-10% | 20-50% | Aumento minimo |
Standard (IP65) | 10-20% | 50-100% | Aumento moderato |
Lavaggio (IP67) | 20-30% | 100-200% | Aumento significativo |
Sanitario (IP69K) | 30-50% | 200-400% | Aumento importante |
Mark, che gestisce l'automazione di un impianto di trasformazione alimentare in California, aveva bisogno di attuatori per una nuova linea di produzione di salse che richiedeva lavaggi giornalieri ad alta pressione con detergenti caustici. Gli attuatori elettrici richiedevano costose custodie in acciaio inox e complessi sistemi di tenuta che costavano $4.500 per unità, mentre i cilindri sanitari Bepto con superfici elettrolucidate e guarnizioni conformi alla FDA costavano $1.200 per unità e fornivano una capacità di pulizia superiore con un tempo di attività di 99,8% in due anni di funzionamento.
Che ruolo hanno le vibrazioni, gli urti e l'esposizione ai prodotti chimici nella selezione?
Le sollecitazioni meccaniche e i requisiti di compatibilità chimica hanno un impatto significativo sulle prestazioni e sulla durata degli attuatori, con tecnologie diverse che mostrano vantaggi distinti in condizioni operative difficili.
I cilindri pneumatici offrono una resistenza superiore alle vibrazioni e agli urti grazie alla struttura meccanica e alla flessibilità di montaggio, oltre a un'eccellente compatibilità chimica con la scelta dei materiali, mentre gli attuatori elettrici soffrono della sensibilità dei componenti elettronici alle sollecitazioni meccaniche e delle limitate opzioni di resistenza chimica.

Resistenza alle vibrazioni e agli urti
Tolleranza alle vibrazioni dei cilindri pneumatici
I sistemi meccanici eccellono negli ambienti ad alta vibrazione:
- Costruzione solida: I componenti metallici resistono alla fatica indotta dalle vibrazioni
- Montaggio flessibile: Ammortizzatori e giunti flessibili consentono il movimento
- Nessuna elettronica sensibile: Funzionamento meccanico non influenzato dalle vibrazioni
- Durata comprovata: Decenni di funzionamento affidabile nelle attrezzature mobili
Sensibilità alle vibrazioni dell'attuatore elettrico
I componenti elettronici sono soggetti a sollecitazioni meccaniche:
- Fatica del giunto a saldare: Le vibrazioni ripetute causano guasti ai collegamenti elettrici
- Allentamento dei componenti: Le sollecitazioni meccaniche allentano i collegamenti elettrici
- Sensibilità dell'encoder: Dispositivi di retroazione della posizione danneggiati dalle vibrazioni
- Interruzione del circuito di controllo: Interferenza elettronica da vibrazioni meccaniche
Resistenza agli urti e agli impatti
Assorbimento pneumatico degli urti
I cilindri gestiscono gli impatti meccanici improvvisi:
Livello di shock | Risposta pneumatica | Vulnerabilità elettrica | Esempi di applicazione |
---|---|---|---|
Leggero (1-5g) | Nessun effetto | Problemi potenziali | Macchinari generici |
Moderato (5-15g) | Tolleranza eccellente | Sollecitazione del componente | Attrezzature mobili |
Pesante (15-50 g) | Buono con lo smorzamento | Probabile fallimento | Macchinari a impatto |
Grave (>50g) | Richiede l'isolamento | Fallimento certo | Pile driver, martelli |
Strategie di protezione dagli impatti
Protezione degli attuatori dagli urti meccanici:
- Supporti per ammortizzatori: Isolamento dalle vibrazioni per componenti sensibili
- Giunti flessibili: Adattamento a disallineamenti e urti
- Sistemi di smorzamento: Assorbimento dell'energia durante gli impatti
- Isolamento strutturale: Separazione degli attuatori dalle fonti di vibrazione
Considerazioni sull'esposizione chimica
Compatibilità chimica dei pneumatici
I materiali dei cilindri resistono agli attacchi chimici:
- Struttura in acciaio inox: Resistenza alla corrosione in ambienti aggressivi
- Guarnizioni resistenti agli agenti chimici: Viton, PTFE ed elastomeri speciali
- Rivestimenti protettivi: Rivestimenti in PTFE, ceramica e polimeri
- Selezione del materiale: Materiali personalizzati per ambienti chimici specifici
Attuatore elettrico Limitazioni chimiche
I sistemi elettronici devono affrontare problemi di compatibilità chimica:
- Opzioni di materiale limitate: I materiali standard potrebbero non resistere agli agenti chimici
- Complessità delle guarnizioni: I punti di tenuta multipli aumentano il potenziale di guasto
- Limiti del rivestimento: I rivestimenti protettivi possono interferire con la dissipazione del calore.
- Complessità della manutenzione: Decontaminazione chimica richiesta per il servizio
Applicazioni in ambiente chimico
Operazioni in atmosfera corrosiva
Vantaggi pneumatici in ambienti chimici aggressivi:
- Trattamento acido: Acciaio inossidabile e guarnizioni resistenti agli acidi
- Ambienti caustici: Materiali e rivestimenti resistenti agli alcali
- Esposizione ai solventi: Elastomeri e metalli resistenti agli agenti chimici
- Nebbia salina: Materiali marini per applicazioni costiere
Resistenza chimica specializzata
Opzioni di materiali Bepto per ambienti chimici:
Classe chimica | Materiali consigliati | Opzioni di tenuta | Opzioni di rivestimento |
---|---|---|---|
Acidi | 316SS, Hastelloy | Viton, PTFE | PTFE, ceramica |
Basi | 316SS, Inconel | EPDM, Viton | Rivestimenti polimerici |
Solventi | Acciaio inox | Viton, FFKM | Rivestimento in PTFE |
Ossidanti | Monel, Inconel | FFKM | Rivestimenti specializzati |
Applicazioni mobili e di trasporto
Apparecchiature montate su veicoli
I sistemi pneumatici eccellono nelle applicazioni mobili:
- Attrezzature montate su camion: Vibrazioni e urti costanti dovuti alla circolazione stradale
- Macchine da costruzione: Ambienti ad alta vibrazione e impatto
- Attrezzature agricole: Condizioni di campo con polvere, umidità e urti
- Applicazioni marine: Movimento costante e vibrazioni dovute all'azione delle onde
Sistemi ferroviari e di transito
Le applicazioni di trasporto favoriscono l'affidabilità del pneumatico:
- Operatori per porte: Migliaia di cicli giornalieri con esposizione alle vibrazioni
- Sistemi frenanti: Applicazioni critiche per la sicurezza che richiedono affidabilità
- Sistemi di sospensione: Variazioni di carico e vibrazioni costanti
- Attrezzatura della piattaforma: Esposizione agli agenti atmosferici e stress meccanico
Test di stress ambientale
Standard per le prove di vibrazione
Standard industriali per la resistenza alle vibrazioni:
- MIL-STD-8104: Standard militare per i test ambientali
- IEC 60068: Standard internazionale per le prove ambientali
- Norme ASTM: Società americana per le prove e i materiali
- ISO 16750: Standard per le prove ambientali nel settore automobilistico
Test di compatibilità chimica
Verifica delle prestazioni dei materiali in ambienti chimici:
- ASTM D543: Test standard per la resistenza chimica delle materie plastiche
- Standard NACE: Associazione nazionale degli ingegneri della corrosione
- ISO 175: Determinazione della resistenza chimica delle materie plastiche
- Test personalizzati: Test di esposizione chimica per applicazioni specifiche
Considerazioni sulla progettazione per ambienti difficili
Progettazione del sistema pneumatico
Ottimizzazione dei cilindri per condizioni difficili:
- Selezione del materiale: Scelta di metalli e guarnizioni appropriati
- Design di montaggio: Sistemi di montaggio flessibili per l'isolamento dalle vibrazioni
- Configurazione delle guarnizioni: Barriere a tenuta multipla per la protezione chimica
- Disposizioni sul drenaggio: Prevenzione dell'accumulo di sostanze chimiche e della corrosione
Strategie di protezione
Migliorare la sopravvivenza degli attuatori in ambienti difficili:
- Custodie di protezione: Protezione dall'esposizione a sostanze chimiche e detriti
- Sistemi di ventilazione: Prevenzione dell'accumulo di vapori chimici
- Sistemi di monitoraggio: Rilevamento precoce del danno ambientale
- Manutenzione preventiva: Ispezione regolare e sostituzione dei componenti
Impatto dei costi della protezione ambientale
Costi di tempra ambientale
Le misure di protezione influiscono sull'economia del sistema:
Tipo di protezione | Impatto dei costi della pneumatica | Impatto dei costi elettrici | Vantaggi in termini di affidabilità |
---|---|---|---|
Vibrazione di base | Premio 5-15% | Premio 25-75% | Miglioramento moderato |
Protezione dagli urti | 15-25% premio | 50-150% premio | Miglioramento significativo |
Resistenza chimica | Premio 20-40% | 100-300% premio | Miglioramento importante |
Protezione combinata | Premio 30-60% | 200-500% premio | Eccellente affidabilità |
Manutenzione in ambienti difficili
Vantaggi della manutenzione pneumatica
Vantaggi del servizio in condizioni difficili:
- Costruzione robusta: I componenti resistono all'esposizione ambientale
- Decontaminazione semplice: Procedure di pulizia di base prima della manutenzione
- Capacità di riparazione sul campo: Assistenza in loco in ambienti difficili
- Procedure standard: Si applicano le pratiche di manutenzione convenzionali
Le sfide della manutenzione del sistema elettrico
Requisiti di servizio complessi in ambienti difficili:
- Sensibilità ambientale: Componenti danneggiati dall'esposizione durante il servizio
- Requisiti di decontaminazione: Pulizia approfondita prima e dopo il servizio
- Attrezzature specializzate: Protezione dell'ambiente durante la manutenzione
- Tempi di inattività prolungati: Tempo supplementare per le procedure di protezione ambientale
Lisa, che gestisce le attrezzature di un'azienda mineraria del Nevada, aveva bisogno di attuatori per le attrezzature di lavorazione del minerale esposte a vibrazioni costanti, polvere chimica e temperature estreme. Gli attuatori elettrici si guastavano nel giro di 8-12 mesi, nonostante le costose custodie protettive, mentre i cilindri Bepto in acciaio inox con guarnizioni resistenti alle sostanze chimiche hanno funzionato in modo affidabile per oltre 4 anni con la sola sostituzione di routine delle guarnizioni, riducendo i costi annuali degli attuatori di 75% e migliorando la disponibilità del sistema a 98,5%.
Conclusione
I fattori ambientali, tra cui temperature estreme, atmosfere esplosive, contaminazione, vibrazioni ed esposizione chimica, favoriscono fortemente i cilindri pneumatici per le condizioni difficili, mentre gli attuatori elettrici richiedono ambienti controllati e costosi sistemi di protezione, rendendo l'analisi ambientale fondamentale per la scelta ottimale dell'attuatore.
Domande frequenti sui fattori ambientali nella selezione degli attuatori
D: I cilindri pneumatici possono operare in atmosfere esplosive senza particolari modifiche?
Sì, i cilindri pneumatici sono intrinsecamente antideflagranti perché non contengono fonti di accensione elettrica, il che li rende ideali per gli ambienti pericolosi senza le costose custodie antideflagranti o le certificazioni richieste per gli attuatori elettrici.
D: Come influiscono le temperature estreme sulla scelta tra attuatori pneumatici ed elettrici?
I cilindri pneumatici funzionano in modo affidabile da -40°F a +200°F con materiali appropriati, mentre gli attuatori elettrici funzionano in genere solo in intervalli da -10°F a +140°F, rendendo i sistemi pneumatici superiori per fonderie, magazzini frigoriferi e applicazioni esterne.
D: Quale tecnologia gestisce meglio i requisiti di contaminazione e lavaggio?
I cilindri pneumatici eccellono grazie a design sigillati, grado di protezione IP67 e capacità di lavaggio con materiali per uso alimentare, mentre gli attuatori elettrici richiedono costose custodie protettive e devono affrontare la sensibilità all'umidità in ambienti contaminati.
D: I cilindri senza stelo offrono una migliore protezione ambientale rispetto ai cilindri standard?
I cilindri pneumatici senza stelo offrono una maggiore protezione ambientale grazie al design chiuso e all'accoppiamento magnetico, garantendo una migliore resistenza alla contaminazione e un funzionamento più fluido in ambienti polverosi o corrosivi rispetto ai cilindri standard.
D: Come influiscono le vibrazioni e gli urti sulle prestazioni degli attuatori pneumatici rispetto a quelli elettrici?
I cilindri pneumatici offrono una resistenza superiore alle vibrazioni e agli urti grazie alla struttura meccanica, mentre gli attuatori elettrici soffrono della sensibilità dei componenti elettronici, dell'affaticamento dei giunti di saldatura e del danneggiamento dell'encoder in ambienti ad alta vibrazione.
-
Esplorate le proprietà dei materiali di tenuta ad alte prestazioni come Viton (FKM) e PTFE per comprenderne le capacità di resistenza alle temperature e agli agenti chimici. ↩
-
Comprendere le direttive ATEX, le normative dell'Unione Europea che definiscono i requisiti delle apparecchiature utilizzate in atmosfere potenzialmente esplosive. ↩
-
Scoprite cosa significano le classificazioni Ingress Protection (IP) come IP67 e IP69K e come definiscono la resistenza di un prodotto alla polvere e ai getti d'acqua ad alta pressione e ad alta temperatura. ↩
-
Scoprite lo scopo del MIL-STD-810, uno standard militare statunitense che definisce le rigorose procedure di test ambientali per le apparecchiature. ↩