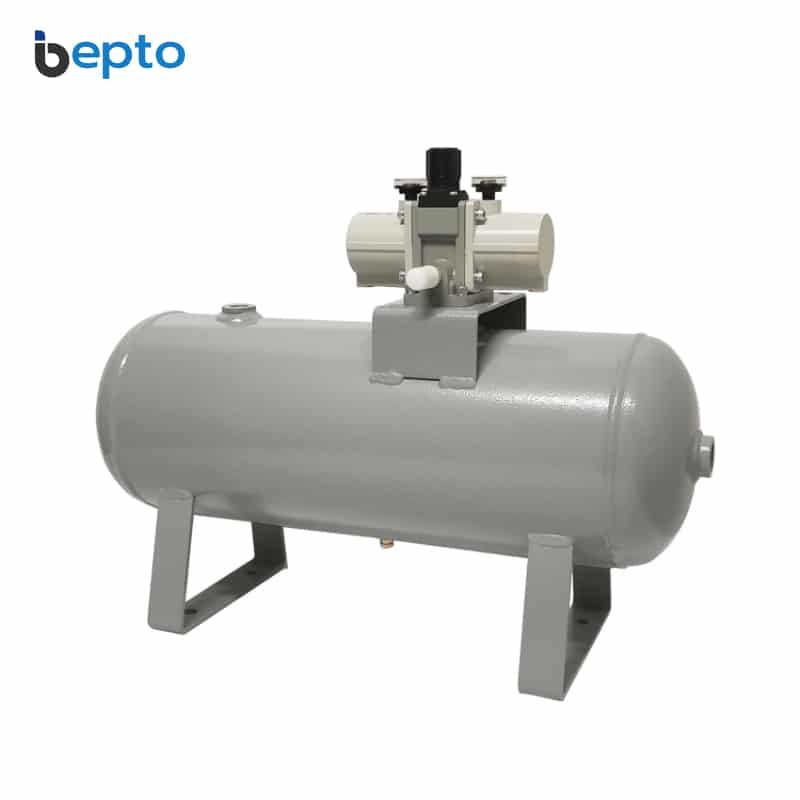
Many engineers struggle with inadequate pneumatic system performance, experiencing pressure drops, slow response times, and excessive compressor cycling that could be eliminated through proper accumulator sizing and implementation.
Pneumatic accumulator sizing requires calculating the required air volume based on system demand, pressure differential, and cycle frequency using the formula V = (Q × t × P1) / (P1 – P2), where proper sizing ensures consistent pressure, reduces compressor cycling, and improves overall system efficiency.
Last week, David from a North Carolina textile plant called me after his pneumatic system couldn’t maintain pressure during peak demand cycles, causing his rodless cylinders1 to operate sluggishly and reducing production by 25% before we helped him properly size and install accumulators that restored full system performance.
Table of Contents
- What Are the Key Factors That Determine Pneumatic Accumulator Size Requirements?
- How Do You Calculate the Required Accumulator Volume for Different Applications?
- What Are the Different Types of Pneumatic Accumulators and Their Sizing Considerations?
- How Do You Select and Install Accumulators for Maximum System Performance?
What Are the Key Factors That Determine Pneumatic Accumulator Size Requirements?
Understanding the critical factors that influence accumulator sizing is essential for designing pneumatic systems that deliver consistent performance and optimal energy efficiency.
Pneumatic accumulator sizing depends on system air consumption rate, acceptable pressure drop, cycle frequency, compressor capacity, and peak demand duration, with proper analysis of these factors ensuring adequate stored air volume to maintain system pressure during high-demand periods.
System Air Consumption Analysis
Peak Demand Calculation
The first step in accumulator sizing involves analyzing peak air consumption:
- Individual cylinder consumption: Calculate air usage per cylinder cycle
- Simultaneous operation: Determine how many cylinders operate concurrently
- Cycle frequency: Establish the maximum cycles per minute
- Duration analysis: Measure peak demand periods
Air Flow Rate Determination
Calculate total system air flow requirements:
Component Type | Typical Consumption | Calculation Method | Example Values |
---|---|---|---|
Standard cylinder | 0.1-2.0 SCFM | Bore area × stroke × cycles/min | 1.2 SCFM |
Rodless cylinder | 0.2-5.0 SCFM | Chamber volume × cycles/min | 2.8 SCFM |
Blow-off nozzles | 1-15 SCFM | Orifice size × pressure | 8.5 SCFM |
Tool operation | 2-25 SCFM | Manufacturer specifications | 12.0 SCFM |
Pressure Requirements and Tolerances
Operating Pressure Range
Define acceptable pressure parameters:
- Maximum pressure (P1): System charging pressure (typically 100-150 PSI)
- Minimum pressure (P2): Lowest acceptable operating pressure (typically 80-90 PSI)
- Pressure differential (ΔP): P1 – P2 determines usable stored air
- Safety margin: Additional capacity for unexpected demand spikes
Pressure Drop Analysis
Consider pressure losses throughout the system:
- Distribution losses: Pressure drop through piping and fittings
- Component requirements: Minimum pressure needed for proper operation
- Dynamic losses: Pressure drops during high flow conditions
- Accumulator location: Distance from point of use affects sizing
Compressor Characteristics
Compressor Capacity Matching
Accumulator sizing must consider compressor capabilities:
- Delivery rate: Actual CFM output at operating pressure
- Duty cycle: Continuous vs. intermittent operation capability
- Recovery time: Time required to recharge system after demand
- Efficiency factors: Real-world performance vs. rated capacity
Load/Unload Cycling
Accumulator sizing affects compressor operation:
Without Adequate Accumulator:
- Frequent start/stop cycling
- High electrical demand
- Reduced compressor life
- Poor pressure regulation
With Proper Accumulator:
- Extended run times
- Stable pressure delivery
- Improved energy efficiency
- Reduced maintenance requirements
Environmental and Application Factors
Temperature Considerations
Temperature affects accumulator performance:
- Ambient temperature: Affects air density and pressure
- Seasonal variations: Summer/winter performance differences
- Heat generation: Compression heating during charging
- Cooling effects: Expansion cooling during discharge
Duty Cycle Analysis
Application patterns influence sizing requirements:
Application Type | Demand Pattern | Sizing Factor | Accumulator Benefit |
---|---|---|---|
Continuous operation | Steady demand | 1.2-1.5x | Pressure stability |
Intermittent cycling | Peak/idle cycles | 2.0-3.0x | Peak demand handling |
Emergency backup | Infrequent use | 3.0-5.0x | Extended operation |
Surge applications | Short high demand | 1.5-2.5x | Rapid response |
At Bepto, we regularly help customers optimize their pneumatic systems by properly sizing accumulators for their rodless cylinder applications. Our experience shows that correctly sized accumulators can improve system response time by 40-60% while reducing energy consumption by 15-25%.
How Do You Calculate the Required Accumulator Volume for Different Applications?
Accurate accumulator volume calculation requires understanding the fundamental gas laws and applying appropriate formulas based on specific application requirements and operating conditions.
Accumulator volume calculation uses Boyle’s Law2 (P1V1 = P2V2) combined with flow rate analysis, typically requiring V = (Q × t × P1) / (P1 – P2) where Q is flow rate, t is time duration, P1 is charging pressure, and P2 is minimum operating pressure.
Basic Volume Calculation Formula
Standard Accumulator Sizing Equation
The fundamental formula for accumulator sizing:
V = (Q × t × P1) / (P1 – P2)
Where:
- V = Required accumulator volume (cubic feet)
- Q = Air flow rate during peak demand (SCFM)
- t = Duration of peak demand (minutes)
- P1 = Maximum system pressure (PSIA)
- P2 = Minimum acceptable pressure (PSIA)
Pressure Conversion Considerations
Always use absolute pressure (PSIA)3 in calculations:
- Gauge pressure + 14.7 = Absolute pressure
- Example: 100 PSIG = 114.7 PSIA
- Critical: Using gauge pressure gives incorrect results
Step-by-Step Calculation Process
Step 1: Determine Peak Air Demand
Calculate total system air consumption during peak operation:
Example Calculation:
- 4 rodless cylinders operating simultaneously
- Each cylinder: 2.5 SCFM consumption
- Total peak demand: 4 × 2.5 = 10 SCFM
Step 2: Establish Pressure Parameters
Define operating pressure range:
- Charging pressure: 120 PSIG (134.7 PSIA)
- Minimum pressure: 90 PSIG (104.7 PSIA)
- Pressure differential: 134.7 – 104.7 = 30 PSI
Step 3: Determine Demand Duration
Analyze peak demand timing:
- Continuous peak: Duration of maximum flow requirement
- Intermittent peak: Time between compressor cycles
- Emergency backup: Required operation time without compressor
Step 4: Apply Sizing Formula
Using the example values:
- Q = 10 SCFM
- t = 2 minutes (peak demand duration)
- P1 = 134.7 PSIA
- P2 = 104.7 PSIA
V = (10 × 2 × 134.7) / (134.7 – 104.7) = 2694 / 30 = 89.8 cubic feet
Application-Specific Sizing Methods
Continuous Operation Applications
For systems with steady air demand:
System Parameter | Calculation Method | Typical Values |
---|---|---|
Base consumption | Sum of all continuous loads | 5-50 SCFM |
Peak factor | Multiply by 1.2-1.5 | 1.3 typical |
Duration | Compressor cycle time | 5-15 minutes |
Safety factor | Add 20-30% capacity | 1.25 typical |
Intermittent Cycling Applications
For systems with periodic high demand:
Sizing Approach:
- Identify cycle pattern: Peak demand vs. idle periods
- Calculate peak volume: Air required during maximum demand
- Determine recovery time: Time available for recharging
- Size for worst case: Ensure adequate capacity for longest cycle
Emergency Backup Applications
For systems requiring operation during compressor failure:
Backup Sizing Formula:
V = (Q × t × P1) / (P1 – P2) × Safety Factor
Where safety factor = 1.5-2.0 for critical applications
Advanced Calculation Considerations
Multiple Pressure Level Systems
Some systems operate at different pressure levels:
High Pressure Zone:
- Primary accumulator: Sized for high-pressure applications
- Pressure reducing valves: Maintain lower pressures
- Secondary accumulators: Smaller tanks for low-pressure zones
Temperature Compensation
Temperature affects air density and pressure:
Temperature Correction Factor:
Corrected Volume = Calculated Volume × (T1/T2)
Where:
- T1 = Standard temperature (520°R)
- T2 = Operating temperature (°R)
Practical Sizing Examples
Example 1: Packaging Line Application
System requirements:
- Peak demand: 15 SCFM for 3 minutes
- Operating pressure: 100 PSIG (114.7 PSIA)
- Minimum pressure: 85 PSIG (99.7 PSIA)
Calculation:
V = (15 × 3 × 114.7) / (114.7 – 99.7) = 5162.5 / 15 = 344 cubic feet
Selected accumulator: 350-400 cubic feet capacity
Example 2: Assembly Station Application
System requirements:
- Intermittent demand: 8 SCFM for 1.5 minutes every 10 minutes
- Operating pressure: 90 PSIG (104.7 PSIA)
- Minimum pressure: 75 PSIG (89.7 PSIA)
Calculation:
V = (8 × 1.5 × 104.7) / (104.7 – 89.7) = 1256.4 / 15 = 84 cubic feet
Selected accumulator: 100 cubic feet capacity
Sizing Verification Methods
Performance Testing
Verify accumulator sizing through testing:
- Monitor pressure drop: During peak demand periods
- Measure recovery time: Compressor recharge duration
- Check cycle frequency: Compressor start/stop cycles
- Evaluate performance: System response and stability
Adjustment Calculations
If initial sizing proves inadequate:
- Pressure drop excessive: Increase accumulator size by 25-50%
- Slow recovery: Check compressor capacity or add secondary accumulator
- Frequent cycling: Increase accumulator size or adjust pressure differential
Marcus, a plant engineer from a Georgia automotive facility, implemented our accumulator sizing recommendations for his rodless cylinder system. “Following Bepto’s calculations, we installed a 280-cubic-foot accumulator that eliminated pressure drops during our peak assembly cycles. Our cycle times improved by 35%, and compressor runtime decreased by 40%, saving us $3,200 annually in energy costs.”
What Are the Different Types of Pneumatic Accumulators and Their Sizing Considerations?
Understanding the various pneumatic accumulator designs and their specific characteristics is crucial for selecting the optimal type and size for different system requirements and operating conditions.
Pneumatic accumulators include receiver tanks, bladder accumulators, piston accumulators, and diaphragm accumulators, each with unique sizing considerations based on response time, pressure stability, contamination sensitivity, and maintenance requirements that affect volume calculations and system performance.
Receiver Tank Accumulators
Design Characteristics
Receiver tanks are the most common pneumatic accumulator type:
- Simple construction: Steel or aluminum pressure vessel
- Large capacity: Available in sizes from 5 to 10,000+ gallons
- Cost effective: Lowest cost per cubic foot of storage
- Versatile mounting: Vertical or horizontal installation options
Sizing Considerations for Receiver Tanks
Receiver tank sizing follows standard accumulator calculations with these factors:
Sizing Factor | Consideration | Impact on Volume |
---|---|---|
Moisture separation | Allows 10-15% extra volume | Increase by 1.15x |
Temperature effects | Large thermal mass | Minimal correction needed |
Pressure drop | Gradual discharge | Standard calculation applies |
Installation space | Size constraints | May require multiple units |
Performance Characteristics
Receiver tanks provide specific advantages:
- Excellent moisture separation: Large volume allows water dropout
- Thermal stability: Mass provides temperature buffering
- Low maintenance: No moving parts or seals to replace
- Long service life: 20+ years with proper maintenance
Bladder Accumulator4 Systems
Design and Operation
Bladder accumulators use flexible separation:
- Rubber bladder: Separates compressed air from hydraulic fluid or provides clean air
- Rapid response: Immediate pressure delivery
- Compact design: High pressure capability in small volume
- Clean air delivery: Bladder prevents contamination
Sizing Calculations for Bladder Accumulators
Bladder accumulator sizing requires modified calculations:
Effective Volume = Total Volume × Bladder Efficiency Factor
Where bladder efficiency factor = 0.85-0.95 depending on design
Application-Specific Considerations
Bladder accumulators excel in specific applications:
- Clean air requirements: Pharmaceutical and food processing
- Rapid response: High-speed pneumatic systems
- Limited space: Compact installations
- Pressure surge control: Dampening pressure spikes
Piston Accumulator Designs
Mechanical Configuration
Piston accumulators use mechanical separation:
- Moving piston: Separates gas and liquid chambers
- Precise control: Accurate pressure regulation
- High pressure capability: Suitable for 3000+ PSI systems
- Adjustable precharge: Variable pressure settings
Sizing Methodology
Piston accumulator sizing considers mechanical factors:
Usable Volume = Total Volume × (P1 – P2) / P1 × Piston Efficiency
Where piston efficiency = 0.90-0.98 depending on seal design
Diaphragm Accumulator Systems
Construction Features
Diaphragm accumulators offer unique advantages:
- Flexible diaphragm: Metal or elastomer separation
- Contamination barrier: Prevents cross-contamination
- Maintenance access: Replaceable diaphragm design
- Pressure pulsation damping: Excellent dynamic response
Sizing Parameters
Diaphragm accumulator sizing accounts for:
Parameter | Standard Tank | Diaphragm Design | Sizing Impact |
---|---|---|---|
Effective volume | 100% | 80-90% | Increase calculated size |
Response time | Moderate | Excellent | May allow smaller size |
Pressure stability | Good | Excellent | Standard calculation |
Maintenance factor | Low | Moderate | Consider replacement costs |
Accumulator Type Selection Matrix
Application-Based Selection
Choose accumulator type based on system requirements:
Receiver Tanks Best For:
- Large volume storage requirements
- Cost-sensitive applications
- Moisture separation needs
- Long-term storage applications
Bladder Accumulators Best For:
- Clean air delivery requirements
- Rapid response applications
- Space-constrained installations
- Pressure surge dampening
Piston Accumulators Best For:
- High-pressure applications
- Precise pressure control
- Variable precharge requirements
- Heavy-duty industrial use
Diaphragm Accumulators Best For:
- Contamination-sensitive processes
- Pulsation dampening applications
- Moderate pressure requirements
- Replaceable element designs
Sizing Comparison by Type
Volume Efficiency Factors
Different accumulator types provide varying effective volumes:
Accumulator Type | Volume Efficiency | Sizing Multiplier | Typical Applications |
---|---|---|---|
Receiver tank | 100% | 1.0x | General industrial |
Bladder | 85-95% | 1.1x | Clean applications |
Piston | 90-98% | 1.05x | High pressure |
Diaphragm | 80-90% | 1.15x | Food/pharma |
Cost-Performance Analysis
Consider total cost of ownership:
Initial Cost Ranking (Low to High):
- Receiver tanks
- Diaphragm accumulators
- Bladder accumulators
- Piston accumulators
Maintenance Cost Ranking (Low to High):
- Receiver tanks
- Piston accumulators
- Diaphragm accumulators
- Bladder accumulators
Installation and Mounting Considerations
Space Requirements
Different types have varying installation needs:
- Receiver tanks: Require significant floor space or overhead mounting
- Bladder/Piston: Compact mounting in any orientation
- Diaphragm: Moderate space with access for maintenance
Piping and Connections
Connection requirements vary by type:
- Receiver tanks: Multiple ports for inlet, outlet, drain, and instrumentation
- Specialized accumulators: Specific port configurations and orientations
- Maintenance access: Consider service requirements in sizing and placement
Performance Optimization Strategies
Multiple Accumulator Systems
Some applications benefit from multiple accumulator types:
- Primary storage: Large receiver tank for bulk storage
- Secondary response: Bladder accumulator for rapid response
- Pressure regulation: Diaphragm accumulator for stable delivery
- System optimization: Combine types for optimal performance
Staged Pressure Systems
Multi-stage systems optimize performance:
- High-pressure stage: Compact accumulator for maximum storage
- Intermediate stage: Pressure regulation and conditioning
- Low-pressure stage: Large volume for extended operation
- Control integration: Automated pressure management
At Bepto, we help customers select the optimal accumulator type and size for their specific rodless cylinder applications. Our engineering team considers not just volume requirements, but also response time, contamination sensitivity, and maintenance requirements to recommend the most cost-effective solution.
How Do You Select and Install Accumulators for Maximum System Performance?
Proper accumulator selection and installation are critical for achieving optimal pneumatic system performance, energy efficiency, and long-term reliability in industrial applications.
Accumulator selection requires matching calculated volume requirements with appropriate type, pressure rating, and mounting configuration, while proper installation includes strategic placement, adequate piping, safety devices, and monitoring systems to ensure maximum performance and safe operation.
Accumulator Selection Criteria
Technical Specification Matching
Select accumulators based on calculated requirements:
Selection Parameter | Calculation Method | Safety Factor | Selection Criteria |
---|---|---|---|
Volume capacity | Use sizing formula | 1.2-1.5x | Next larger standard size |
Pressure rating | Maximum system pressure | 1.25x minimum | ASME code compliance |
Temperature rating | Operating temperature range | ±20°F margin | Material compatibility |
Connection size | Flow rate requirements | Minimize pressure drop | 1/2″ minimum for most applications |
Material and Construction Selection
Choose appropriate materials for operating conditions:
- Carbon steel: Standard industrial applications, cost-effective
- Stainless steel: Corrosive environments, food/pharmaceutical
- Aluminum: Weight-sensitive applications, moderate pressures
- Specialized coatings: Harsh chemical environments
Strategic Installation Planning
Optimal Placement Locations
Accumulator placement significantly affects system performance:
Primary Accumulator Placement:
- Near compressor: Reduces pressure drop in main distribution
- Central location: Minimizes piping distances to major consumers
- Accessible mounting: Allows maintenance and monitoring access
- Stable foundation: Prevents vibration and stress
Secondary Accumulator Placement:
- Point of use: Provides immediate response for high-demand equipment
- End of long runs: Compensates for pressure drop in distribution piping
- Critical applications: Backup storage for essential operations
- Surge protection: Dampens pressure spikes from rapid valve operation
Piping Design Considerations
Proper piping ensures maximum accumulator effectiveness:
Inlet Piping:
- Size adequately: Minimum pressure drop during charging
- Include isolation valve: For maintenance and safety
- Install check valve: Prevents backflow during compressor shutdown
- Provide drain valve: For moisture removal and maintenance
Outlet Piping:
- Minimize restrictions: Reduce pressure drop during discharge
- Strategic branching: Direct routing to high-demand areas
- Flow control: Regulate discharge rate if needed
- Monitoring points: Pressure and flow measurement locations
Safety System Integration
Required Safety Devices
Install essential safety equipment:
Safety Device | Purpose | Installation Location | Maintenance Requirements |
---|---|---|---|
Pressure relief valve | Overpressure protection | Accumulator top | Annual testing |
Pressure gauge | System monitoring | Visible location | Calibration every 2 years |
Drain valve | Moisture removal | Lowest point | Weekly operation |
Isolation valve | Service shutdown | Inlet line | Quarterly operation |
Safety Compliance Requirements
Ensure compliance with applicable codes:
- ASME Section VIII5: Pressure vessel construction standards
- OSHA regulations: Workplace safety requirements
- Local codes: Municipal and state pressure vessel regulations
- Insurance requirements: Carrier-specific safety standards
Performance Optimization Techniques
Pressure Management Strategies
Optimize system pressure for maximum efficiency:
Pressure Band Optimization:
- Narrow band: More frequent cycling, better pressure stability
- Wide band: Less frequent cycling, higher energy efficiency
- Application matching: Match pressure band to equipment requirements
- Seasonal adjustment: Modify settings for temperature variations
Flow Distribution Design
Design piping for optimal flow distribution:
Main Distribution Strategy:
- Loop systems: Provide multiple flow paths
- Graduated sizing: Larger pipes near accumulator, smaller at endpoints
- Strategic valving: Allow isolation of system sections
- Expansion accommodation: Allow for thermal expansion
Monitoring and Control Systems
Performance Monitoring Equipment
Install monitoring systems for optimal operation:
Basic Monitoring:
- Pressure gauges: Local indication of system pressure
- Flow meters: Monitor consumption patterns
- Temperature sensors: Track operating temperatures
- Hour meters: Record compressor operating time
Advanced Monitoring:
- Data logging: Record pressure, flow, and temperature trends
- Alarm systems: Alert operators to abnormal conditions
- Remote monitoring: Centralized system oversight
- Predictive maintenance: Trend analysis for maintenance planning
Control System Integration
Integrate accumulators with system controls:
Control Function | Basic System | Advanced System | Performance Benefit |
---|---|---|---|
Pressure control | Pressure switch | PID controller | ±2 PSI vs ±0.5 PSI |
Load management | Manual operation | Automatic sequencing | 15-25% energy savings |
Demand prediction | Reactive control | Predictive algorithms | 20-30% efficiency gain |
Maintenance scheduling | Time-based | Condition-based | 40-60% cost reduction |
Installation Best Practices
Mechanical Installation
Follow proper installation procedures:
Foundation Requirements:
- Adequate support: Size foundation for accumulator weight plus air
- Vibration isolation: Prevent transmission of compressor vibration
- Access clearance: Allow space for maintenance and inspection
- Drainage provision: Slope foundation for moisture drainage
Mounting and Support:
- Proper orientation: Follow manufacturer recommendations
- Secure attachment: Use appropriate fasteners and brackets
- Thermal expansion: Allow for temperature-related movement
- Seismic considerations: Meet local earthquake requirements in applicable areas
Electrical and Control Connections
Install electrical systems properly:
- Power supply: Adequate capacity for control systems and monitoring
- Grounding: Proper electrical grounding for safety
- Conduit protection: Protect wiring from mechanical damage
- Control integration: Interface with existing plant control systems
Commissioning and Testing Procedures
Initial System Testing
Perform comprehensive testing before operation:
Pressure Testing:
- Hydrostatic test: 1.5x operating pressure with water
- Pneumatic test: Gradual pressure increase to operating level
- Leak testing: Soap solution or electronic leak detection
- Relief valve testing: Verify proper operation and settings
Performance Verification:
- Capacity testing: Verify calculated vs. actual storage capacity
- Response testing: Measure system response to demand changes
- Efficiency testing: Monitor compressor cycling and energy consumption
- Safety testing: Verify all safety systems operate correctly
Documentation and Training
Complete installation with proper documentation:
- Installation drawings: As-built piping and electrical diagrams
- Operating procedures: Standard operating and emergency procedures
- Maintenance schedules: Preventive maintenance requirements
- Training records: Operator and maintenance personnel training
Troubleshooting Common Issues
Performance Problems and Solutions
Address common accumulator issues:
Problem | Symptoms | Likely Causes | Solutions |
---|---|---|---|
Inadequate capacity | Pressure drops quickly | Undersized accumulator | Add capacity or reduce demand |
Slow recovery | Long recharge times | Undersized compressor/piping | Upgrade compressor or piping |
Frequent cycling | Compressor starts/stops often | Narrow pressure band | Widen pressure differential |
Excessive moisture | Water in air lines | Poor drainage/separation | Improve drainage, add dryers |
Maintenance Optimization
Establish effective maintenance programs:
- Routine inspections: Weekly visual inspections and pressure checks
- Scheduled maintenance: Monthly drain operations and quarterly valve testing
- Predictive maintenance: Trend monitoring and analysis
- Emergency procedures: Rapid response to system failures
Rebecca, who manages facilities for a Pennsylvania food processing plant, shared her experience with our accumulator sizing and installation service: “Bepto’s engineers helped us design and install a three-stage accumulator system that eliminated pressure fluctuations in our packaging lines. Our product quality improved significantly, and we reduced compressed air energy costs by 28% while increasing production capacity by 15%.”
Conclusion
Proper pneumatic accumulator sizing and installation requires careful analysis of system demands, accurate volume calculations, appropriate type selection, and strategic placement to achieve optimal performance, energy efficiency, and reliable operation in industrial pneumatic systems.
FAQs About Pneumatic Accumulator Sizing
Q: How do I know if my accumulator is properly sized for my system?
A properly sized accumulator maintains system pressure within acceptable limits during peak demand periods, prevents excessive compressor cycling (more than 6-10 starts per hour), and provides adequate response time for pneumatic equipment, with pressure drops typically limited to 10-15 PSI during normal operation.
Q: Can I use multiple smaller accumulators instead of one large accumulator?
Yes, multiple smaller accumulators can provide the same total volume as one large unit and offer advantages like distributed storage, easier installation in tight spaces, and redundancy, but ensure proper piping design to prevent pressure imbalances and consider the higher cost per cubic foot of storage.
Q: What happens if I oversize my pneumatic accumulator?
Oversized accumulators increase initial cost, require more space, take longer to reach operating pressure during startup, and may lead to moisture accumulation problems, but generally don’t harm system performance and can provide beneficial pressure stability and reduced compressor cycling.
Q: How often should pneumatic accumulators be drained and maintained?
Drain accumulators weekly in humid environments or daily in critical applications to remove moisture, inspect pressure relief valves annually, check pressure gauges every 6 months, and perform complete internal inspection every 5-10 years depending on operating conditions and local regulations.
Q: What’s the difference between accumulator sizing for continuous vs. intermittent applications?
Continuous applications require accumulators sized for steady-state demand plus peak surge capacity (typically 1.2-1.5x base demand), while intermittent applications need larger accumulators sized for peak demand duration between compressor cycles (typically 2-5x peak demand), with sizing calculations adjusted for duty cycle patterns.
-
Learn about the design and operational advantages of rodless pneumatic cylinders, which are often used in material handling and automation. ↩
-
Explore Boyle’s Law ($P_1V_1 = P_2V_2$), a fundamental principle describing the inverse relationship between the pressure and volume of a gas at constant temperature. ↩
-
Understand the critical difference between absolute pressure (PSIA), which is measured from a perfect vacuum, and gauge pressure (PSIG), which is measured from atmospheric pressure. ↩
-
Discover the construction and operating principles of bladder accumulators and their applications in fluid power systems. ↩
-
Learn about ASME Section VIII, the division of the Boiler and Pressure Vessel Code that governs the design and construction of pressure vessels. ↩