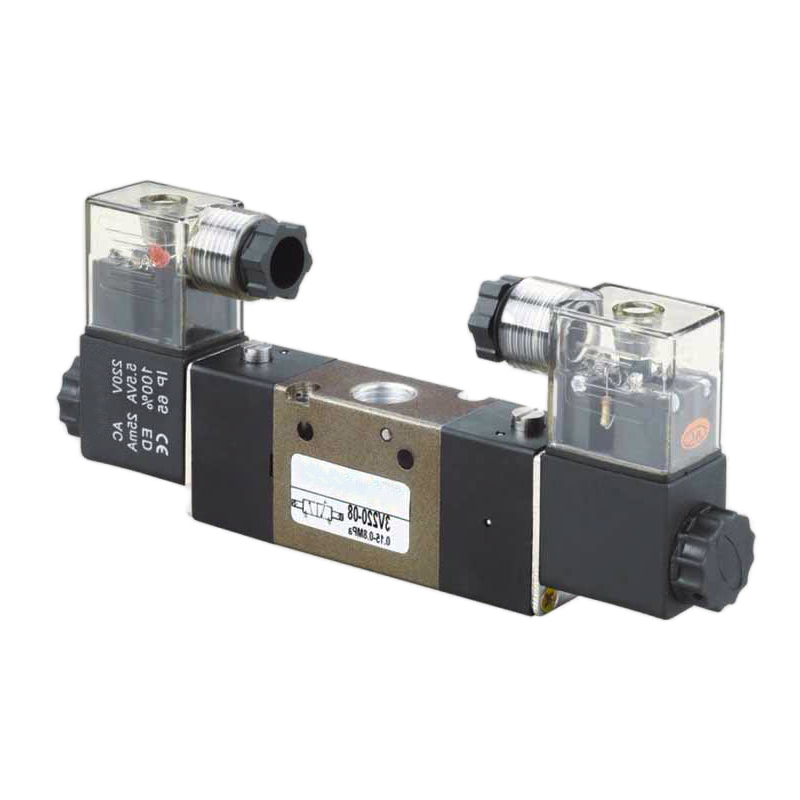
When your automated production line struggles with inconsistent valve response, excessive energy consumption, and unreliable operation of large pneumatic cylinders, the solution often lies in understanding how pilot operated valves can provide precise control with minimal input energy while handling high flow rates.
Pneumatic pilot operated valves work by using a small pilot signal to control a larger main valve, where low-pressure pilot air operates a small control valve that directs high-pressure air to actuate the main valve spool or piston, enabling precise control of high-flow pneumatic systems with minimal energy input.
Two weeks ago, I assisted Marcus Thompson, a production engineer at a packaging facility in Manchester, England, whose rodless cylinder1 positioning system was experiencing erratic movement due to inadequate valve response, requiring an upgrade to pilot operated valves for reliable high-speed operation.
Table of Contents
- What Are the Key Components and Operating Principles of Pilot Operated Valves?
- Why Do Pilot Operated Valves Provide Superior Performance for Large Pneumatic Systems?
- How Do Different Types of Pilot Operated Valves Compare in Industrial Applications?
- What Are the Installation and Maintenance Requirements for Optimal Performance?
What Are the Key Components and Operating Principles of Pilot Operated Valves?
Understanding the internal construction and operation of pilot operated valves is crucial for proper selection and application in pneumatic systems.
Pilot operated valves consist of a main valve body with large flow ports, a pilot valve section with small control ports, and connecting passages that allow pilot pressure to actuate the main valve spool, creating a two-stage amplification system where small pilot signals control large main flows.
Main Valve Components
Primary Flow Section
The main valve handles the bulk air flow to and from your pneumatic equipment:
- Large flow ports (typically 1/2″ to 2″ or larger)
- Main valve spool with precision-machined lands
- High-capacity exhaust ports for rapid cylinder retraction
- Robust valve body designed for high flow rates
Pilot Control Section
The pilot section provides the control intelligence:
- Small pilot ports (typically 1/8″ to 1/4″)
- Pilot valve spool or poppet design
- Low-force actuator (solenoid, manual, or pneumatic)
- Internal pilot passages connecting to main valve
Operating Sequence
Step | Pilot State | Main Valve Action | System Response |
---|---|---|---|
1 | No pilot signal | Main valve centered | Cylinder holds position |
2 | Pilot signal applied | Pilot valve shifts | Internal pressure builds |
3 | Pilot pressure acts | Main spool moves | High flow to cylinder |
4 | Pilot signal removed | Pilot valve returns | Main valve centers |
Pressure Amplification Principle
The key advantage is force multiplication – a small pilot force (typically 3-5 PSI) can control main valve operation at full system pressure (80-150 PSI), providing excellent control sensitivity with high flow capacity.
Why Do Pilot Operated Valves Provide Superior Performance for Large Pneumatic Systems?
Pilot operated valves offer significant advantages over direct-operated valves when controlling high-flow pneumatic applications like large cylinders and rodless actuators.
Pilot operated valves provide superior performance because they separate control function from flow capacity, enabling precise control with low input energy while delivering high flow rates up to 1000+ SCFM, making them ideal for large cylinders, rodless systems, and high-speed applications where direct-operated valves would require excessive force.
Performance Advantages
High Flow Capacity
Pilot operated valves excel in high-demand applications:
- Flow rates up to 1000+ SCFM2
- Large port sizes without proportional control force increase
- Rapid response despite high flow capacity
- Consistent performance across pressure ranges
Energy Efficiency
The two-stage design provides exceptional efficiency:
- Low pilot energy (typically 0.1-0.5 SCFM pilot consumption)
- Reduced control system load on PLCs and control panels
- Lower heat generation in control circuits
- Extended component life due to reduced stress
Application Comparison
Valve Type | Max Flow (SCFM) | Control Force | Response Time | Best Applications |
---|---|---|---|---|
Direct Operated | 50-200 | High | Fast | Small cylinders, simple control |
Pilot Operated | 200-1000+ | Low | Very Fast | Large cylinders, rodless systems |
Servo Valves | 100-500 | Very Low | Ultra Fast | Precision positioning |
Rodless Cylinder Applications
Four months ago, I worked with Sarah Martinez, automation engineer at a logistics center in Phoenix, Arizona. Her high-speed sorting system used large rodless cylinders for package positioning, but the existing direct-operated valves couldn’t provide adequate flow for the required cycle times. The system was operating 40% slower than specification due to insufficient air flow. We replaced the valves with Bepto pilot operated units rated for 600 SCFM, which increased system speed to 105% of design capacity, improved sorting accuracy by 25%, and reduced energy consumption by 30% through more efficient air usage. The upgrade paid for itself in just 6 weeks through increased throughput. 🚀
How Do Different Types of Pilot Operated Valves Compare in Industrial Applications?
Various pilot operated valve designs offer different advantages depending on specific application requirements and operating conditions.
Different pilot operated valve types include solenoid pilot (most common for automation), pneumatic pilot (for remote control), and manual pilot (for setup/maintenance), with 5-port 2-position valves being standard for single-acting cylinders and 5-port 3-position valves preferred for double-acting cylinders requiring mid-stroke stopping capability.
Pilot Actuation Methods
Solenoid Pilot Operation
Most common in automated systems:
- Electrical control integration with PLCs3
- Fast response times (10-50 milliseconds)
- Precise timing for automated sequences
- Remote control capability over long distances
Pneumatic Pilot Operation
Ideal for hazardous or remote locations:
- Intrinsically safe4 operation in explosive atmospheres
- Simple control using pilot air signals
- No electrical connections required
- Reliable operation in harsh environments
Manual Pilot Operation
Used for setup, maintenance, and emergency control:
- Direct operator control for troubleshooting
- Emergency override capability
- Setup and testing functions
- Maintenance positioning of equipment
Valve Configuration Options
Configuration | Positions | Applications | Advantages |
---|---|---|---|
5/2 Pilot | 2-position | Standard cylinders | Simple, reliable |
5/3 Pilot | 3-position | Precision control | Mid-stroke stopping |
4/2 Pilot | 2-position | Single-acting | Cost effective |
3/2 Pilot | 2-position | Simple control | Compact design |
Performance Specifications
Response Characteristics
- Switching time: 15-100 milliseconds typical
- Flow capacity: 200-1000+ SCFM depending on size
- Pressure range: 20-250 PSI operating pressure
- Pilot pressure: 3-15 PSI minimum for reliable operation
Environmental Ratings
- Temperature range: -10°F to +180°F standard
- Vibration resistance: Up to 10G acceleration
- IP ratings: IP65/IP67 available for harsh environments
- Corrosion resistance: Various coating options available
What Are the Installation and Maintenance Requirements for Optimal Performance?
Proper installation and maintenance of pilot operated valves ensures reliable operation and maximum service life in demanding industrial applications.
Pilot operated valves require clean, dry pilot air at 15-20 PSI above switching pressure, proper mounting orientation, adequate flow capacity in pilot lines, and regular maintenance including filter changes, seal inspection, and pilot pressure verification to ensure reliable operation and prevent system downtime.
Installation Requirements
Air Supply Preparation
Critical for reliable pilot valve operation:
- Pilot air filtration to 5 microns or better
- Moisture removal to -40°F pressure dew point5
- Pressure regulation for consistent pilot pressure
- Adequate pilot flow capacity (typically 1-5 SCFM)
Mounting Considerations
- Proper orientation according to manufacturer specifications
- Vibration isolation in high-vibration environments
- Accessibility for maintenance and troubleshooting
- Environmental protection from contamination
Maintenance Schedule
Maintenance Task | Frequency | Critical Points | Performance Impact |
---|---|---|---|
Filter replacement | Monthly | Clean pilot air supply | Prevents sticking |
Pressure check | Quarterly | Verify pilot pressure | Ensures reliable switching |
Seal inspection | Semi-annually | Check for leakage | Maintains efficiency |
Complete service | Annually | Full disassembly/cleaning | Extends service life |
Troubleshooting Guide
Common Issues
- Slow switching: Usually pilot air supply problems
- Incomplete shifting: Insufficient pilot pressure or contamination
- Erratic operation: Moisture or contamination in pilot circuit
- No response: Pilot valve failure or blocked passages
Preventive Measures
- Quality air preparation prevents most problems
- Regular maintenance extends component life
- Proper sizing ensures adequate performance margins
- Environmental protection reduces contamination exposure
Bepto Pilot Valve Advantages
Our pilot operated valves feature:
- Proven reliability in demanding industrial applications
- High flow capacity for large pneumatic systems
- Easy maintenance with accessible components
- Technical support for application assistance
- Competitive pricing compared to OEM alternatives
We provide comprehensive technical documentation and support to ensure optimal performance in your specific application. 🎯
Conclusion
Pilot operated valves provide the ideal solution for controlling high-flow pneumatic systems with precision and efficiency, making them essential for modern industrial automation applications requiring reliable performance.
FAQs About Pneumatic Pilot Operated Valves
What’s the difference between pilot operated and direct operated valves?
Pilot operated valves use a small pilot signal to control a larger main valve, while direct operated valves require the full control force to move the main valve directly. This makes pilot operated valves much more suitable for high-flow applications where direct operated valves would require excessive control force and energy.
How much pilot pressure do I need for reliable operation?
Most pilot operated valves require 15-20 PSI pilot pressure above the switching threshold, typically 3-5 PSI minimum pilot pressure for reliable operation. Insufficient pilot pressure causes slow or incomplete valve switching, while excessive pressure wastes energy without improving performance.
Can pilot operated valves work with rodless cylinders?
Yes, pilot operated valves are excellent for rodless cylinders because they provide the high flow rates needed for rapid acceleration and precise positioning of large moving masses. The high flow capacity and fast response make them ideal for the demanding performance requirements of rodless cylinder applications.
What maintenance do pilot operated valves require?
Pilot operated valves need clean, dry pilot air supply, monthly filter changes, quarterly pilot pressure verification, and annual complete service including seal inspection. Proper air preparation prevents most problems and significantly extends valve service life.
Why do my pilot operated valves respond slowly?
Slow valve response usually indicates contaminated or insufficient pilot air supply, blocked pilot passages, or worn pilot valve seals. Check pilot air filtration, verify adequate pilot pressure and flow, and inspect for internal contamination or component wear.
-
Discover the design, types, and operational advantages of rodless pneumatic cylinders in industrial automation. ↩
-
Understand the definition of Standard Cubic Feet per Minute (SCFM) and why it’s a critical unit for measuring gas flow in pneumatic systems. ↩
-
Learn about Programmable Logic Controllers (PLCs) and their fundamental role in controlling machinery and processes in automation. ↩
-
Explore the concept of intrinsic safety, a design technique applied to electrical equipment for safe use in hazardous locations. ↩
-
Learn about pressure dew point, a key measurement used to determine the water vapor content in compressed air systems. ↩