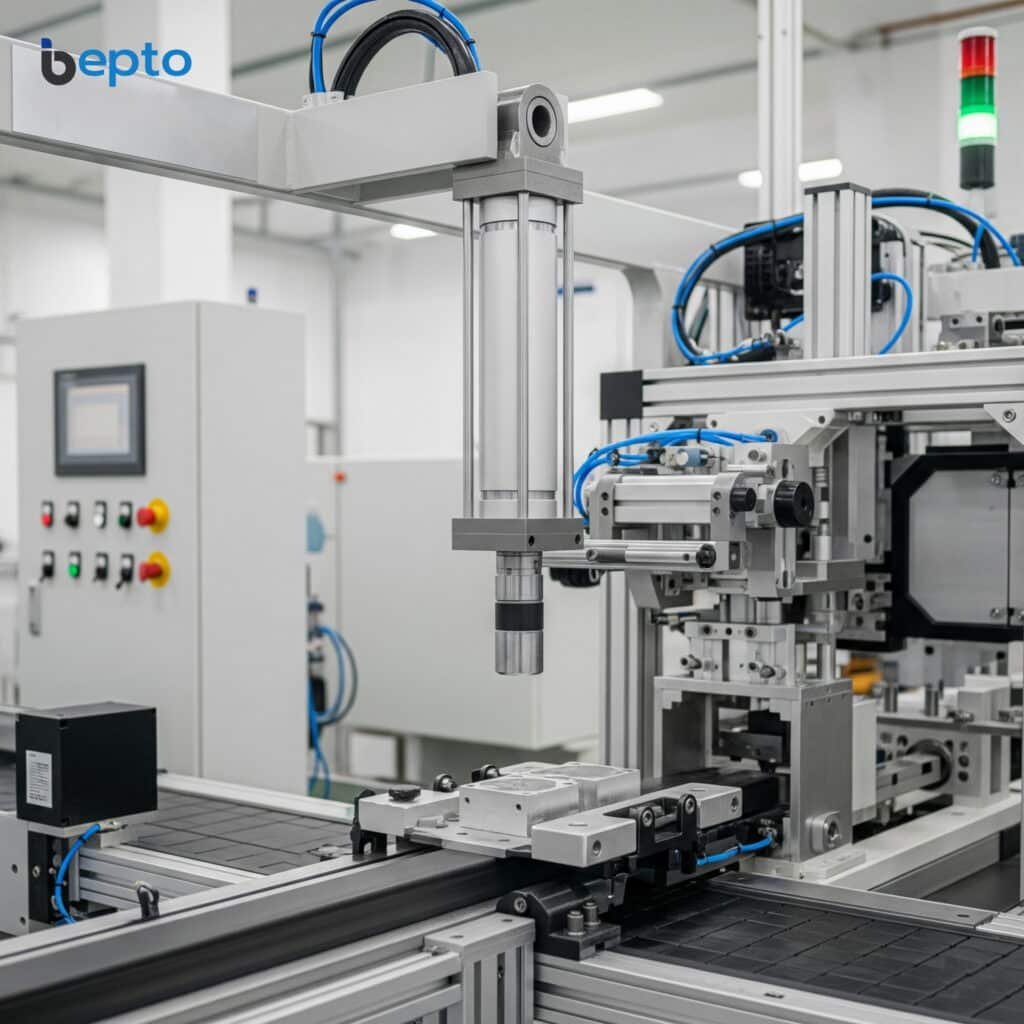
When your pneumatic cylinders operate slower than expected, fail to reach full force output, or consume excessive compressed air, the culprit is often excessive back pressure in your exhaust lines that’s restricting proper air flow and degrading system performance throughout your production line.
Back pressure in a pneumatic system is the resistance to air flow in exhaust lines that opposes the normal discharge of compressed air from cylinders and valves, typically measured in PSI, caused by restrictions like undersized fittings, long tubing runs, or clogged mufflers that reduce cylinder speed and force output.
Two months ago, I assisted Robert Thompson, a maintenance supervisor at a packaging facility in Manchester, England, whose rodless cylinder1 positioning system was operating at only 60% of design speed due to excessive back pressure from improperly sized exhaust components.
Table of Contents
- What Are the Root Causes and Sources of Back Pressure in Pneumatic Systems?
- How Does Back Pressure Affect Cylinder Performance and System Efficiency?
- What Are the Methods for Measuring and Calculating Acceptable Back Pressure Levels?
- How Can You Minimize Back Pressure for Optimal Pneumatic System Performance?
What Are the Root Causes and Sources of Back Pressure in Pneumatic Systems?
Understanding the various sources of back pressure is crucial for diagnosing performance issues and optimizing pneumatic system design for maximum efficiency.
Back pressure sources include undersized exhaust ports and fittings, excessive tubing length, restrictive mufflers or silencers, multiple fittings and connections, contaminated filters, and improper valve sizing that create resistance to air flow and force cylinders to work against exhaust restrictions during operation.
Primary Back Pressure Sources
Exhaust Line Restrictions
The most common causes of excessive back pressure:
- Undersized tubing with internal diameter too small for flow requirements
- Multiple fittings creating turbulence and pressure drops
- Long exhaust runs increasing friction losses over distance
- Sharp bends and restrictive routing causing flow disruption
Component-Related Restrictions
Equipment components that contribute to back pressure:
Component Type | Typical Pressure Drop | Common Issues | Solutions |
---|---|---|---|
Standard Mufflers | 2-8 PSI | Clogged elements | Regular cleaning/replacement |
Quick Disconnects | 1-3 PSI | Multiple connections | Minimize quantity |
Flow Controls | 5-15 PSI | Improper adjustment | Correct sizing/setting |
Filters | 2-10 PSI | Contamination buildup | Scheduled maintenance |
System Design Factors
Valve Configuration Impact
Valve design significantly affects exhaust flow:
- Small exhaust ports relative to supply ports
- Internal valve restrictions in complex valve designs
- Pilot-operated valves with restricted pilot exhaust paths
- Manifold systems with shared exhaust lines
Installation Variables
How components are installed affects back pressure:
- Exhaust line elevation requiring air to flow upward
- Shared exhaust manifolds creating interference between cylinders
- Temperature effects on air density and flow characteristics
- Vibration-induced restrictions from loose or damaged connections
Environmental Contributions
Contamination Effects
Operating environment impacts on back pressure:
- Dust and debris accumulation in exhaust lines
- Moisture condensation creating flow restrictions
- Oil carryover from compressors coating internal surfaces
- Chemical deposits in corrosive environments
Atmospheric Conditions
External factors influencing exhaust flow:
- Altitude effects on atmospheric pressure differential
- Temperature variations affecting air density
- Humidity levels contributing to condensation issues
- Barometric pressure changes affecting exhaust efficiency
How Does Back Pressure Affect Cylinder Performance and System Efficiency?
Back pressure creates multiple negative impacts on pneumatic system operation, reducing both individual component performance and overall system efficiency.
Back pressure reduces cylinder speed by 10-50%, decreases available force output by up to 30%, increases compressed air consumption by 15-40%, causes erratic motion and positioning errors, and can lead to premature component wear due to increased operating stresses and extended cycle times.
Performance Impact Analysis
Speed Reduction Effects
Back pressure directly impacts cylinder operating speeds:
- Retraction speed most affected due to smaller rod-side area
- Extension speed also reduced but typically less severely
- Acceleration rates decreased during rapid positioning moves
- Deceleration characteristics altered affecting positioning accuracy
Force Output Degradation
Available cylinder force is reduced by back pressure:
Back Pressure Level | Force Reduction | Speed Impact | Typical Causes |
---|---|---|---|
0-5 PSI | Minimal | <10% reduction | Well-designed system |
5-15 PSI | 10-20% | 15-30% reduction | Moderate restrictions |
15-25 PSI | 20-30% | 30-50% reduction | Significant problems |
>25 PSI | >30% | >50% reduction | System redesign needed |
Energy Consumption Consequences
Compressed Air Waste
Back pressure increases air consumption through several mechanisms:
- Extended cycle times requiring longer air supply periods
- Higher supply pressures needed to overcome exhaust restrictions
- Incomplete exhaust causing residual pressure in cylinders
- System pressure fluctuations triggering excessive compressor cycling
Economic Impact Assessment
The cost of excessive back pressure includes:
- Increased energy bills from higher compressor operation
- Reduced productivity from slower cycle times
- Premature component replacement due to increased wear
- Maintenance costs for troubleshooting performance issues
Real-World Performance Example
Last year, I worked with Sarah Martinez, production manager at an automotive assembly plant in Detroit, Michigan. Her rodless cylinder conveyor system was experiencing 40% slower than specified cycle times, causing production bottlenecks. Investigation revealed 22 PSI back pressure from undersized 1/4″ exhaust tubing that should have been 1/2″ for the high-flow application. The original equipment supplier had used standard tubing sizes without considering the high exhaust flow requirements of the large rodless cylinders. We replaced the exhaust lines with properly sized Bepto components, reducing back pressure to 6 PSI and restoring full system speed. The $1,200 investment in upgraded exhaust components increased production throughput by 35% and reduced compressed air consumption by 25%, saving $3,800 monthly in energy costs. 🚀
System Reliability Issues
Component Stress Factors
Excessive back pressure creates additional stresses:
- Seal wear from pressure differentials across cylinder seals
- Valve component stress from fighting exhaust restrictions
- Mounting stress from altered force characteristics
- Tubing fatigue from pressure pulsations and vibration
Operational Consistency Problems
Back pressure affects system predictability:
- Variable cycle times depending on load conditions
- Positioning repeatability issues in precision applications
- Temperature sensitivity as back pressure varies with conditions
- Load-dependent performance variations affecting product quality
What Are the Methods for Measuring and Calculating Acceptable Back Pressure Levels?
Accurate measurement and calculation of back pressure levels is essential for diagnosing system problems and ensuring optimal pneumatic performance.
Back pressure measurement requires installing pressure gauges at cylinder exhaust ports during operation, with acceptable levels typically under 10-15 PSI for standard cylinders and under 5-8 PSI for high-speed applications, calculated using flow rate equations and component pressure drop specifications to determine total system resistance.
Measurement Techniques
Direct Pressure Measurement
The most accurate method for determining actual back pressure:
- Gauge installation at cylinder exhaust port during operation
- Dynamic measurement during actual cylinder cycling
- Multiple measurement points throughout exhaust system
- Data logging to capture pressure variations over time
Calculation Methods
Engineering calculations for system design:
Calculation Type | Application | Accuracy Level | When to Use |
---|---|---|---|
Flow equations | System design | ±15% | New installations |
Component specs | Troubleshooting | ±10% | Existing systems |
CFD analysis2 | Complex systems | ±5% | Critical applications |
Empirical data | Similar systems | ±20% | Quick estimates |
Acceptable Back Pressure Limits
Application-Specific Guidelines
Different applications have varying back pressure tolerances:
- Standard industrial cylinders: 10-15 PSI maximum
- High-speed applications: 5-8 PSI maximum
- Precision positioning: 3-5 PSI maximum
- Rodless cylinder systems: 6-10 PSI maximum depending on size
Performance vs. Back Pressure Relationship
Understanding the performance impact curve:
- 0-5 PSI: Minimal performance impact
- 5-10 PSI: Noticeable speed reduction, acceptable for many applications
- 10-15 PSI: Significant impact, limit for standard applications
- >15 PSI: Unacceptable for most industrial applications
Measurement Equipment Requirements
Pressure Gauge Specifications
Proper instrumentation for accurate readings:
- Gauge range: 0-30 PSI typical for back pressure measurement
- Accuracy: ±1% of full scale for reliable data
- Response time: Fast enough to capture dynamic pressure changes
- Connection type: Compatible with pneumatic fittings
Data Collection Methods
Approaches for comprehensive back pressure analysis:
- Instantaneous readings during specific cycle points
- Continuous monitoring throughout complete cycles
- Statistical analysis of pressure variations
- Trend analysis over extended operating periods
Calculation Examples
Basic Flow Calculation
Simplified method for estimating back pressure:
Back Pressure = (Flow Rate × Tube Length × Friction Factor) / (Tube Diameter⁴)
Where factors include:
- Flow rate in SCFM from cylinder specifications
- Tube length including equivalent length of fittings
- Friction factors from engineering tables
- Internal diameter of exhaust tubing
Component Pressure Drop Summation
Total system back pressure calculation:
- Tubing friction loss: Calculated from flow and geometry
- Fitting losses: From manufacturer specifications
- Muffler pressure drop: From performance curves
- Valve internal losses: From technical data sheets
How Can You Minimize Back Pressure for Optimal Pneumatic System Performance?
Reducing back pressure requires systematic attention to exhaust system design, component selection, and maintenance practices to ensure maximum pneumatic efficiency.
Minimize back pressure by using properly sized exhaust tubing (typically one size larger than supply lines), reducing fitting quantities, selecting low-restriction mufflers, maintaining short direct exhaust runs, implementing regular maintenance schedules, and considering dedicated exhaust manifolds for multiple cylinder applications.
Design Optimization Strategies
Exhaust Line Sizing Guidelines
Proper tubing selection is critical for low back pressure:
Cylinder Bore | Supply Line Size | Recommended Exhaust Size | Flow Capacity |
---|---|---|---|
1-2 inch | 1/4″ | 3/8″ | Up to 40 SCFM |
2-3 inch | 3/8″ | 1/2″ | 40-100 SCFM |
3-4 inch | 1/2″ | 5/8″ or 3/4″ | 100-200 SCFM |
Rodless systems | Variable | Custom sizing | 50-500+ SCFM |
Component Selection Criteria
Choose components that minimize flow restrictions:
- Large port valves with exhaust ports equal to or larger than supply
- Low-restriction mufflers designed for high flow applications
- Minimal fitting quantities using direct connections where possible
- High-flow quick disconnects when removable connections needed
Installation Best Practices
Exhaust Routing Optimization
Minimize pressure drops through proper installation:
- Short, direct runs to atmosphere or exhaust manifolds
- Gradual bends instead of sharp 90-degree turns
- Adequate support to prevent sagging and restriction
- Proper slope for moisture drainage in humid environments
Manifold System Design
For multiple cylinder applications:
- Oversized manifolds to handle combined exhaust flows
- Individual cylinder connections sized for peak flow rates
- Central exhaust points to minimize total tubing length
- Pressure equalization chambers for consistent performance
Maintenance Protocols
Preventive Maintenance Schedule
Regular maintenance prevents back pressure buildup:
Maintenance Task | Frequency | Critical Points | Performance Impact |
---|---|---|---|
Muffler cleaning | Monthly | Remove contamination | Maintains low restriction |
Filter replacement | Quarterly | Prevent clogging | Ensures adequate flow |
Connection inspection | Semi-annually | Check for damage | Prevents air leaks |
System pressure test | Annually | Verify performance | Identifies degradation |
Troubleshooting Procedures
Systematic approach to identifying back pressure sources:
- Pressure measurement at multiple system points
- Component isolation testing to identify restrictions
- Flow rate verification against design specifications
- Visual inspection for obvious restrictions or damage
Advanced Solutions
Exhaust Boosters
For extreme back pressure situations:
- Venturi exhausters3 using supply air to create vacuum
- Vacuum generators for applications requiring sub-atmospheric exhaust
- Exhaust accumulators for smoothing pulsating flows
- Active exhaust systems with powered extraction
System Monitoring
Continuous performance optimization:
- Pressure sensors for real-time back pressure monitoring
- Flow meters to verify adequate exhaust capacity
- Performance trending to identify gradual degradation
- Automated alerts for excessive back pressure conditions
Bepto Solutions for Back Pressure Reduction
Our pneumatic components are specifically designed to minimize back pressure:
- Oversized exhaust ports in our replacement valves
- High-flow mufflers with minimal pressure drop
- Large-bore fittings for unrestricted connections
- Technical support for system optimization
- Performance guarantees on back pressure specifications
We provide comprehensive system analysis and recommendations to help you achieve optimal pneumatic performance with minimal back pressure restrictions. 🎯
Conclusion
Understanding and controlling back pressure is essential for achieving optimal pneumatic system performance, energy efficiency, and reliable operation in demanding industrial applications.
FAQs About Back Pressure in Pneumatic Systems
What is considered excessive back pressure in a pneumatic system?
Back pressure above 10-15 PSI is generally considered excessive for standard industrial cylinders, while high-speed applications should stay below 5-8 PSI. Excessive back pressure reduces cylinder speed by 20-50% and can decrease available force output significantly, making it a critical factor in system performance.
How do I measure back pressure in my pneumatic system?
Install a pressure gauge at the cylinder exhaust port during operation to measure dynamic back pressure accurately. Take readings during actual cylinder cycling rather than static conditions, as back pressure varies significantly with flow rate and system operation.
Can back pressure damage my pneumatic cylinders?
While back pressure typically won’t cause immediate damage, it increases seal wear, creates additional stress on components, and can lead to premature failure over time. The main concerns are reduced performance and increased energy consumption rather than catastrophic failure.
Why is my cylinder slower on retraction than extension?
Retraction is typically slower because the rod-side chamber has less area for exhaust flow, creating higher back pressure during retraction strokes. This is normal, but excessive back pressure from restrictions amplifies this natural difference significantly.
What’s the difference between back pressure and supply pressure?
Supply pressure is the compressed air pressure feeding into cylinders (typically 80-100 PSI), while back pressure is the resistance to exhaust flow (should be under 15 PSI). Both affect performance, but back pressure specifically impacts exhaust flow and cylinder speed during retraction or extension completion.
-
Discover the design, types, and operational advantages of rodless pneumatic cylinders in industrial automation. ↩
-
Explore Computational Fluid Dynamics (CFD), a powerful simulation tool used by engineers to analyze fluid flow and thermal performance. ↩
-
Understand the Venturi effect, a principle in fluid dynamics that describes the reduction in pressure when a fluid flows through a constricted section. ↩