Les ingénieurs sont soumis à une pression constante pour optimiser les lignes de production tout en faisant face aux contraintes d'espace et aux problèmes de contamination. Les vérins à tige traditionnels créent des cauchemars en matière de maintenance et occupent un espace précieux au sol.
Un chariot pneumatique sans tige fonctionne en utilisant de l'air comprimé pour déplacer un piston interne qui se connecte à un chariot externe par l'intermédiaire d'un couplage magnétique ou d'une liaison mécanique, fournissant un mouvement linéaire sans tige exposée tout en intégrant des guides de précision pour un fonctionnement en douceur.
Il y a deux semaines, j'ai reçu un appel urgent d'Henrik, directeur de production d'une usine de transformation alimentaire danoise. Sa ligne d'emballage ne cessait de s'arrêter parce que des résidus de chocolat bloquaient les tiges cylindriques exposées. Nous lui avons expédié nos lames d'air magnétiques sans tige dans les 48 heures. Après l'installation, sa ligne a fonctionné sans contamination pendant trois mois d'affilée, ce qui lui a permis d'économiser plus de $50 000 euros en coûts d'immobilisation.
Table des matières
- Quels sont les principaux composants d'un toboggan pneumatique sans tige ?
- Comment fonctionne le système de couplage magnétique ?
- Qu'est-ce qui différencie les vérins sans tige des vérins traditionnels ?
- Comment contrôler la vitesse et la position ?
- Quels sont les différents types de mécanismes de transfert de force ?
- Comment calculer la performance et le dimensionnement ?
- Quelles sont les applications courantes des toboggans pneumatiques sans tige ?
- Quelles sont les étapes d'entretien et de dépannage nécessaires ?
- Conclusion
- FAQ sur les toboggans à air sans tige
Quels sont les principaux composants d'un toboggan pneumatique sans tige ?
La compréhension de chaque composant vous aide à sélectionner le bon vérin pneumatique sans tige et à l'entretenir correctement pour des années de service fiable.
Un chariot pneumatique sans tige contient un corps de cylindre en aluminium, un piston interne avec un mécanisme d'accouplement, un chariot externe avec des guides intégrés, des ports pneumatiques, des capteurs de position et du matériel de montage conçus pour fonctionner ensemble de manière transparente.
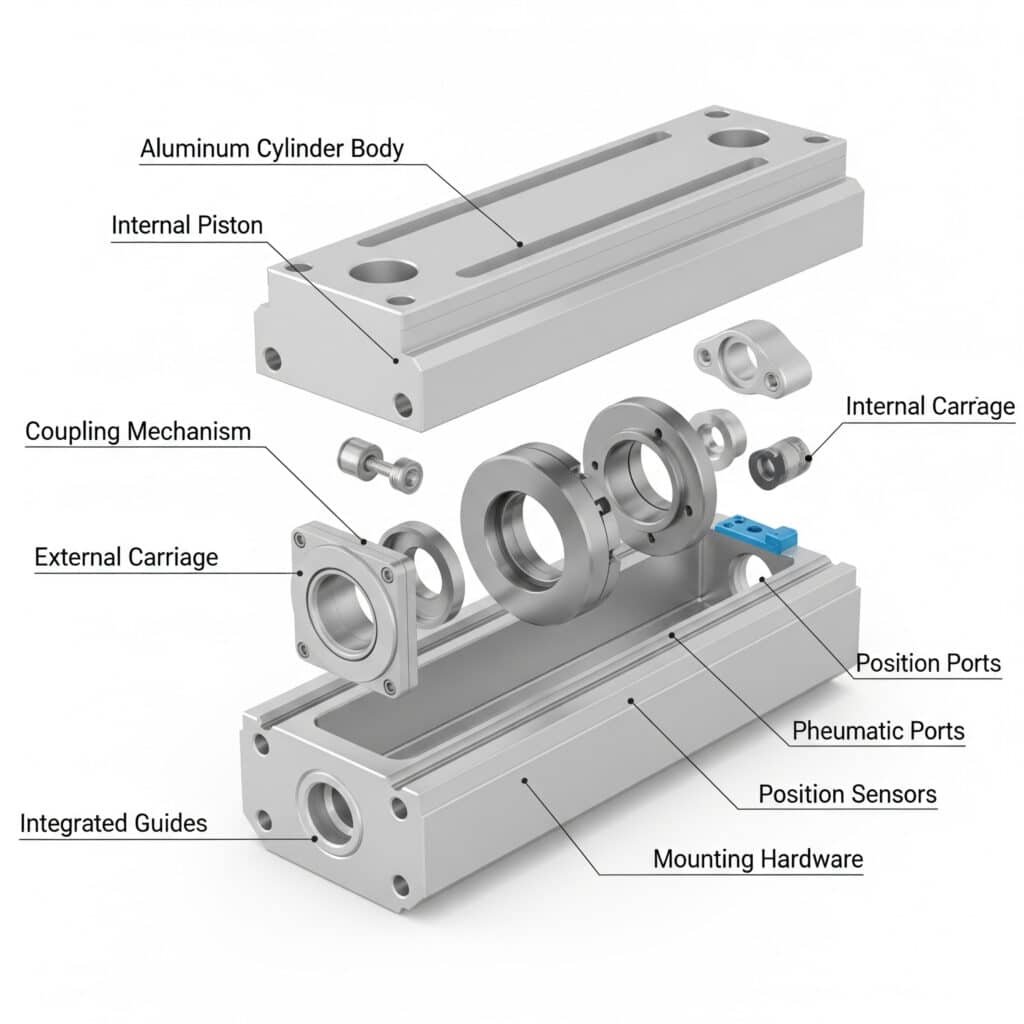
Construction du corps du cylindre
Le corps du vérin constitue le cœur du système de vérins sans tige. La plupart des fabricants utilisent des profils en aluminium extrudé pour un rapport poids/résistance optimal et une résistance à la corrosion.
L'alésage interne nécessite un usinage de précision pour obtenir des états de surface compris entre 0,4 et 0,8. Ra1. Cette finition lisse assure une bonne performance des joints et prolonge la durée de vie des composants.
L'épaisseur de la paroi varie en fonction de la taille de l'alésage et de la pression de fonctionnement. Les modèles standard supportent une pression de fonctionnement allant jusqu'à 10 bars, avec des facteurs de sécurité appropriés.
Assemblage du piston interne
Le piston interne convertit la pression pneumatique en force linéaire. Les pistons de haute qualité sont construits en aluminium léger pour minimiser la masse en mouvement et permettre une accélération plus rapide.
Les joints de piston créent la limite de pression entre les chambres du cylindre. Nous utilisons généralement des joints en polyuréthane ou en NBR en fonction des conditions de fonctionnement et de la compatibilité des fluides.
Des éléments magnétiques intégrés dans le piston créent la force d'accouplement. Les aimants en néodyme et terres rares fournissent le couplage le plus puissant dans le plus petit emballage.
Système de chariot externe
Le chariot externe repose sur des guides linéaires de précision et supporte la charge de votre application. La conception du chariot affecte la rigidité du système et la capacité de charge.
Composant | Options de matériaux | Gamme de tailles typiques | Caractéristiques principales |
---|---|---|---|
Corps de cylindre | Aluminium, anodisé | Alésage de 20 à 100 mm | Résistant à la corrosion |
Piston interne | Aluminium, acier | Correspond à la taille de l'alésage | Conception légère |
Chariot externe | Aluminium, acier | Longueur 50-200 mm | Grande rigidité |
Guides linéaires | Acier trempé | Différents profils | Mouvement de précision |
Aimants | Néodyme | Grade N42-N52 | Stabilité de la température |
Intégration des guides linéaires
Les guides linéaires intégrés éliminent le besoin de systèmes de guidage externes. Cela permet de gagner de l'espace et de réduire la complexité de l'installation tout en garantissant un alignement correct.
Les guides à roulement à billes offrent un fonctionnement plus souple et une plus grande précision. Ils conviennent aux applications nécessitant une précision de positionnement de 0,1 mm.
Les guides à roulements supportent des charges plus importantes tout en conservant une bonne précision. Ils conviennent parfaitement aux applications lourdes avec des exigences de précision modérées.
Les guides à palier lisse constituent la solution la plus économique pour les applications de base. Ils offrent des performances adéquates pour les tâches de positionnement simples.
Configuration des ports pneumatiques
Les orifices d'air relient l'alimentation en air comprimé aux chambres du cylindre. Le dimensionnement des orifices affecte la capacité de débit et la vitesse de fonctionnement.
La taille des orifices standard varie de G1/8 à G1/2 en fonction de la taille de l'alésage du vérin. Des orifices plus grands permettent un fonctionnement plus rapide mais nécessitent une capacité de débit plus élevée.
Les options d'emplacement des ports comprennent les ports d'extrémité, les ports latéraux ou les deux. Les ports latéraux permettent des installations plus compactes dans les espaces restreints.
Systèmes de détection de position
Des capteurs magnétiques détectent la position du piston à travers la paroi non magnétique du cylindre. Interrupteurs Reed2 fournissent un simple retour d'information sur la position marche/arrêt.
Détecteurs à effet Hall3 offrent une détection de position plus précise avec une capacité de sortie analogique. Ils permettent de réaliser des systèmes de contrôle de position en boucle fermée.
Les capteurs externes situés sur le chariot offrent la plus grande précision. Les codeurs linéaires permettent d'atteindre une résolution de positionnement de l'ordre du micromètre.
Comment fonctionne le système de couplage magnétique ?
Le système de couplage magnétique transfère la force pneumatique sans contact physique, ce qui permet un fonctionnement propre et sans entretien.
L'accouplement magnétique utilise de puissants aimants au néodyme dans le piston interne et le chariot externe pour transférer la force à travers la paroi non magnétique du cylindre, ce qui permet d'obtenir un rendement de 85-95% sans usure mécanique.
Principes du champ magnétique
Les aimants permanents créent un champ magnétique qui traverse la paroi du cylindre en aluminium. L'attraction magnétique entre les assemblages d'aimants internes et externes transfère directement la force.
L'intensité du champ magnétique diminue avec la distance. L'entrefer entre les aimants internes et externes a une influence déterminante sur l'intensité et l'efficacité du couplage.
L'orientation de l'aimant affecte les caractéristiques du couplage. La magnétisation radiale permet un couplage uniforme sur la circonférence du cylindre.
Calcul de la force d'accouplement
La force de couplage maximale dépend de la puissance de l'aimant, de la distance de l'entrefer et de la conception du circuit magnétique. Les systèmes typiques atteignent une force de couplage de 200 à 2000 N.
L'efficacité de l'accouplement varie de 85 à 95% en fonction de la qualité de la conception. Les systèmes à haut rendement transfèrent davantage de force pneumatique à la charge.
Les facteurs de sécurité empêchent le glissement de l'accouplement sous des charges normales. La protection contre les surcharges intervient lorsque les forces appliquées dépassent la capacité de l'accouplement magnétique.
Effets de la température
La force de l'aimant diminue avec l'augmentation de la température. Les aimants en néodyme perdent environ 0,12% de force par degré Celsius.
La plage de température de fonctionnement influe sur le choix de la qualité de l'aimant. Les aimants standard fonctionnent à 80°C, tandis que les aimants haute température fonctionnent à 150°C.
Une compensation de température peut être nécessaire pour les applications critiques. Cela permet de garantir des performances constantes en cas de variations de température.
Optimisation du circuit magnétique
La conception des pièces polaires concentre le flux magnétique pour une efficacité maximale du couplage. La géométrie appropriée des pièces polaires augmente la capacité de transfert de force.
La contre-ferrure fournit un chemin de retour pour le flux magnétique. Une épaisseur suffisante de contre-fer empêche la saturation magnétique et maintient la force de couplage.
L'uniformité de l'entrefer assure un couplage constant autour du cylindre. Les tolérances de fabrication doivent maintenir un alignement magnétique correct.
Qu'est-ce qui différencie les vérins sans tige des vérins traditionnels ?
Les vérins sans tige résolvent les problèmes fondamentaux qui limitent les performances des vérins à tige traditionnels dans les systèmes d'automatisation modernes.
Les vérins sans tige éliminent les tiges exposées, ce qui réduit l'encombrement de 50%, empêche l'accumulation de contamination, élimine les problèmes de flambage et permet une meilleure prise en charge des charges latérales grâce aux guides intégrés.
Comparaison de l'efficacité de l'espace
Les vérins traditionnels nécessitent un espace pour l'extension complète de la tige plus la longueur du corps du vérin. L'espace total nécessaire est égal à la longueur de la course plus la longueur du cylindre plus l'espace de sécurité.
Les conceptions sans tige n'ont besoin que d'une longueur de course et d'un jeu minimal aux extrémités. Cela permet d'économiser 40-60% d'espace d'installation par rapport aux vérins traditionnels.
Les installations compactes permettent une plus grande densité de machines et une meilleure utilisation de l'espace. Cela a un impact direct sur la capacité de production et les coûts des installations.
Résistance à la contamination
Les tiges de piston exposées accumulent la poussière, les débris et les matériaux de traitement. Cette contamination entraîne l'usure, le grippage et la défaillance des joints.
Les conceptions sans tige ne comportent aucune pièce mobile exposée. La construction étanche empêche l'entrée de la contamination et élimine les besoins de nettoyage.
Les applications agroalimentaires bénéficient particulièrement de la résistance à la contamination. Les modèles scellés répondent aux exigences strictes en matière d'hygiène sans modification.
Avantages structurels
Les vérins traditionnels à longue course souffrent d'un flambage de la tige sous l'effet des charges latérales. La charge critique de flambage est la suivante Formule d'Euler4: Fcr = π²EI/(KL)².
Les vérins sans tige éliminent totalement les problèmes de flambage. Le piston interne ne peut pas se déformer, ce qui permet des longueurs de course illimitées dans des limites pratiques.
La capacité de charge latérale augmente considérablement avec les guides intégrés. Les systèmes de guidage peuvent supporter des charges radiales allant jusqu'à plusieurs milliers de Newtons.
Facteur de performance | Cylindre traditionnel | Cylindre sans tige | Amélioration |
---|---|---|---|
Espace nécessaire | 2x course + corps | 1x course seulement | Réduction 50% |
Longueur de course maximale | 2-3 mètres typiques | Possibilité de 6 mètres et plus | 200% augmentation |
Capacité de charge latérale | Très limité | Excellent | Amélioration de 10x |
Risque de contamination | Forte exposition | Entièrement scellé | Réduction 95% |
Fréquence d'entretien | Nettoyage hebdomadaire | Inspection mensuelle | Réduction 75% |
Capacités de manutention de charges
Les vérins traditionnels nécessitent des guides externes pour toute charge latérale. Cela augmente le coût, la complexité et l'encombrement de l'installation.
Les guides intégrés dans les vérins sans tige gèrent les charges latérales, les moments et les charges décentrées. Cela élimine les besoins en guides externes dans la plupart des applications.
L'analyse des charges combinées montre que les vérins sans tige gèrent mieux les combinaisons de forces complexes que les conceptions traditionnelles avec guides externes.
Comment contrôler la vitesse et la position ?
Des systèmes de contrôle appropriés garantissent que votre chariot pneumatique sans tige fonctionne en douceur et avec précision tout en répondant aux exigences de votre application.
Contrôlez la vitesse des vérins sans tige à l'aide de vannes de régulation de débit et de régulateurs de pression, obtenez un positionnement grâce à différents types de capteurs et mettez en œuvre une servocommande pour des profils de mouvement précis et un fonctionnement en boucle fermée.
Méthodes de contrôle de la vitesse
Les régulateurs de débit régulent le débit d'air entrant et sortant des chambres du cylindre. Le débit affecte directement la vitesse du piston selon la formule Q = A × V.
Le contrôle des compteurs restreint le flux d'air entrant dans le cylindre. Cela permet une accélération en douceur et un bon contrôle de la vitesse sous différentes charges.
La commande de sortie des compteurs restreint le flux d'air d'échappement du cylindre. Cette méthode permet un meilleur contrôle de la charge et une décélération en douceur.
Le contrôle bidirectionnel du flux permet un réglage indépendant de la vitesse pour les mouvements d'extension et de rétraction. Cela permet d'optimiser les temps de cycle pour différentes conditions de chargement.
Systèmes de contrôle de la pression
Les régulateurs de pression maintiennent une pression de fonctionnement constante malgré les variations de l'alimentation. La stabilité de la pression garantit la répétabilité de la force et de la vitesse.
Les pressostats fournissent un simple retour d'information sur la position en fonction de la pression de la chambre. Ils détectent de manière fiable les conditions de fin de course.
Le contrôle proportionnel de la pression permet une sortie de force variable. Cela convient aux applications nécessitant différents niveaux de force pendant le fonctionnement.
Technologies de détection de position
Les interrupteurs magnétiques à lames détectent la position du piston à travers les parois du cylindre. Ils fournissent des signaux simples de marche/arrêt pour le contrôle de base de la position.
Les capteurs à effet Hall offrent un retour d'information analogique sur la position avec une résolution plus élevée. Ils permettent un contrôle proportionnel de la position et un positionnement intermédiaire.
Les potentiomètres linéaires situés sur le chariot externe fournissent un retour d'information continu sur la position. Ils conviennent aux applications nécessitant un positionnement précis.
Les codeurs optiques offrent la résolution et la précision de position les plus élevées. Ils permettent une servocommande avec une capacité de positionnement inférieure au millimètre.
Intégration des servocommandes
Les servovalves assurent un contrôle proportionnel du débit sur la base de signaux de commande électriques. Elles permettent un contrôle précis de la vitesse et de la position.
Les systèmes de contrôle en boucle fermée comparent la position réelle à la position commandée. Le contrôle par rétroaction maintient la précision malgré les variations de charge.
Les contrôleurs de mouvement coordonnent plusieurs axes et exécutent des profils de mouvement complexes. Ils intègrent les vérins sans tige dans des systèmes d'automatisation sophistiqués.
L'intégration de l'automate permet la coordination avec d'autres fonctions de la machine. Les protocoles de communication standard simplifient l'intégration du système.
Quels sont les différents types de mécanismes de transfert de force ?
Différents mécanismes de transfert de force conviennent à diverses applications et exigences de performance dans les systèmes de vérins pneumatiques sans tige.
Les vérins sans tige utilisent des accouplements magnétiques pour les applications propres, des systèmes de câbles pour les forces élevées, des mécanismes à bande pour les environnements difficiles et des liaisons mécaniques pour une transmission de force maximale, chacun offrant des avantages spécifiques.
Systèmes de couplage magnétique
Le couplage magnétique offre le fonctionnement le plus propre, sans connexion physique entre les composants internes et externes. Cela élimine l'usure et la maintenance.
La force de couplage varie de 200 à 2000 N en fonction de la taille et de la configuration de l'aimant. Des forces plus élevées nécessitent des aimants plus grands et augmentent le coût du système.
La protection contre le glissement évite les dommages en cas de surcharge. L'accouplement magnétique se désengage automatiquement lorsque les forces dépassent les limites de conception.
La stabilité de la température varie en fonction de la qualité de l'aimant choisi. Les aimants haute température conservent leurs performances jusqu'à une température de fonctionnement de 150°C.
Transfert de force par câble
Les systèmes de câbles en acier relient les pistons internes aux chariots externes par des sorties de câbles étanches. Ils offrent une capacité de force supérieure à celle des systèmes magnétiques.
Les matériaux utilisés pour les câbles comprennent l'acier inoxydable pour la résistance à la corrosion et les câbles aéronautiques pour la flexibilité. Le choix du câble a une incidence sur la durée de vie et les performances du système.
Les systèmes de poulies redirigent les forces du câble et peuvent fournir un avantage mécanique. Une conception adéquate des poulies minimise les frottements et l'usure des câbles.
Les problèmes d'étanchéité se posent là où les câbles sortent du cylindre. Les joints dynamiques doivent s'adapter au mouvement des câbles tout en empêchant les fuites d'air.
Systèmes de mécanismes à bande
Des bandes d'acier flexibles transfèrent la force à travers des fentes dans la paroi du cylindre. Elles supportent les forces les plus élevées et les conditions environnementales les plus difficiles.
Les matériaux des bandes comprennent l'acier au carbone, l'acier inoxydable et les alliages spéciaux. Le choix du matériau dépend des exigences en matière d'environnement et de force.
Le scellement des fentes empêche les fuites d'air tout en permettant le mouvement de la bande. Des systèmes d'étanchéité avancés minimisent les fuites sans frottement excessif.
La tolérance à la contamination est excellente car les bandes peuvent pousser à travers les débris. Cela convient aux applications dans des environnements poussiéreux ou sales.
Systèmes de liaison mécanique
Les connexions mécaniques directes assurent un transfert de force positif sans glissement. Elles offrent une transmission de force maximale mais une complexité accrue.
Les systèmes de liaison comprennent la crémaillère, les systèmes de levier et les mécanismes d'engrenage. Le choix dépend des exigences en matière de force et des contraintes d'espace.
La complexité de l'étanchéité augmente avec les pénétrations mécaniques à travers les parois du cylindre. Plusieurs joints dynamiques peuvent être nécessaires.
Les besoins d'entretien sont plus importants en raison de l'usure mécanique et des besoins de lubrification. Un entretien régulier permet de maintenir des performances optimales.
Type de transfert | Gamme de forces | Adéquation de l'environnement | Niveau de maintenance | Meilleures applications |
---|---|---|---|---|
Magnétique | 200-2000N | Propre, température modérée | Très faible | Alimentation, pharmacie, électronique |
Câble | 500-5000N | Industrie générale | Faible | Emballage, assemblage |
Bande | 1000-8000N | Dure, contaminée | Modéré | Industrie lourde, mines |
Mécanique | 2000-15000N | Propre, contrôlé | Haut | Applications à force élevée |
Comment calculer la performance et le dimensionnement ?
Des calculs de performance précis garantissent une sélection correcte des vérins sans tige et une performance optimale du système pour votre application spécifique.
Calculer les performances des vérins sans tige à l'aide des équations de force (F = P × A × η), des calculs de vitesse (V = Q/A), de l'analyse de l'accélération et des facteurs d'efficacité pour déterminer le dimensionnement, la consommation d'air et les performances attendues.
Méthodes de calcul de la force
La force théorique est égale à la pression de l'air multipliée par la surface effective du piston : F = P × A. Cela donne la force maximale disponible dans des conditions idéales.
La force effective tient compte des pertes par frottement et de l'efficacité de l'accouplement : F_eff = P × A × η_coupling × η_friction. L'efficacité globale typique est comprise entre 75 et 90%.
L'analyse des charges comprend le poids statique, les forces de processus, les forces d'accélération et le frottement. Toutes les forces doivent être prises en compte pour un dimensionnement correct.
Des facteurs de sécurité doivent être appliqués aux charges calculées. Les facteurs de sécurité recommandés vont de 1,5 à 2,5 en fonction de la criticité de l'application.
Analyse de la vitesse et du temps de cycle
La vitesse du cylindre est liée au débit d'air : V = Q/A, où la vitesse est égale au débit divisé par la surface effective.
Le temps d'accélération dépend de la force nette et de la masse en mouvement : t = (V × m)/F_net. Des forces plus élevées permettent une accélération plus rapide.
Le temps de cycle comprend les phases d'accélération, de vitesse constante et de décélération. La durée totale du cycle affecte la productivité et le débit.
Les effets d'amortissement réduisent la vitesse près des extrémités de la course. La distance d'amortissement est généralement comprise entre 10 et 50 mm en fonction de la vitesse et de la charge.
Calculs de la consommation d'air
La consommation d'air par cycle est égale au volume du cylindre multiplié par le rapport de pression : V_air = volume du cylindre × (P_abs/P_atm).
La consommation totale du système comprend les pertes par les vannes, les raccords et les fuites. Les pertes ajoutent généralement 20 à 30% à la consommation théorique.
Le dimensionnement du compresseur doit tenir compte de la demande de pointe et des pertes du système. Une capacité adéquate permet d'éviter les chutes de pression en cours de fonctionnement.
L'analyse des coûts énergétiques permet de justifier l'optimisation du système. L'air comprimé coûte généralement $0,02-0,05 par mètre cube.
Optimisation des performances
Le choix de la taille de l'alésage permet d'équilibrer la force requise avec la vitesse et la consommation d'air. Des alésages plus grands fournissent plus de force mais consomment plus d'air.
La longueur de la course a une incidence sur le coût du système et l'espace nécessaire. Les courses plus longues peuvent nécessiter des systèmes de guidage et des structures de montage plus importants.
L'optimisation de la pression de fonctionnement tient compte des besoins en force et des coûts énergétiques. Des pressions plus élevées réduisent la taille des cylindres mais augmentent la consommation d'énergie.
Le choix du système de contrôle correspond à la complexité des exigences de l'application. Les systèmes simples coûtent moins cher mais offrent des fonctionnalités limitées.
Quelles sont les applications courantes des toboggans pneumatiques sans tige ?
Les vérins sans tige excellent dans les applications où l'efficacité de l'espace, la résistance à la contamination ou les longues courses sont des facteurs critiques de succès.
Les applications courantes des vérins sans tige comprennent les machines d'emballage, l'automatisation de l'assemblage, les systèmes de manutention, les opérations de prise et de dépose, et l'intégration des convoyeurs, où une conception compacte et un fonctionnement fiable sont essentiels.
Applications de l'industrie de l'emballage
Les lignes d'emballage bénéficient d'une conception compacte et d'un fonctionnement à grande vitesse. Les glissières pneumatiques sans tige permettent de positionner les produits, de manipuler les cartons et d'intégrer les convoyeurs de manière efficace.
Les emballages alimentaires bénéficient particulièrement d'une conception résistante à la contamination. La construction étanche répond aux exigences strictes en matière d'hygiène sans modifications particulières.
Les emballages pharmaceutiques nécessitent une documentation propre sur le fonctionnement et la validation. Nos systèmes comprennent des certificats de matériaux et des kits d'aide à la validation.
Les lignes d'emballage à grande vitesse atteignent des cadences de 300 par minute. Les pièces mobiles légères permettent une accélération et une décélération rapides.
Systèmes d'automatisation de l'assemblage
L'assemblage électronique utilise des cylindres sans tige pour le placement des composants et la manipulation des circuits imprimés. La propreté des opérations évite la contamination des composants électroniques sensibles.
Les applications d'assemblage automobile comprennent l'insertion de pièces, l'installation de fixations et le positionnement pour l'inspection de la qualité. La fiabilité est cruciale pour la continuité de la production.
L'assemblage de dispositifs médicaux nécessite un positionnement précis et un contrôle de la contamination. Les systèmes validés sont conformes aux normes de la FDA et de l'OMS. Exigences de l'ISO5.
Les systèmes d'assemblage multipostes coordonnent plusieurs vérins sans tige pour les opérations complexes. Les mouvements synchronisés optimisent les temps de cycle et la qualité.
Opérations de manutention
Les systèmes d'automatisation des entrepôts utilisent des vérins sans tige pour les opérations de tri, de déviation et de positionnement. Leur fonctionnement fiable garantit une grande disponibilité du système.
Les centres de distribution bénéficient d'un fonctionnement à grande vitesse et d'un positionnement précis. Un positionnement précis améliore l'efficacité du tri et réduit les erreurs.
Les systèmes de palettisation utilisent plusieurs cylindres sans tige coordonnés pour la formation des couches. Un positionnement précis permet d'obtenir des schémas de palettes optimaux.
Les systèmes de stockage automatisés exigent un positionnement précis pour la gestion des stocks. La précision garantit la récupération et le stockage corrects des articles.
Applications d'enlèvement et de placement
L'intégration robotique utilise des vérins sans tige pour des axes de mouvement supplémentaires. L'extension de la portée améliore l'utilisation de l'espace de travail du robot et sa flexibilité.
Les systèmes guidés par vision combinent des cylindres sans tige avec des caméras pour un positionnement adaptatif. Cela permet de gérer les variations de produits sans reprogrammation.
Les applications de prélèvement à grande vitesse bénéficient de chariots légers et rapides. L'inertie réduite permet une accélération rapide et un arrêt précis.
Les applications de manutention douce utilisent des profils d'accélération contrôlés. La douceur du mouvement évite d'endommager le produit pendant les opérations de manutention.
Domaine d'application | Principaux avantages | Taux de cycle typique | Gamme de forces | Longueur de la course |
---|---|---|---|---|
Emballage | Rapidité, propreté | 100-300 cpm | 200-1500N | 100-1000mm |
Assemblée | Précision, fiabilité | 50-150 cpm | 300-2000N | 50-500mm |
Manutention | Capacité de charge, durabilité | 20-100 cpm | 500-5000N | 200-2000mm |
Pick-and-Place | Vitesse, précision | 200-500 cpm | 100-1000N | 50-800mm |
Quelles sont les étapes d'entretien et de dépannage nécessaires ?
Un entretien adéquat garantit un fonctionnement fiable et maximise la durée de vie de votre système de vérin pneumatique sans tige.
L'entretien des vérins sans tige comprend le remplacement régulier des filtres à air, la lubrification des guides, l'inspection des joints, le nettoyage des capteurs et le contrôle des performances afin de prévenir les pannes et de maintenir un fonctionnement optimal.
Calendrier d'entretien préventif
Les contrôles quotidiens comprennent une inspection visuelle à la recherche de fuites, de bruits inhabituels ou d'un fonctionnement erratique. Une détection précoce permet d'éviter que des problèmes mineurs ne se transforment en défaillances majeures.
L'entretien hebdomadaire comprend l'inspection du filtre à air et son remplacement si nécessaire. Un air propre et sec est essentiel pour un fonctionnement fiable et une longue durée de vie des joints.
L'entretien mensuel comprend la lubrification du guide, le nettoyage du capteur et la vérification des performances. Un entretien régulier permet de maintenir des performances optimales et de prévenir l'usure.
La révision annuelle comprend le remplacement des joints, l'inspection interne et le test complet du système. Les révisions programmées permettent d'éviter les pannes imprévues.
Problèmes courants de dépannage
Un fonctionnement lent indique généralement un débit d'air restreint ou une faible pression. Vérifier les filtres, les régulateurs et les réglages du régulateur de débit.
Un mouvement erratique peut être dû à de l'air contaminé, à des joints usés ou à des problèmes de capteur. Un diagnostic systématique permet d'identifier la cause première.
Les erreurs de position peuvent résulter d'un mauvais alignement du capteur, d'interférences magnétiques ou d'un glissement de l'accouplement. Un diagnostic correct permet d'éviter les problèmes récurrents.
Une consommation d'air excessive indique une fuite interne ou une inefficacité du système. La détection et la réparation des fuites permettent de rétablir un fonctionnement normal.
Procédures de remplacement des joints
Le remplacement des joints nécessite le démontage du cylindre et un outillage approprié. Suivez les procédures du fabricant pour éviter tout dommage pendant l'entretien.
Le choix du joint dépend des conditions d'utilisation et de la compatibilité du support. N'utilisez que des joints de rechange approuvés pour garantir un fonctionnement fiable.
L'installation nécessite une orientation et une lubrification correctes du joint. Une installation incorrecte entraîne une défaillance prématurée et des performances médiocres.
L'essai du système après le remplacement du joint permet de vérifier son bon fonctionnement. Les tests de performance permettent de s'assurer que la réparation a été effectuée avec succès.
Suivi des performances
Le contrôle de la force de sortie détecte la dégradation de l'accouplement ou l'usure interne. Des tests réguliers permettent d'identifier les problèmes avant qu'une défaillance ne se produise.
La surveillance de la vitesse révèle les restrictions de débit ou les problèmes de pression. Une surveillance constante permet une maintenance prédictive.
Le test de précision de la position vérifie le fonctionnement du capteur et l'alignement du système. Un étalonnage régulier permet de maintenir la précision du positionnement.
La surveillance de la consommation d'air permet d'identifier les problèmes d'efficacité et les fuites. L'analyse des tendances permet une planification proactive de la maintenance.
Conclusion
Les glissières pneumatiques sans tige offrent un mouvement linéaire peu encombrant et résistant à la contamination grâce à une technologie de couplage avancée, ce qui les rend essentielles pour les applications d'automatisation modernes exigeant fiabilité et performance.
FAQ sur les toboggans à air sans tige
Comment fonctionne un vérin pneumatique sans tige ?
Un vérin pneumatique sans tige fonctionne en utilisant l'air comprimé pour déplacer un piston interne relié à un chariot externe par un couplage magnétique ou une liaison mécanique, éliminant ainsi la tige de piston exposée tout en fournissant un mouvement linéaire régulier.
Quels sont les principaux avantages des cylindres sans tige par rapport aux cylindres traditionnels ?
Les vérins sans tige permettent d'économiser de l'espace d'installation 50%, de résister à la contamination grâce à une conception étanche, de gérer des longueurs de course illimitées sans flambage et d'offrir une excellente capacité de charge latérale grâce à des guides linéaires intégrés.
Quelle force peut exercer un cylindre magnétique sans tige ?
Les vérins magnétiques sans tige fournissent généralement une force de sortie de 200 à 2000 N en fonction de la taille de l'alésage et de la configuration de l'aimant, avec une efficacité de couplage allant de 85 à 95% de la force pneumatique théorique.
Quel entretien les toboggans à air sans tige nécessitent-ils ?
Les glissières pneumatiques sans tige nécessitent un minimum d'entretien, notamment le remplacement régulier du filtre à air, la lubrification mensuelle des guides, l'inspection annuelle des joints et le nettoyage des capteurs, afin de maintenir des performances et une fiabilité optimales.
Les vérins sans tige peuvent-ils supporter des charges et des moments latéraux ?
Oui, les vérins sans tige excellent dans la manipulation de charges latérales allant jusqu'à plusieurs milliers de Newtons et de moments grâce à leurs systèmes de guidage linéaire de précision intégrés, ce qui élimine le besoin de guides externes.
Comment contrôler la vitesse d'un cylindre pneumatique sans tige ?
Contrôle de la vitesse du vérin sans tige à l'aide de régulateurs de débit sur les conduites d'alimentation en air, avec un contrôle d'entrée pour une accélération en douceur et un contrôle de sortie pour une meilleure manipulation de la charge et une meilleure décélération.
Quelles sont les applications qui conviennent le mieux aux glissières pneumatiques sans tige ?
Les glissières pneumatiques sans tige sont particulièrement adaptées aux machines d'emballage, à l'automatisation de l'assemblage, à la manutention, aux opérations de prise et de dépose et à toutes les applications nécessitant un encombrement réduit, une résistance à la contamination ou de grandes longueurs de course.
-
Découvrez comment Ra (rugosité moyenne) est défini et mesuré en tant que paramètre clé de l'état de surface technique. ↩
-
Découvrez le principe de fonctionnement des interrupteurs Reed et la manière dont ils sont utilisés en tant que capteurs à activation magnétique. ↩
-
Comprendre la physique de l'effet Hall et son application dans la création de capteurs de position précis et sans contact. ↩
-
Examiner la dérivation et l'application de la formule d'Euler pour le calcul de la charge critique de flambage dans les colonnes structurelles. ↩
-
Accédez à une vue d'ensemble des exigences ISO pour les systèmes de gestion de la qualité dans l'industrie des dispositifs médicaux. ↩