Ingenieure gehen oft davon aus, dass elektrische Aktuatoren automatisch eine höhere Präzision bieten, was zu überdimensionierten Lösungen und unnötigen Kosten führt, obwohl pneumatische Zylinder die Positionierungsanforderungen mit wesentlich geringeren Investitionen und geringerer Komplexität erfüllen könnten.
Elektrische Aktuatoren bieten eine überragende Präzision mit einer Positioniergenauigkeit von ±0,001-0,01 mm und einer Wiederholgenauigkeit von ±0,002 mm, während pneumatische Zylinder in der Regel eine Genauigkeit von ±0,1-1,0 mm erreichen. Damit sind elektrische Systeme für die Mikropositionierung unverzichtbar, während pneumatische Lösungen für die meisten industriellen Positionieranforderungen ausreichen.
Gestern entdeckte Carlos aus einem mexikanischen Elektronikmontagewerk, dass seine teuren Servoaktuatoren eine 50-mal höhere Präzision boten, als für seine Anwendung erforderlich war, während Bepto kolbenstangenlose Zylinder1 seinen Bedarf an ±0,5 mm Positionierung zu geringeren Kosten mit 70% hätte decken können.
Inhaltsübersicht
- Welche Präzision erreichen elektrische Stellantriebe tatsächlich?
- Wie präzise können Pneumatikzylinder in realen Anwendungen sein?
- Welche Anwendungen erfordern tatsächlich eine hochpräzise Positionierung?
- Wie skalieren Kosten und Komplexität mit den Präzisionsanforderungen?
Welche Präzision erreichen elektrische Stellantriebe tatsächlich?
Die Präzisionsfähigkeiten elektrischer Stellantriebe variieren je nach Systemdesign, Rückmeldevorrichtungen und Steuerungskomplexität erheblich, wobei die Leistung von einfacher Positionierung bis zu Submikrometergenauigkeit reicht.
Elektrische Stellantriebe der Spitzenklasse erreichen eine Positioniergenauigkeit von ±0,001-0,01 mm mit einer Wiederholgenauigkeit von ±0,002 mm unter Verwendung von Servomotoren und hochauflösenden Encodern, während einfache elektrische Stellantriebe eine Genauigkeit von ±0,1-0,5 mm bieten, die mit pneumatischen Präzisionssystemen vergleichbar ist, jedoch wesentlich höhere Kosten und Komplexität verursacht.
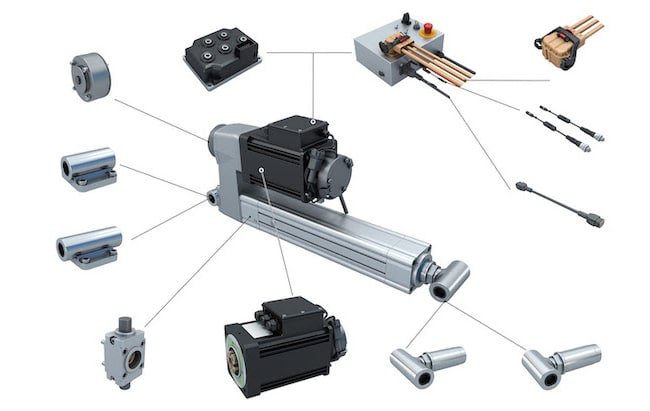
Elektrische Stellantriebe Präzision Kategorien
Leistung des Servosystems
Hochpräzise Servoaktuatoren liefern außergewöhnliche Genauigkeit:
- Ortungsgenauigkeit: ±0,001-0,01mm je nach Systemaufbau
- Reproduzierbarkeit: ±0,002-0,005 mm für eine gleichmäßige Positionierung
- Auflösung: 0,0001-0,001mm inkrementale Bewegungsmöglichkeit
- Stabilität: ±0,001-0,003mm Positionshaltegenauigkeit
Schrittmotor Präzision
Schrittmotorgestützte Systeme bieten eine gute Präzision bei geringeren Kosten:
- Schrittweise Auflösung: 0,01-0,1mm pro Schritt je nach Spindelsteigung
- Ortungsgenauigkeit: ±0,05-0,2 mm bei ordnungsgemäßer Kalibrierung
- Reproduzierbarkeit±0,02-0,1 mm für gleichbleibende Leistung
- Microstepping2: Bessere Auflösung durch elektronische Untergliederung
Vergleich der Präzisionsleistung
Elektrischer Aktuator Präzisionsmatrix
Aktuator Typ | Positionierungsgenauigkeit | Reproduzierbarkeit | Auflösung | Typische Kosten |
---|---|---|---|---|
High-End-Servo | ±0,001-0,005 mm | ±0,002mm | 0,0001 mm | $3000-$8000 |
Standard-Servo | ±0,01-0,05 mm | ±0,005 mm | 0,001 mm | $1500-$4000 |
Präzisionsschrittmacher | ±0,05-0,2 mm | ±0,02 mm | 0,01 mm | $800-$2500 |
Basic Stepper | ±0,1-0,5 mm | ±0,05 mm | 0,05 mm | $400-$1200 |
Faktoren, die die Präzision elektrischer Stellantriebe beeinflussen
Mechanische Konstruktionselemente
Die physikalische Konstruktion wirkt sich auf die erreichbare Präzision aus:
- Qualität der Leitspindel: Präzisionsgeschliffene Schrauben reduzieren Spiel und Fehler
- Lagersysteme: Hochpräzise Lager minimieren Spiel und Durchbiegung
- Strukturelle Steifigkeit: Steife Konstruktion verhindert Durchbiegung unter Last
- Thermische Stabilität: Temperaturkompensation erhält die Genauigkeit
Komplexität des Kontrollsystems
Elektronische Steuersysteme bestimmen das Präzisionsvermögen:
- Auflösung des Encoders: Höher aufgelöstes Feedback verbessert die Positionierungsgenauigkeit
- Steuerungsalgorithmen: Fortgeschrittene PID- und Vorwärtsregelung3 Leistung steigern
- Kalibrierungssysteme: Automatischer Fehlerausgleich und Mapping
- Umweltausgleich: Temperatur- und Lastkorrekturalgorithmen
Grenzen der Präzision in der realen Welt
Faktoren für Umweltauswirkungen
Die Betriebsbedingungen beeinflussen die tatsächliche Genauigkeit:
- Temperaturschwankungen: Die thermische Ausdehnung beeinflusst mechanische Komponenten
- Auswirkungen von Vibrationen: Externe Vibrationen verschlechtern die Positionierungsgenauigkeit
- Lastschwankungen: Veränderte Lasten beeinflussen die Systemkonformität und Genauigkeit
- Verlauf der Abnutzung: Der Verschleiß von Bauteilen verringert mit der Zeit die Präzision
Herausforderungen bei der Systemintegration
Die Präzision des gesamten Systems hängt von mehreren Faktoren ab:
- Montagegenauigkeit: Die Präzision der Installation beeinflusst die Gesamtleistung
- Kupplungssysteme: Mechanische Verbindungen führen zu Nachgiebigkeit und Spiel
- Lastkupplung: Anwendungslasten verursachen Durchbiegung und Positionierungsfehler
- Abstimmung des Kontrollsystems: Richtige Parameteroptimierung für Präzision unerlässlich
Präzisionsmessung und Verifizierung
Prüf- und Kalibrierungsverfahren
Die Überprüfung der Präzision elektrischer Stellantriebe erfordert anspruchsvolle Methoden:
- Laser-Interferometrie4: Die genaueste Methode zur Positionsmessung
- Lineare Drehgeber: Hochauflösende Rückmeldung zur Positionsüberprüfung
- Messuhren: Mechanische Messung zur Überprüfung der Grundgenauigkeit
- Statistische Analyse: Mehrere Messungen zur Beurteilung der Wiederholbarkeit
Standards für die Leistungsdokumentation
Industrienormen definieren Präzisionsmessungen:
- ISO-Normen: Internationale Spezifikationen für die Positionierungsgenauigkeit
- Herstellerangaben: Werksprüfung und Zertifizierungsverfahren
- Testen von Anwendungen: Überprüfung im Feld unter realen Betriebsbedingungen
- Kalibrierungsintervalle: Regelmäßige Überprüfung zur Wahrung von Präzisionsansprüchen
Anna, eine Konstrukteurin von Präzisionsmaschinen in der Schweiz, spezifizierte ursprünglich ±0,001 mm Servoaktuatoren für ihre Montageausrüstung. Nach einer Analyse ihrer tatsächlichen Toleranzanforderungen stellte sie fest, dass eine Genauigkeit von ±0,05 mm ausreichend war, so dass sie kostengünstigere Steppersysteme verwenden konnte, die ihr Aktuatorbudget um 60% reduzierten und gleichzeitig alle Leistungsanforderungen erfüllten.
Wie präzise können Pneumatikzylinder in realen Anwendungen sein?
Die Präzisionsfähigkeiten von Pneumatikzylindern werden oft unterschätzt, wobei moderne Konstruktionen und Steuerungssysteme für viele industrielle Anwendungen eine überraschend genaue Positionierung ermöglichen.
Moderne Pneumatikzylinder mit Präzisionssteuerungen können eine Positioniergenauigkeit von ±0,1-0,5 mm und eine Wiederholgenauigkeit von ±0,05-0,2 mm erreichen, während Standardzylinder eine Genauigkeit von ±0,5-2,0 mm bieten. Damit eignen sich Pneumatiksysteme für die meisten industriellen Positionieranforderungen zu deutlich geringeren Kosten als elektrische Alternativen.
Pneumatische Präzisionsfähigkeiten
Standard-Zylinder Präzision
Mit einfachen Pneumatikzylindern wird eine praxisgerechte Positioniergenauigkeit erreicht:
- Endlagengenauigkeit: ±0,5-2,0mm mit mechanischen Anschlägen
- Dämpfende Präzision: ±0,2-1,0 mm bei angemessener Geschwindigkeitskontrolle
- Reproduzierbarkeit±0,1-0,5 mm für konsistente Endpositionierung
- Empfindlichkeit der Last±0,5-1,5 mm Abweichung bei unterschiedlichen Belastungen
Verbesserte Präzisionssysteme
Fortschrittliche pneumatische Konstruktionen verbessern die Positionierungsfähigkeit:
- Servo-pneumatische Systeme: ±0,1-0,5 mm Genauigkeit mit Positionsrückmeldung
- Präzisionsregulatoren: ±0,05-0,2 mm Wiederholbarkeit mit Druckkontrolle
- Geführte Zylinder: ±0,2-0,8mm Genauigkeit mit integrierten Linearführungen
- Multi-Position-Systeme: ±0,3-1,0 mm Genauigkeit bei Zwischenpositionen
Bepto Präzisionszylinder-Lösungen
Vorteile des kolbenstangenlosen Präzisionszylinders
Unsere kolbenstangenlosen Druckluftzylinder bieten verbesserte Genauigkeit:
Typ des Zylinders | Positionierungsgenauigkeit | Reproduzierbarkeit | Hubbereich | Präzisionsmerkmale |
---|---|---|---|---|
Standard stangenlos | ±0,5-1,0 mm | ±0,2-0,5 mm | 100-6000mm | Magnetische Kupplung |
Präzision stangenlos | ±0,2-0,5 mm | ±0,1-0,3 mm | 100-4000mm | Lineare Führungen |
Servo-pneumatisch | ±0,1-0,3 mm | ±0,05-0,2 mm | 100-2000mm | Rückmeldung zur Position |
Multi-Position | ±0,3-0,8 mm | ±0,2-0,5 mm | 100-3000mm | Zwischenstopps |
Techniken zur Präzisionsverbesserung
Bepto-Zylinder sind mit präzisionsverbessernden Merkmalen ausgestattet:
- Präzisionsbearbeitung: Enge Toleranzen bei kritischen Komponenten
- Qualitätssiegel: Reibungsarme Dichtungen reduzieren Stick-Slip-Effekte
- Dämpfungssysteme: Einstellbare Dämpfung für gleichmäßige Abbremsung
- Präzision bei der Montage: Präzise Montageschnittstellen und Ausrichtungsmerkmale
Faktoren, die die pneumatische Präzision beeinflussen
Auswirkungen auf die Luftqualität
Die Qualität der Druckluft wirkt sich direkt auf die Positionierungsgenauigkeit aus:
- DruckstabilitätDruckschwankungen von ±0,1 bar beeinflussen die Positionierung um ±0,2-0,5 mm
- Luftbehandlung: Richtige Filtration und Schmierung verbessern die Konsistenz
- Temperaturkontrolle: Stabile Lufttemperatur reduziert thermische Effekte
- Durchflusskontrolle: Präzise Geschwindigkeitskontrolle verbessert die Wiederholbarkeit der Positionierung
Komplexität des Kontrollsystems
Grundlegende Kontrollmethoden
Einfache pneumatische Steuerungen sorgen für ausreichende Präzision:
- Mechanische Anschläge: Feste Endlagen mit ±0,2-0,5 mm Genauigkeit
- Dämpfungsventile: Geschwindigkeitskontrolle für gleichmäßiges Abbremsen
- Druckregelung: Kraftkontrolle mit Einfluss auf die Endlage
- Durchflussbegrenzung: Geschwindigkeitskontrolle für bessere Wiederholbarkeit
Fortgeschrittene Kontrollsysteme
Hochentwickelte pneumatische Steuerungen erhöhen die Präzision:
- Rückmeldung zur Position: Lineare Sensoren sorgen für einen geschlossenen Regelkreis
- Servo-Ventile: Proportionale Steuerung für präzise Positionierung
- Elektronische Kontrollen: PLC-basierte Systeme mit Positionsalgorithmen
- Druckprofilierung: Variabler Druck für Lastausgleich
Anwendungsspezifische Präzisionsanforderungen
Fertigung Montageanwendungen
Typische Präzisionsanforderungen in der industriellen Montage:
- Einfügen von Komponenten: ±1-3mm Genauigkeit in der Regel ausreichend
- Positionierung der TeileWiederholbarkeit von ±0,5-2 mm für die meisten Operationen
- Materialumschlag: ±2-5mm Genauigkeit ausreichend für Transferoperationen
- Positionierung der Vorrichtungen: ±0,5-1,5 mm Genauigkeit bei der Werkstückaufnahme
Verpackung und Materialhandhabung
Präzisionsanforderungen für Verpackungsvorgänge:
- Produktpositionierung: ±1-5 mm Genauigkeit für die meisten Verpackungsanforderungen
- Anwendung des Etiketts: ±0,5-2mm Genauigkeit bei der Platzierung der Etiketten
- Transfers über das Förderband: ±2-10mm Genauigkeit ausreichend für Materialfluss
- Sortiervorgänge: ±1-3mm Genauigkeit für Produktumlenkung
Strategien zur Präzisionsverbesserung
Systemdesign-Optimierung
Maximierung der Präzision von Pneumatikzylindern durch Design:
- Starre Montage: Steife Befestigungssysteme reduzieren Durchbiegungsfehler
- Lastausgleich: Richtige Lastverteilung verbessert die Genauigkeit
- Präzision bei der Ausrichtung: Genaue Installation entscheidend für Leistung
- Umweltkontrolle: Temperatur- und Schwingungsisolierung
Erweiterung des Kontrollsystems
Höhere Präzision durch bessere Kontrolle:
- Druckregelung: Stabiler Versorgungsdruck verbessert Wiederholbarkeit
- Geschwindigkeitskontrolle: Einheitliche Anfluggeschwindigkeiten verbessern die Positionierung
- Lastausgleich: Anpassung der Parameter an unterschiedliche Lasten
- Rückkopplungssysteme: Positionssensoren für den geschlossenen Regelkreis
Präzisionsmessung und Verifizierung
Feldtestmethoden
Praktische Ansätze zur Messung der pneumatischen Präzision:
- Messuhren: Mechanische Messung zur Beurteilung der Grundgenauigkeit
- Lineare Skalen: Optische Messung für höhere Genauigkeit
- Statistische Stichproben: Mehrfachmessungen zur Analyse der Wiederholbarkeit
- Belastungstests: Präzisionsprüfung unter realen Betriebsbedingungen
Optimierung der Leistung
Verbesserung der Präzision von Pneumatikzylindern durch Tuning:
- Einstellung der Dämpfung: Optimierung der Verzögerung für gleichmäßiges Anhalten
- Druckoptimierung: Ermitteln des optimalen Betriebsdrucks für die Genauigkeit
- Abstimmung der Geschwindigkeit: Anpassung der Anfluggeschwindigkeiten für beste Wiederholbarkeit
- Umweltausgleich: Berücksichtigung von Temperatur- und Lastschwankungen
Miguel, der in Spanien automatisierte Montageanlagen entwickelt, erreichte mit den kolbenstangenlosen Zylindern von Bepto eine Positioniergenauigkeit von ±0,3 mm, indem er eine angemessene Druckregelung und Dämpfungseinstellung implementierte. Diese Präzision erfüllte seine Montageanforderungen zu 65% niedrigeren Kosten als die Servoaktuatoren, die er ursprünglich in Betracht gezogen hatte, und bot gleichzeitig schnellere Zykluszeiten und eine einfachere Wartung.
Welche Anwendungen erfordern tatsächlich eine hochpräzise Positionierung?
Das Verständnis echter Präzisionsanforderungen hilft den Ingenieuren, eine Überspezifikation zu vermeiden und kosteneffektive Aktuatorlösungen auszuwählen, die die tatsächlichen Leistungsanforderungen ohne unnötige Komplexität erfüllen.
Echte Ultrahochpräzision (±0,01 mm oder besser) ist nur in 5-10% der industriellen Anwendungen erforderlich, vor allem in der Halbleiterfertigung, der Präzisionsbearbeitung und der optischen Montage, während der Großteil der industriellen Automatisierung erfolgreich mit einer Präzision von ±0,1-1,0 mm arbeitet, die Pneumatikzylinder kostengünstig bieten können.
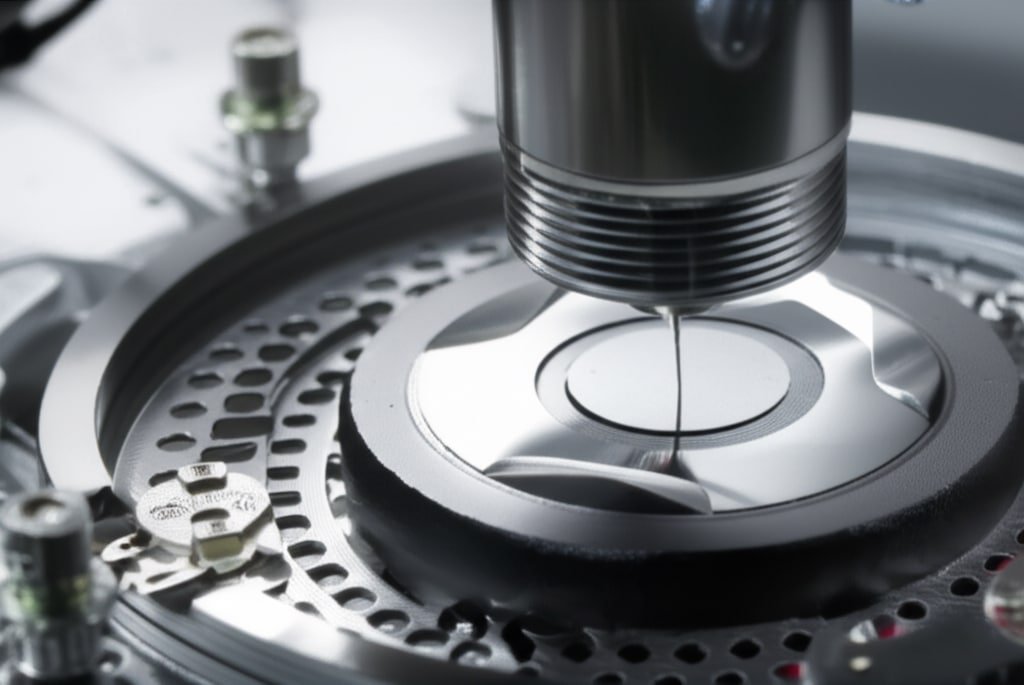
Ultra-Hochpräzisionsanwendungen
Herstellung von Halbleitern
Die Chipherstellung erfordert eine außergewöhnliche Positioniergenauigkeit:
- Handhabung von Wafern±0,005-0,02 mm für die Platzierung und Ausrichtung der Matrizen
- Drahtbonden: ±0,002-0,01mm für elektrische Anschlüsse
- Lithographie: ±0,001-0,005mm für die Musterausrichtung
- Montagearbeiten: ±0,01-0,05 mm für die Platzierung der Komponenten
Präzisionsbearbeitungsvorgänge
Die hochpräzise Fertigung erfordert eine enge Positionierung:
- CNC-Bearbeitung: ±0,005-0,02 mm für die Herstellung von Präzisionsteilen
- Schleifen: ±0,002-0,01mm für die Oberflächenbearbeitung
- Messsysteme: ±0,001-0,005mm für die Qualitätsprüfung
- Positionierung der Werkzeuge±0,01-0,05 mm für die Platzierung der Schneidwerkzeuge
Anwendungen, die für pneumatische Präzision geeignet sind
Automobilherstellung
Anforderungen an die Präzision der Fahrzeugproduktion:
Art der Operation | Erforderliche Präzision | Pneumatisches Leistungsvermögen | Kostenvorteil |
---|---|---|---|
Schweißen der Karosserie | ±1-3mm | ±0,5-1,0 mm | Ausgezeichnete Übereinstimmung |
Montage von Bauteilen | ±0,5-2mm | ±0,2-0,8 mm | Gute Übereinstimmung |
Materialumschlag | ±2-5mm | ±0,5-2,0 mm | Ausgezeichnete Übereinstimmung |
Positionierung der Vorrichtungen | ±1-2mm | ±0,3-1,0 mm | Gute Übereinstimmung |
Anwendungen in der Verpackungsindustrie
Gewerbliche Verpackungen brauchen Präzision:
- Produktpositionierung: ±1-5mm ausreichend für die meisten Gehäusetypen
- Anwendung des Etiketts: ±0,5-2mm ausreichend für kommerzielle Etikettierung
- Formung von Kartons: ±2-10mm akzeptabel für Verpackungsvorgänge
- Palettieren: ±5-20mm ausreichend für automatisches Stapeln
Lebensmittel- und Getränkeindustrie
Sanitäre Anwendungen mit mäßigen Präzisionsanforderungen:
- Handhabung des Produkts: ±2-10mm geeignet für die Lebensmittelverarbeitung
- Abfüllvorgänge: ±1-5mm ausreichend für die meisten Abfüllsysteme
- Verpackung: ±2-8mm ausreichend für Lebensmittelverpackungen
- Fördersysteme: ±5-15 mm zulässig für den Materialtransport
Allgemeine Fertigungsanwendungen
Montagearbeiten
Typische Anforderungen an die Montagegenauigkeit:
- Einfügen von Komponenten: ±1-3mm für die meisten mechanischen Baugruppen
- Einbau von Befestigungselementen: ±0,5-2mm bei automatischer Befestigung
- Teilweise Orientierung: ±2-5mm für Vorschub und Positionierung
- Qualitätskontrolle: ±0,5-2mm für Gut/Schlecht-Kontrolle
Materialtransportsysteme
Präzisionsbedarf bei der Materialbewegung:
- Auswählen und platzieren: ±1-5mm für die meisten Handhabungsvorgänge
- Sortiersysteme±2-8mm für Produktumlenkung
- Übertragungsmechanismen: ±3-10mm für Förderband-Schnittstellen
- Speichersysteme: ±5-20mm für automatische Lagerhaltung
Rahmen für die Präzisionsanforderungsanalyse
Kriterien für die Bewertung der Bewerbung
Ermittlung des tatsächlichen Präzisionsbedarfs:
- Produkttoleranzen: Welche Genauigkeit ist für das Endprodukt erforderlich?
- Prozessfähigkeit5: Welche Präzision können nachgelagerte Prozesse bieten?
- Qualitätsstandards: Welche Positionierungsgenauigkeit gewährleistet eine akzeptable Qualität?
- Kostensensibilität: Wie wirken sich die Präzisionsanforderungen auf die Gesamtprojektkosten aus?
Folgen der Überspezifizierung
Probleme, die durch zu hohe Genauigkeitsanforderungen verursacht werden:
- Unnötige Kosten: 3-5x höhere Kosten für Antrieb und System
- Erhöhte Komplexität: Anspruchsvollere Kontrolle und Wartungsbedarf
- Erweiterte Zeitpläne: Längere Planungs-, Beschaffungs- und Inbetriebnahmezeiten
- Operative Herausforderungen: Höhere Qualifikationsanforderungen und Wartungskosten
Kosten-Nutzen-Analyse der Präzision
Verhältnis zwischen Präzision und Kosten
Verständnis der wirtschaftlichen Auswirkungen von Präzisionsanforderungen:
Präzisionsnivellier | Aktuator Kostenmultiplikator | Systemkomplexität | Wartungsfaktor |
---|---|---|---|
±1-2mm | 1,0x (Basiswert) | Einfach | 1.0x |
±0,5-1mm | 1.5-2x | Mäßig | 1.2-1.5x |
±0,1-0,5 mm | 2-4x | Komplexe | 1.5-2.5x |
±0,01-0,1 mm | 4-8x | Sehr komplex | 2.5-4x |
±0,001-0,01 mm | 8-15x | Äußerst komplex | 4-8x |
Alternative Präzisionslösungen
Mechanische Präzisionsverbesserung
Bessere Präzision ohne teure Aktuatoren zu erreichen:
- Präzisionsbefestigungen: Mechanische Referenzen verbessern die Positionierungsgenauigkeit
- Führungssysteme: Linearführungen reduzieren Positionierungsfehler
- Systeme zur Einhaltung der Vorschriften: Flexible Kupplungen gleichen Positionierungsfehler aus
- Kalibrierungsmethoden: Software-Kompensation für systematische Fehler
Optimierung der Prozessgestaltung
Gestaltung von Prozessen zur Anpassung an die verfügbare Präzision:
- Stapeln von Toleranzen: Konstruktion von Baugruppen zum Ausgleich von Positionierungsfehlern
- Selbstausrichtende Merkmale: Produktdesigns, die Positionierungsfehler korrigieren
- Flexibilität der Prozesse: Operationen, die mit größeren Positionstoleranzen arbeiten
- Qualitätssysteme: Inspektion und Korrektur statt perfekter Positionierung
Branchenspezifische Präzisionsrichtlinien
Elektronikfertigung
Die Präzisionsanforderungen variieren je nach Anwendung:
- PCB-Montage±0,1-0,5 mm für die meisten Komponentenplatzierungen
- Montage des Steckers: ±0,05-0,2mm für elektrische Anschlüsse
- Montage des Gehäuses: ±0,5-2mm für mechanische Gehäuse
- Prüfvorgänge: ±0,2-1mm für automatisierte Prüfungen
Pharmazeutische Herstellung
Präzisionsbedarf in der Arzneimittelproduktion:
- Handhabung von Tabletten±1-3 mm für die meisten pharmazeutischen Verfahren
- Verpackungsarbeiten±0,5-2 mm für die Blisterpackungsbildung
- Abfüllanlagen±0,2-1mm für Flüssigkeitsabfüllvorgänge
- Kennzeichnung: ±0,5-2mm für die pharmazeutische Etikettierung
Sarah, die Automatisierungsprojekte für einen britischen Konsumgüterhersteller leitet, führte ein Präzisionsaudit ihrer Produktionslinien durch. Sie entdeckte, dass 85% ihrer Positionierungsanforderungen innerhalb von ±1 mm lagen, was es ihr ermöglichte, teure Servosysteme durch kolbenstangenlose Bepto-Zylinder zu ersetzen. Durch diese Änderung konnten die Automatisierungskosten um $280.000 gesenkt werden, während gleichzeitig alle Qualitätsstandards eingehalten und die Zuverlässigkeit des Systems verbessert wurde.
Wie skalieren Kosten und Komplexität mit den Präzisionsanforderungen?
Das Verständnis der exponentiellen Beziehung zwischen Präzisionsanforderungen und Systemkosten hilft Ingenieuren, fundierte Entscheidungen über die Auswahl und Spezifikation von Aktuatoren zu treffen.
Die Kosten für Aktuatoren steigen mit den Präzisionsanforderungen exponentiell an: Systeme mit einem Durchmesser von ±0,01 mm kosten 8-15 Mal mehr als Systeme mit einem Durchmesser von ±1 mm, während die Kosten für Komplexität, Wartung und Schulung noch schneller ansteigen.
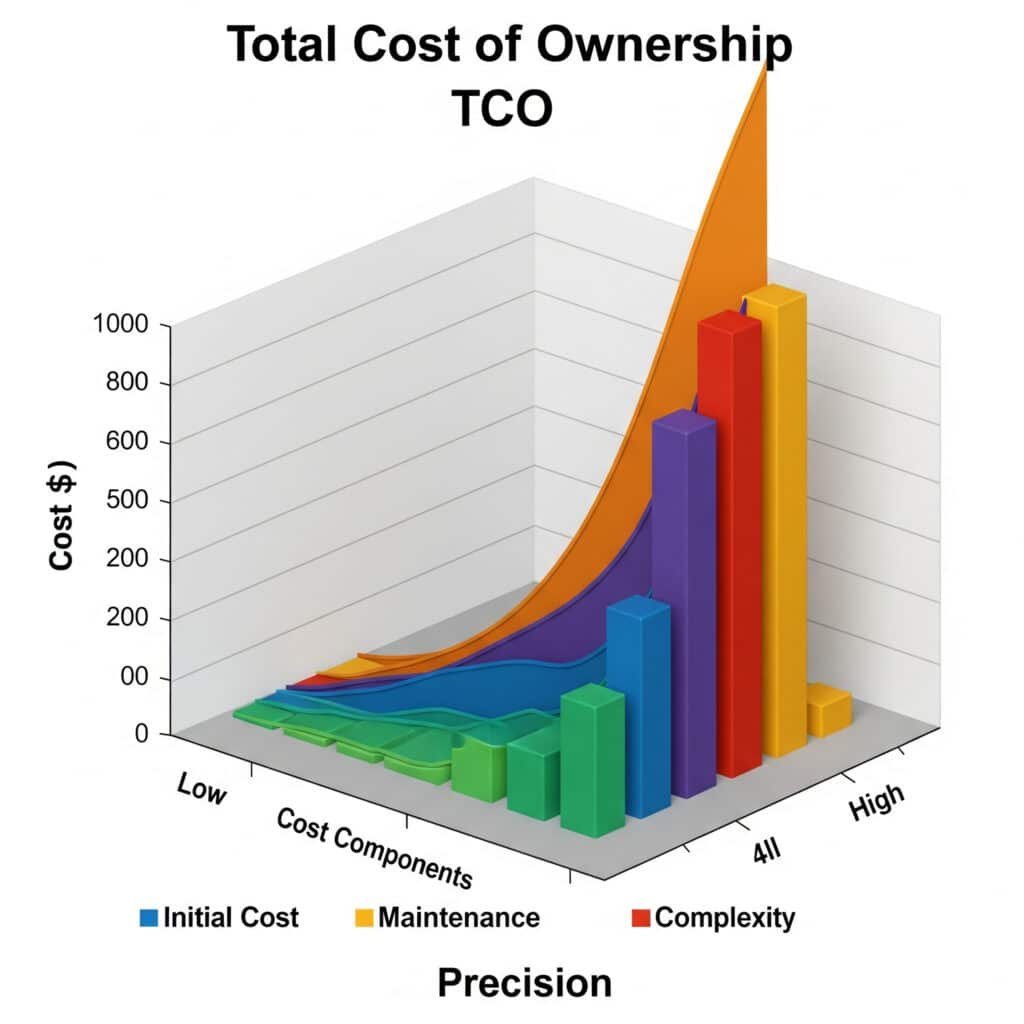
Analyse der Kostenskala
Aktuator Kostenprogression
Präzisionsanforderungen treiben die Kosten exponentiell in die Höhe:
Präzisionsnivellier | Pneumatische Kosten | Elektrische Kosten | Kostenmultiplikator | Bepto Vorteil |
---|---|---|---|---|
±2-5mm | $100-$400 | $500-$1500 | 1.0x | 70-80% Einsparungen |
±1-2mm | $150-$600 | $800-$2500 | 1.5-2x | 65-75% Einsparungen |
±0,5-1mm | $200-$800 | $1500-$4000 | 2-3x | 60-70% Einsparungen |
±0,1-0,5 mm | $300-$1200 | $3000-$8000 | 4-6x | Begrenzte pneumatische |
±0,01-0,1 mm | Nicht anwendbar | $6000-$15000 | 8-12x | Elektrisch erforderlich |
±0,001-0,01 mm | Nicht anwendbar | $12000-$30000 | 15-25x | Elektrisch erforderlich |
Eskalation der Systemkomplexität
Anforderungen für unterstützende Komponenten
Präzision erfordert immer ausgefeiltere Unterstützungssysteme:
- Grundlegende Systeme: Einfache Ventile und einfache Steuerungen
- Mäßige Präzision: Servoventile und Positionsrückmeldung
- Hohe Präzision: Fortschrittliche Steuerungen und Umweltisolierung
- Ultrahohe Präzision: Reinräume und Schwingungsisolierung
Komplexität von Kontrollsystemen
Die Anforderungen an die Präzision treiben die Komplexität der Steuerung voran:
Präzisionsnivellier | Komplexität der Kontrolle | Stunden programmieren | Instandhaltungskenntnisse |
---|---|---|---|
±2-5mm | Basic ein/aus | 1-4 Stunden | Mechanisch |
±1-2mm | Einfache Positionierung | 4-16 Stunden | Grundlegende elektrische |
±0,5-1mm | Steuerung im geschlossenen Kreislauf | 16-40 Stunden | Erweiterte elektrische |
±0,1-0,5 mm | Servo-Steuerung | 40-120 Stunden | Experte für Programmierung |
±0,01-0,1 mm | Erweiterte Servo | 120-300 Stunden | Spezialist erforderlich |
Auswirkungen auf die Gesamtbetriebskosten
Fünf-Jahres-Kostenprognose
Die Präzisionsanforderungen betreffen alle Kostenkategorien:
Kostenkategorie | ±2mm System | ±0,5mm System | ±0,1mm System | ±0,01mm System |
---|---|---|---|---|
Erstausstattung | $2,000 | $8,000 | $20,000 | $50,000 |
Einrichtung | $500 | $2,000 | $8,000 | $20,000 |
Ausbildung | $500 | $2,000 | $8,000 | $20,000 |
Jährliche Wartung | $200 | $800 | $3,000 | $8,000 |
5 Jahre insgesamt | $4,000 | $16,000 | $51,000 | $140,000 |
Umwelt- und Infrastrukturkosten
Anforderungen an eine präzise Umgebung
Höhere Präzision erfordert kontrollierte Umgebungen:
- Temperaturkontrolle±0,1°C für Ultrahochpräzisionssysteme
- Schwingungsisolierung: Spezialisierte Fundamente und Isolationssysteme
- Saubere Umgebungen: Gefilterte Luft und Kontaminationskontrolle
- Kontrolle der Luftfeuchtigkeit: Stabiler Feuchtigkeitsgehalt für Maßhaltigkeit
Investitionen in die Infrastruktur
Präzisionssysteme benötigen eine unterstützende Infrastruktur:
- Qualität der Stromversorgung: Geregelte Stromversorgungen und UPS-Systeme
- Netzinfrastruktur: Hochgeschwindigkeits-Kommunikationssysteme
- Kalibrierungsausrüstung: Präzisionsmess- und Prüfgeräte
- Wartungseinrichtungen: Reinräume und spezielle Arbeitsbereiche
Präzise Optimierungsstrategien
Right-Sizing der Präzisionsanforderungen
Vermeidung von Überspezifizierung durch sorgfältige Analyse:
- Analyse der Toleranzen: Den tatsächlichen Präzisionsbedarf verstehen
- Prozessfähigkeit: Anpassung der Präzision an die Produktionsanforderungen
- Qualitätssysteme: Inspektion statt perfekter Positionierung
- Optimierung des Designs: Produkte schaffen, die Positionierungsfehler ausgleichen
Bepto Kosteneffiziente Lösungen
Pneumatische Präzisionsoptimierung
Maximierung der Präzision von Pneumatikzylindern auf kostengünstige Weise:
- Entwurf des Systems: Richtige Montage und Ausrichtung für beste Genauigkeit
- Optimierung der Steuerung: Druck- und Geschwindigkeitskontrolle für Wiederholbarkeit
- Qualitätskomponenten: Präzisionsgefertigte Zylinder und Steuerungen
- Anwendungstechnik: Anpassung der Zylinderkapazität an die Anforderungen
Hybride Ansätze
Kombination von Technologien für ein optimales Kosten-Nutzen-Verhältnis:
- Grob-/Feinpositionierung: Pneumatisch für schnelle Bewegungen, elektrisch für Präzision
- Selektive Präzision: Hohe Präzision nur bei absoluter Notwendigkeit
- Mechanische Präzision: Verwendung von Vorrichtungen und Hilfsmitteln zur Verbesserung der Positionierung
- Prozessentschädigung: Software-Korrektur für Positionierungsfehler
Entscheidungsrahmen für die Präzisionsauswahl
Bewertung der Anforderungen an die Präzision
Systematischer Ansatz zur Ermittlung des tatsächlichen Bedarfs:
- Produktanalyse: Welche Präzision ist für das Endprodukt erforderlich?
- Prozessfähigkeit: Was können die nachgelagerten Prozesse leisten?
- Auswirkungen auf die Qualität: Wie wirkt sich der Positionierungsfehler auf die Endqualität aus?
- Kostensensibilität: Welches Präzisionsniveau optimiert die Gesamtkosten des Projekts?
Matrix für die Technologieauswahl
Auswahl der optimalen Aktuatortechnologie auf der Grundlage der Präzisionsanforderungen:
Anforderung an die Präzision | Empfohlene Technologie | Optimierung der Kosten | Kompromisse bei der Leistung |
---|---|---|---|
±5-10mm | Standard pneumatisch | Geringste Kosten | Grundlegende Positionierung |
±1-3mm | Pneumatische Präzision | Guter Wert | Mäßige Präzision |
±0,3-1mm | Erweiterte pneumatische | Ausgewogene Kosten | Gute Präzision |
±0,1-0,3 mm | Elektrische Basis | Höhere Kosten | Ausgezeichnete Präzision |
±0,01-0,1 mm | Servo elektrisch | Hohe Kosten | Überlegene Präzision |
<±0,01mm | Ultrapräzise elektrische | Extreme Kosten | Höchste Präzision |
Analyse der Investitionsrentabilität
Rechtfertigung von Präzisionsinvestitionen
Feststellen, wann sich hohe Präzision auszahlt:
- Verbesserung der Qualität: Geringere Kosten für Ausschuss und Nacharbeit
- Prozessfähigkeit: Ermöglichung neuer Produkte oder Verfahren
- Wettbewerbsvorteil: Marktdifferenzierung durch Präzision
- Vorteile der Automatisierung: Geringerer Arbeitsaufwand und verbesserte Konsistenz
Kosten-Nutzen-Optimierung
Finden des optimalen Präzisionsniveaus:
- Analyse der Grenzkosten: Kosten für jedes Präzisionsinkrement
- Bewertung der Auswirkungen auf die Qualität: Vorteil einer besseren Positionierung
- Risikobewertung: Kosten von Positionierungsfehlern gegenüber Investitionen in die Präzision
- Langfristige Überlegungen: Technologieentwicklung und Veralterung
James, ein Projektingenieur bei einem deutschen Automobilzulieferer, spezifizierte ursprünglich ±0,1 mm Servoantriebe für seine Montagelinie auf der Grundlage von Zeichnungstoleranzen. Nach der Durchführung einer Prozessfähigkeitsstudie stellte er fest, dass eine Positionierung von ±0,5 mm angemessen war, so dass er kolbenstangenlose Zylinder von Bepto verwenden konnte, die seine Projektkosten von $180.000 auf $65.000 reduzierten, während sie alle Produktionsanforderungen erfüllten und die Zykluszeiten um 25% verbesserten.
Schlussfolgerung
Elektrische Aktuatoren bieten eine überragende Präzision (±0,001-0,01 mm), die für spezielle Anwendungen unerlässlich ist, während pneumatische Zylinder eine angemessene Präzision (±0,1-1,0 mm) für die meisten industriellen Anforderungen bei deutlich geringeren Kosten und geringerer Komplexität bieten, so dass die Analyse der Präzisionsanforderungen für die optimale Auswahl des Aktuators entscheidend ist.
Häufig gestellte Fragen zur Präzision von Zylindern und elektrischen Stellantrieben
F: Kann man mit Pneumatikzylindern eine Positionierungsgenauigkeit im Submillimeterbereich erreichen?
Ja, moderne Pneumatikzylinder mit Präzisionssteuerung können eine Positioniergenauigkeit von ±0,1-0,5 mm erreichen, was für die meisten industriellen Anwendungen ausreicht und wesentlich kostengünstiger ist als elektrische Aktuatoren, die eine unnötig hohe Präzision bieten.
F: Wie viel Prozent der industriellen Anwendungen erfordern tatsächlich Ultrahochpräzision?
Nur 5-10% der industriellen Anwendungen erfordern wirklich eine Präzision von mehr als ±0,1 mm, wobei die meisten Fertigungs-, Verpackungs- und Montagevorgänge mit einer Positioniergenauigkeit von ±0,5-2,0 mm erfolgreich funktionieren, die pneumatische Systeme kostengünstig bieten.
F: Wie viel mehr kosten hochpräzise elektrische Stellantriebe im Vergleich zu pneumatischen Zylindern?
Hochpräzise elektrische Stellantriebe (±0,01 mm) kosten 8-15 mal mehr als entsprechende Pneumatikzylinder (±0,5 mm), wobei die Gesamtsystemkosten einschließlich Installation, Programmierung und Wartung oft 10-20 mal höher sind.
F: Bieten kolbenstangenlose Zylinder eine bessere Präzision als Standardzylinder?
Ja, kolbenstangenlose Druckluftzylinder bieten in der Regel eine Positioniergenauigkeit von ±0,2-0,8 mm im Vergleich zu ±0,5-2,0 mm bei Standardzylindern, was auf ihre geführte Konstruktion und die geringere Seitenbelastung zurückzuführen ist.
F: Kann ich die Präzision von Pneumatikzylindern verbessern, ohne auf elektrische Antriebe umzusteigen?
Ja, die pneumatische Präzision kann durch eine angemessene Druckregulierung, Geschwindigkeitssteuerung, mechanische Führungen, Positionsrückmeldesysteme und eine sorgfältige Systemauslegung verbessert werden, wodurch oft eine angemessene Präzision zu einem Bruchteil der Kosten für elektrische Aktuatoren erreicht wird.
-
Entdecken Sie die Vorteile von kolbenstangenlosen Pneumatikzylindern in der Industrieautomation: Konstruktion, Typen und Betrieb. ↩
-
Erfahren Sie, wie Microstepping funktioniert, um die Auflösung zu erhöhen und die Bewegung eines Schrittmotors zu glätten. ↩
-
Erkunden Sie die Prinzipien von Proportional-Integral-Derivative (PID)-Reglern, einem weit verbreiteten und leistungsstarken Regelkreismechanismus. ↩
-
Verstehen Sie die physikalischen Grundlagen der Laserinterferometrie und ihre Anwendung als hochpräzises Messinstrument in Wissenschaft und Technik. ↩
-
Erfahren Sie mehr über die Prozessfähigkeitsanalyse, ein statistisches Werkzeug, mit dem festgestellt werden kann, ob ein Fertigungsprozess in der Lage ist, Teile innerhalb bestimmter Grenzen herzustellen. ↩